Niewypełnienie żywicą epoksydową
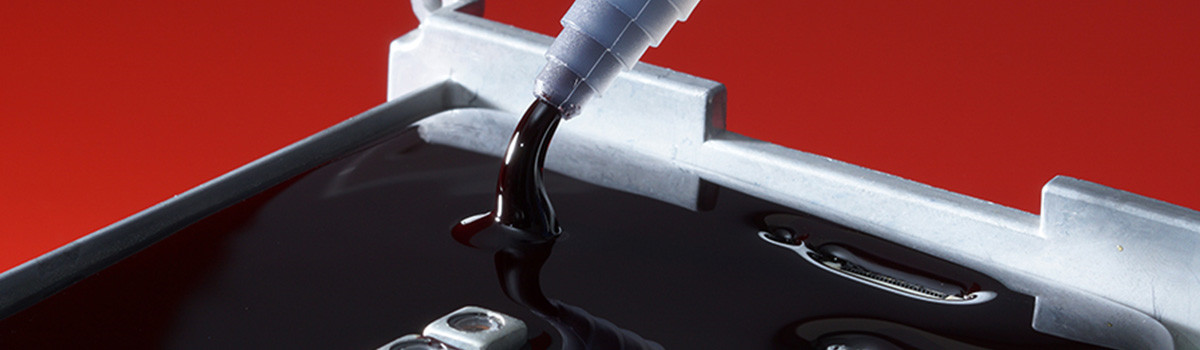
Podkład epoksydowy to rodzaj kleju stosowanego w celu zwiększenia niezawodności elementów elektronicznych, szczególnie w zastosowaniach związanych z pakowaniem półprzewodników. Wypełnia lukę między opakowaniem a płytką drukowaną (PCB), zapewniając mechaniczne wsparcie i odciążenie, aby zapobiec uszkodzeniom związanym z rozszerzaniem i kurczeniem termicznym. Podkład epoksydowy poprawia również parametry elektryczne pakietu poprzez zmniejszenie pasożytniczej indukcyjności i pojemności. W tym artykule badamy różne zastosowania żywicy epoksydowej wypełniającej, różne dostępne rodzaje i ich zalety.
Znaczenie niedopełnienia żywicy epoksydowej w opakowaniach półprzewodnikowych
Podkład epoksydowy ma kluczowe znaczenie w opakowaniach półprzewodników, zapewniając mechaniczne wzmocnienie i ochronę delikatnych elementów mikroelektronicznych. Jest to specjalistyczny materiał klejący stosowany do wypełniania luki między chipem półprzewodnikowym a podłożem opakowania, zwiększający niezawodność i wydajność urządzeń elektronicznych. Tutaj zbadamy znaczenie niedopełnionej żywicy epoksydowej w opakowaniach półprzewodników.
Jedną z podstawowych funkcji niedopełnionej żywicy epoksydowej jest poprawa wytrzymałości mechanicznej i niezawodności opakowania. Podczas pracy chipy półprzewodnikowe są poddawane różnym naprężeniom mechanicznym, takim jak rozszerzanie i kurczenie termiczne, wibracje i wstrząsy mechaniczne. Naprężenia te mogą prowadzić do powstawania pęknięć połączeń lutowanych, co może powodować awarie elektryczne i skracać ogólną żywotność urządzenia. Podkład epoksydowy działa jako środek redukujący naprężenia poprzez równomierne rozłożenie naprężeń mechanicznych na chipie, podłożu i połączeniach lutowanych. Skutecznie minimalizuje powstawanie pęknięć oraz zapobiega propagacji pęknięć już istniejących, zapewniając wieloletnią niezawodność opakowania.
Innym krytycznym aspektem wypełniacza epoksydowego jest jego zdolność do zwiększania wydajności termicznej urządzeń półprzewodnikowych. Rozpraszanie ciepła staje się poważnym problemem, ponieważ urządzenia elektroniczne kurczą się i zwiększają gęstość mocy, a nadmierne ciepło może obniżyć wydajność i niezawodność chipa półprzewodnikowego. Podkład epoksydowy ma doskonałe właściwości przewodzenia ciepła, co pozwala na efektywne odprowadzanie ciepła z chipa i rozprowadzanie go po całym opakowaniu. Pomaga to utrzymać optymalną temperaturę roboczą i zapobiega powstawaniu gorących punktów, poprawiając w ten sposób ogólne zarządzanie temperaturą urządzenia.
Podkład epoksydowy chroni również przed wilgocią i zanieczyszczeniami. Wnikanie wilgoci może prowadzić do korozji, upływu prądu i wzrostu materiałów przewodzących, co prowadzi do nieprawidłowego działania urządzenia. Podkład epoksydowy działa jak bariera, uszczelniając wrażliwe obszary i zapobiegając przedostawaniu się wilgoci do opakowania. Zapewnia również ochronę przed kurzem, brudem i innymi zanieczyszczeniami, które mogą niekorzystnie wpływać na parametry elektryczne układu półprzewodnikowego. Zabezpieczając chip i jego połączenia, wypełniacz epoksydowy zapewnia długoterminową niezawodność i funkcjonalność urządzenia.
Ponadto niedopełniona żywica epoksydowa umożliwia miniaturyzację opakowań półprzewodników. Przy stałym zapotrzebowaniu na mniejsze i bardziej kompaktowe urządzenia żywica epoksydowa z niedostatecznym wypełnieniem umożliwia stosowanie technik pakowania flip-chip i chip-scale. Techniki te polegają na bezpośrednim zamontowaniu chipa na podłożu opakowania, eliminując potrzebę łączenia przewodów i zmniejszając rozmiar opakowania. Podkład epoksydowy zapewnia wsparcie strukturalne i utrzymuje integralność interfejsu chip-substrat, umożliwiając pomyślne wdrożenie tych zaawansowanych technologii pakowania.
Jak niedostateczna żywica epoksydowa odpowiada na wyzwania
Opakowania półprzewodnikowe odgrywają kluczową rolę w wydajności, niezawodności i trwałości urządzeń elektronicznych. Polega na umieszczeniu układów scalonych (IC) w obudowach ochronnych, zapewnieniu połączeń elektrycznych i rozproszeniu ciepła wytwarzanego podczas pracy. Jednak opakowania półprzewodnikowe stoją przed kilkoma wyzwaniami, w tym naprężeniami termicznymi i wypaczeniami, które mogą znacząco wpłynąć na funkcjonalność i niezawodność zapakowanych urządzeń.
Jednym z głównych wyzwań jest stres termiczny. Układy scalone wytwarzają ciepło podczas pracy, a nieodpowiednie odprowadzanie ciepła może zwiększyć temperaturę wewnątrz obudowy. Ta zmiana temperatury powoduje stres termiczny, ponieważ różne materiały w opakowaniu rozszerzają się i kurczą z różną szybkością. Nierównomierne rozszerzanie i kurczenie się może powodować naprężenia mechaniczne, prowadzące do uszkodzeń połączeń lutowanych, rozwarstwień i pęknięć. Stres termiczny może zagrozić integralności elektrycznej i mechanicznej opakowania, ostatecznie wpływając na wydajność i niezawodność urządzenia.
Warpage to kolejne krytyczne wyzwanie w opakowaniach półprzewodnikowych. Wypaczenie odnosi się do wygięcia lub odkształcenia podłoża opakowania lub całego opakowania. Może wystąpić podczas procesu pakowania lub w wyniku stresu termicznego. Wypaczenie jest spowodowane przede wszystkim niedopasowaniem współczynnika rozszerzalności cieplnej (CTE) różnych materiałów w opakowaniu. Na przykład współczynnik CTE silikonowej matrycy, podłoża i formy może się znacznie różnić. Pod wpływem zmian temperatury materiały te rozszerzają się lub kurczą w różnym tempie, co prowadzi do wypaczenia.
Warpage stwarza kilka problemów dla pakietów półprzewodnikowych:
- Może to powodować powstawanie punktów koncentracji naprężeń, zwiększając prawdopodobieństwo uszkodzeń mechanicznych i zmniejszając niezawodność skrzynki.
- Wypaczenie może prowadzić do trudności w procesie montażu, ponieważ wpływa na wyrównanie opakowania z innymi komponentami, takimi jak płytka drukowana (PCB). Ta niewspółosiowość może pogorszyć połączenia elektryczne i spowodować problemy z wydajnością.
- Warpage może mieć wpływ na ogólny współczynnik kształtu opakowania, utrudniając integrację urządzenia z aplikacjami o małych rozmiarach lub gęsto zaludnionymi płytkami drukowanymi.
Aby sprostać tym wyzwaniom, w pakowaniu półprzewodników stosuje się różne techniki i strategie. Obejmują one zastosowanie zaawansowanych materiałów o dopasowanych współczynnikach CTE w celu zminimalizowania naprężeń termicznych i wypaczeń. Symulacje termomechaniczne i modelowanie są przeprowadzane w celu przewidywania zachowania opakowania w różnych warunkach termicznych. Modyfikacje projektowe, takie jak wprowadzanie struktur odciążających i zoptymalizowane układy, są wdrażane w celu zmniejszenia naprężeń termicznych i wypaczeń. Ponadto rozwój ulepszonych procesów produkcyjnych i sprzętu pomaga zminimalizować występowanie wypaczeń podczas montażu.
