Klej wiążący FPC
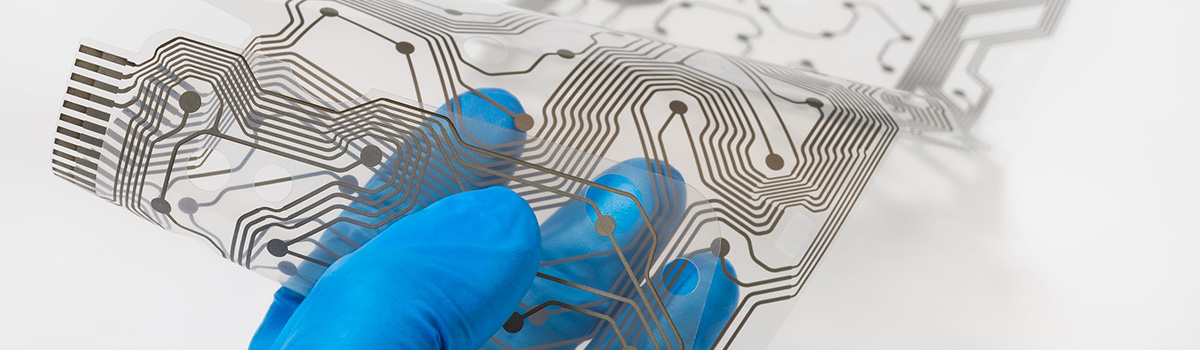
Klej wiążący FPC jest kluczowym elementem w produkcji i montażu elastycznych płytek obwodów drukowanych (FPC), które są szeroko stosowane w różnych urządzeniach elektronicznych, w tym w smartfonach, urządzeniach do noszenia i zastosowaniach motoryzacyjnych. Kleje te zapewniają silne właściwości wiążące, izolację elektryczną i ochronę przed czynnikami środowiskowymi, zapewniając jednocześnie elastyczność i trwałość płyt FPC. Wraz ze wzrostem zapotrzebowania na elastyczne i niezawodne urządzenia elektroniczne, znaczenie wydajnych i niezawodnych klejów FPC stało się coraz ważniejsze. W tym artykule zbadamy różne rodzaje, zastosowania i wyzwania związane z klejami FPC, podkreślając ich kluczową rolę w zapewnianiu elastyczności i niezawodności urządzeń elektronicznych.
Rodzaje kleju wiążącego FPC
Kleje FPC (Flexible Printed Circuit) są niezbędne do montażu i łączenia elastycznych obwodów w różnych urządzeniach elektronicznych. Kleje te zapewniają niezawodne i trwałe połączenie elastycznego obwodu z docelowym podłożem. Na rynku dostępnych jest kilka rodzajów klejów FPC, z których każdy ma unikalne właściwości i zastosowania. Ta odpowiedź zawiera przegląd niektórych popularnych rodzajów klejów łączących FPC.
- Kleje na bazie akrylu: Kleje na bazie akrylu są popularne ze względu na ich doskonałą przyczepność do różnych podłoży, w tym metali, tworzyw sztucznych i szkła. Oferują elastyczność, stabilność termiczną oraz odporność na wilgoć i chemikalia. Kleje akrylowe są dostępne w różnych formach, takich jak taśmy, folie i płynne kleje, co czyni je uniwersalnymi do różnych zastosowań związanych z łączeniem FPC.
- Kleje na bazie epoksydów: Kleje na bazie epoksydów zapewniają wysoką siłę wiązania i są szeroko stosowane do klejenia FPC. Zapewniają doskonałą przyczepność do różnych podłoży i zapewniają dobre właściwości elektroizolacyjne. Kleje epoksydowe są dostępne w różnych formułach, w tym w systemach jednoskładnikowych i dwuskładnikowych, zapewniając opcje dla wielu procesów łączenia i warunków utwardzania.
- Kleje na bazie silikonu: Kleje na bazie silikonu są znane ze swojej elastyczności, odporności na wysokie temperatury i doskonałych właściwości izolacji elektrycznej. Mogą wytrzymać ekstremalne temperatury i zapewniają dobrą odporność na wilgoć, dzięki czemu nadają się do wymagających środowisk. Kleje silikonowe są powszechnie stosowane w aplikacjach wymagających krytycznego zarządzania temperaturą i niezawodności.
- Kleje wrażliwe na nacisk (PSA): PSA to materiały adhezyjne, które tworzą natychmiastowe wiązanie po przyłożeniu nacisku. Eliminują potrzebę innych procesów utwardzania, dzięki czemu są wygodne w zastosowaniach związanych z łączeniem FPC. PSA zapewniają dobrą przyczepność do różnych podłoży i można je łatwo usunąć bez pozostawiania śladów, co czyni je idealnymi do tymczasowego łączenia lub poprawek.
- Kleje utwardzane promieniami UV: Kleje utwardzane promieniowaniem UV to kleje w płynie, które szybko utwardzają się pod wpływem światła ultrafioletowego. Oferują szybki czas utwardzania, wysoką siłę wiązania i doskonałą przyczepność do różnych podłoży. Kleje utwardzane promieniami UV są powszechnie stosowane w aplikacjach łączenia FPC, gdzie wymagany jest szybki montaż i zwiększona produktywność.
- Kleje przewodzące: Kleje przewodzące są specjalnie opracowane do klejenia i przewodnictwa elektrycznego. Zawierają przewodzące wypełniacze, takie jak srebro lub węgiel, które umożliwiają klejowi ustanowienie połączeń elektrycznych między elementami obwodu. Kleje przewodzące są szeroko stosowane w łączeniu FPC do zastosowań takich jak ekranowanie EMI, uziemianie i połączenia elektryczne.
- Kleje przewodzące ciepło: Kleje przewodzące ciepło zostały zaprojektowane tak, aby zapewniały zarówno właściwości wiążące, jak i wydajne przenoszenie ciepła. Są one używane w aplikacjach łączenia FPC, w których zarządzanie termiczne ma kluczowe znaczenie, takich jak łączenie elastycznych obwodów z radiatorami lub innymi podłożami przewodzącymi ciepło.
Należy zauważyć, że wybór kleju wiążącego FPC zależy od różnych czynników, w tym konkretnych wymagań aplikacji, materiałów podłoża, warunków środowiskowych i procesów produkcyjnych. Konsultacje z producentami lub dostawcami klejów mogą dostarczyć bardziej szczegółowych informacji i wskazówek dotyczących wyboru najbardziej odpowiedniego kleju do konkretnego zastosowania łączenia FPC.
Kleje akrylowe: najczęstszy wybór
Kleje akrylowe są popularne w różnych gałęziach przemysłu ze względu na ich wszechstronność, silne właściwości wiążące i łatwość użycia. Kleje te składają się z polimerów akrylowych, które zapewniają doskonałą przyczepność do szerokiej gamy podłoży. Tutaj zbadamy, dlaczego kleje akrylowe są najczęstszym wyborem w 450 słowach.
Jedną z najważniejszych zalet klejów akrylowych jest ich zdolność do łączenia ze sobą różnych materiałów. Kleje akrylowe mogą tworzyć trwałe i niezawodne wiązania, niezależnie od tego, czy klejone są tworzywa sztuczne, metale, ceramika, drewno, a nawet szkło. Ta wszechstronność sprawia, że nadają się do różnych zastosowań motoryzacyjnych, budowlanych, elektronicznych i oznakowań.
Kleje akrylowe zapewniają również doskonałą siłę wiązania i mogą tworzyć mocne wiązania, które wytrzymują duże obciążenia, zmiany temperatury i warunki środowiskowe. Dzięki temu idealnie nadają się do zastosowań, w których trwałość i długotrwała wydajność mają kluczowe znaczenie.
Kolejnym powodem popularności klejów akrylowych jest ich szybki czas utwardzania. W porównaniu z innymi rodzajami klejów, kleje akrylowe mają stosunkowo krótki czas utwardzania, co pozwala na szybsze cykle produkcyjne. Często osiągają wytrzymałość w ciągu kilku minut, skracając czas montażu i zwiększając produktywność.
Ponadto kleje akrylowe są znane z odporności na wilgoć, chemikalia i promieniowanie UV. Mają doskonałą wodoodporność i mogą zachować swoje właściwości klejące nawet w wilgotnym środowisku. Ta cecha sprawia, że nadają się do zastosowań zewnętrznych i środowisk, w których spodziewana jest ekspozycja na trudne warunki.
Kleje akrylowe zapewniają również doskonałą stabilność termiczną. Mogą wytrzymać szeroki zakres temperatur, od ekstremalnie niskich do wysokich temperatur, bez uszczerbku dla siły wiązania. Ta odporność termiczna sprawia, że nadają się do zastosowań, w których często występują wahania temperatury, na przykład w przemyśle motoryzacyjnym i elektronicznym.
Oprócz swoich właściwości fizycznych, kleje akrylowe są łatwe w obsłudze i aplikacji. Dostępne są w różnych formach, w tym płynów, past, filmów i taśm, oferując elastyczność w metodach aplikacji. Można je nakładać za pomocą zautomatyzowanych systemów dozujących lub ręcznie, w zależności od specyficznych wymagań aplikacji.
Ponadto kleje akrylowe są na ogół bezwonne i mają niską zawartość lotnych związków organicznych (LZO). Dzięki temu są bezpieczniejsze niż kleje na bazie rozpuszczalników, które mogą wydzielać silne zapachy lub zawierać szkodliwe chemikalia.
Kleje silikonowe: doskonała odporność na środowisko
Kleje silikonowe to klasa klejów znanych ze swojej doskonałej odporności na warunki środowiskowe. Oferują wyjątkową wydajność i trwałość w różnych zastosowaniach, dzięki czemu są bardzo poszukiwane w przemyśle motoryzacyjnym, elektronicznym, lotniczym, budowlanym i medycznym.
Jedną z najważniejszych zalet klejów silikonowych jest ich odporność na ekstremalne temperatury. Mogą wytrzymać wysokie i niskie temperatury, nie tracąc właściwości adhezyjnych ani nie stając się kruche. Dzięki temu nadają się do zastosowań, w których często występują wahania temperatury, na przykład w silnikach samochodowych lub urządzeniach elektronicznych.
Kleje silikonowe wykazują również doskonałą odporność na wilgoć i wodę. W przeciwieństwie do wielu innych rodzajów klejów, mogą zachować wytrzymałość i integralność nawet w przypadku wystawienia na działanie wody lub wilgotnego środowiska. Ta właściwość ma kluczowe znaczenie w zastosowaniach wymagających wodoodporności, takich jak uszczelnianie uszczelek, łączenie elementów podwodnych lub ochrona obwodów elektronicznych przed uszkodzeniem przez wilgoć.
Ponadto kleje silikonowe zapewniają wyjątkową odporność na promieniowanie UV i warunki atmosferyczne. Mogą wytrzymać długotrwałą ekspozycję na światło słoneczne, deszcz, śnieg i inne czynniki środowiskowe bez degradacji lub utraty swoich właściwości adhezyjnych. Dzięki temu idealnie nadają się do zastosowań zewnętrznych, takich jak uszczelnianie oznakowań zewnętrznych, łączenie paneli słonecznych lub ochrona zewnętrznych urządzeń elektronicznych.
Odporność chemiczna to kolejny obszar, w którym kleje silikonowe wyróżniają się. Są odporne na różne chemikalia, w tym rozpuszczalniki, oleje, paliwa i kwasy. Odporność ta jest istotna w branżach takich jak motoryzacja i lotnictwo, gdzie narażenie na wiele chemikaliów jest codzienne. Nawet w agresywnych chemikaliach kleje silikonowe mogą zachować swoją integralność i przyczepność, zapewniając długotrwałą wydajność i niezawodność.
Oprócz odporności na warunki środowiskowe, kleje silikonowe oferują doskonałe właściwości izolacji elektrycznej. Mają wysoką wytrzymałość dielektryczną i mogą zapewniać izolację przed prądami elektrycznymi. Dzięki temu idealnie nadają się do klejenia i uszczelniania elementów elektronicznych, gdzie izolacja elektryczna i ochrona mają kluczowe znaczenie.
Kleje silikonowe są dostępne w różnych formach, w tym w systemach jednoskładnikowych lub dwuskładnikowych, a także z różnymi mechanizmami utwardzania, takimi jak utwardzanie termiczne, utwardzanie wilgocią lub utwardzanie UV. Ta wszechstronność pozwala na szeroki zakres zastosowań i wymagań dotyczących łączenia.
Warto zauważyć, że chociaż kleje silikonowe zapewniają wyjątkową odporność na warunki środowiskowe, mogą nie mieć tak wysokiej początkowej siły wiązania, jak niektóre inne rodzaje klejów. Rekompensują to jednak swoją elastycznością, trwałością i wieloletnim działaniem w trudnych warunkach.
Kleje utwardzane promieniami UV: szybkie i precyzyjne wiązanie
Kleje utwardzane promieniowaniem UV, znane również jako kleje utwardzane promieniowaniem ultrafioletowym, zyskały znaczną popularność w różnych gałęziach przemysłu ze względu na ich zdolność do szybkiego i precyzyjnego łączenia. Kleje te oferują wiele zalet w porównaniu z tradycyjnymi systemami klejącymi, co czyni je preferowanym wyborem do zastosowań wymagających szybkiego i niezawodnego klejenia.
Kleje utwardzane promieniowaniem UV zawierają specjalne fotoinicjatory, które inicjują proces pod wpływem światła ultrafioletowego. Reakcja utwardzania zachodzi niemal natychmiast, umożliwiając szybkie tworzenie wiązań. W przeciwieństwie do konwencjonalnych klejów, które do utwardzania wykorzystują ciepło lub reakcje chemiczne, kleje utwardzane promieniowaniem UV zapewniają praktycznie natychmiastowe wiązanie, oszczędzając cenny czas produkcji i zwiększając wydajność.
Jedną z najważniejszych zalet klejów utwardzanych promieniowaniem UV jest ich precyzyjna zdolność wiązania. Reakcja utwardzania jest ściśle kontrolowana i zlokalizowana, dzięki czemu klej utwardza się tylko w żądanym obszarze. Umożliwia to precyzyjne pozycjonowanie i wyrównywanie komponentów, nawet w złożonych zespołach. Producenci mogą osiągnąć wąskie tolerancje i utrzymać wysoką jakość produktu za pomocą klejów utwardzanych promieniowaniem UV.
Szybki czas utwardzania klejów UV jest szczególnie korzystny w branżach, w których kluczowe znaczenie ma szybka realizacja produkcji. Na przykład w produkcji elektroniki kleje utwardzane promieniowaniem UV umożliwiają szybkie łączenie elementów, skracając czas montażu i zwiększając produktywność. Podobnie w branży urządzeń medycznych kleje UV zapewniają szybkie i niezawodne łączenie różnych materiałów, umożliwiając szybki montaż skomplikowanych urządzeń medycznych.
Kleje utwardzane promieniami UV zapewniają doskonałą siłę wiązania i trwałość. Po utwardzeniu kleje te tworzą silne wiązania, które są odporne na różne warunki środowiskowe, w tym wahania temperatury, wilgoć i chemikalia. Spoiwa wykazują wysoką odporność na żółknięcie lub degradację w czasie, zapewniając długotrwałą wydajność i niezawodność.
Kleje utwardzane promieniowaniem UV są wszechstronne i kompatybilne z różnymi podłożami, w tym z tworzywami sztucznymi, metalami, szkłem i ceramiką. Mogą łączyć ze sobą różne materiały, poszerzając zakres zastosowań, w których można je wykorzystać. Kleje utwardzane promieniowaniem UV oferują niezawodne rozwiązanie dla różnorodnych potrzeb w zakresie klejenia, od zatrzaskiwanych elementów plastikowych w przemyśle motoryzacyjnym po montaż urządzeń elektronicznych.
Ponadto kleje utwardzane promieniowaniem UV nie zawierają rozpuszczalników, co eliminuje potrzebę stosowania lotnych związków organicznych (LZO) i zmniejsza wpływ na środowisko. Oferują również korzyści dla zdrowia i bezpieczeństwa, minimalizując narażenie na niebezpieczne chemikalia. Brak rozpuszczalników i lotnych związków organicznych przyczynia się do czystszego i zdrowszego środowiska pracy dla operatorów.
Kleje epoksydowe: Wysoka siła wiązania i odporność chemiczna
Kleje epoksydowe są popularne w różnych gałęziach przemysłu ze względu na ich wysoką siłę wiązania i doskonałe właściwości odporności chemicznej. Oferują liczne zalety w porównaniu z innymi opcjami kleju, dzięki czemu są wszechstronne i niezawodne w wielu zastosowaniach.
Jedną z najważniejszych zalet klejów epoksydowych jest ich wyjątkowa siła wiązania. Tworzą silne wiązania, które mogą wytrzymać znaczne naprężenia i obciążenia, gdy są prawidłowo stosowane, dzięki czemu nadają się do zastosowań wymagających trwałego i długotrwałego wiązania. Kleje epoksydowe mogą łączyć różne materiały, w tym metale, tworzywa sztuczne, ceramikę, szkło i kompozyty, zapewniając niezawodne rozwiązanie do łączenia dla różnych gałęzi przemysłu.
Oprócz wysokiej siły wiązania, kleje epoksydowe wykazują doskonałą odporność chemiczną. Mogą wytrzymać różne chemikalia, w tym rozpuszczalniki, kwasy, zasady, oleje i paliwa. Ta odporność na działanie środków chemicznych zapewnia stabilność kleju i siłę wiązania nawet w trudnych warunkach. W związku z tym kleje epoksydowe są powszechnie stosowane w przemyśle motoryzacyjnym, lotniczym, elektronicznym i chemicznym, gdzie narażenie na chemikalia stanowi problem.
Odporność chemiczna klejów epoksydowych wynika z ich unikalnej struktury molekularnej. Kleje epoksydowe składają się z żywicy i utwardzacza, które reagują chemicznie, tworząc usieciowaną sieć. Ta usieciowana struktura zapewnia klejowi wytrzymałość i odporność na chemikalia. Proces utwardzania klejów epoksydowych można regulować w celu uzyskania różnych poziomów odporności chemicznej, co pozwala na dostosowanie do wymagań konkretnego zastosowania.
Ponadto kleje epoksydowe zapewniają doskonałą odporność na temperaturę, co jest kolejnym kluczowym czynnikiem w wielu gałęziach przemysłu. Mogą zachować siłę i integralność wiązania w wysokich i niskich temperaturach, dzięki czemu nadają się do zastosowań narażonych na ekstremalne wahania temperatury. Ta właściwość ma fundamentalne znaczenie w branżach takich jak przemysł lotniczy i motoryzacyjny, gdzie komponenty mogą podlegać znacznym wahaniom temperatury.
Kolejną zaletą klejów epoksydowych jest ich wszechstronność w zakresie metod aplikacji. Można je stosować różnymi technikami, w tym dozowaniem ręcznym, dozowaniem strzykawką, nanoszeniem w sprayu i automatycznymi systemami dozowania. Ta elastyczność metod aplikacji umożliwia wydajne i precyzyjne łączenie w różnych środowiskach produkcyjnych.
Należy zauważyć, że odpowiednie przygotowanie powierzchni i techniki nakładania kleju są niezbędne do uzyskania optymalnej siły wiązania i odporności chemicznej za pomocą klejów epoksydowych. Powierzchnie powinny być czyste, suche i wolne od zanieczyszczeń, aby zapewnić maksymalną przyczepność. Dodatkowo klej należy mieszać zgodnie z zaleceniami producenta uwzględniając właściwe proporcje żywicy do utwardzacza oraz odpowiednie warunki utwardzania.
Podsumowując, kleje epoksydowe zapewniają wysoką siłę wiązania i doskonałą odporność chemiczną, co czyni je idealnym wyborem do różnych zastosowań. Ich zdolność do łączenia różnych materiałów, odporność na agresywne chemikalia i dobre działanie w ekstremalnych temperaturach czyni je niezastąpionymi w przemyśle motoryzacyjnym, lotniczym, elektronicznym i chemicznym. Przy odpowiednim przygotowaniu powierzchni i technikach aplikacji, kleje epoksydowe mogą zapewnić trwałe i niezawodne wiązania, przyczyniając się do ogólnej wydajności i trwałości zmontowanych elementów.
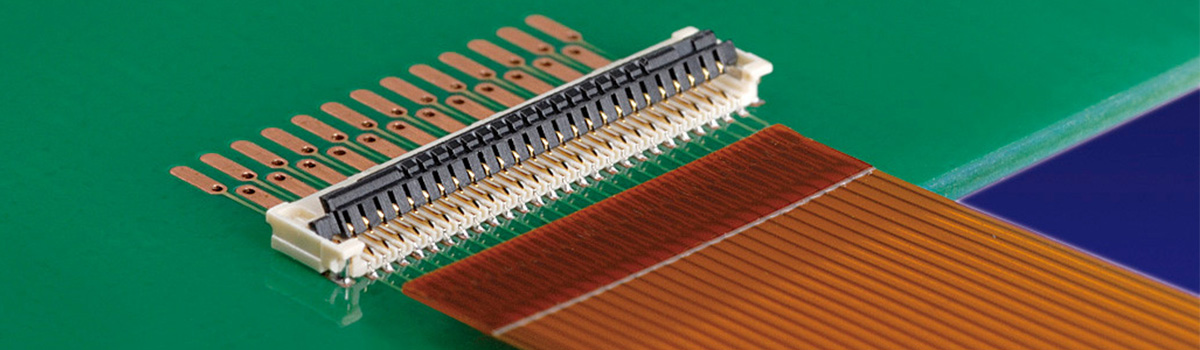
Kleje przewodzące: umożliwianie połączeń elektrycznych
Kleje przewodzące odgrywają kluczową rolę w umożliwianiu połączeń elektrycznych w różnych zastosowaniach. Te innowacyjne materiały stanowią skuteczną alternatywę dla tradycyjnych metod lutowania lub mocowania mechanicznego, oferując doskonałą przewodność elektryczną, łatwość użycia i wszechstronność. W tym artykule omówiono kluczowe cechy i zastosowania klejów przewodzących.
Kleje przewodzące są formułowane przy użyciu kombinacji przewodzących wypełniaczy, takich jak srebro, miedź lub węgiel, oraz spoiwa polimerowego. Wypełniacze przewodzące ułatwiają przepływ prądu elektrycznego, a spoiwo zapewnia przyczepność do różnych podłoży. Ta unikalna kompozycja sprawia, że kleje przewodzące zapewniają niezawodne połączenia elektryczne nawet w trudnych warunkach.
Jedną z podstawowych zalet klejów przewodzących jest ich kompatybilność z szeroką gamą materiałów. Mogą łączyć metale, ceramikę, szkło, tworzywa sztuczne, a nawet elastyczne podłoża, dzięki czemu nadają się do różnych gałęzi przemysłu. Łączenie różnych materiałów jest szczególnie korzystne w przemyśle elektronicznym, gdzie muszą być łączone elementy o różnych współczynnikach rozszerzalności cieplnej.
Kleje przewodzące zapewniają doskonałe przewodnictwo elektryczne, porównywalne z tradycyjnym lutowaniem. Ta właściwość umożliwia im skuteczną wymianę połączeń lutowanych w określonych zastosowaniach. Ponadto kleje przewodzące wykazują lepszą odporność na cykle termiczne, naprężenia mechaniczne i wibracje niż połączenia lutowane. Te cechy sprawiają, że idealnie nadają się do zastosowań z częstymi wahaniami temperatury lub ruchami automatycznymi.
Łatwość aplikacji to kolejna istotna zaleta klejów przewodzących. Zazwyczaj są one dostępne w wygodnych postaciach, takich jak strzykawki, lub dozowane jako folie lub taśmy. Pozwala to na precyzyjne i kontrolowane dozowanie, dzięki czemu nadają się do zautomatyzowanych i ręcznych procesów montażu. W przeciwieństwie do lutowania, które wymaga specjalistycznego sprzętu i wiedzy, kleje przewodzące można łatwo nakładać po minimalnym przeszkoleniu.
Kleje przewodzące znajdują zastosowanie w różnych gałęziach przemysłu. W sektorze elektronicznym są one używane do mocowania komponentów, łączenia matryc, łączenia przewodów oraz jako alternatywa dla lutowania w montażu płytek drukowanych (PCB). Są również wykorzystywane do produkcji elastycznej elektroniki, gdzie tradycyjne metody lutowania nie są możliwe ze względu na elastyczność substratów.
W przemyśle motoryzacyjnym kleje przewodzące są wykorzystywane do łączenia czujników, anten i systemów oświetleniowych. Zapewniają doskonałą przyczepność do materiałów stosowanych w przemyśle motoryzacyjnym, w tym do tworzyw sztucznych i kompozytów. Co więcej, ich odporność na trudne warunki środowiskowe, takie jak wahania temperatury, wilgotność i narażenie chemiczne, czyni je idealnym wyborem dla elektroniki samochodowej.
Kleje przewodzące odgrywają również znaczącą rolę w medycynie. Montują urządzenia medyczne, takie jak czujniki, elektrody i urządzenia do implantacji. Biokompatybilne warianty klejów przewodzących zapewniają, że są one bezpieczne w kontakcie z tkankami ludzkimi.
Kleje o niskim stopniu odgazowania: krytyczne w zastosowaniach kosmicznych
Kleje o niskim poziomie odgazowywania odgrywają kluczową rolę w zastosowaniach kosmicznych, w których materiały muszą wytrzymać ekstremalne warunki środowiska kosmicznego. Odgazowywanie odnosi się do uwalniania lotnych związków z materiałów pod wpływem próżni lub wysokich temperatur. W kosmosie te lotne związki mogą stanowić poważne zagrożenie dla funkcjonalności i niezawodności wrażliwego sprzętu i instrumentów.
W próżni kosmicznej odgazowane materiały mogą skraplać się na pobliskich powierzchniach, takich jak soczewki optyczne lub czujniki, powodując zanieczyszczenie i pogorszenie działania. Zanieczyszczenia mogą pogorszyć dokładność pomiarów, obniżyć jakość sygnału, a nawet doprowadzić do awarii krytycznych komponentów. Co więcej, skondensowane odgazowane materiały mogą gromadzić się z czasem, tworząc warstwę, która może pochłaniać lub rozpraszać światło, wpływając na układy optyczne i urządzenia obrazujące.
Kleje o niskiej emisji gazów są specjalnie opracowane, aby zminimalizować uwalnianie lotnych związków. Zostały zaprojektowane tak, aby miały niską prężność pary, co oznacza, że uwalniają mniej gazów i oparów pod wpływem próżni. Ta cecha pomaga zapobiegać zanieczyszczeniu i degradacji wrażliwych powierzchni i komponentów.
Statki kosmiczne i satelity polegają na klejach o niskiej emisji gazów do różnych zastosowań. Jednym z ważnych zastosowań jest łączenie i hermetyzacja elementów elektronicznych. Kleje te zapewniają solidne i niezawodne wiązanie między różnymi materiałami, jednocześnie minimalizując ryzyko zanieczyszczenia i problemów związanych z odgazowywaniem. Zapewniają integralność strukturalną komponentów i łączność elektryczną, pozwalając im wytrzymać wibracje i wstrząsy występujące podczas startu i operacji w kosmosie.
Kleje o niskim stopniu odgazowania są również niezbędne w układach optycznych stosowanych w teleskopach kosmicznych, kamerach i czujnikach. Kleje stosowane w tych systemach muszą mieć minimalny wpływ na przejrzystość i działanie soczewek, luster i detektorów. Ograniczając odgazowywanie, kleje te zachowują właściwości optyczne i zapobiegają tworzeniu się warstw zanieczyszczeń, które mogłyby pogorszyć jakość obrazu lub zakłócić precyzyjne pomiary.
Ponadto zarządzanie ciepłem jest kluczowym czynnikiem w zastosowaniach kosmicznych. Kleje o niskiej emisji gazów łączą radiatory, materiały termiczne i inne elementy biorące udział w rozpraszaniu ciepła. Kleje te zapewniają efektywne przenoszenie ciepła, jednocześnie minimalizując ryzyko zanieczyszczenia, które mogłoby pogorszyć działanie systemów zarządzania ciepłem.
Aby spełnić surowe wymagania zastosowań kosmicznych, kleje o niskim poziomie odgazowywania przechodzą rygorystyczne testy i procesy certyfikacji. Materiały są poddawane cyklom termicznym, działaniu próżni i analizie w celu oceny ich właściwości odgazowywania. Kleje, które spełniają standardy określone przez organizacje, takie jak wymagania NASA dotyczące odgazowywania (takie jak ASTM E595), są uważane za odpowiednie do misji kosmicznych.
Kleje przewodzące ciepło: zarządzanie ciepłem w urządzeniach elektronicznych
Kleje termoprzewodzące odgrywają kluczową rolę w zarządzaniu ciepłem w urządzeniach elektronicznych. W miarę zmniejszania się rozmiarów komponentów elektronicznych i pracy przy wyższych gęstościach mocy, efektywne odprowadzanie ciepła staje się coraz ważniejsze dla zapewnienia optymalnej wydajności i niezawodności. Kleje przewodzące ciepło stanowią realne rozwiązanie, skutecznie przenosząc ciepło z elementów generujących ciepło do radiatorów lub innych mechanizmów rozpraszania ciepła. W tym artykule zbadamy krytyczne aspekty klejów przewodzących ciepło i ich rolę w zarządzaniu ciepłem w urządzeniach elektronicznych.
Kleje termoprzewodzące to specjalnie opracowane materiały, które mają zarówno właściwości adhezyjne, jak i wysoką przewodność cieplną. Mają one na celu tworzenie silnych połączeń między elementami wytwarzającymi ciepło, takimi jak układy scalone lub urządzenia zasilające, a radiatorami lub innymi elementami chłodzącymi. Adhezyjny charakter tych materiałów zapewnia niezawodne mocowanie, a ich wysoka przewodność cieplna umożliwia wydajne przenoszenie ciepła.
Jedną z głównych zalet klejów przewodzących ciepło jest ich zdolność do wypełniania małych szczelin i nierówności między współpracującymi powierzchniami, minimalizując w ten sposób opór cieplny. Ta cecha jest szczególnie korzystna w przypadku mocowania elementów o niepłaskich powierzchniach lub w przypadku mikroskopijnych szczelin powietrznych utrudniających przepływ ciepła. Wypełniając te luki, kleje przewodzące ciepło zapewniają bliski kontakt między znakami, poprawiając wymianę ciepła i zmniejszając ryzyko powstawania gorących punktów.
Innym krytycznym aspektem zarządzania ciepłem w urządzeniach elektronicznych jest odporność na cykliczne zmiany temperatury i naprężenia mechaniczne. Urządzenia elektroniczne podczas pracy są narażone na zmienne warunki temperaturowe i drgania mechaniczne. Kleje termoprzewodzące zostały opracowane w taki sposób, aby zachować siłę klejenia i wydajność termiczną w szerokim zakresie temperatur, zapewniając niezawodne odprowadzanie ciepła nawet w trudnych warunkach.
Ponadto kleje przewodzące ciepło zapewniają właściwości izolacji elektrycznej, zapobiegając zwarciom elektrycznym między elementami. Ta cecha ma kluczowe znaczenie w urządzeniach elektronicznych, w których wiele elementów jest gęsto upakowanych i istnieje ryzyko przypadkowego zetknięcia się elementów przewodzących.
Kleje termoprzewodzące można nakładać różnymi metodami, w tym poprzez dozowanie, sitodruk lub laminowanie folii. Kleje te są dostępne w różnych lepkościach i mechanizmach utwardzania, co pozwala na elastyczność procesu produkcyjnego. Niektóre kleje przewodzące ciepło utwardzają się w temperaturze pokojowej, podczas gdy inne wymagają podwyższonej temperatury lub światła UV. Producenci mogą wybrać spoiwo, które najlepiej odpowiada ich specyficznym wymaganiom produkcyjnym.
Kleje samoprzylepne: łatwe w użyciu i aplikacji
Kleje samoprzylepne zrewolucjonizowały sposób, w jaki podchodzimy do różnych projektów i zadań wymagających łączenia materiałów. Kleje te są niezwykle łatwe w użyciu i aplikacji, co czyni je popularnymi wśród profesjonalistów i entuzjastów majsterkowania. Dzięki swojej wygodzie i wszechstronności kleje samoprzylepne stały się popularnym rozwiązaniem dla wielu zastosowań.
Jedną z głównych zalet klejów samoprzylepnych jest ich prostota. W przeciwieństwie do tradycyjnych klejów, które często wymagają mieszania lub specjalistycznych narzędzi, kleje samoprzylepne są wstępnie nałożone na materiał podkładowy i gotowe do użycia po wyjęciu z opakowania. Eliminuje to potrzebę dodatkowego wyposażenia lub obszernych przygotowań, oszczędzając czas i wysiłek.
Proces aplikacji klejów samoprzylepnych jest prosty i przyjazny dla użytkownika. Wszystko, co musisz zrobić, to oderwać papier podkładowy, aby odsłonić stronę samoprzylepną i mocno docisnąć go do żądanej powierzchni. Klej wiąże szybko i pewnie, zapewniając natychmiastową adhezję bez zacisków i czasu schnięcia. Dzięki temu kleje samoprzylepne idealnie nadają się do szybkich napraw, tymczasowych instalacji lub projektów, w których liczy się czas.
Kolejną zaletą klejów samoprzylepnych jest ich wszechstronność. Są dostępne w różnych formach, takich jak taśmy, arkusze lub kropki, aby dostosować się do różnych zastosowań i materiałów. Niezależnie od tego, czy potrzebujesz przymocować lekkie przedmioty, zamontować dekoracje, czy też niektóre ciężkie przedmioty, samoprzylepny klej jest odpowiedni do tego zadania. Dobrze przylegają do różnych powierzchni, w tym drewna, metalu, szkła, plastiku i tkaniny, oferując elastyczność i kompatybilność z różnymi materiałami.
Kleje samoprzylepne są również znane z czystego nakładania. W przeciwieństwie do tradycyjnych klejów, które mogą powodować bałagan i wymagać czyszczenia, kleje samoprzylepne nie pozostawiają śladów po prawidłowym nałożeniu i usunięciu. Jest to szczególnie korzystne podczas pracy na delikatnych lub wykończonych powierzchniach, które chcesz chronić przed uszkodzeniem.
Oprócz łatwości użycia, kleje samoprzylepne często wykazują silne właściwości wiążące. Kleje zostały zaprojektowane tak, aby zapewnić niezawodne i trwałe połączenie, zapewniając, że przymocowane elementy pozostają bezpiecznie na swoim miejscu. Jednak wybór odpowiedniego rodzaju kleju do projektu i przestrzeganie wskazówek producenta w celu uzyskania optymalnych rezultatów ma kluczowe znaczenie.
Folie samoprzylepne: zwiększenie wydajności i spójności
Folie samoprzylepne to wszechstronne materiały, które oferują różnorodne zastosowania w różnych gałęziach przemysłu. Są to cienkie warstwy lepkich substancji nałożonych na materiał podkładowy, taki jak papier, plastik lub tkanina. Folie te zapewniają wiele korzyści, zwiększając wydajność i spójność w różnych procesach. W tym artykule zbadamy, w jaki sposób folie samoprzylepne poprawiają wydajność i spójność w różnych zastosowaniach.
Jedną z kluczowych zalet folii samoprzylepnych jest ich łatwość aplikacji. W przeciwieństwie do tradycyjnych klejów, które mogą wymagać mieszania lub specjalistycznego sprzętu, folie samoprzylepne są gotowe do użycia. Można je łatwo przyciąć do pożądanych kształtów i rozmiarów, dzięki czemu idealnie nadają się do szybkiego i precyzyjnego nakładania. Oszczędza to czas i zasoby procesów produkcyjnych i montażowych, zwiększając ogólną wydajność.
Ponadto folie samoprzylepne zapewniają stałą skuteczność łączenia. Ich jednolita grubość i kontrolowane właściwości adhezyjne zapewniają niezawodne przyleganie różnych materiałów. Niezależnie od tego, czy chodzi o łączenie dwóch powierzchni, laminowanie warstw czy mocowanie elementów, folie samoprzylepne zapewniają stałą siłę wiązania, minimalizując ryzyko awarii lub przeróbek. Ta spójność poprawia jakość produktu, zmniejsza ilość odpadów i zwiększa produktywność.
Innym sposobem, w jaki folie samoprzylepne zwiększają wydajność, jest ich kompatybilność z systemami automatyki. Wraz z rosnącym trendem automatyzacji w różnych branżach, folie samoprzylepne są projektowane tak, aby były kompatybilne z zrobotyzowanymi procesami montażu i pakowania. Można je łatwo zintegrować ze zautomatyzowanymi liniami produkcyjnymi, umożliwiając szybkie i precyzyjne operacje łączenia. To nie tylko poprawia wydajność, ale także zmniejsza koszty pracy i błędy ludzkie.
Ponadto folie samoprzylepne oferują zwiększoną skuteczność w zastosowaniach uszczelniających i ochronnych. Stanowią barierę przed wilgocią, kurzem i zanieczyszczeniami, zapobiegając uszkodzeniu wrażliwych komponentów lub produktów. Niezależnie od tego, czy chodzi o uszczelnianie urządzeń elektronicznych, pakowanie produktów spożywczych czy też zabezpieczanie powierzchni przed korozją, folie samoprzylepne zapewniają niezawodną i stałą ochronę. Przyczynia się to do długowieczności i niezawodności produktów, zmniejszając potrzebę częstej konserwacji lub wymiany.
Ponadto folie samoprzylepne umożliwiają wydajne dostosowywanie i elastyczność projektowania. Można je dostosować do konkretnych wymagań, takich jak różne siły wiązania, odporność na temperaturę lub właściwości optyczne. Pozwala to producentom na optymalizację właściwości kleju w oparciu o potrzeby ich aplikacji, zapewniając najlepszą wydajność i niezawodność. Ponadto folie samoprzylepne można łatwo zadrukować lub ozdobić, oferując możliwości promowania marki i estetyczny wygląd.
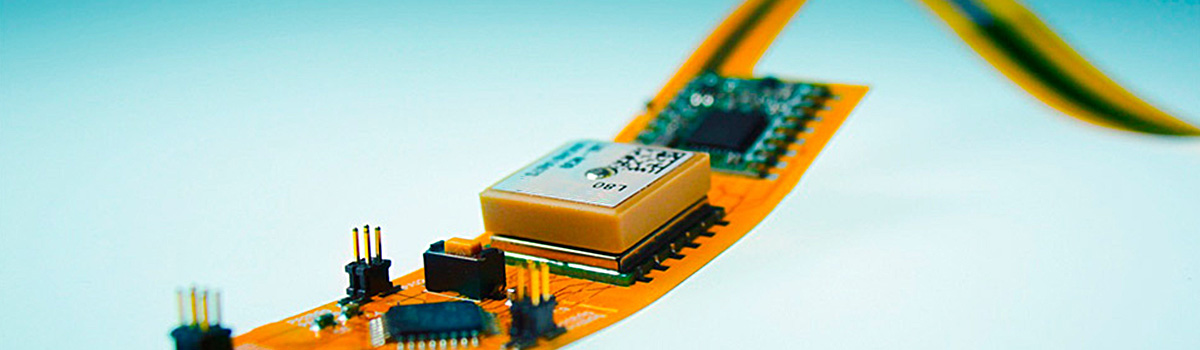
Kleje termotopliwe: szybkie i trwałe wiązanie
Kleje topliwe (HMA) to uniwersalne kleje, które oferują szybkie i trwałe rozwiązania w zakresie klejenia w różnych branżach i zastosowaniach. Te kleje lub gorący klej to materiały termoplastyczne, które są topione do stanu ciekłego i nakładane w stanie stopionym. Po schłodzeniu twardnieją i tworzą silne wiązanie między podłożami. Oto bliższe spojrzenie na właściwości, zalety i zastosowania klejów topliwych.
Jedną z krytycznych zalet HMA jest ich zdolność szybkiego wiązania. Kleje te szybko upłynniają się po podgrzaniu, co pozwala na wydajną i szybką aplikację. Eliminują potrzebę odparowania rozpuszczalnika lub reakcji chemicznych, w przeciwieństwie do innych rodzajów klejów. Szybkie krzepnięcie klejów termotopliwych skraca czas montażu i produkcji, zwiększając produktywność i zmniejszając koszty.
Ponadto kleje termotopliwe zapewniają wyjątkową trwałość połączeń klejonych. Wykazują doskonałą odporność na wilgoć, chemikalia i wahania temperatury. Ta sprężystość sprawia, że nadają się do wymagających środowisk i zastosowań, które wymagają trwałego i niezawodnego łączenia. HMA oferują również elastyczność i odporność na uderzenia, dzięki czemu wytrzymują wibracje i wstrząsy bez uszczerbku dla integralności wiązania.
HMA znajdują zastosowanie w różnych branżach, w tym w opakowaniach, obróbce drewna, motoryzacji, elektronice, tekstyliach i budownictwie. Kleje termotopliwe są szeroko stosowane w opakowaniach do uszczelniania pudełek i kartonów, zamknięć z zabezpieczeniem gwarancyjnym oraz klejenia etykiet i taśm. Zapewniają bezpieczne i odporne na manipulacje plomby, zapewniając integralność produktu i zapobiegając kradzieży.
Zastosowania HMA w obróbce drewna obejmują operacje oklejania krawędzi, fornirowania i laminowania. Szybkowiążący charakter klejów topliwych ułatwia wydajne procesy na linii montażowej. Tworzą silne wiązania w drewnianych połączeniach, wzmacniając strukturalną integralność i trwałość mebli i szafek.
Producenci samochodów polegają na klejach topliwych do klejenia elementów wewnętrznych i zewnętrznych, łączenia przewodów i uszczelniania uszczelek. Trwałość i odporność termiczna tych klejów czyni je idealnymi do zastosowań motoryzacyjnych, gdzie wydajność w ekstremalnych warunkach ma kluczowe znaczenie.
Montaż i produkcja elektroniki często wykorzystuje kleje topliwe do łączenia komponentów, sczepiania przewodów i hermetyzacji. Ich zdolność do łączenia różnych materiałów, takich jak tworzywa sztuczne, metale i szkło, sprawia, że nadają się do różnorodnych zastosowań elektronicznych.
Zastosowania klejów topliwych w przemyśle włókienniczym obejmują laminowanie tkanin, obszywanie i łączenie aplikacji. Umożliwiają precyzyjne i czyste łączenie bez szycia, zszywania lub innych mechanicznych metod mocowania.
W sektorze budowlanym HMA są używane do montażu podłóg, paneli, izolacji i klejenia płytek. Ich właściwości szybkowiążące ułatwiają szybkie procesy budowlane i zapewniają niezawodną przyczepność do różnych materiałów budowlanych.
Kleje wrażliwe na nacisk: zapewnienie spójnej przyczepności
Kleje samoprzylepne (PSA) to uniwersalne materiały stosowane w różnych gałęziach przemysłu, od motoryzacji i elektroniki po opakowania i urządzenia medyczne. Kleje te oferują wyjątkowe zalety, takie jak łatwość aplikacji, natychmiastowe wiązanie i zdolność przylegania do szerokiej gamy powierzchni. Jednak zapewnienie spójnej przyczepności może być wyzwaniem podczas pracy z PSA. Oto kilka kluczowych kwestii, które należy wziąć pod uwagę, aby uzyskać niezawodną i spójną przyczepność za pomocą klejów samoprzylepnych.
- Przygotowanie powierzchni: Właściwe przygotowanie powierzchni ma kluczowe znaczenie dla uzyskania spójnej przyczepności z klejami samoprzylepnymi. Powierzchnie muszą być czyste, suche i wolne od kurzu, oleju, smaru i wilgoci. Czyszczenie powierzchni odpowiednimi rozpuszczalnikami lub środkami czyszczącymi oraz stosowanie technik takich jak ścieranie lub obróbka plazmowa może poprawić przyczepność poprzez zwiększenie energii powierzchniowej i usunięcie potencjalnych barier dla wiązania.
- Kompatybilność materiałowa: Niezbędne jest zapewnienie kompatybilności PSA z materiałem podłoża. Niektóre PSA mogą wykazywać słabą przyczepność lub problemy z kompatybilnością z niektórymi powierzchniami. Zrozumienie składu chemicznego i właściwości zarówno kleju, jak i podłoża może pomóc w doborze odpowiedniego kleju do konkretnego zastosowania, zapewniając spójną przyczepność.
- Technika aplikacji: Technika aplikacji odgrywa znaczącą rolę w uzyskaniu jednolitej przyczepności. Ciśnienie, temperatura i czas przebywania podczas aplikacji mogą wpływać na siłę wiązania. Należy bezwzględnie przestrzegać zaleceń producenta dotyczących parametrów aplikacji, w tym odpowiedniego docisku oraz zalecanego zakresu temperatur klejenia.
- Czas utwardzania: kleje samoprzylepne zazwyczaj wymagają pewnej ilości czasu, aby uzyskać pełną siłę przyczepności. Ten czas utwardzania lub „przebywania” umożliwia płynięcie kleju i tworzenie silnych wiązań z podłożem. Istotne jest, aby zapewnić wystarczający czas utwardzania przed poddaniem sklejonego elementu naprężeniom lub obciążeniom. Pośpiech w procesie może spowodować słabszą przyczepność lub nawet uszkodzenie kleju.
- Czynniki środowiskowe: Warunki środowiskowe mogą wpływać na działanie PSA. Czynniki takie jak temperatura, wilgotność i narażenie na chemikalia lub promieniowanie UV mogą wpływać na właściwości kleju i przyczepność. Zrozumienie specyficznych warunków środowiskowych, na które klej będzie narażony, i wybór kleju o odpowiedniej odporności na te czynniki może pomóc w zapewnieniu spójnej przyczepności w czasie.
- Testy i kontrola jakości: Regularne testy i środki kontroli jakości są niezbędne do zapewnienia spójnej przyczepności. Różne metody testowe, takie jak przyczepność do odrywania, wytrzymałość na ścinanie i przylepność, mogą ocenić działanie kleju. Ustanowienie odpowiednich protokołów testowania i przeprowadzanie regularnych kontroli jakości podczas produkcji może pomóc we wczesnej identyfikacji wszelkich niespójności lub problemów i zapewnić spójną przyczepność produktu końcowego.
- Przechowywanie i okres przydatności do spożycia: Właściwe warunki przechowywania i przestrzeganie zaleceń dotyczących okresu przydatności do spożycia są niezbędne do zachowania właściwości kleju. PSA mogą z czasem ulec degradacji pod wpływem ciepła, światła lub powietrza, wpływając na ich właściwości adhezyjne. Przechowywanie wiązań w kontrolowanych warunkach i używanie ich w zalecanym okresie przydatności do spożycia może pomóc w utrzymaniu spójnej przyczepności.
Techniki dozowania kleju: precyzja i wydajność
Techniki dozowania kleju mają kluczowe znaczenie w różnych gałęziach przemysłu, zapewniając precyzję i wydajność w aplikacjach klejenia. Niezależnie od tego, czy chodzi o produkcję, montaż czy naprawę, właściwa metoda dozowania może znacząco wpłynąć na jakość i niezawodność połączeń klejowych. W tym artykule omówimy krytyczne techniki, które pomagają osiągnąć precyzję i wydajność dozowania kleju przy ograniczonej liczbie słów.
- Ręczne dozowanie: Ręczne dozowanie kleju jest powszechnie stosowane w operacjach na małą skalę lub w złożonych aplikacjach. Polega na precyzyjnym nakładaniu kleju za pomocą ręcznych urządzeń, takich jak strzykawki, wyciskane butelki lub pędzle. Chociaż ta metoda zapewnia elastyczność i kontrolę, zależy ona od umiejętności i konsekwencji operatora.
- