Klej półprzewodnikowy
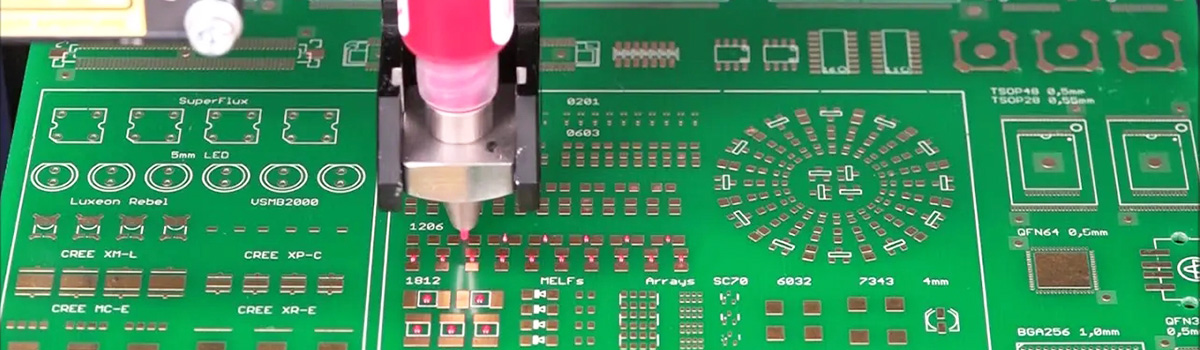
Klej półprzewodnikowy jest kluczowym elementem w produkcji i montażu urządzeń półprzewodnikowych, takich jak mikroprocesory, układy pamięci i inne układy scalone. Kleje te zapewniają solidne i niezawodne możliwości łączenia oraz ochronę przed czynnikami środowiskowymi i naprężeniami termicznymi. Wraz z rosnącym zapotrzebowaniem na mniejsze, szybsze i bardziej złożone urządzenia półprzewodnikowe, wysokowydajne i niezawodne rozwiązania klejące stały się ważniejsze niż kiedykolwiek. W tym artykule zbadamy różne rodzaje, zastosowania i wyzwania związane z klejami półprzewodnikowymi, podkreślając ich kluczową rolę w umożliwieniu miniaturyzacji i wysokiej wydajności urządzeń półprzewodnikowych.
Rodzaje klejów półprzewodnikowych
Kleje półprzewodnikowe odgrywają kluczową rolę w procesach produkcji i montażu urządzeń elektronicznych. Kleje te zostały zaprojektowane w celu zapewnienia solidnego i niezawodnego łączenia różnych elementów urządzeń półprzewodnikowych, takich jak układy scalone, podłoża i opakowania. Mogą wytrzymać trudne warunki środowiskowe, cykle termiczne i obciążenia mechaniczne. Na rynku dostępnych jest kilka rodzajów klejów półprzewodnikowych, z których każdy ma unikalne właściwości i zastosowania. Przyjrzyjmy się niektórym powszechnie stosowanym klejom półprzewodnikowym:
- Kleje epoksydowe: Kleje epoksydowe są szeroko stosowane w zastosowaniach półprzewodnikowych ze względu na ich doskonałą siłę wiązania, wysoką odporność chemiczną i dobre właściwości izolacji elektrycznej. Zapewniają silną przyczepność do różnych materiałów, w tym metali, ceramiki i tworzyw sztucznych. Kleje epoksydowe utwardzają się w temperaturze pokojowej lub pod wpływem ciepła, tworząc sztywne i trwałe wiązanie.
- Kleje silikonowe: Kleje na bazie silikonu są znane ze swojej elastyczności, stabilności termicznej i odporności na ekstremalne temperatury. W zależności od składu mogą wytrzymać szeroki zakres temperatur od -50°C do 200°C lub nawet więcej. Kleje silikonowe wykazują doskonałe właściwości izolacji elektrycznej i są powszechnie stosowane w aplikacjach, w których zarządzanie termiczne ma kluczowe znaczenie, takich jak urządzenia energoelektroniczne.
- Kleje akrylowe: Kleje akrylowe zapewniają szybkie utwardzanie, wysoką siłę wiązania oraz dobrą odporność na temperaturę i wilgoć. Są znane ze swojej wszechstronności i mogą wiązać się z różnymi podłożami, w tym metalami, tworzywami sztucznymi i szkłem. Kleje akrylowe, takie jak elektronika samochodowa i montaż diod LED, są często stosowane w aplikacjach wymagających dużej wytrzymałości i trwałości.
- Kleje poliuretanowe: Kleje poliuretanowe zapewniają równowagę między elastycznością a wytrzymałością. Zapewniają dobrą przyczepność do różnych materiałów, w tym metali, tworzyw sztucznych i szkła. Kleje poliuretanowe są odporne na uderzenia, wibracje i cykle termiczne, dzięki czemu nadają się do zastosowań, w których występują naprężenia mechaniczne, takich jak elektronika samochodowa i lotnicza.
- Kleje przewodzące: Kleje przewodzące są formułowane z przewodzącymi wypełniaczami, takimi jak srebro, miedź lub węgiel, aby umożliwić przewodnictwo elektryczne w klejonych połączeniach. Są powszechnie używane do mocowania matrycowego urządzeń elektronicznych, łączenia typu flip-chip i łączenia elementów. Kleje przewodzące zapewniają niską rezystancję i doskonałą przyczepność, zapewniając niezawodne połączenia elektryczne.
- Kleje do wypełniania: Kleje do wypełniania są przeznaczone specjalnie do zastosowań typu flip-chip, w których chip jest montowany do góry nogami na podłożu. Kleje te płyną pod chipem podczas utwardzania, wypełniając szczeliny między chipem a podłożem. Kleje wypełniające zapewniają wsparcie mechaniczne, poprawiają przewodność cieplną i zapobiegają uszkodzeniom połączeń lutowanych spowodowanych naprężeniami termicznymi.
- Kleje utwardzane promieniami UV: Kleje utwardzane promieniowaniem UV utwardzają się szybko pod wpływem światła ultrafioletowego. Oferują wysoką siłę wiązania, przejrzystość optyczną i odporność chemiczną. Kleje utwardzane promieniowaniem UV są często stosowane w zastosowaniach wymagających szybkiego przetwarzania i precyzyjnego łączenia, takich jak montaż wyświetlaczy, światłowody i urządzenia optoelektroniczne.
Kleje epoksydowe: najczęstszy wybór
Kleje epoksydowe są powszechnie uznawane za jeden z najbardziej powszechnych i wszechstronnych rodzajów. Są szeroko stosowane w różnych branżach i zastosowaniach ze względu na ich wyjątkową siłę wiązania, trwałość i wszechstronność. Tutaj zbadamy, dlaczego kleje epoksydowe są najczęstszym wyborem przy ograniczonej liczbie słów.
- Siła wiązania: Kleje epoksydowe oferują wyjątkową siłę wiązania, dzięki czemu nadają się do różnych materiałów. Niezależnie od tego, czy chodzi o metale, tworzywa sztuczne, ceramikę, drewno czy kompozyty, kleje epoksydowe zapewniają solidne i niezawodne wiązania, zapewniając długowieczność i stabilność łączonych części.
- Wszechstronność: Kleje epoksydowe wykazują doskonałą wszechstronność w metodach aplikacji i opcjach utwardzania. Dostępne są w różnych formach, takich jak systemy jednoczęściowe lub dwuczęściowe, co pozwala na elastyczność w ich zastosowaniu. Ponadto kleje epoksydowe można utwardzać w temperaturze pokojowej lub pod wpływem ciepła, w zależności od specyficznych wymagań aplikacji.
- Odporność chemiczna: Kleje epoksydowe mają wyjątkową odporność chemiczną, dzięki czemu idealnie nadają się do zastosowań, w których narażenie na działanie agresywnych chemikaliów lub rozpuszczalników stanowi problem. Zachowują integralność strukturalną nawet w przypadku wystawienia na działanie różnych chemikaliów, olejów, paliw i kwasów, zapewniając trwałość połączonych zespołów.
- Odporność na temperaturę: Kleje epoksydowe mogą wytrzymać szeroki zakres temperatur, dzięki czemu nadają się do zastosowań wymagających odporności na wysokie lub niskie temperatury. Czy to w przemyśle motoryzacyjnym, lotniczym czy elektronicznym, kleje epoksydowe zapewniają niezawodne łączenie nawet w ekstremalnych temperaturach.
- Zdolność do wypełniania szczelin: Kolejną zaletą klejów epoksydowych jest ich zdolność do wypełniania szczelin i nierówności między współpracującymi powierzchniami. Ta cecha zapewnia silne wiązanie nawet wtedy, gdy powierzchnie styku nie są idealnie dopasowane, zapewniając zwiększoną integralność strukturalną łączonych części.
- Właściwości mechaniczne: Kleje epoksydowe oferują doskonałe właściwości mechaniczne, takie jak wysoka wytrzymałość na rozciąganie i ścinanie oraz dobra odporność na uderzenia. Te właściwości sprawiają, że nadają się do zastosowań nośnych, w których klej musi wytrzymać znaczne naprężenia lub uderzenia bez uszczerbku dla siły wiązania.
- Izolacja elektryczna: Kleje epoksydowe wykazują doskonałe właściwości izolacji elektrycznej, dzięki czemu są popularne w zastosowaniach elektronicznych i elektrycznych. Zapewniają skuteczną izolację, chroniąc wrażliwe elementy elektroniczne przed prądem elektrycznym lub zwarciem.
- Łatwość użycia: Kleje epoksydowe są stosunkowo łatwe w użyciu i nakładaniu. Można je precyzyjnie dozować, co pozwala na kontrolowaną aplikację i minimalizację strat. Ponadto kleje epoksydowe mają długi czas otwarty, co zapewnia wystarczający czas pracy na montaż części przed związaniem kleju.
Kleje przewodzące: umożliwianie połączeń elektrycznych
Kleje przewodzące są specjalistycznym rodzajem materiału klejącego o właściwościach zarówno adhezyjnych, jak i przewodzących. Zostały zaprojektowane, aby umożliwić łączność elektryczną w różnych zastosowaniach, w których tradycyjne metody lutowania mogą nie być wykonalne lub pożądane. Kleje te oferują wiele zalet, w tym łatwość użycia, przyjazność dla środowiska i wszechstronność.