Korzyści z podkładu epoksydowego
Wypełniacz epoksydowy jest kluczowym składnikiem opakowań półprzewodników, który oferuje kilka korzyści. Ten specjalistyczny materiał epoksydowy jest nakładany między chip półprzewodnikowy a podłoże opakowania, zapewniając wzmocnienie mechaniczne i rozwiązując różne problemy. Oto niektóre z najważniejszych zalet niedostatecznie wypełnionej żywicy epoksydowej:
- Poprawiona niezawodność mechaniczna: Jedną z głównych zalet wypełniacza epoksydowego jest jego zdolność do zwiększania niezawodności mechanicznej pakietów półprzewodnikowych. Podkład epoksydowy tworzy spoiste wiązanie, które poprawia ogólną integralność strukturalną, wypełniając luki i puste przestrzenie między chipem a podłożem. Pomaga to zapobiegać wypaczaniu się opakowania, zmniejsza ryzyko awarii mechanicznych i zwiększa odporność na naprężenia zewnętrzne, takie jak wibracje, wstrząsy i cykle termiczne. Poprawiona niezawodność mechaniczna prowadzi do zwiększenia trwałości produktu i dłuższej żywotności urządzenia.
- Rozpraszanie naprężeń termicznych: epoksydowe wypełnienie pomaga rozproszyć naprężenia termiczne w opakowaniu. Układy scalone wytwarzają ciepło podczas pracy, a nieodpowiednie odprowadzanie ciepła może powodować wahania temperatury wewnątrz pojemnika. Materiał epoksydowy wypełniający, o niższym współczynniku rozszerzalności cieplnej (CTE) w porównaniu z materiałami chipa i podłoża, działa jak warstwa buforowa. Absorbuje naprężenia mechaniczne spowodowane naprężeniami termicznymi, zmniejszając ryzyko uszkodzeń połączeń lutowanych, rozwarstwień i pęknięć. Rozpraszając naprężenia termiczne, niedopełniona żywica epoksydowa pomaga zachować integralność elektryczną i mechaniczną opakowania.
- Udoskonalona wydajność elektryczna: Niedopełniona żywica epoksydowa pozytywnie wpływa na parametry elektryczne urządzeń półprzewodnikowych. Materiał epoksydowy wypełnia szczeliny między chipem a podłożem, zmniejszając pasożytniczą pojemność i indukcyjność. Powoduje to lepszą integralność sygnału, mniejsze straty sygnału i lepszą łączność elektryczną między chipem a resztą obudowy. Zmniejszone efekty pasożytnicze przyczyniają się do lepszej wydajności elektrycznej, wyższych szybkości przesyłania danych i zwiększonej niezawodności urządzenia. Ponadto niedopełniona żywica epoksydowa zapewnia izolację i ochronę przed wilgocią, zanieczyszczeniami i innymi czynnikami środowiskowymi, które mogą pogorszyć parametry elektryczne.
- Redukcja naprężeń i ulepszony montaż: Żywica epoksydowa wypełniająca działa jako mechanizm odprężający podczas montażu. Materiał epoksydowy kompensuje niedopasowanie CTE między chipem a podłożem, zmniejszając naprężenia mechaniczne podczas zmian temperatury. Dzięki temu proces montażu jest bardziej niezawodny i wydajny, minimalizując ryzyko uszkodzenia opakowania lub niewspółosiowości. Kontrolowany rozkład naprężeń zapewniany przez wypełniacz epoksydowy pomaga również zapewnić właściwe wyrównanie z innymi komponentami na płytce drukowanej (PCB) i poprawia ogólną wydajność montażu.
- Miniaturyzacja i optymalizacja współczynnika kształtu: żywica epoksydowa Underfill umożliwia miniaturyzację pakietów półprzewodników i optymalizację współczynnika kształtu. Zapewniając wzmocnienie strukturalne i odprężenie, wypełniacz epoksydowy umożliwia projektowanie i produkcję mniejszych, cieńszych i bardziej zwartych opakowań. Jest to szczególnie ważne w przypadku zastosowań takich jak urządzenia mobilne i elektronika ubieralna, w których przestrzeń jest na wagę złota. Zdolność do optymalizacji współczynników kształtu i osiągania wyższych gęstości komponentów przyczynia się do powstawania bardziej zaawansowanych i innowacyjnych urządzeń elektronicznych.
Rodzaje podkładu epoksydowego
W opakowaniach półprzewodników dostępnych jest kilka typów wypełniaczy epoksydowych, z których każdy został zaprojektowany w celu spełnienia określonych wymagań i sprostania różnym wyzwaniom. Oto kilka powszechnie stosowanych rodzajów żywicy epoksydowej wypełniającej:
- Kapilarny wypełniacz epoksydowy: Kapilarny wypełniacz epoksydowy jest najbardziej tradycyjnym i szeroko stosowanym typem. Żywica epoksydowa o niskiej lepkości wpływa do szczeliny między chipem a podłożem poprzez działanie kapilarne. Wypełnienie kapilarne jest zwykle dozowane na krawędzi chipa, a gdy opakowanie jest podgrzewane, żywica epoksydowa przepływa pod chipem, wypełniając puste przestrzenie. Ten rodzaj wypełnienia nadaje się do opakowań z małymi szczelinami i zapewnia dobre wzmocnienie mechaniczne.
- No-Flow Underfill Epoxy: No-Flow Underfill Epoxy jest preparatem o wysokiej lepkości, który nie płynie podczas utwardzania. Jest nakładany jako wstępnie nałożona żywica epoksydowa lub jako film między chipem a podłożem. Niepłynna żywica epoksydowa do wypełnienia jest szczególnie przydatna w przypadku obudów typu flip-chip, w których wypukłości lutownicze wchodzą w bezpośrednią interakcję z podłożem. Eliminuje konieczność przepływu kapilarnego i zmniejsza ryzyko uszkodzenia złącza lutowniczego podczas montażu.
- Podpełnienie na poziomie płytki (WLU): Podpełnienie na poziomie płytki jest wypełniaczem epoksydowym nakładanym na poziomie płytki przed wyodrębnieniem poszczególnych wiórów. Polega na dozowaniu materiału podkładowego na całej powierzchni płytki i utwardzeniu go. Niedopełnienie na poziomie płytki ma kilka zalet, w tym równomierne pokrycie niedopełnienia, skrócony czas montażu i lepszą kontrolę procesu. Jest powszechnie stosowany do produkcji wielkoseryjnej małych urządzeń.
- Formowane wypełnienie (MUF): Formowane wypełnienie jest wypełniaczem epoksydowym nakładanym podczas formowania kapsułkującego. Materiał wypełniający jest dozowany na podłoże, a następnie wiór i podłoże są zamykane w masie do formowania. Podczas formowania żywica epoksydowa przepływa i wypełnia szczelinę między wiórem a podłożem, zapewniając wypełnienie i hermetyzację w jednym kroku. Formowana podkładka zapewnia doskonałe wzmocnienie mechaniczne i upraszcza proces montażu.
- Podkład nieprzewodzący (NCF): Nieprzewodzący wypełniacz epoksydowy jest specjalnie opracowany, aby zapewnić izolację elektryczną między połączeniami lutowanymi na chipie i podłożu. Zawiera wypełniacze izolujące lub dodatki zapobiegające przewodzeniu elektrycznemu. NCF jest używany w aplikacjach, w których problemem są zwarcia elektryczne między sąsiednimi złączami lutowanymi. Zapewnia zarówno wzmocnienie mechaniczne, jak i izolację elektryczną.
- Podkład termoprzewodzący (TCU): Podkład epoksydowy przewodzący ciepło został zaprojektowany w celu zwiększenia możliwości rozpraszania ciepła przez opakowanie. Zawiera wypełniacze przewodzące ciepło, takie jak cząsteczki ceramiki lub metalu, które poprawiają przewodność cieplną materiału wypełniającego. TCU jest używany w aplikacjach, w których kluczowe znaczenie ma wydajne przenoszenie ciepła, takich jak urządzenia o dużej mocy lub pracujące w wymagających środowiskach termicznych.
To tylko kilka przykładów różnych rodzajów wypełniacza epoksydowego stosowanego w opakowaniach półprzewodników. Wybór odpowiedniej żywicy epoksydowej do wypełnienia zależy od takich czynników, jak konstrukcja opakowania, proces montażu, wymagania termiczne i względy elektryczne. Każda żywica epoksydowa do wypełniania oferuje określone korzyści i jest dostosowana do unikalnych potrzeb różnych zastosowań.
Niedopełnienie kapilarne: Niska lepkość i wysoka niezawodność
Wypełnianie kapilarne odnosi się do procesu stosowanego w przemyśle opakowań półprzewodników w celu zwiększenia niezawodności urządzeń elektronicznych. Polega na wypełnianiu szczelin między mikroukładem elektronicznym a otaczającym go opakowaniem płynnym materiałem o niskiej lepkości, zazwyczaj żywicą epoksydową. Ten materiał wypełniający zapewnia wsparcie strukturalne, poprawia odprowadzanie ciepła i chroni chip przed naprężeniami mechanicznymi, wilgocią i innymi czynnikami środowiskowymi.
Jedną z krytycznych cech wypełnienia kapilarnego jest jego niska lepkość. Materiał wypełniający jest tak sformułowany, aby miał stosunkowo niską gęstość, co umożliwia jego łatwy przepływ do wąskich szczelin między chipem a opakowaniem podczas procesu wypełniania. Gwarantuje to, że materiał wypełniający może skutecznie penetrować i wypełniać wszystkie puste przestrzenie i szczeliny powietrzne, minimalizując ryzyko powstawania pustych przestrzeni i poprawiając ogólną integralność interfejsu chip-obudowa.
