Izolacyjna powłoka epoksydowa
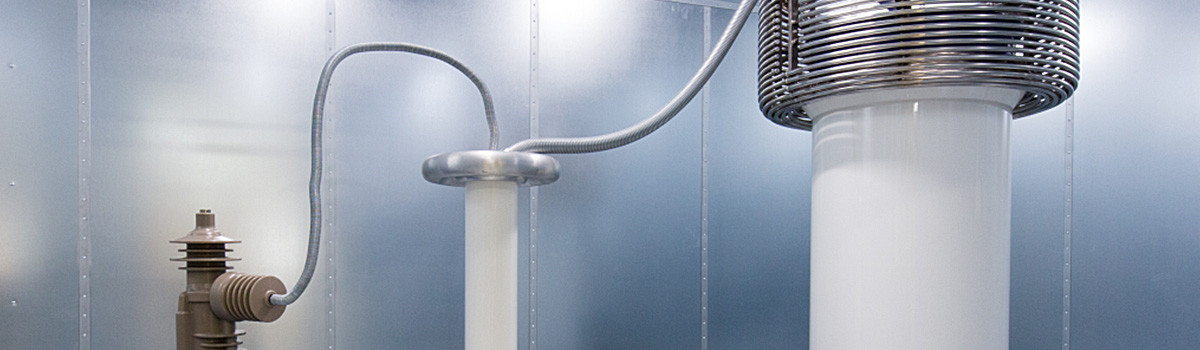
Izolacyjna powłoka epoksydowa jest wszechstronnym i szeroko stosowanym materiałem o doskonałych właściwościach izolacji elektrycznej. W różnych gałęziach przemysłu powszechnie stosuje się go do ochrony elementów elektrycznych, płytek drukowanych i innych wrażliwych urządzeń przed wilgocią, kurzem, chemikaliami i uszkodzeniami fizycznymi. Ten artykuł ma na celu zagłębienie się w izolacyjną powłokę epoksydową, zwrócenie uwagi na jej zastosowania, zalety i krytyczne uwagi dotyczące wyboru odpowiedniej warstwy do określonych potrzeb.
Zrozumienie izolacyjnej powłoki epoksydowej
Izolacyjna powłoka epoksydowa to powłoka ochronna, która zapewnia izolację i odporność na przewodnictwo elektryczne różnych powierzchni. Jest powszechnie stosowany w przemyśle elektronicznym, elektrycznym, motoryzacyjnym i lotniczym w celu ochrony i poprawy wydajności elementów elektrycznych.
Podstawowym celem izolacyjnych powłok epoksydowych jest zapobieganie przepływowi prądu elektrycznego między materiałami przewodzącymi. Powłoki te są nakładane na powierzchnie podatne na zwarcia elektryczne, korozję lub uszkodzenia spowodowane czynnikami środowiskowymi. Materiał epoksydowy działa jak izolator, zapobiegając przenoszeniu elektronów i minimalizując ryzyko awarii lub nieprawidłowego działania elektrycznego.
Izolacyjne powłoki epoksydowe są zazwyczaj wykonane z połączenia żywicy epoksydowej, polimeru termoutwardzalnego i środka utwardzającego. Żywica epoksydowa zapewnia doskonałą przyczepność, odporność chemiczną i wytrzymałość mechaniczną, podczas gdy środek utwardzający wyzwala reakcję sieciowania, która przekształca płynną żywicę epoksydową w trwałą, trwałą powłokę.
Nakładanie izolujących powłok epoksydowych obejmuje kilka etapów. Najpierw powierzchnia przeznaczona do malowania jest dokładnie oczyszczona i przygotowana w celu zapewnienia odpowiedniej przyczepności. Wszelkie zabrudzenia, tłuszcz lub zanieczyszczenia należy usunąć, aby uzyskać czystą powierzchnię klejenia. Następnie powłoka epoksydowa jest mieszana zgodnie z zaleceniami producenta i nakładana na powierzchnię techniką natrysku, pędzla lub zanurzania.
Po nałożeniu powłoka epoksydowa przechodzi proces utwardzania, w trakcie którego twardnieje i tworzy barierę ochronną. Utwardzanie można osiągnąć różnymi metodami, w tym ciepłem, chemikaliami lub jednym i drugim. Utwardzanie poprawia właściwości mechaniczne powłoki, siłę przyczepności i odporność chemiczną.
Izolacyjne powłoki epoksydowe mają kilka zalet:
- Zapewniają izolację elektryczną, zapobiegając przepływowi prądu elektrycznego i zmniejszając ryzyko zwarć lub awarii elektrycznych.
- Powłoki te zapewniają doskonałą ochronę przed czynnikami środowiskowymi, takimi jak wilgoć, chemikalia i ścieranie, wydłużając żywotność powlekanych elementów.
- Izolacyjne powłoki epoksydowe mogą zwiększyć stabilność termiczną powierzchni i odporność na płomień, dzięki czemu nadają się do zastosowań w środowiskach o wysokiej temperaturze.
Znaczenie izolacji elektrycznej
Izolacja elektryczna odgrywa kluczową rolę w utrzymaniu bezpieczeństwa, niezawodności i wydajności systemów elektrycznych. Polega na stosowaniu materiałów i technik zapobiegających przepływowi prądu elektrycznego między przewodzącymi elementami lub powierzchniami. Oto kilka kluczowych powodów podkreślających znaczenie izolacji elektrycznej:
- Ochrona przed porażeniem elektrycznym: Izolacja elektryczna zapobiega bezpośredniemu kontaktowi z przewodami pod napięciem, zmniejszając ryzyko porażenia prądem. Działa jak bariera, która hamuje przepływ prądu elektrycznego przez materiały nieprzewodzące, chroniąc osoby przed potencjalnymi obrażeniami.
- Zapobieganie zwarciom i pożarom elektrycznym: Izolacja pomaga zapobiegać niezamierzonemu kontaktowi elektrycznemu między materiałami przewodzącymi, co może prowadzić do zwarć i pożarów elektrycznych. Izolowanie przewodów, kabli i elementów elektrycznych minimalizuje prawdopodobieństwo powstania łuku elektrycznego, iskier i przegrzania, znacznie zmniejszając ryzyko pożaru i uszkodzenia sprzętu.
- Zwiększona wydajność elektryczna: Materiały izolacyjne o wysokiej wytrzymałości dielektrycznej i niskiej przewodności elektrycznej poprawiają ogólną wydajność systemów elektrycznych. Utrzymują odpowiedni poziom napięcia, zapobiegają prądom upływowym, zmniejszają zakłócenia lub zniekształcenia sygnału, zapewniając optymalne działanie obwodów i urządzeń elektrycznych.
- Ochrona przed czynnikami środowiskowymi: Materiały izolacji elektrycznej są odporne na wilgoć, chemikalia, kurz i inne zanieczyszczenia. Ta ochrona pomaga zapobiegać korozji, degradacji i uszkodzeniom izolacji spowodowanym czynnikami zewnętrznymi, utrzymując w ten sposób długowieczność i niezawodność komponentów elektrycznych.
- Zwiększona efektywność energetyczna: Izolacja zmniejsza straty energii i poprawia wydajność systemów elektrycznych. Zapobiegając upływowi prądu, izolacja minimalizuje straty mocy i usprawnia przesył i dystrybucję energii elektrycznej, co skutkuje zmniejszonym zużyciem energii i niższymi kosztami operacyjnymi.
- Zgodność z normami i przepisami bezpieczeństwa: Izolacja elektryczna jest niezbędna do spełnienia norm i przepisów bezpieczeństwa ustanowionych przez władze i organizacje branżowe. Zgodność z tymi wymaganiami gwarantuje, że instalacje i sprzęt elektryczny są projektowane i eksploatowane w sposób minimalizujący ryzyko dla personelu, mienia i środowiska.
- Ochrona wrażliwego sprzętu: Izolacja ma kluczowe znaczenie dla ochrony wrażliwego sprzętu elektrycznego i elektronicznego przed zakłóceniami elektrycznymi i skokami napięcia. Materiały izolacyjne, takie jak lakiery lub powłoki, chronią delikatne komponenty przed zakłóceniami elektromagnetycznymi (EMI) i wyładowaniami elektrostatycznymi (ESD), zachowując ich funkcjonalność i wydłużając ich żywotność.
Zastosowania izolacyjnej powłoki epoksydowej
Izolacyjna powłoka epoksydowa to specjalistyczna powłoka, która zapewnia doskonałe właściwości izolacji elektrycznej, dzięki czemu nadaje się do różnych zastosowań. Powłoka ta zazwyczaj zawiera żywicę epoksydową, zapewniając właściwości izolacyjne i ochronne. Oto niektóre z krytycznych zastosowań izolacyjnej powłoki epoksydowej:
- Elektronika i komponenty elektryczne: Izolacyjna powłoka epoksydowa jest szeroko stosowana w przemyśle elektronicznym i elektrycznym. Stosuje się go do elementów takich jak płytki drukowane, transformatory, kondensatory i cewki w celu zapewnienia izolacji elektrycznej, zapobiegania zwarciom i zwiększenia ogólnej niezawodności i żywotności tych elementów. Powłoka chroni również przed wilgocią, kurzem i innymi zanieczyszczeniami środowiskowymi.
- Wytwarzanie i przesyłanie energii: Izolacyjne powłoki epoksydowe mają kluczowe znaczenie w systemach wytwarzania i przesyłu energii. Stosuje się je do izolatorów, rozdzielnic, szyn zbiorczych i innych urządzeń wysokiego napięcia, aby zapobiec wyciekom elektrycznym, wyładowaniom koronowym i przeskokom elektrycznym. Zapewniając wysoką wytrzymałość dielektryczną, powłoka pomaga zachować integralność i bezpieczeństwo infrastruktury elektrycznej.
- Silniki i generatory: Silniki elektryczne i generatory wymagają izolacji, aby zapobiec awariom elektrycznym i zapewnić wydajne działanie. Izolacyjne powłoki epoksydowe są nakładane na uzwojenia tych maszyn i inne krytyczne części. Powłoka poprawia izolację elektryczną, poprawia odprowadzanie ciepła i zapewnia ochronę przed chemikaliami, wilgocią i obciążeniami mechanicznymi.
- Przemysł motoryzacyjny: Izolacyjne powłoki epoksydowe znajdują różne zastosowania w sektorze motoryzacyjnym. Izolują połączenia elektryczne, zaciski i wiązki przewodów w pojazdach. Warstwa pomaga zachować integralność elektryczną, zapobiega zwarciom i chroni przed korozją, wibracjami i cyklami termicznymi. Stosowany jest również do izolacji elementów w pojazdach hybrydowych i elektrycznych.
- Lotnictwo i obrona: Izolacyjne powłoki epoksydowe mają kluczowe znaczenie w sektorze lotniczym i obronnym. Są stosowane w systemach elektronicznych, awionice, sprzęcie radarowym i systemach komunikacyjnych, aby zapewnić niezawodne działanie w trudnych warunkach. Powłoka chroni przed zakłóceniami elektrycznymi, promieniowaniem, wilgocią i ekstremalnymi temperaturami.