Jedną z najważniejszych zalet klejów przewodzących jest łatwość ich użycia. W przeciwieństwie do lutowania, które wymaga ciepła i może być skomplikowane, kleje przewodzące można nakładać po prostu przez dozowanie lub rozprowadzenie kleju na żądanych powierzchniach. Dzięki temu są odpowiednie dla szerokiego grona użytkowników, od profesjonalistów po hobbystów, i eliminują potrzebę stosowania specjalistycznego sprzętu.
Przyjazność dla środowiska to kolejna zaleta klejów przewodzących. W przeciwieństwie do lutowania, które zwykle obejmuje lutowie na bazie ołowiu, kleje przewodzące można łączyć z nietoksycznymi materiałami. Dzięki temu są bardziej przyjazne dla środowiska i bezpieczniejsze w obsłudze, zmniejszając ryzyko dla zdrowia użytkowników. Dodatkowo brak ołowiu sprawia, że kleje te są zgodne z przepisami ograniczającymi stosowanie substancji niebezpiecznych.
Kleje przewodzące oferują również wszechstronność materiałów, które mogą ze sobą łączyć. Mogą łączyć materiały przewodzące, takie jak metale, oraz materiały nieprzewodzące, takie jak tworzywa sztuczne, ceramika i szkło. Ta szeroka kompatybilność pozwala na tworzenie wielomateriałowych zespołów ze zintegrowaną łącznością elektryczną, otwierając nowe możliwości projektowe w różnych branżach.
Przewodnictwo tych klejów uzyskuje się przez włączenie przewodzących wypełniaczy, takich jak cząstki srebra lub węgla, do matrycy kleju. Te wypełniacze tworzą ścieżki przewodzące, które umożliwiają przepływ prądu elektrycznego przez łączone powierzchnie. Wybór materiału i stężenia wypełniacza można dostosować do określonych wymagań dotyczących przewodności, co pozwala na precyzyjne dostrojenie właściwości elektrycznych kleju.
Zastosowania klejów przewodzących są szeroko rozpowszechnione. Są powszechnie stosowane w przemyśle elektronicznym do łączenia elementów, zastępowania lub uzupełniania procesów lutowniczych. Kleje przewodzące są szczególnie przydatne do łączenia delikatnych elementów elektronicznych, które nie wytrzymują wysokich temperatur związanych z lutowaniem. Są również wykorzystywane do produkcji elastycznych obwodów, etykiet RFID i ekranów dotykowych, gdzie ich zdolność do łączenia się z różnymi podłożami jest korzystna.
W przemyśle motoryzacyjnym kleje przewodzące służą do montażu czujników, jednostek sterujących i systemów oświetleniowych. Ich niemechaniczne możliwości łączenia zmniejszają punkty skupienia naprężeń, poprawiając niezawodność połączeń elektrycznych i długowieczność. Co więcej, kleje przewodzące umożliwiają zmniejszenie ciężaru pojazdów poprzez wyeliminowanie konieczności stosowania ciężkich metalowych złączy.
Poza elektroniką i zastosowaniami motoryzacyjnymi kleje przewodzące znajdują zastosowanie w urządzeniach medycznych, komponentach lotniczych, a nawet w produktach konsumenckich, takich jak elektronika ubieralna. Ich wszechstronność, łatwość użycia i zalety środowiskowe czynią je atrakcyjnymi dla projektantów przemysłowych i inżynierów.
Kleje do matryc: klejenie chipów półprzewodnikowych z podłożami
Kleje do mocowania matryc odgrywają kluczową rolę w przemyśle półprzewodnikowym, zapewniając niezawodną i wydajną metodę łączenia chipów półprzewodnikowych z podłożami. Kleje te służą jako interfejs między chipem a podłożem, zapewniając bezpieczne i przewodzące elektrycznie połączenie.
Podstawową funkcją klejów mocowanych matrycowo jest zapewnienie mechanicznego wsparcia i połączenia elektrycznego między chipem a podłożem. Muszą one charakteryzować się doskonałymi właściwościami adhezyjnymi, aby zapewnić bezpieczne mocowanie chipa do podłoża w różnych warunkach pracy, w tym w cyklach termicznych, naprężeniach mechanicznych i narażeniu środowiskowym.
Jednym z krytycznych wymagań dotyczących klejów do naklejania na matryce jest ich odporność na wysokie temperatury. Podczas procesów montażu układów scalonych, takich jak lutowanie rozpływowe lub łączenie termokompresyjne, klej musi zachować swoją integralność i siłę przyczepności. Zazwyczaj kleje do przyklejania matrycą są zaprojektowane tak, aby wytrzymywały temperatury powyżej 200°C, zapewniając niezawodne wiązanie.
Kleje do mocowania matryc są powszechnie klasyfikowane jako kleje na bazie żywic epoksydowych i kleje na bazie lutu. Kleje epoksydowe to materiały termoutwardzalne, które utwardzają się pod wpływem ciepła. Zapewniają doskonałą przyczepność, wysoką przewodność cieplną i izolację elektryczną. Z drugiej strony kleje na bazie lutu składają się ze stopu metalu, który topi się podczas procesu łączenia. Zapewniają ścieżkę elektryczną o niskiej rezystancji i wysoką przewodność cieplną, dzięki czemu nadają się do zastosowań z rozpraszaniem dużej mocy.
Wybór kleju mocowanego na matrycy zależy od kilku czynników, w tym konkretnego zastosowania, warunków pracy i materiału podłoża. Klej musi być kompatybilny z materiałami, do których będzie klejony, zapewniając odpowiednią przyczepność i zapobiegając wszelkim niekorzystnym interakcjom. Klej musi również charakteryzować się dobrymi właściwościami dozowania i płynięcia, aby ułatwić wiązanie i zminimalizować puste przestrzenie lub szczeliny między chipem a podłożem.
Aby uzyskać niezawodne wiązanie, niezbędne jest przygotowanie powierzchni. Podłoże i powierzchnie wiórów należy dokładnie oczyścić z zanieczyszczeń, tlenków i innych zanieczyszczeń utrudniających przyczepność. Techniki obróbki powierzchni, takie jak czyszczenie plazmowe, trawienie chemiczne lub czyszczenie ultradźwiękowe, są powszechnie stosowane w celu zwiększenia wydajności wiązania kleju.
Po nałożeniu kleju do mocowania matrycy chip jest ostrożnie umieszczany i wyrównywany na podłożu. Można zastosować ciśnienie lub ciepło, aby zapewnić odpowiednie zwilżenie i kontakt między klejem a klejonymi powierzchniami. Klej jest następnie utwardzany lub zestalany, kończąc proces wiązania.
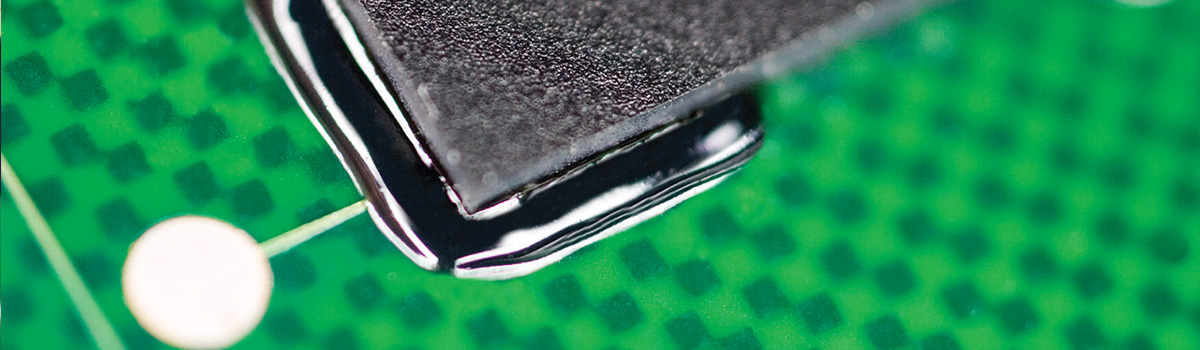
Kleje wypełniające: ochrona przed stresem termicznym
Kleje wypełniające to podstawowe materiały stosowane w opakowaniach elektronicznych w celu ochrony przed naprężeniami termicznymi. Zapewniają wzmocnienie mechaniczne i poprawiają niezawodność urządzeń elektronicznych, minimalizując wpływ cykli termicznych i wstrząsów mechanicznych.
Naprężenie termiczne jest poważnym problemem w zespołach elektronicznych ze względu na niedopasowanie współczynników rozszerzalności cieplnej (CTE) między różnymi materiałami. Gdy urządzenie podlega wahaniom temperatury, materiały rozszerzają się i kurczą w różnym tempie, powodując naprężenia, które mogą zawieść. Kleje wypełniające pomagają złagodzić ten problem, działając jako bufor między chipem a podłożem, pochłaniając i rozprowadzając naprężenia spowodowane cyklami termicznymi.
Podstawową funkcją klejów wypełniających jest wzmacnianie połączeń lutowanych, które łączą układ scalony (IC) z podłożem. Podczas produkcji chip jest montowany na podłożu za pomocą lutu, który tworzy wiązanie między dwoma komponentami. Jednak niedopasowanie CTE między chipem a podłożem może powodować koncentrację naprężeń w połączeniach lutowanych. Kleje podkładowe są wtryskiwane w szczelinę między chipem a podłożem, wypełniając puste przestrzenie i tworząc mocną i elastyczną warstwę. Ta warstwa zmniejsza koncentrację naprężeń, poprawiając ogólną integralność mechaniczną zespołu.
Kleje wypełniające zapewniają również doskonałe przewodnictwo cieplne, kluczowe dla rozpraszania ciepła wytwarzanego przez elementy elektroniczne. Skuteczne odprowadzanie ciepła ma kluczowe znaczenie dla zapobiegania przegrzaniu oraz utrzymania wydajności i trwałości urządzenia. Ułatwiając przenoszenie ciepła z chipa na podłoże, kleje wypełniające pomagają utrzymać stabilną temperaturę roboczą i zapobiegają uszkodzeniu układu scalonego przez naprężenia termiczne.
Ponadto kleje podkładowe chronią przed wilgocią i zanieczyszczeniami. Urządzenia elektroniczne są często narażone na trudne warunki, w tym wilgoć i różne chemikalia, które mogą obniżyć ich wydajność i niezawodność. Materiały wypełniające stanowią barierę, zapobiegając wnikaniu wilgoci i przenikaniu szkodliwych substancji do opakowania wiórów. Ta ochrona pomaga utrzymać parametry elektryczne i wydłużyć żywotność urządzenia.
Kleje typu Flip Chip: umożliwiają miniaturyzację
Kleje typu Flip Chip mają kluczowe znaczenie dla umożliwienia miniaturyzacji różnych urządzeń elektronicznych. Wraz z postępem technologicznym istnieje stałe zapotrzebowanie na mniejsze, lżejsze i mocniejsze maszyny. Łączenie typu flip-chip stało się preferowaną metodą uzyskiwania połączeń o dużej gęstości w takich urządzeniach. Kleje te ułatwiają bezpośrednie elektryczne i mechaniczne połączenie między chipem a podłożem, oferując liczne korzyści w zakresie miniaturyzacji.
Jedną z krytycznych zalet klejów typu flip-chip jest ich zdolność do zmniejszania całkowitego rozmiaru opakowań elektronicznych. Tradycyjne techniki łączenia przewodów wymagają miejsca na pętle z drutu, co ogranicza osiągalny rozmiar urządzenia. Natomiast łączenie typu flip-chip eliminuje potrzebę stosowania pętli z drutu, znacznie zmniejszając rozmiar opakowania. Mniejsza powierzchnia jest istotna w przenośnych urządzeniach elektronicznych, takich jak smartfony, tablety i urządzenia do noszenia, gdzie przestrzeń jest na wagę złota.
Dodatkowo kleje typu flip-chip umożliwiają zwiększenie wydajności urządzenia. Bezpośrednie połączenie elektryczne między chipem a podłożem zmniejsza długość ścieżki sygnału i indukcyjność, poprawiając wydajność elektryczną. Jest to szczególnie ważne w zastosowaniach o dużej szybkości, takich jak mikroprocesory i układy pamięci, gdzie minimalizacja opóźnień i strat sygnału ma kluczowe znaczenie. Flip chip bonding przyczynia się do szybszego transferu danych, mniejszego zużycia energii i zwiększonej niezawodności urządzenia poprzez ograniczenie efektów pasożytniczych.
Ponadto kleje typu flip-chip oferują doskonałe możliwości zarządzania termicznego. Zarządzanie rozpraszaniem ciepła staje się poważnym wyzwaniem, ponieważ komponenty elektroniczne stają się coraz mocniejsze i gęsto upakowane. Flip chip bonding pozwala na bezpośrednie mocowanie chipa do podłoża, co poprawia efektywność wymiany ciepła. Umożliwia to efektywne odprowadzanie ciepła, zapobiegając przegrzaniu i poprawiając ogólną niezawodność i żywotność urządzenia. Efektywne zarządzanie temperaturą jest niezbędne w przypadku urządzeń o wysokiej wydajności, takich jak procesory graficzne (GPU) i jednostki centralne (CPU).
Kolejną zaletą klejów typu flip-chip jest ich stabilność mechaniczna. Materiały klejące stosowane w łączeniu typu flip-chip zapewniają solidne i niezawodne połączenia. Brak połączeń drutowych eliminuje ryzyko pęknięcia lub zmęczenia drutu, zapewniając długotrwałą integralność mechaniczną. Wytrzymałość klejów typu flip-chip sprawia, że nadają się one do zastosowań narażonych na trudne warunki pracy, takich jak elektronika samochodowa lub systemy lotnicze.
Ponadto kleje typu flip-chip obsługują połączenia o dużej gęstości. Dzięki łączeniu typu flip-chip możliwe jest osiągnięcie dużej liczby połączeń na małej powierzchni, co pozwala na integrację większej liczby funkcji w ograniczonej przestrzeni. Jest to szczególnie korzystne w przypadku złożonych urządzeń elektronicznych, które wymagają wielu połączeń wejścia/wyjścia, takich jak układy scalone, czujniki lub systemy mikroelektromechaniczne (MEMS). Połączenia o dużej gęstości, które umożliwiają kleje typu flip-chip, przyczyniają się do ogólnej miniaturyzacji urządzenia.
Kleje do kapsułkowania: ochrona wrażliwych elementów
Kleje do hermetyzacji są niezbędne do ochrony wrażliwych elementów elektronicznych przed różnymi czynnikami środowiskowymi, naprężeniami mechanicznymi i narażeniem chemicznym. Kleje te zapewniają barierę ochronną, otaczając elementy i zapewniając ich długowieczność i niezawodność. W tym artykule zbadamy znaczenie klejów do enkapsulacji i ich rolę w zabezpieczaniu wrażliwych komponentów.
Wrażliwe elementy elektroniczne, takie jak układy scalone, czujniki i delikatne okablowanie, są podatne na uszkodzenia spowodowane wilgocią, kurzem, wahaniami temperatury i uderzeniami fizycznymi. Kleje do kapsułkowania oferują niezawodne rozwiązanie, tworząc warstwę ochronną wokół tych elementów. Działają jak bariera, chroniąc komponenty przed elementami zewnętrznymi, które mogłyby zagrozić funkcjonalności lub doprowadzić do przedwczesnej awarii.
Jedną z krytycznych właściwości klejów do enkapsulacji jest ich odporność na wnikanie wilgoci. Wilgoć może powodować korozję, zwarcia i wycieki elektryczne, prowadząc do nieprawidłowego działania urządzenia. Kleje do enkapsulacji zapewniają doskonałą odporność na wilgoć, zapobiegając przedostawaniu się wody lub pary wodnej do wrażliwych elementów. Ta cecha ma kluczowe znaczenie w zastosowaniach narażonych na wysoką wilgotność lub w środowiskach bogatych w wilgoć, takich jak elektronika samochodowa lub zewnętrzny sprzęt przemysłowy.
Oprócz ochrony przed wilgocią, kleje do enkapsulacji zapewniają również doskonałą odporność chemiczną. Mogą wytrzymać działanie różnych chemikaliów, w tym rozpuszczalników, kwasów, zasad i środków czyszczących. Ta odporność zapewnia, że wrażliwe komponenty pozostają nienaruszone przez interakcje chemiczne, zachowując ich integralność i funkcjonalność.
Kleje do enkapsulacji zapewniają również mechaniczną ochronę wrażliwych elementów. Działają jak amortyzatory, rozpraszając naprężenia mechaniczne i wibracje, które mogłyby uszkodzić komponenty. Ta funkcja jest niezbędna w aplikacjach narażonych na częste ruchy, takich jak lotnictwo, motoryzacja i elektronika użytkowa.
Ponadto kleje do kapsułkowania oferują doskonałe właściwości zarządzania termicznego. Posiadają wysoką przewodność cieplną, co pozwala na efektywne odprowadzanie ciepła z wrażliwych elementów. Kleje te pomagają utrzymać optymalną temperaturę roboczą, skutecznie rozpraszając ciepło, zapobiegając naprężeniom termicznym i zapewniając długoterminową niezawodność.
Kolejną zaletą klejów do kapsułkowania jest ich zdolność do zwiększania integralności strukturalnej zespołów elektronicznych. Hermetyzacja i łączenie ze sobą różnych komponentów zapewnia dodatkową wytrzymałość i stabilność całego systemu. Ta cecha jest szczególnie korzystna w zastosowaniach, w których niezbędna jest wytrzymałość mechaniczna, takich jak przemysłowe systemy sterowania lub elektronika klasy wojskowej.
Kleje do kapsułkowania są dostępne w różnych formułach, aby sprostać różnym wymaganiom aplikacji. Mogą to być płynne kleje, które utwardzają się w temperaturze pokojowej lub związki przewodzące ciepło, stosowane w zastosowaniach wymagających dużej mocy. Wybór odpowiedniego kleju zależy od takich czynników jak pożądany poziom ochrony, warunki eksploatacji, czas utwardzania oraz proces montażu.
Kleje o niskim stopniu odgazowania: krytyczne w zastosowaniach kosmicznych
Kleje o niskim poziomie odgazowywania odgrywają kluczową rolę w zastosowaniach kosmicznych, w których niezbędne jest utrzymanie czystego i kontrolowanego środowiska. Odgazowywanie odnosi się do uwalniania lotnych związków organicznych (LZO) i innych zanieczyszczeń z materiałów, w tym klejów, w warunkach próżni lub niskiego ciśnienia. Odgazowanie może uszkodzić wrażliwy sprzęt, układy optyczne i powierzchnie statków kosmicznych w ekstremalnych warunkach kosmicznych, gdzie nie ma ciśnienia atmosferycznego. Dlatego stosowanie klejów o niskim wydzielaniu gazów ma kluczowe znaczenie dla zapewnienia niezawodnej wydajności i długowieczności misji kosmicznych.
Jednym z głównych problemów związanych z odgazowywaniem jest osadzanie się zanieczyszczeń na krytycznych powierzchniach, takich jak soczewki optyczne i czujniki. Zanieczyszczenia mogą tworzyć cienką warstwę na tych powierzchniach, zmniejszając ich przezroczystość, obniżając wydajność i zakłócając pomiary naukowe. W przypadku układów optycznych nawet niewielkie zmniejszenie otwartości może znacząco wpłynąć na jakość obrazów i danych zbieranych z kosmosu. Kleje o niskim stopniu odgazowywania mają na celu zminimalizowanie uwalniania lotnych związków, zmniejszenie ryzyka zanieczyszczenia i zachowanie funkcjonalności wrażliwych instrumentów.
Innym krytycznym aspektem klejów o niskiej emisji gazów jest ich wpływ na komponenty elektroniczne i obwody. Lotne związki organiczne uwalniane podczas odgazowywania mogą powodować korozję lub degradację delikatnych układów elektronicznych, prowadząc do nieprawidłowego działania lub całkowitej awarii. Dotyczy to szczególnie statków kosmicznych, w których elementy elektroniczne są narażone na próżnię kosmiczną, ekstremalne zmiany temperatury i promieniowanie. Kleje o niskim wydzielaniu gazów są formułowane z materiałów o niskiej prężności par, co minimalizuje uwalnianie związków powodujących korozję i chroni integralność systemów elektronicznych.
Co więcej, odgazowywanie może również zagrażać zdrowiu astronautów i możliwości zamieszkania statków kosmicznych z załogą. W zamkniętych środowiskach, takich jak kapsuły kosmiczne lub stacje kosmiczne, gromadzenie się lotnych związków organicznych podczas odgazowywania może tworzyć nieprzyjemną lub niebezpieczną atmosferę. Kleje o niskim poziomie odgazowania pomagają ograniczyć to ryzyko, zmniejszając emisję związków lotnych, zapewniając astronautom bezpieczne i zdrowe środowisko podczas ich misji.
Aby osiągnąć niskie właściwości odgazowujące, kleje stosowane w zastosowaniach kosmicznych przechodzą rygorystyczne testy i procesy kwalifikacyjne. Procesy te obejmują poddawanie klejów symulowanym warunkom przestrzennym, w tym komorom próżniowym, ekstremalnym temperaturom i różnym obciążeniom środowiskowym. Kleje spełniające rygorystyczne wymagania dotyczące niskiego odgazowywania posiadają certyfikaty i dopuszczenia do użytku w misjach kosmicznych.
Kleje waflowe: redukcja kosztów i zwiększenie wydajności
Łączenie na poziomie płytek jest kluczowym procesem w przemyśle półprzewodnikowym, w którym wiele układów scalonych lub płytek jest połączonych ze sobą w celu utworzenia złożonych układów scalonych. Tradycyjnie ten proces łączenia obejmował techniki lutowania lub łączenia drutów, które wymagają precyzyjnego wyrównania i indywidualnego łączenia każdego układu scalonego, co skutkuje wyższymi kosztami i niższą wydajnością. Jednak postęp w technologii klejów utorował drogę dla klejów wiążących na poziomie płytek, które oferują redukcję kosztów i zwiększoną wydajność w produkcji półprzewodników.
Kleje łączące na poziomie płytki są zaprojektowane w celu zapewnienia niezawodnego i solidnego wiązania między płytkami lub chipami na poziomie płytki, eliminując potrzebę stosowania indywidualnych procesów łączenia. Kleje te są zwykle nakładane jako cienka warstwa między płytkami i utwardzane w kontrolowanych warunkach w celu uzyskania pożądanej siły wiązania. Oto kilka kluczowych czynników przyczyniających się do obniżenia kosztów i zwiększenia wydajności:
- Uproszczenie procesu: Kleje łączące na poziomie płytek upraszczają proces łączenia, umożliwiając jednoczesne łączenie wielu chipów lub płytek w jednym kroku. Eliminuje to potrzebę skomplikowanego wyrównywania i indywidualnego łączenia każdego chipa, oszczędzając czas i redukując koszty produkcji. Ponadto klej można nakładać równomiernie na dużą powierzchnię, zapewniając spójną przyczepność na płytce.
- Wysoka siła wiązania i niezawodność: Kleje wiążące na poziomie płytek oferują doskonałe właściwości adhezyjne, co skutkuje wysoką siłą wiązania między płytkami. To solidne wiązanie zapewnia niezawodną łączność i minimalizuje ryzyko rozwarstwienia lub awarii podczas kolejnych etapów produkcji lub działania urządzenia. Mechaniczne, termiczne i elektryczne właściwości kleju można dostosować do konkretnych wymagań aplikacji, co jeszcze bardziej zwiększa niezawodność.
- Ekonomiczne materiały: Kleje łączące na poziomie płytek często wykorzystują opłacalne materiały w porównaniu z tradycyjnymi technikami łączenia. Kleje te można formułować przy użyciu różnych polimerów, takich jak epoksydy, poliimidy lub akrylany, które są łatwo dostępne i zapewniają dobrą wydajność za rozsądną cenę. Wybór spośród różnych materiałów umożliwia producentom optymalizację doboru kleju w oparciu o wydajność, cenę i kompatybilność z różnymi podłożami.
- Poprawa wydajności: kleje wiążące na poziomie płytek przyczyniają się do poprawy wydajności w produkcji półprzewodników. Równomierne nałożenie kleju na płytkę minimalizuje ryzyko powstawania pustych przestrzeni, uwięzienia powietrza lub nierównego wiązania, co może prowadzić do defektów lub awarii. Co więcej, wyeliminowanie sklejania się pojedynczych wiórów zmniejsza ryzyko niewspółosiowości lub uszkodzeń podczas procesu łączenia, co skutkuje wyższymi uzyskami i mniejszą liczbą braków.
- Kompatybilność z zaawansowanymi technologiami pakowania: Kleje wiążące na poziomie wafla są kompatybilne z różnymi zaawansowanymi technologiami pakowania, takimi jak pakowanie na poziomie wafla (WLCSP), pakowanie na poziomie wafla (FOWLP) lub procesy integracji 3D. Te kleje umożliwiają integrację wielu układów scalonych lub różnych komponentów w kompaktowej obudowie, ułatwiając miniaturyzację i umożliwiając zaawansowaną funkcjonalność urządzeń elektronicznych.

Kleje utwardzane promieniami UV: szybkie i precyzyjne wiązanie
Kleje utwardzane promieniami UV to rewolucyjne kleje, które zapewniają szybkie i precyzyjne łączenie. Zyskały popularność w różnych gałęziach przemysłu ze względu na swoje unikalne właściwości i przewagę nad tradycyjnymi klejami. Kleje utwardzane promieniowaniem UV zazwyczaj składają się z monomeru, fotoinicjatora i stabilizatora. Pod wpływem światła ultrafioletowego (UV) kleje te przechodzą reakcję fotochemiczną, która prowadzi do szybkiego utwardzania i wiązania.
Jedną z najważniejszych zalet klejów utwardzanych promieniami UV jest ich krótki czas utwardzania. W przeciwieństwie do tradycyjnych połączeń, których pełne utwardzenie wymaga godzin, a nawet dni, kleje utwardzane promieniowaniem UV utwardzają się w ciągu kilku sekund do minut. Ten szybki czas utwardzania znacznie zwiększa wydajność produkcji i skraca czas oczekiwania na linii montażowej, co skutkuje znacznymi oszczędnościami kosztów dla producentów. Błyskawiczne tworzenie wiązania pozwala również na natychmiastową obsługę i dalszą obróbkę sklejonych elementów.
Precyzyjna zdolność wiązania klejów utwardzanych promieniowaniem UV to kolejna istotna zaleta. Klej pozostaje płynny aż do wystawienia na działanie promieni UV, zapewniając wystarczająco dużo czasu na wyrównanie i ustawienie klejonych części. Po wystawieniu kleju na działanie promieni UV szybko twardnieje, tworząc solidne i trwałe wiązanie. Ta precyzyjna zdolność łączenia jest korzystna dla zastosowań wymagających wysokiej dokładności i wąskich tolerancji, takich jak elektronika, optyka i urządzenia medyczne.
Kleje utwardzane promieniowaniem UV zapewniają również doskonałą siłę wiązania i trwałość. Utwardzony klej tworzy mocne wiązanie, które jest odporne na różne czynniki środowiskowe, w tym ekstremalne temperatury, wilgoć i chemikalia. Zapewnia to długowieczność i niezawodność łączonych elementów, dzięki czemu kleje utwardzane promieniami UV nadają się do wymagających zastosowań.
Ponadto kleje utwardzane promieniowaniem UV nie zawierają rozpuszczalników i charakteryzują się niską emisją lotnych związków organicznych (LZO). W przeciwieństwie do klejów na bazie rozpuszczalników, które wymagają wyschnięcia i uwalniają potencjalnie szkodliwe opary, kleje utwardzane promieniowaniem UV są przyjazne dla środowiska i bezpieczne. To czyni je atrakcyjnym wyborem dla branż, które chcą zmniejszyć swój wpływ na środowisko i zachować zgodność z przepisami.
Kolejnym godnym uwagi aspektem jest wszechstronność klejów utwardzanych promieniami UV. Mogą łączyć różne materiały, w tym szkło, metale, tworzywa sztuczne, ceramikę, a nawet różne podłoża. Ta szeroka kompatybilność sprawia, że kleje utwardzane promieniowaniem UV nadają się do różnorodnych zastosowań w przemyśle motoryzacyjnym, lotniczym, elektronicznym i medycznym.
Kleje w postaci pasty przewodzącej: umożliwienie elastycznej i drukowanej elektroniki
Kleje w postaci pasty przewodzącej stały się kluczową technologią umożliwiającą rozwój elastycznej i drukowanej elektroniki. Te innowacyjne materiały łączą właściwości tradycyjnych klejów z przewodnictwem metali, otwierając nowe możliwości produkcji i integracji urządzeń elektronicznych na różnych podłożach.
Jedną z głównych zalet klejów w postaci pasty przewodzącej jest ich zdolność do zapewniania zarówno przyczepności mechanicznej, jak i przewodności elektrycznej. Tradycyjne kleje są zwykle izolujące, co ogranicza ich zastosowanie w zastosowaniach elektronicznych. Z kolei kleje w postaci pasty przewodzącej zawierają cząstki przewodzące, takie jak srebro, miedź lub węgiel, które ułatwiają przepływ prądu. Ta podwójna funkcjonalność pozwala im służyć zarówno jako klej, jak i ścieżka przewodząca, co czyni je idealnymi do łączenia elementów elektronicznych lub tworzenia ścieżek przewodzących na elastycznych podłożach.
Elastyczność klejów w postaci pasty przewodzącej to kolejna kluczowa cecha, która sprawia, że nadają się one do elastycznej elektroniki. Te kleje mogą zachować swoją przewodność elektryczną nawet w przypadku zginania, rozciągania lub skręcania. Ta elastyczność ma kluczowe znaczenie w zastosowaniach, takich jak urządzenia do noszenia, elastyczne wyświetlacze i elektronika konforemna, w których tradycyjne sztywne obwody byłyby niepraktyczne lub niemożliwe do wdrożenia. Kleje w postaci pasty przewodzącej umożliwiają tworzenie solidnych i niezawodnych połączeń elektrycznych na elastycznych podłożach, zapewniając wydajność i trwałość elastycznych urządzeń elektronicznych.
Ponadto kleje w postaci pasty przewodzącej są kompatybilne z różnymi technikami drukowania, takimi jak sitodruk, druk atramentowy i druk fleksograficzny. Ta kompatybilność pozwala na masową i ekonomiczną produkcję elektroniki drukowanej. Procesy drukowania umożliwiają nakładanie klejów w postaci pasty przewodzącej w precyzyjnych wzorach, co umożliwia tworzenie złożonych obwodów i projektów elektronicznych przy minimalnych stratach materiału. Możliwość drukowania ścieżek przewodzących bezpośrednio na elastycznych podłożach upraszcza proces produkcyjny i skraca czas produkcji, czyniąc drukowaną elektronikę opłacalnym rozwiązaniem dla produkcji na dużą skalę.
Kleje w postaci pasty przewodzącej mają również zalety w zakresie odprowadzania ciepła. Obecność cząstek przewodzących w tych klejach ułatwia odprowadzanie ciepła generowanego przez elementy elektroniczne. Właściwość ta ma kluczowe znaczenie dla zapewnienia niezawodności i wydajności urządzeń wytwarzających znaczne ilości ciepła, takich jak energoelektronika czy diody LED dużej mocy. Używając przewodzących klejów w postaci pasty jako interfejsów termicznych, ciepło może być skutecznie przenoszone z elementu wytwarzającego ciepło do radiatora, poprawiając ogólną wydajność i żywotność urządzenia.
Pasty lutownicze: alternatywa dla klejenia
Pasty lutownicze, znane również jako pasty lutownicze, stanowią alternatywę dla klejenia w różnych zastosowaniach. Podczas gdy klejenie polega na użyciu klejów do łączenia materiałów, pasty lutownicze wykorzystują inny mechanizm, aby uzyskać solidne i niezawodne połączenie. W tej odpowiedzi omówimy pasty lutownicze jako alternatywę dla klejenia w limicie 450 słów.
Pasty lutownicze składają się z mieszaniny cząstek stopu metalu, topnika i spoiwa. Cząstki stopu metalu zazwyczaj składają się z cyny, ołowiu, srebra lub kombinacji tych metali. Zmiana pomaga w procesie lutowania, usuwając tlenki z powierzchni metalowych i sprzyjając zwilżaniu i przyczepności. Spoiwo utrzymuje pastę razem i umożliwia jej łatwą aplikację.
Jedną z głównych zalet past lutowniczych nad klejeniem jest wytrzymałość i trwałość połączenia. Lutowanie tworzy wiązanie metalurgiczne między łączonymi materiałami, w wyniku czego powstaje mocne połączenie, które może wytrzymać różne naprężenia mechaniczne, termiczne i elektryczne. Połączenie lutowane jest często bardziej wytrzymałe i niezawodne niż połączenia klejowe, które mogą ulec degradacji z czasem lub w określonych warunkach.
Pasty lutownicze zapewniają również szybszy i wydajniejszy proces łączenia. Pastę można dokładnie nałożyć na żądane miejsca, a połączenie można uformować poprzez podgrzanie zespołu do temperatury topnienia lutu. Ten proces jest często szybszy niż klejenie, które może wymagać czasu utwardzania lub schnięcia. Ponadto pasty lutownicze umożliwiają jednoczesne łączenie wielu elementów, skracając czas montażu i zwiększając produktywność.
Kolejną zaletą jest uniwersalność past lutowniczych w łączeniu różnych materiałów. Klejenie może mieć ograniczenia w przypadku łączenia różnych materiałów lub materiałów o różnych współczynnikach rozszerzalności cieplnej. Pasty lutownicze mogą tworzyć niezawodne połączenia między różnymi materiałami, w tym metalami, ceramiką i niektórymi tworzywami sztucznymi, dzięki czemu nadają się do różnych zastosowań.
Ponadto pasty lutownicze mogą poprawić przewodność cieplną i elektryczną w porównaniu z klejeniem. Ta właściwość jest szczególnie korzystna w zastosowaniach, w których kluczowe znaczenie ma rozpraszanie ciepła lub ciągłość elektryczna, takich jak zespoły elektroniczne — złącze lutowane tworzy bezpośrednią ścieżkę metaliczną, ułatwiając efektywne przenoszenie ciepła i przewodzenie elektryczne.
Należy jednak pamiętać, że pasty lutownicze mają również pewne uwagi i ograniczenia. Na przykład niektóre stopy lutownicze zawierają ołów, który może podlegać ograniczeniom ze względu na kwestie środowiskowe i zdrowotne. Bezołowiowe pasty lutownicze zostały opracowane jako alternatywy, ale mogą one mieć inne właściwości i wymagać uwzględnienia określonych procesów.
Techniki dozowania kleju: precyzja i wydajność
Techniki dozowania kleju mają kluczowe znaczenie w różnych gałęziach przemysłu, od produkcji po budownictwo. Osiągnięcie precyzji i wydajności w nakładaniu kleju jest niezbędne do zapewnienia niezawodnych wiązań, minimalizacji odpadów i poprawy ogólnej wydajności. W tym artykule omówimy krytyczne techniki, które pomagają osiągnąć precyzję i wydajność dozowania kleju.
- Zautomatyzowane systemy dozujące: Zautomatyzowane systemy dozujące wykorzystują ramiona robotów lub sprzęt sterowany komputerowo do precyzyjnego nakładania klejów. Systemy te oferują wysoką powtarzalność, dokładność i szybkość, zapewniając spójne nakładanie kleju na wiele części lub produktów. Eliminując błędy ludzkie, zautomatyzowane systemy minimalizują ilość odpadów i zwiększają wydajność procesów dozowania kleju.
- Systemy dozowania i mieszania: Niektóre aplikacje wymagają dozowania dwóch lub więcej składników, które należy zmieszać w określonym stosunku. Systemy dozowania i mieszania precyzyjnie odmierzają i łączą składniki kleju przed jego rozprowadzeniem, zapewniając dokładne proporcje i stałą jakość. Systemy te są szczególnie korzystne w przypadku dwuskładnikowych epoksydów, poliuretanów i innych klejów reaktywnych.
- Dozowanie kontrolowane ciśnieniem: Techniki dozowania kontrolowanego ciśnieniem obejmują stosowanie systemów pneumatycznych lub hydraulicznych do kontrolowania natężenia przepływu i ciśnienia kleju. Klej jest dozowany z kontrolowaną szybkością, utrzymując stałą siłę, zapewniając precyzyjną aplikację i minimalizując nadmiar kleju. Dozowanie sterowane ciśnieniem jest powszechnie stosowane w aplikacjach wymagających cienkich linii, kropek lub skomplikowanych wzorów.
- Dozowanie strumieniowe i igłowe: Techniki dozowania strumieniowego i igłowego są odpowiednie do zastosowań wymagających szybkiego i precyzyjnego nakładania kleju. Systemy natryskiwania wykorzystują impulsy ciśnienia do dozowania drobnych kropelek lub ciągłych linii kleju. Z drugiej strony dozowanie igłowe polega na użyciu igły lub dyszy do nanoszenia kleju w kontrolowanych ilościach. Techniki te są powszechnie stosowane w montażu elektroniki, gdzie wymagane są małe, precyzyjne warstwy kleju.
- Systemy natryskiwania i powlekania: W przypadku klejenia lub powlekania dużych powierzchni systemy natryskiwania i powlekania zapewniają wydajne dozowanie kleju. Systemy te wykorzystują techniki atomizacji w celu wytworzenia drobnej mgiełki lub sprayu kleju, zapewniając równomierne pokrycie i minimalne straty. Systemy natryskiwania i powlekania są szeroko stosowane w przemyśle motoryzacyjnym, lotniczym i meblarskim.
- Zawory i dysze dozujące: Wybór zaworów i dysz dozujących ma kluczowe znaczenie dla osiągnięcia precyzji dozowania kleju. Różne typy zaworów i dysz, takie jak zawory iglicowe, zawory membranowe lub dysze stożkowe, zapewniają zróżnicowaną kontrolę nad natężeniem przepływu, wzorem i rozmiarem kropli. Wybór odpowiedniego zaworu lub dyszy do konkretnego kleju i wymagań aplikacji jest niezbędny do uzyskania precyzyjnego i wydajnego dozowania.
- Systemy sterowane wizyjnie: Systemy dozujące sterowane wizyjnie wykorzystują kamery i zaawansowane oprogramowanie do wykrywania i śledzenia pozycji części lub substratów. Analizując przechwycone obrazy, system dostosowuje parametry dozowania kleju w czasie rzeczywistym, zapewniając dokładne umieszczenie nawet na nierównych powierzchniach lub elementach o różnych wymiarach. Systemy sterowane wizyjnie zwiększają precyzję i wydajność, jednocześnie dostosowując się do zmian procesu.
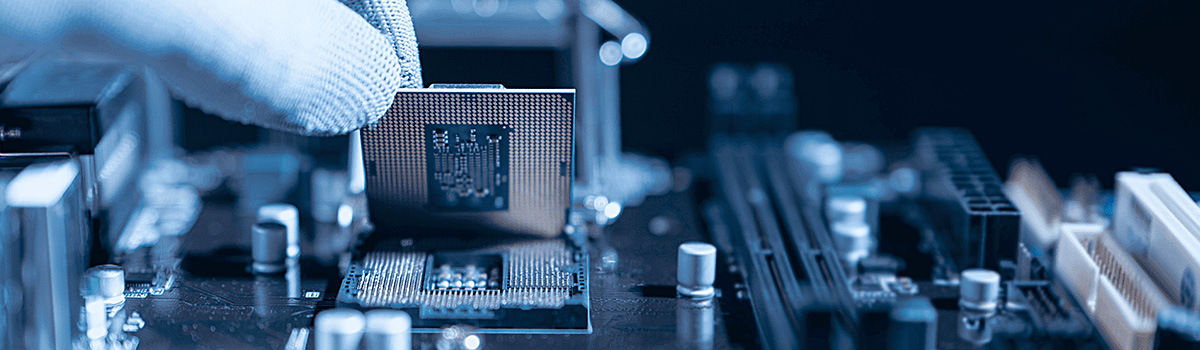
Wyzwania w aplikacji kleju do półprzewodników
Nakładanie kleju do półprzewodników wiąże się z kilkoma wyzwaniami, które mogą mieć wpływ na wydajność i niezawodność urządzeń elektronicznych. Wyzwania te wynikają z wyjątkowych wymagań i właściwości półprzewodników oraz wymagających warunków pracy, którym są poddawane. Oto niektóre z najważniejszych wyzwań związanych z aplikacją kleju półprzewodnikowego:
- Zarządzanie ciepłem: Półprzewodniki wytwarzają ciepło podczas pracy, a skuteczne zarządzanie ciepłem ma kluczowe znaczenie dla zapobiegania przegrzaniu. Materiały klejące stosowane w półprzewodnikach muszą mieć doskonałe przewodnictwo cieplne, aby skutecznie przenosić ciepło z urządzenia. Zapewnienie odpowiedniej przyczepności bez uszczerbku dla parametrów termicznych jest dużym wyzwaniem.
- Kompatybilność chemiczna: półprzewodniki są narażone na działanie różnych chemikaliów podczas ich żywotności, w tym środków czyszczących, rozpuszczalników i topników. Materiały klejące powinny być chemicznie kompatybilne z tymi substancjami, aby uniknąć degradacji lub utraty przyczepności w miarę upływu czasu. Wybór materiałów klejących odpornych na działanie określonych chemikaliów to złożone zadanie.
- Naprężenia mechaniczne: Urządzenia elektroniczne często podlegają naprężeniom mechanicznym z powodu rozszerzalności cieplnej, wibracji i sił zewnętrznych. Aby wytrzymać te naprężenia, materiały klejące muszą mieć odpowiednie właściwości mechaniczne, takie jak elastyczność i wytrzymałość. Słaba przyczepność może prowadzić do rozwarstwienia, pękania lub uszkodzenia mechanicznego elementu półprzewodnikowego.
- Miniaturyzacja: Wraz z trwającym trendem miniaturyzacji urządzenia półprzewodnikowe stają się coraz mniejsze i bardziej złożone. Aplikacja kleju w tak miniaturowych strukturach wymaga dużej precyzji i kontroli. Zapewnienie równomiernego pokrycia, unikanie pustych przestrzeni i utrzymanie stałej grubości spoiny staje się krytycznym wyzwaniem.
- Zgodność procesu: Produkcja półprzewodników obejmuje wiele etapów przetwarzania, w tym czyszczenie, osadzanie i pakowanie. Materiały klejące powinny być kompatybilne z tymi procesami bez negatywnego wpływu na ich działanie. Wyzwania pojawiają się przy znalezieniu klejów, które wytrzymują procesy w wysokich temperaturach, są odporne na wilgoć i zachowują stabilność w całym cyklu produkcyjnym.
- Niezawodność i starzenie się: Oczekuje się, że urządzenia półprzewodnikowe będą miały długą żywotność i niezawodne działanie w różnych warunkach pracy. Materiały klejące muszą wykazywać długotrwałą stabilność, odporność na starzenie i niezawodną przyczepność przez dłuższy czas. Wyzwanie polega na przewidywaniu i łagodzeniu potencjalnych mechanizmów degradacji, które mogą mieć wpływ na wydajność i niezawodność urządzenia półprzewodnikowego.
- Względy środowiskowe: Materiały klejące stosowane w zastosowaniach półprzewodnikowych muszą być zgodne z przepisami i normami dotyczącymi ochrony środowiska.
- Obejmuje to ograniczenie substancji niebezpiecznych, takich jak ołów i inne toksyczne materiały. Opracowanie przyjaznych dla środowiska rozwiązań w zakresie klejów, które spełniają wymogi prawne bez uszczerbku dla wydajności, może być trudne.
- Koszt i skalowalność: Materiały klejące powinny być opłacalne i skalowalne, aby sprostać wymaganiom produkcji półprzewodników na dużą skalę. Zrównoważenie kwestii związanych z kosztami z wymaganiami dotyczącymi wydajności stanowi wyzwanie przy wyborze odpowiednich materiałów klejących i optymalizacji procesu aplikacji.
Testy niezawodności: ocena działania kleju
Testy niezawodności są niezbędnym procesem oceny wydajności klejów. Kleje są powszechnie stosowane w różnych gałęziach przemysłu, w tym motoryzacyjnym, lotniczym, elektronicznym i budowlanym, gdzie odgrywają kluczową rolę w łączeniu różnych materiałów. Niezawodność klejów ma kluczowe znaczenie dla zapewnienia trwałości i długotrwałej funkcjonalności klejonych elementów.
Jednym z kluczowych aspektów testowania niezawodności jest ocena wytrzymałości i przyczepności kleju. Obejmuje to poddanie próbek kleju różnym warunkom naprężeń w celu symulacji rzeczywistych scenariuszy i określenia ich działania przy różnych obciążeniach, temperaturach i warunkach środowiskowych. Próby rozciągania, ścinania i odrywania są powszechnie przeprowadzane w celu oceny właściwości mechanicznych kleju i zdolności do wytrzymywania sił działających w różnych kierunkach.
Oprócz testów mechanicznych, czynniki środowiskowe odgrywają znaczącą rolę w działaniu kleju. Kleje mogą być narażone na ekstremalne temperatury, wilgoć, substancje chemiczne i promieniowanie UV w okresie użytkowania. Dlatego testowanie niezawodności polega na poddawaniu lepkich próbek testom przyspieszonego starzenia, w których są one wystawione na działanie trudnych warunków środowiskowych przez dłuższy czas. Pomaga to przewidzieć długoterminowe działanie kleju i ocenić jego odporność na degradację, taką jak utrata przyczepności lub niszczenie chemiczne.
Kolejnym ważnym aspektem testów niezawodności jest ocena trwałości kleju pod cyklicznymi obciążeniami. W wielu zastosowaniach kleje są poddawane powtarzającym się naprężeniom mechanicznym, takim jak wibracje lub cykle termiczne. Testy zmęczeniowe oceniają odporność kleju na zniszczenie pod tymi cyklicznymi obciążeniami. Próbki są zwykle poddawane określonej liczbie cykli obciążenia, a ich działanie jest monitorowane pod kątem wszelkich oznak wad kleju, takich jak propagacja pęknięć lub rozwarstwienie wiązania.
Ponadto testy niezawodności obejmują ocenę działania kleju w rzeczywistych warunkach. Może to obejmować testowanie zdolności kleju do łączenia różnych materiałów powszechnie stosowanych w przemyśle, takich jak metale, tworzywa sztuczne, kompozyty lub szkło. Próbki są przygotowywane przy użyciu standardowych procedur i poddawane protokołom testowym, które symulują specyficzne wymagania aplikacji. Pozwala to inżynierom ocenić kompatybilność kleju z różnymi podłożami i ocenić jego siłę wiązania, elastyczność i odporność na czynniki środowiskowe.
Badanie niezawodności obejmuje również ocenę kompatybilności chemicznej kleju z innymi substancjami, z którymi może się on stykać w trakcie jego stosowania lub użytkowania. Polega to na przeprowadzeniu testów kompatybilności w celu ustalenia, czy klej nie reaguje niekorzystnie z rozpuszczalnikami, środkami czyszczącymi, paliwami lub innymi chemikaliami, które mogą znajdować się w środowisku. Testy zgodności chemicznej pomagają zidentyfikować potencjalne problemy, które mogą prowadzić do uszkodzenia lub degradacji kleju.
Podsumowując, testowanie niezawodności jest kluczowym krokiem w ocenie wydajności kleju. Obejmuje ocenę właściwości mechanicznych, przeprowadzanie testów przyspieszonego starzenia, ocenę trwałości pod obciążeniem cyklicznym, ocenę wydajności w rzeczywistych warunkach oraz testowanie kompatybilności chemicznej. Przeprowadzając kompleksowe testy niezawodności, producenci i inżynierowie mogą zapewnić przydatność klejów i długoterminową wydajność w zamierzonych zastosowaniach.
Względy środowiskowe w kleju półprzewodnikowym
Kleje do półprzewodników odgrywają kluczową rolę w montażu i pakowaniu urządzeń elektronicznych, szczególnie w przemyśle półprzewodnikowym. Chociaż te kleje zapewniają podstawowe funkcje, takie jak wiązanie i odprowadzanie ciepła, ważne jest, aby wziąć pod uwagę ich wpływ na środowisko przez cały cykl ich życia. Oto kilka kluczowych kwestii środowiskowych związanych z klejem do półprzewodników:
- Toksyczność: Wiele klejów półprzewodnikowych zawiera niebezpieczne substancje, w tym lotne związki organiczne (LZO), metale ciężkie i inne toksyczne chemikalia. Substancje te mogą mieć niekorzystny wpływ na zdrowie ludzi i środowisko. Minimalizowanie lub eliminowanie szkodliwych składników w recepturach klejów ma kluczowe znaczenie dla zmniejszenia ich wpływu na środowisko.
- Emisje: Podczas produkcji i stosowania klejów półprzewodnikowych lotne składniki mogą być uwalniane do powietrza, przyczyniając się do zanieczyszczenia powietrza. Na przykład emisje lotnych związków organicznych mogą przyczyniać się do powstawania ozonu w warstwie przyziemnej i powstawania szkodliwych cząstek stałych. Producenci powinni dążyć do opracowania receptur klejów o niskiej zawartości lotnych związków organicznych i wdrożyć rygorystyczne środki kontroli emisji, aby złagodzić ten wpływ na środowisko.
- Zużycie energii: Produkcja klejów półprzewodnikowych wymaga energochłonnych procesów, w tym syntezy, mieszania i utwardzania. Zmniejszenie zużycia energii poprzez optymalizację procesów i zastosowanie energooszczędnych technologii może zminimalizować wpływ na środowisko związany z produkcją klejów.
- Wytwarzanie odpadów: Przemysł półprzewodników generuje znaczne ilości odpadów, a kleje przyczyniają się do tego strumienia odpadów. Odpady mogą obejmować niewykorzystane lub przeterminowane kleje, materiały opakowaniowe i produkty uboczne produkcji. Wdrażanie praktyk gospodarowania odpadami, takich jak recykling, ponowne użycie lub bezpieczna utylizacja odpadów klejowych, jest niezbędne, aby zminimalizować zanieczyszczenie środowiska i wyczerpywanie zasobów.
- Analiza cyklu życia: Uwzględnienie całego cyklu życia klejów półprzewodnikowych ma kluczowe znaczenie dla kompleksowej oceny ich wpływu na środowisko. Analiza ta obejmuje ocenę śladu ekologicznego wydobycia surowców, produkcji, transportu, zastosowania i utylizacji po zakończeniu eksploatacji. Identyfikacja możliwości ulepszeń na każdym etapie może prowadzić do bardziej zrównoważonych rozwiązań w zakresie klejów.
- Zrównoważone alternatywy: badanie i przyjmowanie zrównoważonych alternatyw ma zasadnicze znaczenie dla zmniejszenia wpływu klejów półprzewodnikowych na środowisko. Może to obejmować wykorzystanie surowców pochodzenia biologicznego lub odnawialnych, opracowywanie preparatów na bazie wody lub niezawierających rozpuszczalników oraz stosowanie procesów produkcyjnych przyjaznych dla środowiska. Promowanie recyklingu klejów lub wdrażanie praktyk gospodarki o obiegu zamkniętym może również przyczynić się do ochrony zasobów.
- Zgodność z przepisami: Producenci klejów muszą przestrzegać przepisów i norm dotyczących ochrony środowiska, dotyczących stosowania chemikaliów, utylizacji i etykietowania. Aby zapewnić ochronę środowiska i zdrowia ludzi, kluczowe znaczenie ma bycie na bieżąco z odpowiednimi przepisami, takimi jak REACH (Registration, Evaluation, Authorization, and Restriction of Chemicals) w Unii Europejskiej i podobne przepisy w różnych regionach.
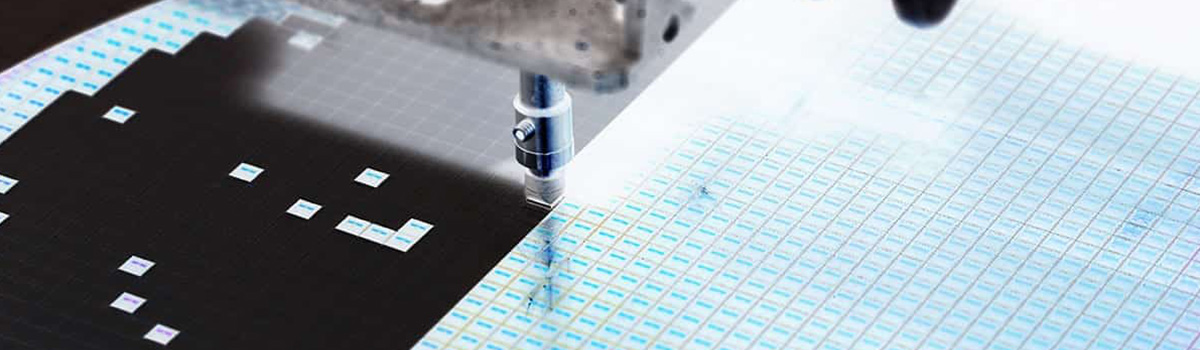
Trendy i innowacje w kleju półprzewodnikowym
Klej półprzewodnikowy odgrywa kluczową rolę w montażu i pakowaniu urządzeń elektronicznych, zapewniając prawidłowe łączenie i stabilność elementów półprzewodnikowych. Wraz z rozwojem technologii pojawia się kilka kluczowych trendów i innowacji w dziedzinie klejów do półprzewodników.
- Miniaturyzacja i większa złożoność urządzeń: Jednym ze znaczących trendów w branży półprzewodników jest postępująca miniaturyzacja urządzeń elektronicznych i rosnąca złożoność ich projektów. Tendencja ta wymaga klejów o ulepszonych właściwościach, takich jak niższa lepkość, większa siła wiązania i zwiększona przewodność cieplna, aby pomieścić mniejsze i gęściej upakowane elementy.
- Zaawansowane techniki pakowania: Zaawansowane techniki pakowania, takie jak system w opakowaniu (SiP), pakowanie na poziomie płytki rozłożonej (FOWLP) i pakowanie 3D, zyskują na popularności ze względu na ich zdolność do poprawy wydajności urządzenia i zmniejszenia rozmiaru. Techniki te często wymagają specjalistycznych klejów, które poradzą sobie z wyjątkowymi wyzwaniami związanymi z łączeniem wielu matryc i komponentów na niewielkiej powierzchni.
- Zarządzanie ciepłem: W miarę jak urządzenia elektroniczne stają się coraz mocniejsze i bardziej kompaktowe, efektywne zarządzanie ciepłem staje się coraz ważniejsze. Kleje półprzewodnikowe o doskonałych właściwościach przewodzenia ciepła są opracowywane w celu ułatwienia odprowadzania ciepła z urządzeń półprzewodnikowych, zapobiegając przegrzaniu i zapewniając optymalną wydajność.
- Utwardzanie w niskiej temperaturze: Tradycyjne kleje półprzewodnikowe często wymagają procesów utwardzania w wysokiej temperaturze, co może być problematyczne w przypadku elementów lub podłoży wrażliwych na temperaturę. Innowacje w zakresie klejów utwardzanych w niskich temperaturach umożliwiają łączenie w znacznie niższych temperaturach, zmniejszając ryzyko termicznego uszkodzenia delikatnych materiałów półprzewodnikowych.
- Nowe formuły materiałów: Naukowcy badają nowe formuły materiałów do klejów półprzewodnikowych, aby sprostać zmieniającym się wymaganiom. Obejmuje to opracowanie klejów przewodzących prąd elektryczny (ECA), które zapewniają wiązanie i przewodnictwo elektryczne, eliminując potrzebę lutowania w określonych zastosowaniach. Ponadto wprowadzane są nowe materiały, takie jak elastyczne kleje, aby sprostać rosnącemu zapotrzebowaniu na elastyczne i podatne na zginanie urządzenia elektroniczne.
- Względy środowiskowe: Zrównoważony rozwój i wpływ na środowisko zyskują coraz większą uwagę w branży półprzewodników. Producenci klejów koncentrują się na opracowywaniu ekologicznych receptur o zmniejszonej zawartości lotnych związków organicznych (LZO) i substancji niebezpiecznych przy jednoczesnym zachowaniu doskonałych właściwości użytkowych.
- Optymalizacja i automatyzacja procesów: wraz z rosnącym zapotrzebowaniem na urządzenia półprzewodnikowe rośnie zapotrzebowanie na wydajne i zautomatyzowane procesy produkcyjne. Producenci klejów współpracują z dostawcami sprzętu w celu optymalizacji procesów dozowania i utwardzania kleju, zapewniając spójne i niezawodne wyniki przy jednoczesnym skróceniu czasu cyklu produkcyjnego.
- Niezawodność i trwałość: Oczekuje się, że urządzenia półprzewodnikowe będą działać niezawodnie przez długi czas, często w trudnych warunkach. Innowacje w zakresie klejów mają na celu poprawę niezawodności urządzeń poprzez zwiększenie siły przyczepności, odporności na wilgoć, temperaturę i różne czynniki środowiskowe.
Obszary zastosowań: elektronika użytkowa, motoryzacja, lotnictwo i inne
Elektroniki użytkowej:
Elektronika użytkowa jest jednym z najważniejszych obszarów zastosowań postępu technologicznego. Obejmuje wiele urządzeń, takich jak smartfony, tablety, laptopy, inteligentne telewizory, urządzenia do noszenia i sprzęt AGD. W ostatnich latach nastąpił znaczny wzrost wydajności, funkcjonalności i łączności w elektronice użytkowej. Na przykład smartfony stały się potężniejsze, oferując zaawansowane funkcje, takie jak kamery o wysokiej rozdzielczości, integracja sztucznej inteligencji i możliwości rzeczywistości rozszerzonej. Inteligentne telewizory obsługują teraz rozdzielczość 4K, a nawet 8K oraz integrację z inteligentnym domem, zapewniając lepszą rozrywkę. Urządzenia do noszenia, takie jak smartwatche i monitory fitness, zyskały popularność dzięki możliwościom monitorowania stanu zdrowia i śledzenia kondycji.
Automobilowy:
Przemysł motoryzacyjny doświadczył niezwykłych postępów, głównie dzięki technologii. Nowoczesne pojazdy mają wyrafinowaną elektronikę i systemy oprogramowania, które zwiększają bezpieczeństwo, wydajność i wygodę użytkownika. Jednym z krytycznych obszarów rozwoju jest jazda autonomiczna, a samojezdne samochody stają się rzeczywistością. Pojazdy te polegają na zaawansowanych czujnikach, algorytmach sztucznej inteligencji i łączności, aby poruszać się po drogach i podejmować inteligentne decyzje. Ponadto aplikacje motoryzacyjne obejmują:
- Systemy informacyjno-rozrywkowe.
- Zaawansowane systemy wspomagania kierowcy (ADAS).
- Łączność w samochodzie.
- Technologia pojazdów elektrycznych.
- Komunikacja pojazd-pojazd.
Lotnictwo:
Przemysł lotniczy w dużym stopniu polega na zaawansowanych technologiach w celu poprawy bezpieczeństwa, wydajności i wydajności. Zastosowania lotnicze obejmują projektowanie i produkcję samolotów, eksplorację kosmosu, systemy satelitarne i zarządzanie ruchem lotniczym. Projektowanie wspomagane komputerowo (CAD) i narzędzia symulacyjne pomagają inżynierom tworzyć bardziej aerodynamiczne i paliwooszczędne samoloty w projektowaniu samolotów. Systemy satelitarne zapewniają globalną komunikację, monitorowanie pogody i usługi nawigacyjne. Przemysł lotniczy wykorzystuje również zaawansowane materiały, takie jak kompozyty i lekkie stopy, w celu zmniejszenia masy i zwiększenia oszczędności paliwa. W eksploracji kosmosu robotyka, teledetekcja i systemy napędowe umożliwiają misjom badanie ciał niebieskich i gromadzenie danych naukowych.
Opieka zdrowotna:
Technologia odgrywa kluczową rolę w opiece zdrowotnej, zmieniając branżę na różne sposoby. Urządzenia i sprzęt medyczny, takie jak aparaty do rezonansu magnetycznego, ultrasonografy i zrobotyzowane systemy chirurgiczne, zrewolucjonizowały procedury diagnostyczne i lecznicze. Elektroniczna dokumentacja medyczna (EHR) i telemedycyna umożliwiają pracownikom służby zdrowia dostęp do informacji o pacjencie i świadczenie opieki zdalnej. Urządzenia do noszenia i systemy monitorowania stanu zdrowia umożliwiają jednostkom śledzenie parametrów życiowych i otrzymywanie spersonalizowanych zaleceń dotyczących opieki zdrowotnej. Algorytmy sztucznej inteligencji i uczenia maszynowego są wykorzystywane do diagnozowania chorób, odkrywania leków i analiz predykcyjnych, co prowadzi do poprawy wyników leczenia pacjentów i dostosowanej medycyny.
Automatyka przemysłowa:
Automatyka przemysłowa polega na wykorzystaniu zaawansowanych technologii do automatyzacji procesów produkcyjnych i poprawy produktywności. Robotyka i ramiona robotyczne są szeroko stosowane do zadań takich jak montaż, spawanie i przenoszenie materiałów. Urządzenia i czujniki Internetu rzeczy (IoT) są wdrażane w celu gromadzenia danych w czasie rzeczywistym i optymalizowania wydajności operacyjnej. Systemy widzenia maszynowego umożliwiają kontrolę i inspekcję jakości, gwarantując, że produkty spełniają surowe normy. Zaawansowane systemy sterowania i algorytmy konserwacji zapobiegawczej pomagają zminimalizować przestoje i zmaksymalizować wydajność produkcji. Automatyka przemysłowa może zwiększyć wydajność, obniżyć koszty i zwiększyć bezpieczeństwo w różnych branżach, w tym w produkcji, logistyce i energetyce.
Perspektywy i możliwości na przyszłość
Przyszłość jest pełna ekscytujących perspektyw i możliwości, napędzanych przez szybki postęp technologiczny, zmieniające się potrzeby społeczne i zmieniające się światowe trendy. Tutaj badamy kilka kluczowych obszarów o znacznym potencjale wzrostu i rozwoju.
- Sztuczna inteligencja (AI) i automatyzacja: Sztuczna inteligencja zmienia branże we wszystkich dziedzinach, zwiększając wydajność, produktywność i podejmowanie decyzji. W miarę dojrzewania technologii AI będą pojawiać się coraz większe możliwości dla specjalistów AI, analityków danych i inżynierów. Automatyzacja będzie nadal usprawniać procesy, prowadząc do tworzenia miejsc pracy w robotyce, uczeniu maszynowym i inteligentnych systemach.
- Energia odnawialna i zrównoważony rozwój: wraz z rosnącym niepokojem związanym ze zmianami klimatycznymi istnieje ogromne zapotrzebowanie na rozwiązania w zakresie energii odnawialnej. Przejście na czystsze źródła, takie jak energia słoneczna, wiatrowa i wodna, stwarza liczne perspektywy. Kariera w inżynierii energii odnawialnej, zarządzaniu energią i zrównoważonym rozwoju będzie miała kluczowe znaczenie w kształtowaniu bardziej ekologicznej przyszłości.
- Opieka zdrowotna i biotechnologia: postępy w badaniach medycznych, medycynie spersonalizowanej i edycji genów rewolucjonizują branżę opieki zdrowotnej. Możliwości obfitują w bioinformatykę, poradnictwo genetyczne, telemedycynę i rozwój farmaceutyczny. Skrzyżowanie technologii i opieki zdrowotnej będzie napędzać innowacje, prowadząc do lepszej opieki nad pacjentem i lepszych wyników.
- Cyberbezpieczeństwo i prywatność danych: Ponieważ nasza zależność od systemów cyfrowych stale rośnie, rośnie również zapotrzebowanie na solidne środki bezpieczeństwa cybernetycznego. Zagrożenia cybernetyczne stają się coraz bardziej wyrafinowane, co powoduje zapotrzebowanie na ekspertów ds. cyberbezpieczeństwa, etycznych hakerów i specjalistów ds. ochrony danych. Ochrona poufnych informacji i rozwijanie bezpiecznej infrastruktury będzie miało kluczowe znaczenie dla organizacji i osób prywatnych.
- Handel elektroniczny i marketing cyfrowy: Handel elektroniczny zmienił sposób, w jaki robimy zakupy, tworząc nowe możliwości dla firm. Internetowe platformy sprzedaży detalicznej, marketing cyfrowy i reklama w mediach społecznościowych stały się niezbędne dla dobrze prosperujących firm. Kariery w zarządzaniu e-commerce, tworzeniu treści cyfrowych i optymalizacji obsługi klienta będą nadal bardzo poszukiwane.
- Eksploracja kosmosu i komercjalizacja: Eksploracja kosmosu przeszła od inicjatyw rządowych do przedsięwzięć komercyjnych, otwierając możliwości w inżynierii lotniczej, technologii satelitarnej i turystyce kosmicznej. Prywatne firmy inwestują w podróże kosmiczne, wydobywanie zasobów i komunikację satelitarną, torując drogę do nowej ery eksploracji kosmosu.
- Zrównoważone rolnictwo i systemy żywnościowe: Ponieważ liczba ludności na świecie ma osiągnąć 9 miliardów do 2050 r., zapewnienie bezpieczeństwa żywności i zrównoważonych praktyk rolniczych ma kluczowe znaczenie. Rolnictwo wertykalne, rolnictwo precyzyjne i alternatywne źródła białka oferują potencjał dla innowacji. Kariera w technologii rolniczej, agronomii i naukach o żywności odegra istotną rolę w zaspokajaniu przyszłych potrzeb żywnościowych.
- Rzeczywistość wirtualna (VR), rzeczywistość rozszerzona (AR) i rzeczywistość rozszerzona (XR): Technologie te mogą zrewolucjonizować rozrywkę, edukację, szkolenia i różne branże. Deweloperzy VR/AR, twórcy treści i projektanci wciągających doświadczeń będą kształtować przyszłość rozrywki, gier i wirtualnej współpracy.
- Technologia finansowa (Fintech): Integracja technologii i finansów doprowadziła do powstania Fintech, oferującego nowe usługi finansowe, cyfrowe rozwiązania płatnicze i technologię blockchain. Oczekuje się, że kariery w analityce finansowej, bezpieczeństwie cybernetycznym w bankowości i rozwoju technologii blockchain będą bardzo poszukiwane.
- Doradztwo w zakresie zrównoważonego rozwoju i zielona architektura: w miarę jak zrównoważony rozwój staje się priorytetem, firmy i osoby prywatne szukają wskazówek, jak zmniejszyć swój ślad węglowy i przyjąć praktyki przyjazne dla środowiska. Zrównoważeni konsultanci, architekci ekologii i inżynierowie środowiska odegrają kluczową rolę w projektowaniu i wdrażaniu zrównoważonych rozwiązań.
Znaczenie współpracy w rozwijaniu technologii klejenia półprzewodników
Współpraca ma kluczowe znaczenie dla rozwoju technologii klejów półprzewodnikowych, napędzania innowacji i zapewnienia jej pomyślnego wdrożenia w różnych branżach. Branża półprzewodników jest bardzo złożona i szybko się rozwija, co wymaga interdyscyplinarnej wiedzy specjalistycznej i współpracy zainteresowanych stron.
- Zróżnicowana wiedza specjalistyczna: Technologia klejów półprzewodnikowych obejmuje wiele dyscyplin, w tym materiałoznawstwo, chemię, inżynierię i produkcję. Współpraca łączy ekspertów z różnych dziedzin, z których każdy wnosi specjalistyczną wiedzę i umiejętności. Dzięki połączeniu różnorodnej wiedzy specjalistycznej partnerstwo umożliwia rozwój nowatorskich materiałów i technik adhezyjnych, które mogą poprawić wydajność, niezawodność i trwałość urządzeń półprzewodnikowych.
- Wymiana wiedzy: współpraca ułatwia wymianę wiedzy i informacji między naukowcami, inżynierami i specjalistami z branży. Dzięki wspólnym wysiłkom poszczególne osoby mogą dzielić się swoimi spostrzeżeniami, doświadczeniami i wynikami badań, co prowadzi do głębszego zrozumienia materiałów klejących i ich zastosowań. Ta wymiana wiedzy może pomóc zidentyfikować pojawiające się trendy, sprostać wyzwaniom technicznym i przyspieszyć rozwój innowacyjnych rozwiązań.
- Ulepszone badania i rozwój: wspólne wysiłki badawczo-rozwojowe umożliwiają łączenie zasobów w zakresie finansowania i sprzętu. Pozwala to na bardziej rozbudowane eksperymenty, testy i analizy, co prowadzi do szybszego odkrywania i wprowadzania innowacji. Pracując razem, naukowcy mogą uzyskać dostęp do wyspecjalizowanych urządzeń, najnowocześniejszych technologii i zaawansowanych narzędzi do charakteryzacji, które mogą nie być dostępne indywidualnie. Takie zasoby mogą znacząco przyczynić się do rozwoju technologii klejów półprzewodnikowych.
- Współpraca przemysł-uniwersytet: Współpraca między przemysłem a środowiskiem akademickim ma kluczowe znaczenie dla przełożenia wyników badań na praktyczne zastosowania. Uniwersytety mogą prowadzić podstawowe badania i badać nowe koncepcje, podczas gdy partnerzy branżowi wnoszą rzeczywistą perspektywę i praktyczne rozważania. Ta współpraca gwarantuje, że rozwój technologii klejów jest zgodny z potrzebami rynku i może być zintegrowany z procesami przemysłowymi. Stowarzyszenie przemysł-uniwersytet promuje również transfer technologii, umożliwiając naukowcom wywieranie namacalnego wpływu na zastosowania komercyjne.
- Standaryzacja i zapewnienie jakości: Współpraca między graczami z branży sprzyja opracowywaniu standardów i wytycznych dotyczących technologii klejenia półprzewodników. Normy pomagają zapewnić spójność, kompatybilność i niezawodność różnych produktów i procesów produkcyjnych. Wspólne wysiłki mogą ustanowić najlepsze praktyki, metodologie testowania i procedury kontroli jakości, które są niezbędne do zagwarantowania wydajności i długoterminowej niezawodności urządzeń półprzewodnikowych.
- Ekspansja rynku i konkurencyjność: Współpraca między firmami działającymi w branży półprzewodników może prowadzić do ekspansji rynkowej i wzrostu konkurencyjności. Firmy mogą łączyć swoje zasoby, wiedzę i wiedzę rynkową, współpracując w celu opracowania rozwiązań w zakresie klejów, które spełniają określone wymagania branżowe. Wysiłki oparte na współpracy mogą również ułatwić przyjęcie technologii adhezyjnej w nowych zastosowaniach i na rynkach wschodzących, dodatkowo stymulując rozwój przemysłu półprzewodnikowego.
Wnioski:
Klej półprzewodnikowy odgrywa kluczową rolę w umożliwianiu miniaturyzacji i zwiększaniu wydajności urządzeń półprzewodnikowych. Zdolność tych klejów do zapewniania silnych właściwości wiążących, ochrony przed czynnikami środowiskowymi i naprężeniami termicznymi oraz przewodności elektrycznej ma kluczowe znaczenie w produkcji i montażu mikroprocesorów, układów pamięci i innych układów scalonych. Wraz z postępem technologii rozwój innowacyjnych rozwiązań w zakresie klejów oraz współpraca między producentami, badaczami i użytkownikami końcowymi będą miały kluczowe znaczenie dla sprostania rosnącym wymaganiom i wyzwaniom przemysłu półprzewodnikowego. Wykorzystując potencjał kleju półprzewodnikowego, możemy utorować drogę jeszcze mniejszym, szybszym i bardziej złożonym urządzeniom półprzewodnikowym, które napędzają nasz współczesny świat.