Materiały do wypełniania kapilarnego o niskiej lepkości mają również kilka innych zalet. Po pierwsze, ułatwiają sprawny przepływ materiału pod wiórem, co prowadzi do skrócenia czasu procesu i zwiększenia przepustowości produkcji. Jest to szczególnie ważne w środowiskach produkcji masowej, w których liczy się oszczędność czasu i kosztów.
Po drugie, niska lepkość zapewnia lepsze właściwości zwilżające i adhezyjne materiału wypełniającego. Pozwala to na równomierne rozprowadzenie materiału i utworzenie mocnych wiązań z chipem i opakowaniem, tworząc niezawodną i solidną hermetyzację. Dzięki temu chip jest bezpiecznie chroniony przed naprężeniami mechanicznymi, takimi jak cykle termiczne, wstrząsy i wibracje.
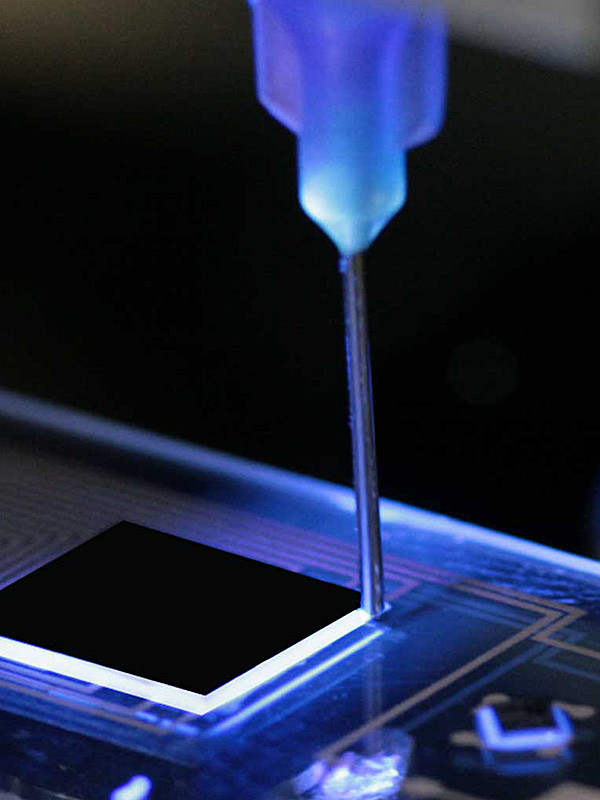
Kolejnym istotnym aspektem wypełniaczy kapilarnych jest ich wysoka niezawodność. Materiały wypełniające o niskiej lepkości zostały specjalnie zaprojektowane, aby wykazywać doskonałą stabilność termiczną, właściwości izolacji elektrycznej oraz odporność na wilgoć i chemikalia. Cechy te są niezbędne do zapewnienia długoterminowej wydajności i niezawodności zapakowanych urządzeń elektronicznych, szczególnie w wymagających zastosowaniach, takich jak motoryzacja, lotnictwo i telekomunikacja.
Ponadto materiały wypełniające kapilary są zaprojektowane tak, aby miały wysoką wytrzymałość mechaniczną i doskonałą przyczepność do różnych materiałów podłoża, w tym metali, ceramiki i materiałów organicznych powszechnie stosowanych w opakowaniach półprzewodników. Dzięki temu materiał podkładowy działa jak bufor naprężeń, skutecznie absorbując i rozpraszając naprężenia mechaniczne powstające podczas pracy lub narażenia na środowisko.
Nieprzepływowe niedopełnienie: Samodozowanie i wysoka przepustowość
Podpełnianie bez przepływu to wyspecjalizowany proces stosowany w przemyśle opakowań półprzewodników w celu zwiększenia niezawodności i wydajności urządzeń elektronicznych. W przeciwieństwie do wypełniaczy kapilarnych, które opierają się na przepływie materiałów o niskiej lepkości, wypełniacze bez przepływu wykorzystują podejście samodozujące z materiałami o wysokiej lepkości. Ta metoda oferuje kilka zalet, w tym samoczynne wyrównywanie, wysoką przepustowość i zwiększoną niezawodność.
Jedną z krytycznych cech niedopełnienia bez przepływu jest jego zdolność do samoczynnego dozowania. Materiał podkładowy stosowany w tym procesie ma wyższą lepkość, co zapobiega jego swobodnemu przepływowi. Zamiast tego materiał wypełniający jest dozowany na powierzchnię styku opakowania chipa w kontrolowany sposób. To kontrolowane dozowanie umożliwia precyzyjne umieszczenie materiału wypełniającego, zapewniając, że jest on nakładany tylko na żądane obszary bez przelewania lub niekontrolowanego rozprzestrzeniania się.
Samodozujący charakter wypełnienia bez przepływu oferuje kilka korzyści. Po pierwsze, pozwala na samoczynne ułożenie materiału podsypki. Podczas dozowania podkładka w naturalny sposób dopasowuje się do chipa i opakowania, równomiernie wypełniając szczeliny i puste przestrzenie. Eliminuje to potrzebę precyzyjnego pozycjonowania i wyrównywania wiórów podczas procesu uzupełniania, oszczędzając czas i wysiłek w produkcji.
Po drugie, funkcja samodozowania niedopełnień bez przepływu umożliwia wysoką przepustowość produkcji. Proces dozowania można zautomatyzować, co pozwala na szybkie i konsekwentne nakładanie materiału podkładowego na wiele wiórów jednocześnie. Poprawia to ogólną wydajność produkcji i obniża koszty produkcji, co czyni ją szczególnie korzystną w środowiskach produkcyjnych o dużej objętości.
Ponadto nieprzepływające materiały wypełniające zapewniają wysoką niezawodność. Materiały wypełniające o wysokiej lepkości zapewniają lepszą odporność na cykle termiczne, naprężenia mechaniczne i czynniki środowiskowe, zapewniając długotrwałą wydajność zapakowanych urządzeń elektronicznych. Materiały wykazują doskonałą stabilność termiczną, właściwości izolacji elektrycznej oraz odporność na wilgoć i chemikalia, przyczyniając się do ogólnej niezawodności urządzeń.
Ponadto materiały wypełniające o dużej lepkości stosowane w wypełniaczach niepłynących mają zwiększoną wytrzymałość mechaniczną i właściwości adhezyjne. Tworzą silne wiązania z chipem i obudową, skutecznie pochłaniając i rozpraszając naprężenia mechaniczne powstające podczas pracy lub narażenia na środowisko. Pomaga to chronić chip przed potencjalnym uszkodzeniem i zwiększa odporność urządzenia na zewnętrzne wstrząsy i wibracje.
Formowane wypełnienie: wysoka ochrona i integracja
Formowane wypełnienie to zaawansowana technika stosowana w przemyśle opakowań półprzewodników w celu zapewnienia wysokiego poziomu ochrony i integracji urządzeń elektronicznych. Polega na hermetyzacji całego chipa i otaczającego go opakowania za pomocą masy formy zawierającej materiał wypełniający. Proces ten oferuje znaczące korzyści w zakresie ochrony, integracji i ogólnej niezawodności.
Jedną z najważniejszych zalet formowanego wypełniacza jest jego zdolność do zapewnienia kompleksowej ochrony chipa. Mieszanka formy stosowana w tym procesie działa jak solidna bariera, otaczając cały chip i opakowanie ochronną powłoką. Zapewnia to skuteczną ochronę przed czynnikami środowiskowymi, takimi jak wilgoć, kurz i zanieczyszczenia, które mogą mieć wpływ na wydajność i niezawodność urządzenia. Hermetyzacja pomaga również chronić chip przed naprężeniami mechanicznymi, cyklami termicznymi i innymi siłami zewnętrznymi, zapewniając jego długoterminową trwałość.
Dodatkowo formowane wypełnienie umożliwia wysoki poziom integracji w obudowie półprzewodników. Materiał wypełniający jest mieszany bezpośrednio z mieszanką formy, co pozwala na bezproblemową integrację procesów wypełniania i hermetyzacji. Ta integracja eliminuje potrzebę osobnego etapu wypełniania, upraszczając proces produkcyjny i redukując czas i koszty produkcji. Zapewnia również spójną i równomierną dystrybucję podkładu w całym opakowaniu, minimalizując puste przestrzenie i wzmacniając ogólną integralność strukturalną.
Ponadto formowane wypełnienie zapewnia doskonałe właściwości odprowadzania ciepła. Mieszanka formy została zaprojektowana tak, aby miała wysoką przewodność cieplną, umożliwiając efektywne odprowadzanie ciepła z chipa. Ma to kluczowe znaczenie dla utrzymania optymalnej temperatury roboczej urządzenia i zapobiegania przegrzaniu, które może prowadzić do pogorszenia wydajności i problemów z niezawodnością. Ulepszone właściwości rozpraszania ciepła formowanego wypełniacza przyczyniają się do ogólnej niezawodności i trwałości urządzenia elektronicznego.
Ponadto formowane wypełnienie umożliwia większą miniaturyzację i optymalizację współczynnika kształtu. Proces enkapsulacji można dostosować do różnych rozmiarów i kształtów opakowań, w tym złożonych struktur 3D. Ta elastyczność pozwala na integrację wielu układów scalonych i innych komponentów w kompaktowej, zajmującej niewiele miejsca obudowie. Zdolność do osiągania wyższych poziomów integracji bez uszczerbku dla niezawodności sprawia, że formowane wypełniacze są szczególnie cenne w zastosowaniach, w których ograniczenia rozmiaru i wagi mają krytyczne znaczenie, takich jak urządzenia mobilne, urządzenia do noszenia i elektronika samochodowa.
Chip Scale Package (CSP) Niedopełnienie: miniaturyzacja i wysoka gęstość
Chip Scale Package (CSP) underfill to kluczowa technologia umożliwiająca miniaturyzację i integrację urządzeń elektronicznych o dużej gęstości. W miarę zmniejszania się rozmiarów urządzeń elektronicznych przy jednoczesnym zwiększaniu funkcjonalności, CSP nie spełnia kluczowej roli w zapewnianiu niezawodności i wydajności tych kompaktowych urządzeń.
CSP to technologia pakowania, która umożliwia bezpośredni montaż układu półprzewodnikowego na podłożu lub płytce drukowanej (PCB) bez konieczności stosowania dodatkowego opakowania. Eliminuje to konieczność stosowania tradycyjnego plastikowego lub ceramicznego pojemnika, zmniejszając całkowity rozmiar i wagę urządzenia. CSP underfill to proces, w którym do wypełnienia szczeliny między chipem a podłożem stosuje się płyn lub materiał kapsułkujący, zapewniając mechaniczne wsparcie i chroniąc chip przed czynnikami środowiskowymi, takimi jak wilgoć i naprężenia mechaniczne.
Miniaturyzacja jest osiągana poprzez niedopełnienie CSP poprzez zmniejszenie odległości między chipem a podłożem. Materiał podkładowy wypełnia wąską szczelinę między wiórem a podłożem, tworząc solidne wiązanie i poprawiając stabilność mechaniczną wióra. Pozwala to na mniejsze i cieńsze urządzenia, dzięki czemu możliwe jest spakowanie większej funkcjonalności w ograniczonej przestrzeni.
Integracja o dużej gęstości to kolejna zaleta niedopełnienia CSP. Eliminując potrzebę stosowania osobnej obudowy, CSP umożliwia montaż chipa bliżej innych komponentów na płytce drukowanej, zmniejszając długość połączeń elektrycznych i poprawiając integralność sygnału. Materiał wypełniający działa również jako przewodnik ciepła, wydajnie rozpraszając ciepło wytwarzane przez chip. Ta zdolność zarządzania termicznego pozwala na wyższe gęstości mocy, umożliwiając integrację bardziej złożonych i mocniejszych układów scalonych z urządzeniami elektronicznymi.
Materiały wypełniające CSP muszą posiadać określone właściwości, aby sprostać wymaganiom miniaturyzacji i integracji o dużej gęstości. Muszą mieć niską lepkość, aby ułatwić wypełnianie wąskich szczelin, a także doskonałe właściwości płynięcia, aby zapewnić równomierne pokrycie i wyeliminować puste przestrzenie. Materiały powinny również charakteryzować się dobrą przyczepnością do wióra i podłoża, zapewniając solidne wsparcie mechaniczne. Dodatkowo muszą wykazywać wysoką przewodność cieplną, aby skutecznie odprowadzać ciepło z chipa.
Niedopełnienie CSP na poziomie płytki: opłacalne i o dużej wydajności
Niedopełnianie opakowań zgorzelinowych na poziomie płytki (WLCSP) jest opłacalną i wysokowydajną techniką pakowania, która oferuje kilka korzyści w zakresie wydajności produkcji i ogólnej jakości produktu. Underfill WLCSP nakłada materiał underfill na wiele chipów jednocześnie, wciąż w formie płytki, zanim zostaną one podzielone na pojedyncze opakowania. Takie podejście oferuje liczne korzyści w zakresie redukcji kosztów, lepszej kontroli procesu i wyższych wydajności produkcji.
Jedną z krytycznych zalet wypełniania WLCSP jest jego opłacalność. Zastosowanie materiału wypełniającego na poziomie wafla usprawnia i usprawnia proces pakowania. Niewypełniony materiał jest dozowany na płytkę przy użyciu kontrolowanego i zautomatyzowanego procesu, co zmniejsza straty materiału i minimalizuje koszty pracy. Ponadto wyeliminowanie poszczególnych etapów obsługi i wyrównywania opakowań skraca całkowity czas i złożoność produkcji, co skutkuje znacznymi oszczędnościami kosztów w porównaniu z tradycyjnymi metodami pakowania.
Ponadto wypełnienie WLCSP zapewnia lepszą kontrolę procesu i wyższą wydajność produkcji. Ponieważ materiał wypełniający jest nakładany na poziomie płytki, umożliwia lepszą kontrolę nad procesem dozowania, zapewniając spójne i równomierne pokrycie podkładu dla każdego chipa na płytce. Zmniejsza to ryzyko pustych przestrzeni lub niepełnego wypełnienia, co może prowadzić do problemów z niezawodnością. Możliwość kontroli i testowania jakości niedopełnienia na poziomie płytki umożliwia również wczesne wykrywanie defektów lub odchyleń procesu, umożliwiając podjęcie działań naprawczych w odpowiednim czasie i zmniejszając prawdopodobieństwo wadliwych opakowań. W rezultacie niedopełnienie WLCSP pomaga osiągnąć wyższą wydajność produkcji i lepszą ogólną jakość produktu.
Podejście na poziomie płytki umożliwia również lepszą wydajność termiczną i mechaniczną. Materiałem wypełniającym stosowanym w WLCSP jest zwykle materiał o niskiej lepkości, płynący kapilarnie, który może skutecznie wypełnić wąskie szczeliny między wiórami a płytką. Zapewnia to solidne mechaniczne wsparcie chipów, zwiększając ich odporność na naprężenia mechaniczne, wibracje i cykliczne zmiany temperatury. Dodatkowo materiał wypełniający działa jak przewodnik ciepła, ułatwiając odprowadzanie ciepła wytwarzanego przez wióry, poprawiając w ten sposób zarządzanie ciepłem i zmniejszając ryzyko przegrzania.
Flip Chip Underfill: Wysoka gęstość I/O i wydajność
Flip chip underfill to kluczowa technologia, która zapewnia wysoką gęstość wejścia/wyjścia (I/O) i wyjątkową wydajność urządzeń elektronicznych. Odgrywa kluczową rolę w zwiększaniu niezawodności i funkcjonalności opakowań typu flip-chip, które są szeroko stosowane w zaawansowanych zastosowaniach półprzewodnikowych. W tym artykule zbadamy znaczenie niedopełnienia flip chipa i jego wpływ na osiągnięcie wysokiej gęstości we/wy i wydajności.
Technologia Flip Chip polega na bezpośrednim połączeniu elektrycznym układu scalonego (IC) lub matrycy półprzewodnikowej z podłożem, eliminując potrzebę łączenia przewodów. Skutkuje to bardziej zwartą i wydajną obudową, ponieważ podkładki we/wy znajdują się na dolnej powierzchni matrycy. Jednak opakowania typu flip-chip stanowią wyjątkowe wyzwania, którym należy sprostać, aby zapewnić optymalną wydajność i niezawodność.
Jednym z krytycznych wyzwań w pakowaniu typu flip chip jest zapobieganie naprężeniom mechanicznym i niedopasowaniu termicznemu między matrycą a podłożem. Podczas procesu produkcyjnego i późniejszej eksploatacji różnice we współczynnikach rozszerzalności cieplnej (CTE) między matrycą a podłożem mogą powodować znaczne naprężenia, prowadzące do pogorszenia wydajności lub nawet awarii. Flip chip underfill to materiał ochronny, który otacza chip, zapewniając mechaniczne wsparcie i odciążenie. Skutecznie rozkłada naprężenia powstające podczas cykli termicznych i zapobiega ich oddziaływaniu na delikatne interkonekty.
Wysoka gęstość we/wy ma kluczowe znaczenie w nowoczesnych urządzeniach elektronicznych, w których niezbędne są mniejsze rozmiary i zwiększona funkcjonalność. Flip chip underfill umożliwia wyższą gęstość we/wy, oferując doskonałą izolację elektryczną i możliwości zarządzania termicznego. Materiał wypełniający wypełnia szczelinę między matrycą a podłożem, tworząc solidne połączenie i zmniejszając ryzyko zwarć lub upływu prądu. Pozwala to na bliższe rozmieszczenie padów we/wy, co skutkuje zwiększoną gęstością we/wy bez utraty niezawodności.
Ponadto wypełnienie typu flip chip przyczynia się do poprawy parametrów elektrycznych. Minimalizuje elektryczne pasożyty między matrycą a podłożem, zmniejszając opóźnienie sygnału i poprawiając integralność sygnału. Materiał wypełniający wykazuje również doskonałe właściwości przewodzenia ciepła, wydajnie odprowadzając ciepło wytwarzane przez chip podczas pracy. Efektywne odprowadzanie ciepła zapewnia utrzymanie temperatury w dopuszczalnych granicach, zapobiegając przegrzaniu i utrzymując optymalną wydajność.
Postępy w materiałach wypełniających typu flip-chip umożliwiły jeszcze większą gęstość wejść/wyjść i poziomy wydajności. Na przykład wypełniacze nanokompozytowe wykorzystują wypełniacze w skali nano, aby poprawić przewodność cieplną i wytrzymałość mechaniczną. Pozwala to na lepsze odprowadzanie ciepła i niezawodność, umożliwiając urządzenia o wyższej wydajności.
Wypełnienie Ball Grid Array (BGA): Wysoka wydajność termiczna i mechaniczna
Ball Grid Array (BGA) nie wypełnia krytycznej technologii oferującej wysoką wydajność termiczną i mechaniczną w urządzeniach elektronicznych. Odgrywa kluczową rolę w zwiększaniu niezawodności i funkcjonalności pakietów BGA, które są szeroko stosowane w różnych aplikacjach. W tym artykule zbadamy znaczenie niedopełnienia BGA i jego wpływ na osiągnięcie wysokiej wydajności termicznej i mechanicznej.
Technologia BGA obejmuje konstrukcję obudowy, w której układ scalony (IC) lub matryca półprzewodnikowa jest zamontowana na podłożu, a połączenia elektryczne są wykonywane przez szereg kulek lutowniczych umieszczonych na dolnej powierzchni obudowy. BGA wypełnia materiał dozowany w szczelinie między matrycą a podłożem, otaczając kulki lutownicze i zapewniając mechaniczne wsparcie i ochronę zespołu.
Jednym z krytycznych wyzwań w opakowaniach BGA jest zarządzanie naprężeniami termicznymi. Podczas pracy układ scalony wytwarza ciepło, a rozszerzanie się i kurczenie termiczne może powodować znaczny nacisk na połączenia lutowane łączące matrycę z podłożem. BGA nie pełni kluczowej roli w łagodzeniu tych naprężeń, tworząc solidne wiązanie z matrycą i podłożem. Działa jako bufor naprężeń, pochłaniając rozszerzalność cieplną i kurczenie się oraz zmniejszając obciążenie połączeń lutowanych. Pomaga to poprawić ogólną niezawodność pakietu i zmniejsza ryzyko awarii połączeń lutowanych.
Innym krytycznym aspektem wypełnienia BGA jest jego zdolność do zwiększania wydajności mechanicznej obudowy. Pakiety BGA są często poddawane naprężeniom mechanicznym podczas przenoszenia, montażu i eksploatacji. Materiał wypełniający wypełnia szczelinę między matrycą a podłożem, zapewniając strukturalne wsparcie i wzmocnienie połączeń lutowanych. Poprawia to ogólną wytrzymałość mechaniczną zespołu, czyniąc go bardziej odpornym na wstrząsy mechaniczne, wibracje i inne siły zewnętrzne. Skutecznie rozkładając naprężenia mechaniczne, niedopełnienie BGA pomaga zapobiegać pękaniu obudowy, rozwarstwianiu lub innym awariom mechanicznym.
Wysoka wydajność cieplna jest niezbędna w urządzeniach elektronicznych do zapewnienia właściwej funkcjonalności i niezawodności. Materiały wypełniające BGA zostały zaprojektowane tak, aby miały doskonałe właściwości przewodnictwa cieplnego. Pozwala im to skutecznie odprowadzać ciepło z matrycy i rozprowadzać je po podłożu, poprawiając ogólne zarządzanie termiczne opakowania. Skuteczne odprowadzanie ciepła pomaga utrzymać niższe temperatury pracy, zapobiegając powstawaniu gorących punktów termicznych i potencjalnemu spadkowi wydajności. Przyczynia się również do długowieczności pudełka, zmniejszając naprężenia termiczne komponentów.
Postępy w materiałach wypełniających BGA doprowadziły do jeszcze wyższej wydajności termicznej i mechanicznej. Udoskonalone formuły i materiały wypełniające, takie jak nanokompozyty lub wypełniacze o wysokiej przewodności cieplnej, umożliwiły lepsze odprowadzanie ciepła i wytrzymałość mechaniczną, dodatkowo zwiększając wydajność pakietów BGA.
Niedopełnienie pakietu Quad Flat Package (QFP): duża liczba wejść/wyjść i solidność
Quad Flat Package (QFP) to pakiet układów scalonych (IC) szeroko stosowany w elektronice. Ma kwadratowy lub prostokątny kształt z wyprowadzeniami wystającymi ze wszystkich czterech stron, zapewniając wiele połączeń wejścia/wyjścia (I/O). Aby zwiększyć niezawodność i wytrzymałość opakowań QFP, powszechnie stosuje się materiały wypełniające.
Underfill to materiał ochronny nakładany między układ scalony a podłoże w celu wzmocnienia wytrzymałości mechanicznej połączeń lutowanych i zapobiegania awariom spowodowanym naprężeniami. Jest to szczególnie istotne w przypadku QFP z dużą liczbą wejść/wyjść, ponieważ duża liczba połączeń może prowadzić do znacznych naprężeń mechanicznych podczas cykli termicznych i warunków operacyjnych.
Materiał wypełniający stosowany w opakowaniach QFP musi posiadać określone właściwości, aby zapewnić solidność. Po pierwsze, powinien mieć doskonałą przyczepność zarówno do układu scalonego, jak i do podłoża, aby stworzyć silne wiązanie i zminimalizować ryzyko rozwarstwienia lub oderwania. Ponadto powinien mieć niski współczynnik rozszerzalności cieplnej (CTE), aby dopasować się do CTE układu scalonego i podłoża, zmniejszając niedopasowanie naprężeń, które może prowadzić do pęknięć lub złamań.
Ponadto materiał wypełniający powinien mieć dobre właściwości płynięcia, aby zapewnić równomierne pokrycie i całkowite wypełnienie szczeliny między układem scalonym a podłożem. Pomaga to wyeliminować puste przestrzenie, które mogą osłabić połączenia lutowane i spowodować zmniejszenie niezawodności. Materiał powinien również charakteryzować się dobrymi właściwościami utwardzania, pozwalającymi na tworzenie sztywnej i trwałej warstwy ochronnej po aplikacji.
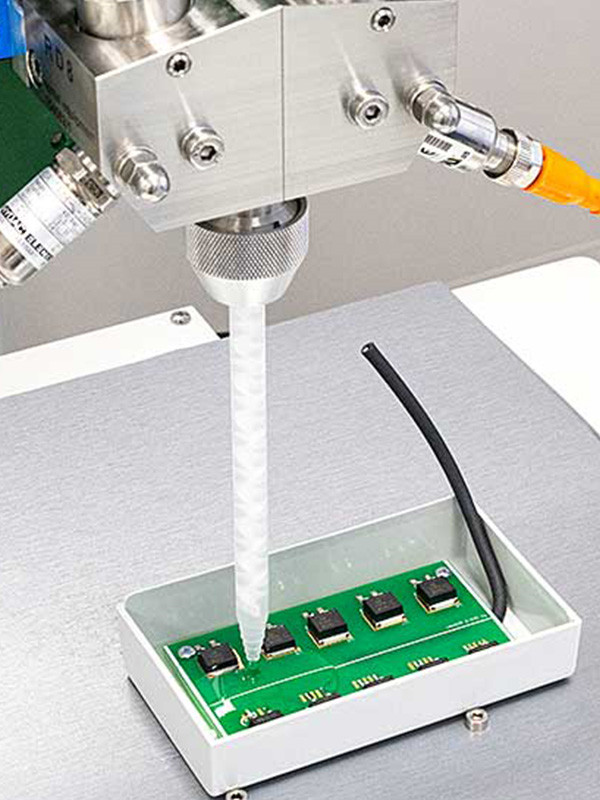
Jeśli chodzi o wytrzymałość mechaniczną, wypełnienie powinno charakteryzować się wysoką wytrzymałością na ścinanie i oddzieranie, aby wytrzymać siły zewnętrzne i zapobiegać deformacji lub rozwarstwieniu opakowania. Powinien również wykazywać dobrą odporność na wilgoć i inne czynniki środowiskowe, aby zachować swoje właściwości ochronne w czasie. Jest to szczególnie ważne w zastosowaniach, w których obudowa QFP może być narażona na trudne warunki lub wahania temperatury.
Dostępne są różne materiały wypełniające, w tym preparaty na bazie żywic epoksydowych, umożliwiające osiągnięcie tych pożądanych właściwości. W zależności od specyficznych wymagań aplikacji, materiały te mogą być dozowane przy użyciu różnych technik, takich jak przepływ kapilarny, natryskiwanie lub sitodruk.
Niedopełnienie systemu w pakiecie (SiP): integracja i wydajność
System-in-Package (SiP) to zaawansowana technologia pakowania integrująca wiele układów półprzewodnikowych, komponentów pasywnych i innych elementów w jednym opakowaniu. SiP oferuje liczne korzyści, w tym zmniejszony współczynnik kształtu, lepszą wydajność elektryczną i rozszerzoną funkcjonalność. Aby zapewnić niezawodność i wydajność zespołów SiP, powszechnie stosuje się materiały wypełniające.
Niedopełnienie w zastosowaniach SiP ma kluczowe znaczenie dla zapewnienia stabilności mechanicznej i łączności elektrycznej między różnymi komponentami w pakiecie. Pomaga to zminimalizować ryzyko awarii wywołanych naprężeniami, takich jak pęknięcia lub pęknięcia połączeń lutowanych, które mogą wystąpić z powodu różnic we współczynnikach rozszerzalności cieplnej (CTE) między komponentami.
Integracja wielu komponentów w pakiecie SiP prowadzi do złożonych wzajemnych połączeń, z wieloma złączami lutowanymi i obwodami o dużej gęstości. Materiały wypełniające pomagają wzmocnić te połączenia, zwiększając wytrzymałość mechaniczną i niezawodność zespołu. Wspierają połączenia lutowane, zmniejszając ryzyko zmęczenia lub uszkodzeń spowodowanych cyklami termicznymi lub obciążeniami mechanicznymi.