- Powłoka płytek obwodów drukowanych (PCB): płytki PCB są podstawą urządzeń elektronicznych. Powłoki epoksydowe chronią obwody PCB i połączenia lutowane przed wilgocią, kurzem i innymi zanieczyszczeniami. Powłoka zapewnia również izolację między warstwami przewodzącymi, zapobiegając zwarciom i zwiększając ogólną trwałość płytek.
- Odporność chemiczna i korozyjna: Izolacyjne powłoki epoksydowe zapewniają doskonałą odporność chemiczną i mogą chronić powierzchnie przed substancjami korozyjnymi. Wykorzystywane są w przetwórstwie chemicznym, przemyśle naftowym i gazowym oraz oczyszczaniu ścieków. Powłoka zapobiega atakom chemicznym, zwiększa żywotność sprzętu i minimalizuje wymagania konserwacyjne.
- Hermetyzacja elektryczna: Izolacyjne powłoki epoksydowe są wykorzystywane do hermetyzacji elektrycznej, szczególnie w zastosowaniach, w których wilgoć lub inne zanieczyszczenia stanowią zagrożenie. Jest powszechnie używany do zalewania i hermetyzacji elementów elektronicznych, czujników i złączy. Powłoka tworzy barierę ochronną przed czynnikami środowiskowymi i obciążeniami mechanicznymi.
Ochrona komponentów elektronicznych
Ochrona elementów elektronicznych jest kluczowa dla zapewnienia ich prawidłowego funkcjonowania i długowieczności. Elementy elektroniczne są często wrażliwe na czynniki środowiskowe, takie jak temperatura, wilgotność, zakłócenia elektryczne i obciążenia fizyczne. Przy odpowiedniej ochronie komponenty te można chronić, a nawet uniemożliwić ich działanie. Oto kilka standardowych metod i technik stosowanych do zabezpieczania elementów elektronicznych:
- Obudowy: Elementy elektroniczne można umieścić w obudowach ochronnych, takich jak obudowy, szafki lub pudełka. Sekcje zapewniają fizyczną ochronę przed kurzem, wilgocią i innymi zanieczyszczeniami. Chronią również komponenty przed przypadkowym uderzeniem lub niewłaściwą obsługą.
- Ekranowanie EMI/RFI: Zakłócenia elektromagnetyczne (EMI) i zakłócenia częstotliwości radiowych (RFI) mogą zakłócać normalne działanie elementów elektronicznych. Ekranowanie EMI/RFI wymaga użycia materiałów przewodzących, takich jak powłoki metalowe lub przewodzące uszczelki, w celu uzyskania efektu klatki Faradaya. To ekranowanie zapobiega zakłócaniu wrażliwych układów elektronicznych przez zewnętrzne sygnały elektromagnetyczne.
- Zarządzanie ciepłem: Elementy elektroniczne wytwarzają ciepło podczas pracy, a nadmierne ciepło może obniżyć ich wydajność i niezawodność. Techniki zarządzania ciepłem, takie jak radiatory, wentylatory i podkładki termiczne, pomagają rozpraszać ciepło i utrzymywać optymalną temperaturę roboczą. Radiatory pochłaniają i rozpraszają ciepło, a wentylatory ułatwiają przepływ powietrza. Podkładki termiczne zapewniają interfejs termiczny między komponentem a radiatorem, zapewniając wydajne przenoszenie ciepła.
- Ochrona przed przepięciami: Przepięcia spowodowane wyładowaniami atmosferycznymi, awariami elektrycznymi lub stanami nieustalonymi podczas przełączania mogą uszkodzić elementy elektroniczne. Urządzenia ochrony przed przepięciami, takie jak tłumiki przepięć lub warystory z tlenku metalu (MOV), przekierowują nadmierne napięcie w celu ochrony elementów. Urządzenia te ograniczają poziomy napięcia i zapobiegają przedostawaniu się przejściowych skoków napięcia do wrażliwych komponentów.
- Uszczelnienie środowiskowe: W określonych zastosowaniach elementy elektroniczne wymagają ochrony przed trudnymi warunkami środowiskowymi, takimi jak wilgoć, chemikalia lub ekstremalne temperatury. Techniki uszczelniania środowiskowego, takie jak powłoki konforemne, mieszanki do zalewania lub uszczelnianie hermetyczne, tworzą barierę, która chroni komponenty przed tymi elementami.
- Zabezpieczenie obwodu: Elementy elektroniczne mogą być podatne na przepięcia, przetężenia i wyładowania elektrostatyczne (ESD). Urządzenia zabezpieczające obwody, takie jak bezpieczniki, wyłączniki automatyczne, tłumiki napięcia przejściowego (diody TVS) i diody zabezpieczające przed wyładowaniami elektrostatycznymi są stosowane w celu ograniczenia i przekierowania nadmiernego prądu, napięcia lub ładunków statycznych z dala od komponentów.
- Uziemienie i połączenie: Właściwe techniki uziemienia i połączenia są niezbędne do ochrony elementów elektronicznych przed zakłóceniami elektrycznymi i zapewnienia bezpieczeństwa. Uziemienie zapewnia drogę do rozpraszania niepożądanych ładunków elektrycznych. Natomiast łączenie zmniejsza różnice potencjałów, które mogłyby spowodować uszkodzenia. Techniki uziemiania i łączenia obejmują stosowanie płaszczyzn uziemiających, przewodów i typowych połączeń uziemiających.
- Filtrowanie: Zakłócenia elektryczne i zakłócenia z różnych źródeł mogą wpływać na działanie elementów elektronicznych. Filtry, takie jak dolnoprzepustowy, górnoprzepustowy lub filtry zakłóceń elektromagnetycznych, mogą wyeliminować lub zredukować niepożądane sygnały i zapewnić czyste zasilanie członków.
- Środki antystatyczne: Wyładowania elektrostatyczne (ESD) mogą spowodować znaczne uszkodzenia elementów elektronicznych. Środki antystatyczne, takie jak stacje robocze odporne na wyładowania elektrostatyczne, opaski na nadgarstek i materiały opakowaniowe, zapobiegają gromadzeniu się ładunków elektrostatycznych i ich rozładowywaniu do wrażliwych części.
- Regularna konserwacja i testowanie: Regularna konserwacja, inspekcja i testowanie są niezbędne do zidentyfikowania potencjalnych problemów z komponentami elektronicznymi. Okresowe kontrole zapewniają prawidłowe działanie środków ochronnych oraz szybkie usuwanie wszelkich usterek lub awarii.
Elementy elektroniczne można zabezpieczyć przed zagrożeniami środowiskowymi, zakłóceniami elektrycznymi i uszkodzeniami fizycznymi, stosując te techniki ochrony. Zapewnia to ich niezawodne działanie i wydłuża ich żywotność, prowadząc do poprawy wydajności i skrócenia przestojów.
Powłoka płytki drukowanej
Powlekanie płytek drukowanych to kluczowy proces w produkcji elektroniki, który polega na nałożeniu warstwy ochronnej na płytkę drukowaną (PCB). Powłoka ta zapewnia izolację, ochronę przed czynnikami środowiskowymi oraz zwiększa niezawodność i trwałość obwodów elektrycznych. W tym artykule zbadamy znaczenie powlekania płytek drukowanych i różne rodzaje stosowanych powłok.
Głównym celem powlekania płytek drukowanych jest ochrona delikatnych elementów elektronicznych przed różnymi obciążeniami środowiskowymi. Naprężenia te obejmują wilgoć, kurz, brud, chemikalia i wahania temperatury, które mogą prowadzić do korozji, zwarć i innych awarii. Powłoka działa jak bariera, zapobiegając przedostawaniu się tych szkodliwych pierwiastków do obwodów i powodowaniu uszkodzeń.
Istnieje kilka rodzajów powłok dostępnych dla płytek drukowanych, z których każda oferuje określone korzyści w zależności od wymagań aplikacji. Jednym z powszechnych typów jest powłoka ochronna, która jest cienką warstwą ochronną nakładaną bezpośrednio na powierzchnię PCB. Powłoki ochronne mogą być wykonane z różnych materiałów, w tym akryli, uretanów, silikonów i żywic epoksydowych. Powłoki te dopasowują się do kształtu płytki drukowanej, pokrywając wszystkie elementy i odsłonięte ślady oraz zapewniają doskonałą ochronę przed wilgocią, kurzem i zanieczyszczeniami chemicznymi.
Innym rodzajem powłoki jest hermetyzacja lub związek zalewania, który jest grubszym materiałem, który pokrywa całą płytkę drukowaną, całkowicie ją otaczając. Mieszanki do zalewania są zwykle wykonane z żywicy epoksydowej lub poliuretanu i zapewniają doskonałą ochronę przed naprężeniami mechanicznymi, wibracjami i ekstremalnymi temperaturami. Są powszechnie stosowane w aplikacjach, w których płytki drukowane są narażone na trudne warunki środowiskowe lub wysoki poziom obciążenia fizycznego.
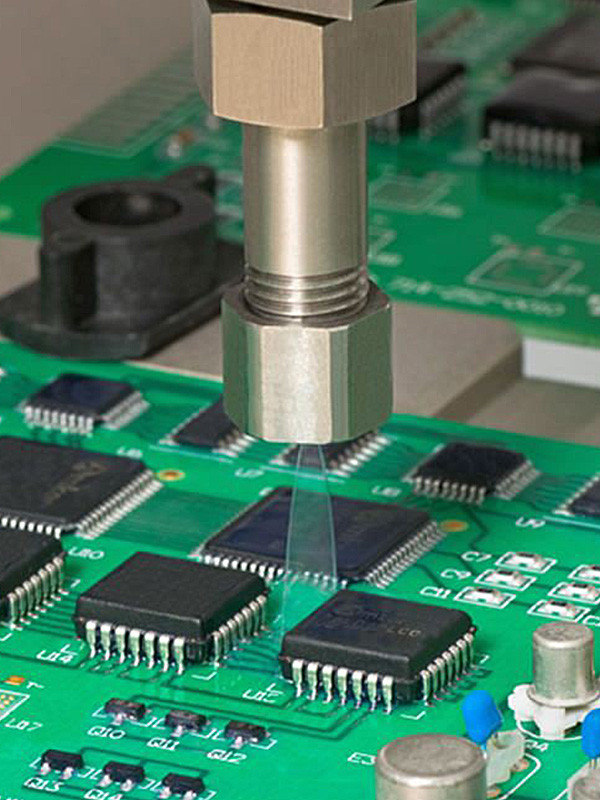
Sam proces powlekania obejmuje staranne techniki aplikacji, aby zapewnić równomierne pokrycie i odpowiednią przyczepność. Można zastosować różne metody, takie jak powlekanie natryskowe, powlekanie zanurzeniowe lub powlekanie selektywne. Powlekanie natryskowe polega na użyciu pistoletu natryskowego lub rozpylacza w celu nałożenia drobnej mgiełki materiału powłokowego na płytkę drukowaną. Z drugiej strony powlekanie zanurzeniowe zanurza płytkę drukowaną w kąpieli materiału powlekającego, umożliwiając jej pełne pokrycie płytki. Powlekanie selektywne to precyzyjna metoda, która nakłada powłokę tylko na określone obszary płytki drukowanej, pozostawiając inne elementy niepowlekane w celu ułatwienia dostępu.
Oprócz ochrony środowiska, powłoki płytek drukowanych zapewniają również właściwości izolacji elektrycznej. Materiał powłoki ma wysoką wytrzymałość dielektryczną, co zapobiega upływowi prądu pomiędzy blisko rozmieszczonymi ścieżkami lub elementami. Jest to szczególnie ważne w zastosowaniach wysokonapięciowych, w których izolacja elektryczna ma kluczowe znaczenie.
Izolacja silnika i transformatora
Ochrona elementów elektronicznych jest kluczowa dla zapewnienia ich prawidłowego funkcjonowania i długowieczności. Elementy elektroniczne są często wrażliwe na czynniki środowiskowe, takie jak temperatura, wilgotność, zakłócenia elektryczne i obciążenia fizyczne. Przy odpowiedniej ochronie komponenty te można chronić, a nawet uniemożliwić ich działanie. Oto kilka standardowych metod i technik stosowanych do zabezpieczania elementów elektronicznych:
- Obudowy: Elementy elektroniczne można umieścić w obudowach ochronnych, takich jak obudowy, szafki lub pudełka. Sekcje zapewniają fizyczną ochronę przed kurzem, wilgocią i innymi zanieczyszczeniami. Chronią również komponenty przed przypadkowym uderzeniem lub niewłaściwą obsługą.
- Ekranowanie EMI/RFI: Zakłócenia elektromagnetyczne (EMI) i zakłócenia częstotliwości radiowych (RFI) mogą zakłócać normalne działanie elementów elektronicznych. Ekranowanie EMI/RFI wymaga użycia materiałów przewodzących, takich jak powłoki metalowe lub przewodzące uszczelki, w celu uzyskania efektu klatki Faradaya. To ekranowanie zapobiega zakłócaniu wrażliwych układów elektronicznych przez zewnętrzne sygnały elektromagnetyczne.
- Zarządzanie ciepłem: Elementy elektroniczne wytwarzają ciepło podczas pracy, a nadmierne ciepło może obniżyć ich wydajność i niezawodność. Techniki zarządzania ciepłem, takie jak radiatory, wentylatory i podkładki, pomagają rozpraszać ciepło i utrzymywać optymalną temperaturę roboczą. Radiatory pochłaniają i rozpraszają ciepło, a wentylatory ułatwiają przepływ powietrza. Podkładki termiczne zapewniają interfejs termiczny między komponentem a radiatorem, zapewniając wydajne przenoszenie ciepła.
- Ochrona przed przepięciami: Przepięcia spowodowane wyładowaniami atmosferycznymi, awariami elektrycznymi lub stanami nieustalonymi podczas przełączania mogą uszkodzić elementy elektroniczne. Urządzenia ochrony przed przepięciami, takie jak tłumiki przepięć lub warystory z tlenku metalu (MOV), przekierowują nadmierne napięcie w celu ochrony elementów. Urządzenia te ograniczają poziomy napięcia i zapobiegają przedostawaniu się przejściowych skoków napięcia do wrażliwych komponentów.
- Uszczelnienie środowiskowe: W określonych zastosowaniach elementy elektroniczne wymagają ochrony przed trudnymi warunkami środowiskowymi, takimi jak wilgoć, chemikalia lub ekstremalne temperatury. Techniki uszczelniania środowiskowego, takie jak powłoki konforemne, mieszanki do zalewania lub uszczelnianie hermetyczne, tworzą barierę, która chroni komponenty przed tymi elementami.
- Zabezpieczenie obwodu: Elementy elektroniczne mogą być podatne na przepięcia, przetężenia i wyładowania elektrostatyczne (ESD). Urządzenia zabezpieczające obwody, takie jak bezpieczniki, wyłączniki automatyczne, tłumiki napięcia przejściowego (diody TVS) i diody zabezpieczające przed wyładowaniami elektrostatycznymi są stosowane w celu ograniczenia i przekierowania nadmiernego prądu, napięcia lub ładunków statycznych z dala od komponentów.
- Uziemienie i połączenie: Właściwe techniki uziemienia i połączenia są niezbędne do ochrony elementów elektronicznych przed zakłóceniami elektrycznymi i zapewnienia bezpieczeństwa. Uziemienie zapewnia drogę do rozpraszania niepożądanych ładunków elektrycznych. Natomiast łączenie zmniejsza różnice potencjałów, które mogłyby spowodować uszkodzenia. Techniki uziemiania i łączenia obejmują stosowanie płaszczyzn uziemiających, przewodów i typowych połączeń uziemiających.
- Filtrowanie: Zakłócenia elektryczne i zakłócenia z różnych źródeł mogą wpływać na działanie elementów elektronicznych. Filtry, takie jak dolnoprzepustowy, górnoprzepustowy lub filtry zakłóceń elektromagnetycznych, mogą wyeliminować lub zredukować niepożądane sygnały i zapewnić czyste zasilanie członków.
- Środki antystatyczne: Wyładowania elektrostatyczne (ESD) mogą spowodować znaczne uszkodzenia elementów elektronicznych. Środki antystatyczne, takie jak stacje robocze odporne na wyładowania elektrostatyczne, opaski na nadgarstek i materiały opakowaniowe, zapobiegają gromadzeniu się ładunków elektrostatycznych i ich rozładowywaniu do wrażliwych części.
- Regularna konserwacja i testowanie: Regularna konserwacja, inspekcja i testowanie są niezbędne do zidentyfikowania potencjalnych problemów z komponentami elektronicznymi. Okresowe kontrole zapewniają prawidłowe działanie środków ochronnych oraz szybkie usuwanie wszelkich usterek lub awarii.
Elementy elektroniczne można zabezpieczyć przed zagrożeniami środowiskowymi, zakłóceniami elektrycznymi i uszkodzeniami fizycznymi, stosując te techniki ochrony. Zapewnia to ich niezawodne działanie i wydłuża ich żywotność, prowadząc do poprawy wydajności i skrócenia przestojów.
Izolacja kabli i przewodów
Izolacja kabli i przewodów odgrywa kluczową rolę w systemach elektrycznych, zapewniając ochronę, izolację i bezpieczeństwo. Odnosi się do zewnętrznej powłoki lub płaszcza otaczającego przewody elektryczne, zapobiegającego przepływowi prądu elektrycznego do niezamierzonych obszarów i chroniącego przewody przed czynnikami środowiskowymi. Wybór materiału izolacyjnego zależy od takich czynników, jak napięcie znamionowe, zakres temperatur, warunki środowiskowe i zamierzone zastosowanie.
Jednym z powszechnie stosowanych materiałów izolacyjnych jest termoplast. Izolacja termoplastyczna jest elastyczna, trwała i odporna na ścieranie i chemikalia. Polichlorek winylu (PVC) to popularny materiał termoplastyczny znany ze swojej przystępnej ceny i szerokiego zakresu zastosowań. Jest powszechnie stosowany w zastosowaniach niskonapięciowych, takich jak okablowanie domowe i kable ogólnego przeznaczenia. Izolacja PVC zapewnia dobre właściwości elektryczne i jest trudnopalna.
Innym szeroko stosowanym materiałem izolacyjnym jest termoutwardzalny. W przeciwieństwie do tworzyw termoplastycznych, termoutwardzalnej izolacji nie można ponownie stopić ani ponownie uformować po związaniu. Polietylen usieciowany (XLPE) jest powszechnie stosowanym materiałem termoutwardzalnym znanym ze swoich doskonałych właściwości elektrycznych, odporności na wysokie temperatury oraz odporności na wilgoć i chemikalia. Izolacja XLPE jest często stosowana w kablach elektroenergetycznych średniego i wysokiego napięcia, w tym w podziemnych systemach przesyłowych i dystrybucyjnych.
Oprócz tworzyw termoplastycznych i termoutwardzalnych do określonych zastosowań przeznaczone są inne specjalistyczne materiały izolacyjne. Na przykład izolacja z kauczuku silikonowego jest znana ze swojej odporności na wysokie temperatury, dzięki czemu nadaje się do zastosowań w ekstremalnych środowiskach, takich jak przemysł lotniczy i motoryzacyjny. Fluoropolimery, takie jak politetrafluoroetylen (PTFE), są stosowane w zastosowaniach wymagających wysokich temperatur i częstotliwości ze względu na ich doskonałe właściwości elektryczne oraz odporność na chemikalia i ciepło.
Napięcie znamionowe oraz przeznaczenie kabla lub przewodu określają grubość warstwy izolacyjnej. Aplikacje o wyższym napięciu wymagają grubszych warstw izolacji, aby wytrzymać wyższe pola elektryczne i zapobiec awariom elektrycznym. Grubość izolacji wpływa również na całkowitą średnicę i elastyczność kabla.
Materiały izolacyjne poddawane są różnym testom, aby zapewnić ich wydajność i bezpieczeństwo. Testy te mogą obejmować pomiar właściwości elektrycznych, takich jak wytrzymałość dielektryczna i rezystancja izolacji, ocena odporności na zmiany temperatury, ognioodporność i właściwości mechaniczne, takie jak elastyczność i odporność na ścieranie. Zgodność z normami i przepisami branżowymi jest niezbędna do zapewnienia niezawodności i bezpieczeństwa systemów elektrycznych.
Przemysł lotniczy i motoryzacyjny
Izolacyjne powłoki epoksydowe znajdują podstawowe zastosowanie zarówno w przemyśle lotniczym, jak i motoryzacyjnym. Powłoki te oferują liczne korzyści, w tym izolację elektryczną, odporność na korozję i ochronę termiczną. Ta odpowiedź dotyczy krytycznych zastosowań izolacyjnych powłok epoksydowych w sektorze lotniczym i motoryzacyjnym, przy jednoczesnym przestrzeganiu limitu 450 słów.
Przemysł lotniczy:
- Konstrukcje samolotów: Izolacyjne powłoki epoksydowe chronią konstrukcje samolotów przed czynnikami środowiskowymi, takimi jak wilgoć, chemikalia i promieniowanie UV. Powłoki te działają jak bariera, zapobiegając korozji i przedłużając żywotność krytycznych komponentów. Dodatkowo zapewniają izolację elektryczną, zmniejszając ryzyko zakłóceń elektrycznych i zwiększając bezpieczeństwo.
- Komponenty elektroniczne: Izolacyjne powłoki epoksydowe są nakładane na elementy elektroniczne w systemach lotniczych, w tym płytki drukowane, złącza i czujniki. Powłoki te zapewniają doskonałe właściwości izolacji elektrycznej, chroniąc wrażliwą elektronikę przed wyładowaniami elektrostatycznymi, wilgocią i zanieczyszczeniami. Warstwy pomagają również w odprowadzaniu ciepła, zapewniając optymalną wydajność i niezawodność systemów elektronicznych.
- Osłony anten: Osłony anten radarowych, które są obudowami ochronnymi dla anten radarów, wymagają izolujących powłok epoksydowych, aby zapewnić przejrzystość sygnału i ochronę przed czynnikami środowiskowymi. Powłoki te zapewniają izolację przed zakłóceniami elektromagnetycznymi (EMI) przy jednoczesnym zachowaniu integralności strukturalnej osłony radaru. Oferują również odporność na erozję i warunki atmosferyczne, utrzymując wydajność systemu radarowego.
Przemysł samochodowy:
- Akumulatory pojazdów elektrycznych (EV): Izolacyjne powłoki epoksydowe mają kluczowe znaczenie dla ochrony akumulatorów pojazdów elektrycznych. Powłoki te zapobiegają przenikaniu wilgoci i zanieczyszczeń, zapewniając integralność i żywotność ogniw baterii. Zapewniają również izolację elektryczną, minimalizując ryzyko zwarć i zwiększając bezpieczeństwo pojazdów elektrycznych.
- Elementy silnika: Izolacyjne powłoki epoksydowe są stosowane na elementach silnika, aby chronić je przed korozją, wysoką temperaturą i działaniem środków chemicznych. Powłoki te poprawiają trwałość i wydajność części silnika, takich jak głowice cylindrów, kolektory dolotowe i układy wydechowe. Warstwy zapewniają również izolację termiczną, zmniejszając przenoszenie ciepła i poprawiając wydajność silnika.
- Układy elektryczne: Izolacyjne powłoki epoksydowe są nakładane na układy elektryczne w pojazdach, w tym na wiązki przewodów, złącza i płytki drukowane. Powłoki te zapewniają izolację elektryczną, zapobiegając zwarciom i zapewniając niezawodne działanie. Chronią również przed wilgocią, chemikaliami i wahaniami temperatury, zwiększając żywotność komponentów elektrycznych.
- Ochrona podwozia i podwozia: Izolacyjne powłoki epoksydowe chronią podwozie i podwozie pojazdów przed korozją powodowaną przez wilgoć, sól i zanieczyszczenia drogowe. Powłoki te tworzą solidną barierę, zapobiegając wnikaniu substancji żrących i przedłużając żywotność pojazdu. Dodatkowo zapewniają izolację termiczną, zmniejszając przenikanie ciepła i poprawiając komfort pasażerów.
Zastosowania morskie i przybrzeżne
Izolacyjne powłoki epoksydowe odgrywają kluczową rolę w zastosowaniach morskich i przybrzeżnych, zapewniając barierę ochronną przed korozją, ścieraniem i przewodnictwem elektrycznym. Te specjalistyczne powłoki oferują wiele korzyści i są szeroko stosowane w środowiskach morskich i przybrzeżnych.
- Statki morskie: Izolacyjne powłoki epoksydowe są szeroko stosowane na statkach morskich, w tym statkach, barkach i platformach morskich. Powłoki te chronią kadłuby przed korozyjnym działaniem słonej wody, chemikaliów i organizmów morskich. Stanowią trwałą barierę ochronną, która wydłuża żywotność statku i zmniejsza wymagania konserwacyjne.
- Morskie platformy naftowe i gazowe: W przypadku poszukiwań i wydobycia ropy naftowej i gazu na morzu izolacyjne powłoki epoksydowe są niezbędne do zachowania integralności platform i sprzętu. Zabezpieczają konstrukcje przed trudnymi warunkami środowiskowymi, w tym korozyjną słoną wodą, wysokimi temperaturami i narażeniem na chemikalia. Powłoki izolacyjne zapewniają również izolację elektryczną, zapobiegając zakłóceniom prądów elektrycznych w wrażliwym sprzęcie i zapewniając bezpieczeństwo.
- Rurociągi i zastosowania podmorskie: Izolacyjne powłoki epoksydowe są nakładane na kanały i sprzęt podwodny w celu ochrony ich przed korozją powodowaną przez wodę morską, wilgoć i chemikalia. Powłoki te działają jak bariera, zapobiegając wnikaniu substancji żrących i utrzymując integralność infrastruktury. Zapewniają również izolację elektryczną, zmniejszając ryzyko zakłóceń elektrycznych lub uszkodzeń.
- Morskie farmy wiatrowe: Izolacyjne powłoki epoksydowe są wykorzystywane do budowy i konserwacji morskich farm wiatrowych. Chronią konstrukcje turbin wiatrowych, w tym wieże, fundamenty i kable podmorskie, przed korozją i degradacją środowiska. Powłoki te zapewniają również izolację elektryczną, zapewniając bezpieczną i wydajną transmisję mocy.
- Sprzęt morski i przybrzeżny: Powłoki epoksydowe są nakładane na różne urządzenia morskie i przybrzeżne, takie jak pompy, zawory, zbiorniki i systemy cumownicze. Powłoki te chronią sprzęt przed korozją, ścieraniem i działaniem środków chemicznych, wydłużając jego żywotność i zmniejszając koszty konserwacji. Właściwości izolacyjne tych powłok zapobiegają również problemom z przewodnictwem elektrycznym, poprawiając bezpieczeństwo i niezawodność sprzętu.
- Floating Production Storage and Offloading (FPSO) Statki: FPSO są szeroko stosowane w wydobyciu ropy i gazu na morzu. Izolacyjne powłoki epoksydowe są nakładane na kadłuby i wewnętrzne struktury FPSO w celu ochrony ich przed korozją, ścieraniem i narażeniem chemicznym. Powłoki te zapewniają długotrwałą ochronę i zapewniają integralność strukturalną naczynia.
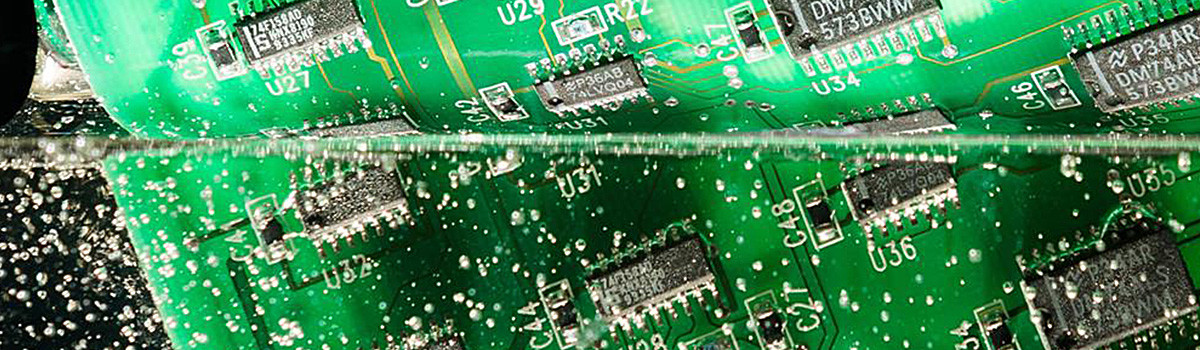
Odporność chemiczna i korozyjna
Izolacyjne powłoki epoksydowe są szeroko stosowane w różnych gałęziach przemysłu do ochrony przed korozją i izolacji elektrycznej. Powłoki te zapewniają doskonałą odporność chemiczną, dzięki czemu nadają się do trudnych środowisk, w których narażenie na substancje żrące jest problemem.
Odporność chemiczna ma kluczowe znaczenie dla izolacyjnych powłok epoksydowych, ponieważ są one często narażone na działanie szerokiej gamy chemikaliów, w tym kwasów, zasad, rozpuszczalników i paliw. Powłoki epoksydowe są odporne na wiele substancji korozyjnych ze względu na ich gęstą strukturę molekularną i usieciowaną sieć polimerową. Taka struktura tworzy barierę, która zapobiega przenikaniu czynników korozyjnych, chroniąc w ten sposób podłoże.
Jednym z podstawowych czynników wpływających na odporność chemiczną powłok epoksydowych jest ich wysoka gęstość usieciowania. Sieciowanie odnosi się do wiązań chemicznych między cząsteczkami epoksydu, w wyniku czego powstaje trójwymiarowa sieć. Sieć ta zwiększa odporność powłoki na agresję chemiczną, tworząc barierę zapobiegającą dyfuzji substancji korozyjnych. Dzięki temu pokryte podłoże pozostaje zabezpieczone przed korozją.
Ponadto powłoki epoksydowe można komponować z różnymi dodatkami i wzmocnieniami w celu zwiększenia ich odporności chemicznej. Na przykład dodatek inhibitorów korozji może dodatkowo poprawić właściwości ochronne powłoki poprzez hamowanie procesu korozji i zmniejszanie degradacji żywicy epoksydowej. Wzmocnienia, takie jak włókno szklane lub nanocząsteczki, mogą również zwiększyć odporność mechaniczną i chemiczną powłoki.
Oprócz odporności chemicznej, izolacyjne powłoki epoksydowe zapewniają doskonałą odporność na korozję. Korozja występuje, gdy materiał reaguje z otoczeniem, co prowadzi do jego pogorszenia i potencjalnej awarii. Powłoki epoksydowe działają jak bariera między środowiskiem korozyjnym a podłożem, zapobiegając kontaktowi wilgoci, tlenu i innych czynników korozyjnych z leżącą pod spodem powierzchnią metalową.
Powłoki epoksydowe zapewniają również doskonałą przyczepność do różnych podłoży, zapewniając długotrwałą ochronę przed korozją. Silne wiązanie warstwy z podłożem zapobiega wnikaniu wilgoci i substancji żrących, zmniejszając prawdopodobieństwo inicjacji i postępu korozji.
Należy zauważyć, że na odporność chemiczną i odporność na korozję izolacyjnych powłok epoksydowych może mieć wpływ temperatura, czas ekspozycji i określone środowisko chemiczne. Chociaż powłoki epoksydowe zapewniają doskonałą odporność na różne chemikalia, bardzo agresywne substancje mogą nadal powodować uszkodzenia przez dłuższy czas lub w ekstremalnych warunkach.
Aby zapewnić optymalną wydajność, wybór odpowiedniej receptury powłoki epoksydowej jest niezbędny w oparciu o specyficzne wymagania aplikacji. Przy wyborze odpowiedniego systemu powłok epoksydowych należy wziąć pod uwagę środowisko pracy, ekspozycję chemiczną, temperaturę i oczekiwaną żywotność.
Przewodność cieplna i rozpraszanie ciepła
Przewodność cieplna i rozpraszanie ciepła są niezbędne w różnych dziedzinach, w tym w inżynierii, elektronice i materiałoznawstwie. Odgrywają one kluczową rolę w określaniu wydajności i niezawodności systemów generujących lub obsługujących ciepło. Przyjrzyjmy się bliżej tym koncepcjom w podanym limicie słów.
Przewodność cieplna odnosi się do zdolności materiału do przewodzenia ciepła i jest to właściwość charakteryzująca łatwość przenoszenia ciepła przez substancję. Materiały o wysokiej przewodności cieplnej umożliwiają szybki przepływ ciepła, podczas gdy te o niskiej przewodności cieplnej utrudniają przenoszenie ciepła. Jednostką miary przewodności cieplnej jest wat na metr-kelwin (W/mK).
Różne czynniki wpływają na przewodność cieplną materiału. Jednym z krytycznych czynników jest struktura molekularna lub atomowa. Substancje o ściśle upakowanych atomach lub cząsteczkach mają zwykle wyższą przewodność cieplną. Metale, takie jak miedź i aluminium, są znane ze swojej wysokiej przewodności cieplnej ze względu na wiązanie metaliczne i ciasno upakowane struktury krystaliczne.
Z drugiej strony materiały o złożonej strukturze molekularnej lub dużych pustkach, takie jak polimery lub izolatory, takie jak drewno lub guma, mają stosunkowo niższą przewodność cieplną. Powietrze i inne gazy są słabymi przewodnikami ciepła, dlatego materiały z uwięzionymi kieszeniami powietrznymi, takie jak materiały izolacyjne, wykazują niską przewodność cieplną.
Rozpraszanie ciepła odnosi się jednak do przenoszenia lub rozpraszania ciepła z systemu lub komponentu w celu zapobieżenia przegrzaniu i utrzymania optymalnych warunków pracy. Efektywne odprowadzanie ciepła ma kluczowe znaczenie dla trwałości i wydajności urządzeń, zwłaszcza tych generujących znaczne ilości ciepła, takich jak elementy elektroniczne, układy zasilania czy silniki.
Istnieją różne metody odprowadzania ciepła, w zależności od konkretnego zastosowania. Niektóre standardowe techniki obejmują przewodzenie, konwekcję i promieniowanie.
Przewodnictwo obejmuje przenoszenie ciepła poprzez bezpośredni kontakt fizyczny między przedmiotami. Wydajne materiały przewodzące ciepło, takie jak metale lub materiały o wysokiej przewodności cieplnej, ułatwiają przenoszenie ciepła między elementami wytwarzającymi ciepło a radiatorami lub układami chłodzenia.
Konwekcja obejmuje przenoszenie ciepła poprzez ruch płynów, takich jak powietrze lub ciecz. Proces ten opiera się na cyrkulacji płynu, naturalnie lub za pomocą wentylatorów lub pomp, w celu odprowadzania ciepła ze źródła. Radiatory z rozszerzonymi powierzchniami są często wykorzystywane do zwiększania powierzchni konwekcyjnej wymiany ciepła.
Promieniowanie odnosi się do emisji i absorpcji promieniowania cieplnego, czyli promieniowania elektromagnetycznego emitowanego przez obiekty ze względu na ich temperaturę. Wszystkie obiekty powyżej temperatury zera absolutnego emitują promieniowanie cieplne. Rozpraszanie ciepła przez promieniowanie ma miejsce, gdy emitowane promieniowanie przenosi ciepło ze źródła do bardziej zrelaksowanego otoczenia.
W celu zwiększenia rozpraszania ciepła stosuje się różne techniki i technologie, w tym radiatory, rurki cieplne, materiały termiczne, wentylatory, systemy chłodzenia cieczą i zaawansowane rozwiązania do zarządzania ciepłem.
Wydajność izolacji elektrycznej
Izolacyjne powłoki epoksydowe mają kluczowe znaczenie w zapewnianiu izolacji elektrycznej w różnych gałęziach przemysłu, w tym w elektronice, sprzęcie elektrycznym i systemach zasilania. Powłoki te mają za zadanie zapobiegać przepływowi prądu elektrycznego i chronić przed awariami elektrycznymi lub zwarciami. Przyjrzyjmy się właściwościom izolacji elektrycznej izolacyjnych powłok epoksydowych w podanym limicie słów.
Jedną z podstawowych właściwości wpływających na właściwości elektroizolacyjne powłok epoksydowych jest ich wysoka wytrzymałość dielektryczna. Wytrzymałość dielektryczna odnosi się do maksymalnego pola elektrycznego, które materiał może wytrzymać bez przebicia elektrycznego. Izolacyjne powłoki epoksydowe są opracowane tak, aby miały wysoką wytrzymałość dielektryczną, co pozwala im wytrzymać wysokie poziomy napięcia i zapobiegać wyciekom elektrycznym lub wyładowaniom łukowym.
Kilka czynników, w tym skład żywicy, proces utwardzania i materiały wypełniające, wpływa na wytrzymałość dielektryczną izolacyjnych powłok epoksydowych. Żywice epoksydowe o dużej masie cząsteczkowej i gęstości usieciowania wykazują wyższą wytrzymałość dielektryczną. Proces utwardzania również odgrywa pewną rolę, ponieważ prawidłowe utwardzanie zapewnia utworzenie gęstej i jednolitej powłoki, która jest w stanie wytrzymać naprężenia elektryczne.
Materiały wypełniające można dodawać do powłok epoksydowych w celu zwiększenia wydajności izolacji elektrycznej. Wypełniacze, takie jak włókno szklane lub wypełniacze mineralne, mogą zwiększyć wytrzymałość dielektryczną poprzez zmniejszenie występowania pustych przestrzeni lub słabych punktów w powłoce. Wypełniacze te poprawiają ogólną jednorodność i integralność strukturalną powłoki, minimalizując ryzyko przebicia elektrycznego.
Izolacyjne powłoki epoksydowe zapewniają również dobrą rezystywność elektryczną, która odnosi się do odporności materiału na przepływ prądu elektrycznego. Wysoka rezystywność elektryczna ma kluczowe znaczenie dla zapobiegania prądom upływowym i utrzymania integralności izolacji elektrycznej. Powłoki epoksydowe zazwyczaj mają wysokie wartości rezystywności, co przyczynia się do ich skuteczności jako izolatorów elektrycznych.
Innym ważnym aspektem właściwości izolacji elektrycznej jest zdolność izolacyjnych powłok epoksydowych do wytrzymania czynników środowiskowych, które mogą wpływać na ich właściwości elektryczne. Czynniki takie jak wilgotność, wahania temperatury i narażenie na chemikalia mogą wpływać na wytrzymałość dielektryczną i rezystywność powłoki. Dlatego istotny jest dobór powłok epoksydowych o odpowiednich recepturach i dodatkach zapewniających długotrwałą izolacyjność elektryczną w określonych warunkach środowiskowych.
Ponadto izolacyjne powłoki epoksydowe powinny wykazywać dobrą przyczepność do podłoża, aby zapewnić długotrwałą izolację elektryczną. Silne wiązanie między warstwą a leżącą pod nią powierzchnią zapobiega powstawaniu pustych przestrzeni lub szczelin, które mogłyby pogorszyć właściwości izolacji elektrycznej. Przygotowanie powierzchni, techniki nakładania powłok oraz kompatybilność powłoki z podłożem wpływają na przyczepność.
Podsumowując, izolacyjne powłoki epoksydowe oferują doskonałe właściwości izolacji elektrycznej, zapewniając wysoką wytrzymałość dielektryczną, rezystywność elektryczną i dobrą przyczepność do podłoża. Ich formuła, proces utwardzania i zastosowanie wypełniaczy przyczyniają się do ich zdolności do wytrzymywania naprężeń elektrycznych i zapobiegania awariom elektrycznym. Właściwy dobór i zastosowanie izolujących powłok epoksydowych ma kluczowe znaczenie dla zapewnienia skutecznej izolacji elektrycznej w różnych zastosowaniach, od elektroniki po systemy elektroenergetyczne.
Rodzaje izolacyjnych powłok epoksydowych
Dostępnych jest kilka rodzajów izolacyjnych powłok epoksydowych, z których każda została zaprojektowana w celu spełnienia określonych wymagań i zapewnienia różnych poziomów izolacji elektrycznej. Oto kilka typowych rodzajów ochronnych powłok epoksydowych:
- Standardowe izolacyjne powłoki epoksydowe: Są to powłoki epoksydowe ogólnego przeznaczenia opracowane w celu zapewnienia podstawowej izolacji elektrycznej. Oferują dobrą wytrzymałość dielektryczną i rezystywność elektryczną, dzięki czemu nadają się do różnych zastosowań.
- Wysokotemperaturowe izolujące powłoki epoksydowe: Powłoki te są specjalnie opracowane, aby wytrzymać podwyższone temperatury bez uszczerbku dla właściwości izolacji elektrycznej. Mogą być stosowane w zastosowaniach, w których spodziewana jest ekspozycja na wysokie temperatury, takich jak silniki, transformatory lub komponenty elektryczne w przemyśle motoryzacyjnym lub lotniczym.
- Termoprzewodzące izolujące powłoki epoksydowe: Powłoki te zapewniają izolację elektryczną i mają dodatkową właściwość przewodności cieplnej. Zostały zaprojektowane tak, aby skutecznie odprowadzać ciepło przy zachowaniu izolacji elektrycznej. Powłoki te są powszechnie stosowane w zastosowaniach wymagających izolacji elektrycznej i efektywnego odprowadzania ciepła, na przykład w energoelektronice.
- Ognioodporne izolacyjne powłoki epoksydowe: Ognioodporne powłoki epoksydowe są opracowane w celu zapewnienia izolacji elektrycznej, oferując jednocześnie odporność na rozprzestrzenianie się płomienia i spalanie. Powłoki te są powszechnie stosowane w zastosowaniach, w których bezpieczeństwo przeciwpożarowe stanowi problem, takich jak panele elektryczne, rozdzielnice lub okablowanie.
- Odporne na chemikalia izolacyjne powłoki epoksydowe: Powłoki te zostały zaprojektowane w celu zapewnienia izolacji elektrycznej, oferując jednocześnie doskonałą odporność na różne chemikalia i substancje korozyjne. Nadają się do zastosowań, w których spodziewane jest narażenie na agresywne chemikalia lub środowiska korozyjne, na przykład w zakładach przetwórstwa chemicznego lub zastosowaniach morskich.
- Izolacyjne powłoki epoksydowe odporne na promieniowanie UV: Powłoki odporne na promieniowanie UV zostały opracowane w celu zapewnienia izolacji elektrycznej, a jednocześnie ochrony przed szkodliwym działaniem promieniowania ultrafioletowego (UV). Powłoki te są powszechnie stosowane w zastosowaniach zewnętrznych lub środowiskach, w których ekspozycja na światło słoneczne jest znaczna, takich jak panele słoneczne lub zewnętrzne urządzenia elektryczne.
- Elastyczne izolacyjne powłoki epoksydowe: Elastyczne powłoki epoksydowe są przeznaczone do zapewniania izolacji elektrycznej w zastosowaniach, w których powlekane podłoże podlega naprężeniom mechanicznym lub ruchom. Powłoki te zapewniają dobrą przyczepność i elastyczność, dzięki czemu wytrzymują zginanie lub rozciąganie bez pękania lub narażania izolacji elektrycznej.
Należy zauważyć, że wybór odpowiedniego typu izolacyjnej powłoki epoksydowej zależy od konkretnych wymagań aplikacji, czynników środowiskowych i oczekiwań dotyczących wydajności. Konsultacje z producentami powłok lub ekspertami branżowymi mogą pomóc w określeniu najbardziej odpowiedniej izolacyjnej powłoki epoksydowej do konkretnego zastosowania.
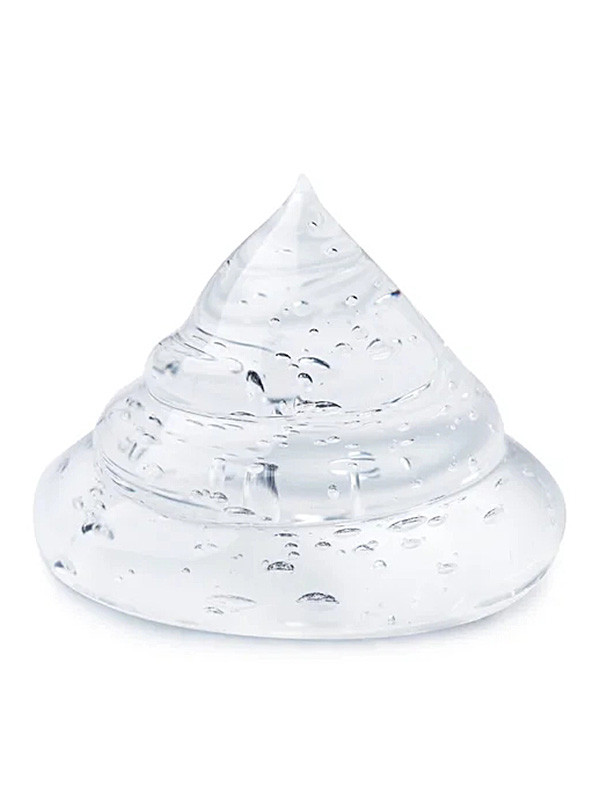
Dwuskładnikowe powłoki epoksydowe
Dwuskładnikowe powłoki epoksydowe są szeroko stosowane w różnych gałęziach przemysłu ze względu na ich wyjątkową trwałość, odporność chemiczną i wszechstronność. Powłoki te składają się z dwóch składników: żywicy i utwardzacza. Połączone w odpowiednich proporcjach przechodzą reakcję chemiczną znaną jako utwardzanie, w wyniku której powstaje trwała i ochronna powłoka. Tutaj przyjrzymy się kluczowym cechom, zastosowaniom i zaletom dwuskładnikowych powłok epoksydowych.
Charakterystyka: Dwuskładnikowe powłoki epoksydowe oferują kilka kluczowych cech, które czynią je wysoce pożądanymi w wielu zastosowaniach. Po pierwsze, zapewniają doskonałą przyczepność do różnych podłoży, w tym betonu, metalu, drewna i włókna szklanego. Ta przyczepność zapewnia długotrwałą wydajność i zapobiega problemom, takim jak łuszczenie się lub rozwarstwianie. Dodatkowo powłoki epoksydowe wykazują wysoką odporność chemiczną, dzięki czemu nadają się do stosowania w środowiskach narażonych na działanie substancji żrących, chemikaliów czy rozpuszczalników. Są również znane ze swojej wyjątkowej twardości, odporności na ścieranie i uderzenia, co przyczynia się do ich długowieczności i trwałości. Ponadto, w zależności od pożądanych wymagań estetycznych i funkcjonalnych, powłoki epoksydowe mogą mieć różne wykończenia, w tym błyszczące, matowe lub teksturowane.
Aplikacje: Dwuskładnikowe powłoki epoksydowe znajdują zastosowanie w różnych gałęziach przemysłu ze względu na ich wszechstronność i właściwości użytkowe. W sektorze przemysłowym są powszechnie stosowane do zabezpieczania posadzek betonowych w zakładach produkcyjnych, magazynach, garażach. Powłoka epoksydowa tworzy bezszwową, trwałą powierzchnię, która jest odporna na duży ruch, uderzenia i wycieki chemikaliów. W przemyśle morskim powłoki epoksydowe są stosowane do kadłubów łodzi, pokładów i innych konstrukcji, chroniąc przed wnikaniem wody, promieniowaniem UV i korozją. Powłoki te są również stosowane w przemyśle motoryzacyjnym do tworzenia warstwy ochronnej na karoseriach samochodów, elementach silnika i powłokach podwozia, zwiększając ich odporność na ścieranie, chemikalia i warunki atmosferyczne. Ponadto dwuskładnikowe powłoki epoksydowe są szeroko stosowane w budownictwie do hydroizolacji, napraw betonu i dekoracyjnych systemów posadzek.
Korzyści: Stosowanie dwuskładnikowych powłok epoksydowych oferuje użytkownikom przemysłowym i komercyjnym liczne korzyści. Po pierwsze, ich wyjątkowa trwałość i odporność na zużycie zapewniają dłuższą żywotność powlekanych powierzchni, zmniejszając koszty konserwacji i wymiany. Powłoki epoksydowe są również stosunkowo łatwe w aplikacji, co pozwala na wydajną instalację i minimalizację przestojów w warunkach przemysłowych. Ich bezszwowa i nieporowata struktura sprawia, że są higieniczne i łatwe w czyszczeniu, dzięki czemu idealnie nadają się do środowisk wymagających wysokiego poziomu czystości, takich jak placówki służby zdrowia czy zakłady przetwórstwa spożywczego. Ponadto powłoki epoksydowe można dostosować do określonych wymagań, w tym właściwości antypoślizgowych, odporności na ciepło lub przewodności elektrycznej. Ta wszechstronność pozwala na indywidualne rozwiązania w różnych zastosowaniach. Wreszcie, dwuskładnikowe powłoki epoksydowe są przyjazne dla środowiska, ponieważ mają niską zawartość lotnych związków organicznych (LZO), dzięki czemu są bezpieczniejsze dla pracowników i środowiska.
Jednoskładnikowe powłoki epoksydowe
Jednoskładnikowe powłoki epoksydowe to powłoki jednoskładnikowe, które oferują wiele zalet w porównaniu z tradycyjnymi dwuskładnikowymi powłokami epoksydowymi, ale przy uproszczonych procesach aplikacji. Powłoki te zawierają żywicę zawierającą zarówno żywicę epoksydową, jak i utwardzacz, co eliminuje potrzebę stosowania oddzielnego utwardzacza. W tym artykule zbadamy właściwości, zastosowania i zalety jednoskładnikowych powłok epoksydowych.
Charakterystyka: Jednoskładnikowe powłoki epoksydowe posiadają kilka kluczowych cech, które czynią je popularnymi w różnych gałęziach przemysłu. Powłoki te wykazują doskonałą przyczepność do różnych podłoży, w tym betonu, metalu i drewna, zapewniając solidne wiązanie i długotrwałą ochronę. Zapewniają dobrą odporność chemiczną, zapewniając ochronę przed substancjami korozyjnymi, chemikaliami i rozpuszczalnikami. Dodatkowo jednoskładnikowe powłoki epoksydowe zapewniają dobrą odporność na ścieranie i trwałość, dzięki czemu nadają się do powierzchni narażonych na intensywny ruch lub zużycie. Można je również formułować z różnymi wykończeniami, takimi jak błyszczące lub matowe, aby uzyskać pożądany efekt estetyczny.
Aplikacje: Jednoskładnikowe powłoki epoksydowe znajdują zastosowanie w różnych branżach i na różnych powierzchniach. W branży budowlanej są powszechnie stosowane do ochrony i ulepszania posadzek betonowych, zapewniając bezproblemowe i trwałe pokrycie w miejscach takich jak magazyny, powierzchnie handlowe i budynki komercyjne. Powłoki te znajdują również zastosowanie w przemyśle motoryzacyjnym, gdzie są wykorzystywane do ochrony antykorozyjnej podwozi pojazdów, elementów podwozia oraz innych powierzchni metalowych. Ponadto jednoskładnikowe powłoki epoksydowe są stosowane w przemyśle morskim na pokładach łodzi, basenach i konstrukcjach morskich, zapewniając odporność na wodę, promieniowanie UV i chemikalia. Mogą być również stosowane na powierzchniach metalowych, takich jak maszyny, urządzenia lub zbiorniki magazynowe, w celu ochrony przed korozją i zużyciem.
Korzyści: Jednoskładnikowe powłoki epoksydowe mają kilka zalet, które czynią je korzystnymi w wielu zastosowaniach. Jedną z kluczowych zalet jest łatwość użytkowania i aplikacji. Ponieważ są one wstępnie zmieszane, nie ma potrzeby odmierzania i mieszania wielu składników, co upraszcza proces powlekania i zmniejsza ryzyko błędów. Dzięki temu idealnie nadają się do mniejszych projektów lub użytkowników z ograniczonym doświadczeniem w zakresie powłok epoksydowych. Ponadto jednoskładnikowe powłoki epoksydowe mają często dłuższą żywotność niż systemy dwuskładnikowe, co pozwala na dłuższy czas pracy i prostszą aplikację. Oferują również doskonałą przyczepność, trwałość i odporność chemiczną, zapewniając długotrwałą ochronę powlekanych powierzchni. Co więcej, jednoskładnikowe powłoki epoksydowe mają zwykle niską zawartość lotnych związków organicznych (LZO), dzięki czemu są przyjazne dla środowiska i bezpieczniejsze dla użytkowników.
Wybór odpowiedniej izolacyjnej powłoki epoksydowej
Wybór izolującej powłoki epoksydowej ma kluczowe znaczenie dla zapewnienia odpowiedniej izolacji i ochrony dla różnych zastosowań. Izolacyjne powłoki epoksydowe mają na celu zapewnienie izolacji elektrycznej i odporności termicznej, zapobiegając przewodzeniu elektrycznemu i przenoszeniu ciepła. Oto kilka kluczowych czynników, które należy wziąć pod uwagę przy wyborze odpowiedniej izolacyjnej powłoki epoksydowej:
- Właściwości elektryczne: Podstawową funkcją izolacyjnej powłoki epoksydowej jest zapewnienie izolacji elektrycznej. Dlatego konieczne jest uwzględnienie właściwości elektrycznych powłoki, takich jak wytrzymałość dielektryczna, rezystywność skrośna i rezystywność powierzchniowa. Wytrzymałość dielektryczna określa maksymalne napięcie, jakie powłoka może wytrzymać przed przebiciem, podczas gdy rezystywność mierzy zdolność materiału do przeciwstawiania się przepływowi prądu elektrycznego. Upewnij się, że warstwa spełnia wymagane normy elektryczne dla konkretnego zastosowania.
- Odporność termiczna: Oczekuje się, że izolacyjne powłoki epoksydowe będą również zapewniać odporność termiczną, aby zapobiec przenoszeniu ciepła. Weź pod uwagę zdolność powłoki do wytrzymywania wysokich temperatur i zapewniania skutecznej izolacji termicznej. Szukaj warstw o niskiej przewodności cieplnej, aby zminimalizować przenoszenie ciepła i zachować stabilność temperatury.
- Kompatybilność podłoża: Oceń kompatybilność powłoki epoksydowej z materiałem podłoża. Izolacyjne powłoki epoksydowe są powszechnie stosowane na metalach miedzianych, aluminiowych lub stalowych. Upewnij się, że powłoka jest tak skomponowana, aby dobrze przylegała do określonego materiału podłoża, zapewniając silne wiązanie i długotrwałą wydajność.
- Metoda aplikacji: Rozważ metodę aplikacji i łatwość aplikacji wybranej izolacyjnej powłoki epoksydowej. Niektóre powłoki nadają się do nakładania natryskowego, podczas gdy inne bardziej nadają się do nakładania pędzlem lub wałkiem. Wybierz warstwę, która jest zgodna z dostępnym sprzętem do aplikacji i wymaganiami projektu.
- Odporność środowiskowa: Oceń warunki ekologiczne, na które będzie narażona powłoka, takie jak wilgotność, chemikalia lub promieniowanie UV. Izolacyjne powłoki epoksydowe powinny zapewniać doskonałą odporność na te czynniki środowiskowe, aby zapewnić długotrwałą wydajność i ochronę. Rozważ powłoki o wysokiej odporności chemicznej i odporności na promieniowanie UV w przypadku narażenia na trudne warunki środowiskowe.
- Certyfikaty i normy: W zależności od zastosowania mogą być wymagane określone certyfikaty lub normy. Na przykład izolacyjne powłoki epoksydowe mogą wymagać spełnienia określonych norm elektrycznych lub certyfikatów w branży elektrycznej. Upewnij się, że wybrana powłoka spełnia standardy i certyfikaty branżowe, aby zapewnić zgodność i wydajność.
- Wydajność i trwałość: Weź pod uwagę ogólną wydajność i trwałość izolacyjnej powłoki epoksydowej. Szukaj warstw o doskonałej przyczepności, odporności na ścieranie i długotrwałej trwałości, aby zapewnić trwałą izolację i ochronę. Oceń odporność powłoki na uszkodzenia fizyczne, takie jak uderzenia lub zarysowania, które mogą pogorszyć właściwości izolacyjne.
- Koszt i wartość: Na koniec oceń koszt i wartość izolacyjnej powłoki epoksydowej. Należy wziąć pod uwagę takie czynniki, jak koszt początkowy, oczekiwana żywotność warstwy oraz potencjalne koszty konserwacji lub wymiany w czasie. Zrównoważenie początkowej inwestycji z długoterminową wydajnością i trwałością pomoże określić ogólną wartość powłoki.
Względy środowiskowe
Względy środowiskowe odgrywają znaczącą rolę w wyborze i zastosowaniu izolacyjnych powłok epoksydowych. Wybór powłok, które zapewniają odpowiednią izolację i minimalizują wpływ na środowisko przez cały cykl życia, ma kluczowe znaczenie. Oto kilka krytycznych kwestii ekologicznych, o których należy pamiętać przy wyborze izolacyjnych powłok epoksydowych:
- Zawartość LZO: Lotne związki organiczne (VOC) to substancje chemiczne, które mogą przyczyniać się do zanieczyszczenia powietrza i mieć potencjalny wpływ na zdrowie. Wybierając izolujące powłoki epoksydowe, wybierz preparaty o niskiej zawartości LZO lub bez LZO. Powłoki te emitują mniej szkodliwych oparów podczas aplikacji i przyczyniają się do poprawy jakości powietrza wewnątrz i na zewnątrz.
- Substancje niebezpieczne: Oceń obecność substancji niebezpiecznych w preparacie powłoki epoksydowej. Niektóre dodatki, rozpuszczalniki lub metale ciężkie mogą szkodzić zdrowiu ludzkiemu lub środowisku. Szukaj powłok wolnych od substancji niebezpiecznych lub o obniżonej zawartości substancji niebezpiecznych, zapewniających bezpieczniejszą obsługę, utylizację i długotrwały wpływ na środowisko.
- Biodegradowalność: Należy wziąć pod uwagę biodegradowalność izolacyjnej powłoki epoksydowej. Powłoki ulegające biodegradacji rozkładają się naturalnie z upływem czasu, zmniejszając ich wpływ na środowisko. Szukaj warstw, które pochodzą z zasobów odnawialnych lub które zostały przetestowane i certyfikowane pod kątem ich biodegradowalności.
- Efektywność energetyczna: Izolacyjne powłoki epoksydowe często poprawiają efektywność energetyczną poprzez zmniejszenie wymiany ciepła. Wybierając powłoki o wysokiej odporności termicznej, można zwiększyć efektywność energetyczną w zastosowaniach takich jak izolacja elektryczna, izolacja budynków czy bariery termiczne. Może to prowadzić do zmniejszenia zużycia energii i mniejszego wpływu na środowisko.
- Trwałość i długowieczność: wybierz izolacyjne powłoki epoksydowe o doskonałej trwałości i długowieczności. Powłoki bardziej odporne na zużycie, korozję lub degradację wymagają rzadszej konserwacji, ponownego nakładania i utylizacji. Zmniejsza to ogólny wpływ na środowisko związany ze stosowaniem powłok.
- Opakowania i odpady: Weź pod uwagę opakowanie izolujących powłok epoksydowych i wytwarzanie odpadów podczas ich użytkowania. Wybierz powłoki, które są pakowane w materiały nadające się do recyklingu lub przyjazne dla środowiska. Ponadto powłoki, które minimalizują powstawanie odpadów podczas aplikacji, takie jak te o zmniejszonej ilości natrysku lub minimalnych wymaganiach dotyczących mieszania, mogą pomóc w zmniejszeniu wpływu na środowisko.
- Certyfikaty środowiskowe: Poszukaj izolacyjnych powłok epoksydowych, które uzyskały certyfikaty ekologiczne lub są zgodne z uznanymi normami środowiskowymi. Przykładami są certyfikaty takie jak LEED (Leadership in Energy and Environmental Design) lub zgodność z normami zarządzania środowiskowego ISO 14001. Certyfikaty te zapewniają, że powłoki przeszły rygorystyczne testy i spełniają określone kryteria środowiskowe.
- Właściwa utylizacja i recykling: Rozważ odpowiednie opcje utylizacji i recyklingu izolacyjnych powłok epoksydowych. Sprawdź lokalne przepisy i wytyczne, aby upewnić się, że powłoki można odpowiednio zutylizować lub poddać recyklingowi po zakończeniu ich cyklu życia. Niektóre powłoki mogą mieć określone programy recyklingu lub dostępne opcje.
Biorąc pod uwagę te względy środowiskowe, można wybrać izolacyjne powłoki epoksydowe, które zapewniają odpowiednią izolację i minimalizują wpływ na środowisko. Wybór powłok przyjaznych dla środowiska przyczynia się do działań na rzecz zrównoważonego rozwoju, zmniejsza zanieczyszczenie i promuje zdrowszy ekosystem.
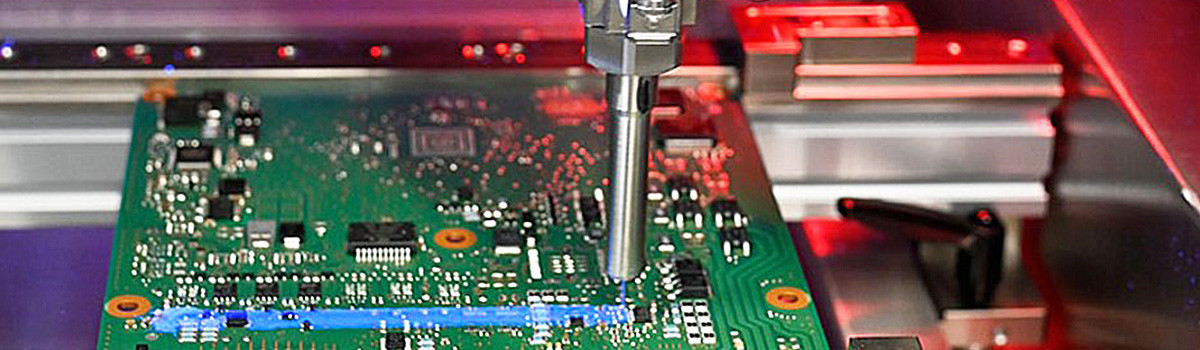
Techniki aplikacji i porady
Właściwe techniki aplikacji są niezbędne do osiągnięcia optymalnych rezultatów podczas izolowania powłok epoksydowych. Poniższe wskazówki pomogą zapewnić udaną aplikację i zwiększyć wydajność warstwy:
- Przygotowanie powierzchni: Dokładnie oczyścić i przygotować powierzchnię przed nałożeniem izolującej powłoki epoksydowej. Usuń brud, kurz, tłuszcz lub istniejące powłoki, które mogą zakłócać przyczepność. Techniki przygotowania powierzchni mogą obejmować piaskowanie, odtłuszczanie lub stosowanie odpowiednich środków czyszczących. Postępować zgodnie z wytycznymi producenta dotyczącymi przygotowania powierzchni w zależności od powłoki i podłoża.
- Proporcje mieszania i czas przydatności do spożycia: Dokładnie postępuj zgodnie z instrukcjami producenta dotyczącymi proporcji mieszania i czasu przydatności do użycia. Izolacyjne powłoki epoksydowe to zazwyczaj systemy dwuskładnikowe, które wymagają dokładnego wymieszania składników żywicy i utwardzacza. Niewłaściwe mieszanie może spowodować niepełne utwardzenie lub pogorszenie wydajności. Zwróć uwagę na czas przydatności do użycia i czas pracy dostępny po wymieszaniu składników. Unikaj przekraczania czasu przydatności do użycia, aby zapewnić prawidłową aplikację.
- Metoda aplikacji: Wybierz odpowiednią metodę aplikacji izolacyjnej powłoki epoksydowej w oparciu o wymagania dotyczące powierzchni i projektu. Standardowe metody aplikacji obejmują nakładanie pędzlem, wałkiem lub natryskiem. Używaj pędzli i wałków do mniejszych powierzchni lub gdy wymagana jest precyzja. Aplikacja natryskowa jest odpowiednia do większych pomieszczeń lub bardziej jednolitego wykończenia. Postępuj zgodnie z zaleceniami producenta dotyczącymi konkretnej powłoki, dotyczącymi metody aplikacji i sprzętu.
- Temperatura i wilgotność: Podczas aplikacji należy wziąć pod uwagę temperaturę i wilgotność otoczenia. Izolacyjne powłoki epoksydowe mogą mieć określone wymagania dotyczące temperatury i wilgotności, aby uzyskać optymalne działanie. Podczas aplikacji i utwardzania należy przestrzegać zaleceń producenta dotyczących zalecanego zakresu temperatur i wilgotności. Ekstremalne temperatury lub wysoka wilgotność mogą wpływać na czas utwardzania powłoki i ogólną wydajność.
- Grubość aplikacji: Nałożyć izolacyjną powłokę epoksydową na zalecaną grubość dla uzyskania pożądanej izolacji i ochrony. Wystarczająca grubość powłoki może pogorszyć właściwości izolacyjne, podczas gdy nadmierna grubość może prowadzić do problemów z utwardzaniem lub niewłaściwej przyczepności. Użyj miernika grubości mokrej powłoki, aby zapewnić spójną i dokładną grubość powłoki podczas całej aplikacji.
- Wentylacja i bezpieczeństwo: Zapewnić odpowiednią wentylację w miejscu aplikacji, aby zminimalizować wdychanie oparów lub oparów. Stosować odpowiednie środki ochrony osobistej (PPE) zgodnie z zaleceniami producenta, takie jak rękawice, okulary ochronne lub środki ochrony dróg oddechowych. Postępuj zgodnie z wytycznymi i przepisami bezpieczeństwa, aby chronić siebie i innych podczas procesu aplikacji.
- Czas utwardzania i schnięcia: Należy zapewnić wystarczający czas utwardzania i schnięcia izolującej powłoki epoksydowej. Postępuj zgodnie z instrukcjami producenta dotyczącymi zalecanego czasu utwardzania i warunków środowiskowych, aby uzyskać odpowiednią przyczepność i wydajność. Unikać narażania powlekanej powierzchni na działanie nadmiernej wilgoci lub naprężeń mechanicznych do czasu całkowitego utwardzenia powłoki.
- Inspekcja i konserwacja: Regularnie sprawdzaj powlekaną powierzchnię pod kątem uszkodzeń lub zużycia. Przeprowadzaj rutynową konserwację, aby zapewnić ciągłą skuteczność izolującej powłoki epoksydowej. Natychmiast rozwiązuj wszelkie problemy, aby zapobiec dalszym obrażeniom lub pogorszeniu stanu zdrowia.
Postępując zgodnie z tymi technikami aplikacji i wskazówkami, można osiągnąć dobre wyniki podczas nakładania izolujących powłok epoksydowych. Właściwe przygotowanie powierzchni, dokładne wymieszanie, odpowiednie metody aplikacji i przestrzeganie wytycznych dotyczących utwardzania pomogą zapewnić pożądaną izolację i ochronę aplikacji.
Proces utwardzania i suszenia
Proces utwardzania i suszenia izolacyjnych powłok epoksydowych jest krytycznym etapem, który określa końcowe właściwości i wydajność powłoki. Właściwe utwardzenie zapewnia mocną, trwałą iw pełni izolującą warstwę. Oto kluczowe czynniki i uwagi dotyczące procesu utwardzania i suszenia izolacyjnych powłok epoksydowych:
- Postępuj zgodnie z instrukcjami producenta: Zawsze zapoznaj się z instrukcjami producenta i arkuszem danych technicznych, aby uzyskać szczegółowe wskazówki dotyczące czasu utwardzania i schnięcia oraz warunków środowiskowych wymaganych dla powłoki. Różne powłoki epoksydowe mogą mieć różne procesy utwardzania i zalecane czasy schnięcia.
- Temperatura otoczenia: Proces utwardzania powłok epoksydowych jest zależny od temperatury. Większość powłok epoksydowych wymaga minimalnego i maksymalnego zakresu temperatur otoczenia do prawidłowego utwardzenia. Upewnij się, że temperatura otoczenia mieści się w określonym zakresie podczas całego procesu utwardzania i suszenia. Ekstremalne wysokie i niskie temperatury mogą niekorzystnie wpływać na proces utwardzania i końcową wydajność powłoki.
- Wilgotność względna: Poziomy wilgotności mogą również wpływać na utwardzanie i suszenie izolacyjnych powłok epoksydowych. W środowiskach o dużej wilgotności czas utwardzania może się wydłużyć z powodu powolnego odparowywania wilgoci z warstwy. I odwrotnie, niska wilgotność może spowodować zbyt szybkie utwardzenie powłoki, naruszając jej integralność. Utrzymuj zalecany poziom wilgotności określony przez producenta dla optymalnego utwardzania.
- Wentylacja: Odpowiednia wentylacja jest niezbędna podczas utwardzania i suszenia, aby zapewnić odpowiednią cyrkulację powietrza i odprowadzanie oparów lub oparów. Dobra wentylacja ułatwia proces utwardzania i zmniejsza ryzyko uwięzienia rozpuszczalnika, co mogłoby wpłynąć na działanie powłoki.
- Czas utwardzania: Czas utwardzania izolacyjnych powłok epoksydowych może się różnić w zależności od konkretnego preparatu, grubości nałożonej warstwy i warunków otoczenia. Konieczne jest przestrzeganie zalecanego czasu utwardzania określonego przez producenta, aby zapewnić całkowite usieciowanie i uzyskanie pożądanych właściwości. Przedwczesne wystawienie na działanie wilgoci, pyłu lub naprężeń mechanicznych podczas procesu utwardzania może pogorszyć właściwości powłoki.
- Czas schnięcia: Czas schnięcia odnosi się do odparowania rozpuszczalnika z powłoki. Czas schnięcia może się różnić w zależności od grubości powłoki, temperatury, wilgotności i wentylacji. Bardzo ważne jest, aby zapewnić zalecany czas schnięcia powłoki, aby uzyskać prawidłowe utworzenie powłoki i uniknąć przedwczesnego manipulowania lub ekspozycji.
- Całkowite utwardzenie: Chociaż po zalecanym czasie schnięcia powłoka może wydawać się sucha w dotyku, należy pamiętać, że całkowite utwardzenie może potrwać dłużej. Pełne utwardzenie odnosi się do całkowitego chemicznego usieciowania i utwardzenia powłoki epoksydowej. Postępuj zgodnie z instrukcjami producenta dotyczącymi zalecanego pełnego czasu utwardzania przed poddaniem powlekanej powierzchni dużym obciążeniom, ścieraniu lub innym obciążeniom.
- Utwardzanie: Niektóre izolacyjne powłoki epoksydowe mogą skorzystać z utwardzenia w celu dalszego polepszenia ich właściwości. Dotwardzanie polega na poddaniu utwardzonej warstwy działaniu podwyższonych temperatur przez określony czas. Proces ten może poprawić odporność chemiczną, twardość i przyczepność powłoki. W stosownych przypadkach należy zapoznać się z wytycznymi producenta dotyczącymi zalecanego procesu dotwardzania.
Uważne przestrzeganie instrukcji producenta, utrzymywanie odpowiednich warunków otoczenia, zapewnienie odpowiedniego czasu utwardzania i schnięcia oraz zapewnienie odpowiedniej wentylacji pozwala osiągnąć optymalne wyniki w izolujących powłokach epoksydowych. Odpowiednio utwardzone i wysuszone powłoki zapewnią wymaganą izolację elektryczną i odporność termiczną dla zamierzonego zastosowania.
Konserwacja i naprawa izolacyjnych powłok epoksydowych
Izolacyjne powłoki epoksydowe są szeroko stosowane w różnych gałęziach przemysłu do ochrony i izolacji urządzeń i infrastruktury elektrycznej. Powłoki te zapewniają trwałą barierę ochronną, która zapobiega przedostawaniu się wilgoci, chemikaliów i innych zanieczyszczeń do podłoża. Jednak, podobnie jak każdy inny system powłok, izolacyjne powłoki epoksydowe mogą wymagać konserwacji i naprawy, aby zapewnić ich skuteczność i długowieczność.
Konserwacja izolacyjnych powłok epoksydowych polega przede wszystkim na regularnym przeglądzie i czyszczeniu. Okresowo sprawdzaj powlekane powierzchnie, aby wykryć wszelkie oznaki uszkodzeń, takie jak pęknięcia, pęcherze lub łuszczenie. Należy zwrócić szczególną uwagę na miejsca narażone na trudne warunki lub obciążenia mechaniczne, ponieważ są one bardziej podatne na uszkodzenia. Jeśli zostaną wykryte jakiekolwiek problemy, natychmiast je rozwiąż, aby zapobiec dalszemu pogorszeniu.
Czyszczenie powlekanych powierzchni jest niezbędne, aby usunąć brud, kurz, oleje i inne zanieczyszczenia, które mogą gromadzić się w miarę upływu czasu. Do delikatnego czyszczenia powierzchni używaj łagodnych, nieściernych środków czyszczących i miękkich szczotek lub ściereczek. Unikaj ostrych chemikaliów lub materiałów ściernych, które rysują lub niszczą powłokę. Regularne czyszczenie pomaga zachować właściwości izolacyjne powłoki epoksydowej i zapobiega gromadzeniu się materiałów przewodzących, które mogłyby zagrozić jej skuteczności.
Jeśli chodzi o naprawę, podejście może się różnić w zależności od rozmiaru uszkodzenia. Możesz użyć epoksydowych zestawów naprawczych zaprojektowanych specjalnie do powłok izolacyjnych w przypadku drobnych urazów, takich jak małe pęknięcia lub odpryski. Zestawy te zazwyczaj zawierają wypełniacz epoksydowy i instrukcje dotyczące jego prawidłowego stosowania. Dokładnie oczyść uszkodzony obszar, postępuj zgodnie z instrukcjami dołączonymi do sprzętu i użyj szpachlówki epoksydowej na uszkodzonej części. Pozostawić do utwardzenia zgodnie z zaleceniami producenta.
W przypadkach, gdy uszkodzenie jest bardziej znaczące, usunięcie uszkodzonej części powłoki może być konieczne, podobnie jak nałożenie nowej warstwy izolującej żywicy epoksydowej. Wymaga to starannego przygotowania powierzchni, w tym oczyszczenia i zszorstkowania obszaru wokół uszkodzenia, aby zapewnić odpowiednią przyczepność nowej powłoki. Postępuj zgodnie z wytycznymi producenta dotyczącymi nakładania nowej powłoki epoksydowej, w tym czasu utwardzania i wymagań temperaturowych.
W niektórych przypadkach bardziej praktyczne może być skorzystanie z profesjonalnej pomocy w zakresie konserwacji i naprawy izolacyjnych powłok epoksydowych. Doświadczeni wykonawcy lub specjaliści od powłok mogą ocenić zakres uszkodzeń, zalecić najodpowiedniejszą metodę naprawy i upewnić się, że ulepszona powłoka spełnia niezbędne normy i wymagania.
Pamiętaj, że regularne przeglądy i konserwacja zapobiegawcza są kluczowe dla przedłużenia żywotności izolacyjnych powłok epoksydowych. Rozwiązując drobne problemy na wczesnym etapie i przestrzegając odpowiednich procedur czyszczenia, można zminimalizować potrzebę rozległych napraw i zapewnić stałą skuteczność powłoki w zakresie ochrony i izolacji sprzętu elektrycznego i infrastruktury.
Wnioski
Izolacyjne powłoki epoksydowe mają kluczowe znaczenie w ochronie elementów elektrycznych i sprzętu przed różnymi czynnikami zewnętrznymi. W zastosowaniach obejmujących elementy elektroniczne, płytki drukowane, silniki i kable, powłoki te zapewniają niezbędną ochronę przed wilgocią, chemikaliami i uszkodzeniami fizycznymi. Właściwy dobór izolacyjnej powłoki epoksydowej zależy od warunków środowiskowych, wymagań eksploatacyjnych i techniki aplikacji. Rozumiejąc korzyści i kwestie związane z izolacyjnymi powłokami epoksydowymi, przemysł może dokonywać świadomych wyborów w celu zwiększenia trwałości, niezawodności i długowieczności swoich systemów elektrycznych i sprzętu.