Jeśli chodzi o parametry elektryczne, materiały wypełniające mają kluczowe znaczenie dla poprawy integralności sygnału i minimalizacji szumów elektrycznych. Wypełniając luki między komponentami i zmniejszając odległość między nimi, underfill pomaga zmniejszyć pasożytniczą pojemność i indukcyjność, umożliwiając szybszą i bardziej wydajną transmisję sygnału.
Ponadto materiały wypełniające do zastosowań SiP powinny mieć doskonałą przewodność cieplną, aby wydajnie rozpraszać ciepło wytwarzane przez zintegrowane komponenty. Skuteczne odprowadzanie ciepła jest niezbędne, aby zapobiec przegrzaniu i utrzymać ogólną niezawodność i wydajność zespołu SiP.
Materiały wypełniające w opakowaniach SiP muszą mieć określone właściwości, aby spełnić te wymagania dotyczące integracji i wydajności. Powinny mieć dobrą rozlewność, aby zapewnić całkowite pokrycie i wypełnienie szczelin między składnikami. Materiał wypełniający powinien również mieć formułę o niskiej lepkości, aby umożliwić łatwe dozowanie i wypełnianie wąskich otworów lub małych przestrzeni.
Ponadto materiał wypełniający powinien wykazywać silną przyczepność do różnych powierzchni, w tym chipów półprzewodnikowych, podłoży i materiałów pasywnych, aby zapewnić niezawodne wiązanie. Powinien być kompatybilny z różnymi materiałami opakowaniowymi, takimi jak podłoża organiczne czy ceramika, oraz wykazywać dobre właściwości mechaniczne, w tym wysoką wytrzymałość na ścinanie i oddzieranie.
Wybór materiału wypełniającego i metody aplikacji zależy od konkretnego projektu SiP, wymagań dotyczących komponentów i procesów produkcyjnych. Techniki dozowania, takie jak przepływ kapilarny, natryskiwanie lub metody wspomagane filmem, powszechnie stosują niedopełnienie w zespołach SiP.
Niedopełnienie optoelektroniki: wyrównanie optyczne i ochrona
Wypełnienie optoelektroniczne obejmuje hermetyzację i ochronę urządzeń optoelektronicznych przy jednoczesnym zapewnieniu precyzyjnego wyrównania optycznego. Urządzenia optoelektroniczne, takie jak lasery, fotodetektory i przełączniki optyczne, często wymagają delikatnego ustawienia elementów optycznych w celu uzyskania optymalnej wydajności. Jednocześnie muszą być chronione przed czynnikami środowiskowymi, które mogłyby wpłynąć na ich funkcjonalność. Podpełnienie optoelektroniczne spełnia oba te wymagania, zapewniając optyczne wyrównanie i ochronę w jednym procesie.
Wyrównanie optyczne jest kluczowym aspektem produkcji urządzeń optoelektronicznych. Polega na dopasowaniu elementów wizualnych, takich jak światłowody, falowody, soczewki lub siatki, w celu zapewnienia wydajnej transmisji i odbioru światła. Dokładne wyrównanie jest konieczne, aby zmaksymalizować wydajność urządzenia i zachować integralność sygnału. Tradycyjne techniki wyrównywania obejmują wyrównywanie ręczne przy użyciu kontroli wzrokowej lub wyrównywanie automatyczne przy użyciu etapów wyrównywania. Jednak metody te mogą być czasochłonne, pracochłonne i podatne na błędy.
Optoelektronika niedopełnia innowacyjne rozwiązanie, wprowadzając funkcje wyrównujące bezpośrednio do materiału wypełniającego. Materiały wypełniające to zazwyczaj płynne lub półpłynne związki, które mogą płynąć i wypełniać szczeliny między elementami optycznymi. Dzięki dodaniu elementów wyrównujących, takich jak mikrostruktury lub znaki odniesienia, w materiale wypełniającym, proces wyrównywania można uprościć i zautomatyzować. Cechy te działają jak prowadnice podczas montażu, zapewniając precyzyjne wyrównanie elementów optycznych bez konieczności wykonywania skomplikowanych procedur ustawiania.
Oprócz wyrównania optycznego, materiały wypełniające chronią urządzenia optoelektroniczne. Komponenty optoelektroniczne są często narażone na trudne warunki środowiskowe, w tym wahania temperatury, wilgoć i obciążenia mechaniczne. Te czynniki zewnętrzne mogą z czasem obniżyć wydajność i niezawodność urządzeń. Materiały wypełniające działają jak bariera ochronna, otaczając elementy optyczne i chroniąc je przed zanieczyszczeniami środowiskowymi. Zapewniają również wzmocnienie mechaniczne, zmniejszając ryzyko uszkodzeń w wyniku wstrząsów lub wibracji.
Materiały wypełniające stosowane w zastosowaniach optoelektronicznych są zwykle zaprojektowane tak, aby miały niski współczynnik załamania światła i doskonałą przezroczystość optyczną. Zapewnia to minimalne zakłócenia sygnałów optycznych przechodzących przez urządzenie. Dodatkowo wykazują dobrą przyczepność do różnych podłoży i mają niskie współczynniki rozszerzalności cieplnej, aby zminimalizować naprężenia urządzenia podczas cykli termicznych.
Proces wypełniania polega na dozowaniu materiału wypełniającego na urządzenie, umożliwieniu mu przepływu i wypełnieniu szczelin między elementami optycznymi, a następnie utwardzeniu go w celu utworzenia stałej kapsułki. W zależności od konkretnego zastosowania materiał wypełniający można nakładać różnymi technikami, takimi jak przepływ kapilarny, dozowanie strumieniowe lub sitodruk. Proces utwardzania można osiągnąć za pomocą ciepła, promieniowania UV lub obu.
Niedopełnienie elektroniki medycznej: biokompatybilność i niezawodność
Elektronika medyczna nie wypełnia specjalistycznego procesu, który obejmuje hermetyzację i ochronę komponentów elektronicznych używanych w urządzeniach medycznych. Urządzenia te odgrywają kluczową rolę w różnych zastosowaniach medycznych, takich jak urządzenia do implantacji, sprzęt diagnostyczny, systemy monitorowania i systemy dostarczania leków. Niedopełnienie elektroniki medycznej koncentruje się na dwóch krytycznych aspektach: biokompatybilności i niezawodności.
Biokompatybilność to podstawowy wymóg stawiany wyrobom medycznym, które mają kontakt z ludzkim ciałem. Materiały wypełniające stosowane w elektronice medycznej muszą być biokompatybilne, co oznacza, że nie powinny powodować szkodliwych skutków ani niepożądanych reakcji w kontakcie z żywą tkanką lub płynami ustrojowymi. Materiały te powinny być zgodne z surowymi przepisami i normami, takimi jak ISO 10993, która określa procedury testowania i oceny biokompatybilności.
Materiały podkładowe do elektroniki medycznej są starannie dobierane lub formułowane w celu zapewnienia biokompatybilności. Zostały zaprojektowane tak, aby były nietoksyczne, niedrażniące i niealergizujące. Materiały te nie powinny wydzielać żadnych szkodliwych substancji ani ulegać degradacji w miarę upływu czasu, ponieważ może to prowadzić do uszkodzenia tkanek lub stanu zapalnego. Biokompatybilne materiały wypełniające mają również niską nasiąkliwość, co zapobiega rozwojowi bakterii lub grzybów, które mogą powodować infekcje.
Niezawodność to kolejny krytyczny aspekt niedopełnienia elektroniki medycznej. Urządzenia medyczne często pracują w trudnych warunkach, takich jak ekstremalne temperatury, wilgoć, płyny ustrojowe i obciążenia mechaniczne. Materiały wypełniające muszą chronić elementy elektroniczne, zapewniając ich długotrwałą niezawodność i funkcjonalność. Niezawodność ma ogromne znaczenie w zastosowaniach medycznych, w których awaria urządzenia może poważnie wpłynąć na bezpieczeństwo i samopoczucie pacjentów.
Materiały podkładowe do elektroniki medycznej powinny charakteryzować się wysoką odpornością na wilgoć i chemikalia, aby wytrzymać narażenie na płyny ustrojowe lub procesy sterylizacji. Powinny również wykazywać dobrą przyczepność do różnych podłoży, zapewniając bezpieczne hermetyzowanie elementów elektronicznych. Właściwości mechaniczne, takie jak niski współczynnik rozszerzalności cieplnej i dobra odporność na wstrząsy, mają kluczowe znaczenie dla zminimalizowania naprężeń detali podczas cykli termicznych lub automatycznego załadunku.
Proces niedopełniania elektroniki medycznej obejmuje:
- Dozowanie materiału wypełniającego na elementy elektroniczne.
- Uzupełnianie braków.
- Utwardzanie go w celu utworzenia ochronnej i mechanicznie stabilnej kapsułki.
Należy zachować ostrożność, aby zapewnić pełne pokrycie funkcji i brak pustych przestrzeni lub kieszeni powietrznych, które mogłyby zagrozić niezawodności urządzenia.
Ponadto podczas niedopełniania urządzeń medycznych brane są pod uwagę dodatkowe kwestie. Na przykład materiał wypełniający powinien być zgodny z metodami sterylizacji stosowanymi w urządzeniu. Niektóre materiały mogą być wrażliwe na określone techniki sterylizacji, takie jak para wodna, tlenek etylenu lub promieniowanie, i może być konieczne wybranie materiałów alternatywnych.
Niedopełnienie elektroniki lotniczej: odporność na wysokie temperatury i wibracje
Elektronika lotnicza nie wypełnia specjalistycznego procesu hermetyzacji i ochrony komponentów elektronicznych w zastosowaniach lotniczych. Środowiska lotnicze stwarzają wyjątkowe wyzwania, w tym wysokie temperatury, ekstremalne wibracje i obciążenia mechaniczne. Dlatego niedopełnienie elektroniki lotniczej koncentruje się na dwóch kluczowych aspektach: odporności na wysokie temperatury i odporności na wibracje.
Odporność na wysokie temperatury jest najważniejsza w elektronice lotniczej ze względu na podwyższone temperatury występujące podczas pracy. Materiały wypełniające stosowane w zastosowaniach lotniczych muszą wytrzymać te wysokie temperatury bez uszczerbku dla wydajności i niezawodności elementów elektronicznych. Powinny wykazywać minimalną rozszerzalność cieplną i pozostawać stabilne w szerokim zakresie temperatur.
Materiały podkładowe do elektroniki lotniczej są wybierane lub opracowywane pod kątem wysokich temperatur zeszklenia (Tg) i stabilności termicznej. Wysoka Tg zapewnia, że materiał zachowuje swoje właściwości mechaniczne w podwyższonych temperaturach, zapobiegając deformacji lub utracie przyczepności. Materiały te mogą wytrzymać ekstremalne temperatury, takie jak podczas startu, ponownego wejścia w atmosferę lub pracy w gorących komorach silnika.
Dodatkowo materiały podkładowe do elektroniki lotniczej powinny charakteryzować się niskimi współczynnikami rozszerzalności cieplnej (CTE). CTE mierzy, jak bardzo materiał rozszerza się lub kurczy pod wpływem zmian temperatury. Dzięki niskiemu współczynnikowi CTE materiały wypełniające mogą zminimalizować obciążenie elementów elektronicznych spowodowane cyklami termicznymi, które mogą prowadzić do uszkodzeń mechanicznych lub zmęczenia złącza lutowniczego.
Odporność na wibracje to kolejny krytyczny wymóg dotyczący niedopełnienia elektroniki lotniczej. Pojazdy lotnicze podlegają różnym wibracjom, w tym silnikowi, wibracjom wywołanym lotem i wstrząsom mechanicznym podczas startu lub lądowania. Wibracje te mogą zagrozić wydajności i niezawodności elementów elektronicznych, jeśli nie są odpowiednio chronione.
Materiały podkładowe stosowane w elektronice lotniczej powinny wykazywać doskonałe właściwości tłumienia drgań. Powinny pochłaniać i rozpraszać energię generowaną przez wibracje, zmniejszając naprężenia i obciążenie elementów elektronicznych. Pomaga to zapobiegać powstawaniu pęknięć, złamań lub innych uszkodzeń mechanicznych spowodowanych nadmiernym narażeniem na wibracje.
Ponadto w zastosowaniach lotniczych preferowane są materiały podkładowe o wysokiej przyczepności i wytrzymałości kohezyjnej. Te właściwości zapewniają, że materiał wypełniający pozostaje mocno związany z komponentami elektronicznymi i podłożem, nawet w warunkach ekstremalnych wibracji. Silna adhezja zapobiega rozwarstwianiu się lub oddzielaniu materiału wypełniającego od elementów, zachowując integralność hermetyzacji i chroniąc przed wnikaniem wilgoci lub zanieczyszczeń.
Proces wypełniania podkładu w elektronice lotniczej zazwyczaj polega na dozowaniu materiału wypełniającego na elementy elektroniczne, umożliwieniu mu przepływu i wypełnieniu szczelin, a następnie utwardzeniu go w celu utworzenia solidnej kapsułki. Proces utwardzania można przeprowadzić metodami utwardzania termicznego lub UV, w zależności od specyficznych wymagań aplikacji.
Niedopełnienie elektroniki samochodowej: trwałość i odporność na cykle termiczne
Elektronika samochodowa nie wypełnia krytycznego procesu, który obejmuje hermetyzację i ochronę komponentów elektronicznych w zastosowaniach motoryzacyjnych. Środowiska motoryzacyjne stanowią wyjątkowe wyzwania, w tym wahania temperatury, cykle termiczne, naprężenia mechaniczne oraz narażenie na wilgoć i chemikalia. Dlatego niedopełnienie elektroniki samochodowej koncentruje się na dwóch krytycznych aspektach: trwałości i odporności na cykle termiczne.
Trwałość jest kluczowym wymogiem w przypadku niedopełnienia elektroniki samochodowej. Podczas normalnej eksploatacji pojazdy samochodowe podlegają ciągłym wibracjom, wstrząsom i naprężeniom mechanicznym. Materiały wypełniające stosowane w zastosowaniach motoryzacyjnych muszą solidnie chronić elementy elektroniczne, zapewniając ich trwałość i długowieczność. Powinny wytrzymać trudne warunki i obciążenia mechaniczne spotykane na drodze oraz odporne na wnikanie wilgoci, kurzu i chemikaliów.
Materiały podkładowe do elektroniki samochodowej są wybierane lub formułowane pod kątem wysokiej wytrzymałości mechanicznej i odporności na uderzenia. Powinny wykazywać doskonałą przyczepność do elementów elektronicznych i podłoża, zapobiegając rozwarstwianiu lub rozdzielaniu pod wpływem naprężeń mechanicznych. Trwałe materiały wypełniające pomagają zminimalizować ryzyko uszkodzenia elementów elektronicznych w wyniku wibracji lub wstrząsów, zapewniając niezawodne działanie przez cały okres eksploatacji pojazdu.
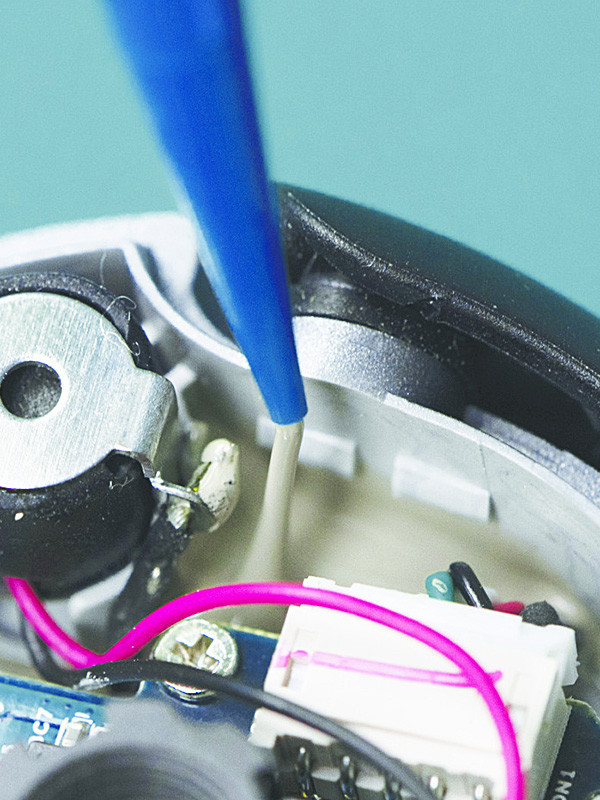
Odporność na cykliczne zmiany temperatury to kolejny krytyczny wymóg dotyczący niedopełnienia elektroniki samochodowej. Pojazdy samochodowe podlegają częstym zmianom temperatury, zwłaszcza podczas uruchamiania i pracy silnika, a te cykle temperaturowe mogą powodować naprężenia termiczne elementów elektronicznych i otaczającego materiału wypełniającego. Materiały podkładowe stosowane w przemyśle motoryzacyjnym muszą charakteryzować się doskonałą odpornością na cykliczne zmiany temperatury, aby wytrzymać te wahania temperatury bez uszczerbku dla ich właściwości.
Materiały podkładowe do elektroniki samochodowej powinny mieć niski współczynnik rozszerzalności cieplnej (CTE), aby zminimalizować naprężenia elementów elektronicznych podczas cykli termicznych. Dobrze dobrany współczynnik CTE między materiałem wypełniającym a składnikami zmniejsza ryzyko zmęczenia złącza lutowniczego, pękania lub innych uszkodzeń mechanicznych spowodowanych naprężeniami termicznymi. Ponadto materiały wypełniające powinny wykazywać dobrą przewodność cieplną, aby skutecznie rozpraszać ciepło, zapobiegając miejscowym gorącym punktom, które mogłyby mieć wpływ na wydajność i niezawodność komponentów.
Ponadto materiały wypełniające do elektroniki samochodowej powinny być odporne na wilgoć, chemikalia i płyny. Powinny mieć niską nasiąkliwość, aby zapobiec rozwojowi pleśni lub korozji elementów elektronicznych. Odporność chemiczna gwarantuje, że materiał podkładowy pozostaje stabilny w przypadku wystawienia na działanie płynów samochodowych, takich jak oleje, paliwa lub środki czyszczące, unikając degradacji lub utraty przyczepności.
Proces wypełniania w elektronice samochodowej zazwyczaj polega na dozowaniu materiału wypełniającego na elementy elektroniczne, umożliwieniu mu przepływu i wypełnieniu szczelin, a następnie utwardzeniu go w celu utworzenia trwałej kapsułki. Proces utwardzania można przeprowadzić metodami utwardzania termicznego lub UV, w zależności od specyficznych wymagań aplikacji i użytego materiału wypełniającego.
Wybór odpowiedniego podkładu epoksydowego
Wybór odpowiedniego podkładu epoksydowego to kluczowa decyzja w montażu i zabezpieczaniu elementów elektronicznych. Podkłady epoksydowe zapewniają wzmocnienie mechaniczne, odprowadzanie ciepła i ochronę przed czynnikami środowiskowymi. Oto kilka kluczowych kwestii, które należy wziąć pod uwagę przy wyborze odpowiedniej żywicy epoksydowej wypełniającej:
- Właściwości termiczne: Jedną z podstawowych funkcji wypełniacza epoksydowego jest rozpraszanie ciepła wytwarzanego przez elementy elektroniczne. Dlatego konieczne jest uwzględnienie przewodności cieplnej i oporu cieplnego żywicy epoksydowej. Wysoka przewodność cieplna pomaga w efektywnym przenoszeniu ciepła, zapobiegając gorącym punktom i utrzymując niezawodność komponentów. Żywica epoksydowa powinna również mieć niską odporność termiczną, aby zminimalizować naprężenia termiczne komponentów podczas cykli temperaturowych.
- Dopasowanie CTE: Współczynnik rozszerzalności cieplnej podkładu epoksydowego (CTE) powinien być dobrze dopasowany do CTE komponentów elektronicznych i podłoża, aby zminimalizować naprężenia termiczne i zapobiec awariom połączeń lutowanych. Ściśle dopasowane CTE pomaga zmniejszyć ryzyko awarii mechanicznych spowodowanych cyklami termicznymi.
- Płynność i zdolność wypełniania szczelin: Niewypełniona żywica epoksydowa powinna mieć dobre właściwości płynięcia i zdolność do skutecznego wypełniania szczelin między składnikami. Zapewnia to całkowite pokrycie i minimalizuje puste przestrzenie lub kieszenie powietrzne, które mogłyby wpłynąć na stabilność mechaniczną i wydajność termiczną zespołu. Lepkość żywicy epoksydowej powinna być odpowiednia dla konkretnego zastosowania i metody montażu, niezależnie od tego, czy jest to przepływ kapilarny, dozowanie strumieniowe czy sitodruk.
- Przyczepność: Silna przyczepność ma kluczowe znaczenie dla podkładu epoksydowego, aby zapewnić niezawodne wiązanie między komponentami a podłożem. Powinien wykazywać dobrą przyczepność do różnych materiałów, w tym metali, ceramiki i tworzyw sztucznych. Właściwości adhezyjne żywicy epoksydowej przyczyniają się do mechanicznej integralności zespołu i długoterminowej niezawodności.
- Metoda utwardzania: Rozważ metodę utwardzania, która najlepiej pasuje do Twojego procesu produkcyjnego. Podkłady epoksydowe można utwardzać za pomocą ciepła, promieniowania UV lub kombinacji obu. Każda metoda utwardzania ma zalety i ograniczenia, a wybór tej, która jest zgodna z wymaganiami produkcyjnymi, ma kluczowe znaczenie.
- Odporność środowiskowa: Oceń odporność podkładu epoksydowego na czynniki środowiskowe, takie jak wilgoć, chemikalia i ekstremalne temperatury. Żywica epoksydowa powinna być odporna na działanie wody, zapobiegając rozwojowi pleśni lub korozji. Odporność chemiczna zapewnia stabilność w kontakcie z płynami samochodowymi, środkami czyszczącymi lub innymi potencjalnie korozyjnymi substancjami. Ponadto żywica epoksydowa powinna zachowywać swoje właściwości mechaniczne i elektryczne w szerokim zakresie temperatur.
- Niezawodność i trwałość: Weź pod uwagę historię i dane dotyczące niezawodności wypełniacza epoksydowego. Poszukaj materiałów epoksydowych przetestowanych i sprawdzonych pod względem skuteczności w podobnych zastosowaniach lub posiadających certyfikaty branżowe i zgodność z odpowiednimi normami. Weź pod uwagę takie czynniki, jak starzenie się, długoterminowa niezawodność i zdolność żywicy epoksydowej do zachowania swoich właściwości w czasie.
Wybierając odpowiednią żywicę epoksydową do wypełniania, należy wziąć pod uwagę specyficzne wymagania aplikacji, w tym zarządzanie termiczne, stabilność mechaniczną, ochronę środowiska i kompatybilność procesu produkcyjnego. Konsultacje z dostawcami żywic epoksydowych lub zasięgnięcie porady eksperta mogą pomóc w podjęciu świadomej decyzji, która spełni potrzeby Twojej aplikacji i zapewni optymalną wydajność i niezawodność.
Przyszłe trendy w wypełnianiu epoksydowym
Żywica epoksydowa do wypełniania stale ewoluuje, napędzana postępem w technologiach elektronicznych, pojawiającymi się zastosowaniami oraz potrzebą poprawy wydajności i niezawodności. W rozwoju i stosowaniu podkładów epoksydowych można zaobserwować kilka przyszłych trendów:
- Miniaturyzacja i opakowania o większej gęstości: Ponieważ urządzenia elektroniczne wciąż się kurczą i charakteryzują się większą gęstością komponentów, żywice epoksydowe muszą się odpowiednio dostosować. Przyszłe trendy będą koncentrować się na opracowywaniu materiałów wypełniających, które penetrują i wypełniają mniejsze szczeliny między komponentami, zapewniając pełne pokrycie i niezawodną ochronę w coraz bardziej miniaturowych zespołach elektronicznych.
- Zastosowania o wysokiej częstotliwości: Wraz z rosnącym zapotrzebowaniem na urządzenia elektroniczne o wysokiej częstotliwości i szybkości, preparaty epoksydowe do wypełniania będą musiały spełniać specyficzne wymagania tych zastosowań. Materiały wypełniające o niskiej stałej dielektrycznej i stycznych o niskich stratach będą niezbędne do zminimalizowania strat sygnału i utrzymania integralności sygnałów o wysokiej częstotliwości w zaawansowanych systemach komunikacyjnych, technologii 5G i innych pojawiających się zastosowaniach.
- Ulepszone zarządzanie termiczne: Rozpraszanie ciepła pozostaje krytycznym problemem w przypadku urządzeń elektronicznych, zwłaszcza przy rosnącej gęstości mocy. Przyszłe preparaty epoksydowe do wypełniania będą koncentrować się na poprawie przewodności cieplnej w celu zwiększenia wymiany ciepła i skutecznego zarządzania problemami termicznymi. Zaawansowane wypełniacze i dodatki zostaną włączone do wypełniaczy epoksydowych w celu uzyskania wyższej przewodności cieplnej przy zachowaniu innych pożądanych właściwości.
- Elastyczna i rozciągliwa elektronika: Rozwój elastycznej i rozciągliwej elektroniki otwiera nowe możliwości wypełniania materiałów epoksydowych. Elastyczne podkłady epoksydowe muszą wykazywać doskonałą przyczepność i właściwości mechaniczne nawet przy wielokrotnym zginaniu lub rozciąganiu. Materiały te umożliwią hermetyzację i ochronę elektroniki w urządzeniach do noszenia, giętkich wyświetlaczach i innych zastosowaniach wymagających elastyczności mechanicznej.
- Rozwiązania przyjazne dla środowiska: Zrównoważony rozwój i względy środowiskowe będą odgrywać coraz ważniejszą rolę w opracowywaniu wypełniających materiałów epoksydowych. Nacisk zostanie położony na tworzenie preparatów epoksydowych wolnych od substancji niebezpiecznych i mających ograniczony wpływ na środowisko w całym cyklu życia, w tym produkcji, użytkowania i utylizacji. Materiały pochodzenia biologicznego lub odnawialne mogą również zyskać na znaczeniu jako zrównoważone alternatywy.
- Ulepszone procesy produkcyjne: Przyszłe trendy w wypełnianiu epoksydowym będą koncentrować się na właściwościach materiałów i postępach w procesach produkcyjnych. Zbadane zostaną techniki, takie jak wytwarzanie addytywne, dozowanie selektywne i zaawansowane metody utwardzania, aby zoptymalizować zastosowanie i wydajność żywicy epoksydowej wypełniającej w różnych procesach montażu elektronicznego.
- Integracja zaawansowanych technik testowania i charakteryzacji: Wraz ze wzrostem złożoności i wymagań urządzeń elektronicznych, pojawi się zapotrzebowanie na zaawansowane metody testowania i charakteryzowania, aby zapewnić niezawodność i wydajność niedopełnionej żywicy epoksydowej. Techniki, takie jak badania nieniszczące, monitorowanie na miejscu i narzędzia symulacyjne, pomogą w rozwoju i kontroli jakości materiałów epoksydowych z niedostatecznym wypełnieniem.
Wnioski
Podkład epoksydowy odgrywa kluczową rolę w zwiększaniu niezawodności i wydajności elementów elektronicznych, szczególnie w opakowaniach półprzewodników. Różne rodzaje żywic epoksydowych do wypełniania oferują szereg korzyści, w tym wysoką niezawodność, samodozowanie, wysoką gęstość oraz wysoką wydajność termiczną i mechaniczną. Wybór odpowiedniej żywicy epoksydowej wypełniającej do zastosowania i opakowania zapewnia solidne i długotrwałe wiązanie. Wraz z postępem technologicznym i zmniejszającymi się rozmiarami opakowań oczekujemy jeszcze bardziej innowacyjnych rozwiązań epoksydowych do wypełniania podkładów, oferujących doskonałą wydajność, integrację i miniaturyzację. Podkład epoksydowy będzie odgrywał coraz ważniejszą rolę w przyszłości elektroniki, umożliwiając nam osiąganie wyższych poziomów niezawodności i wydajności w różnych branżach.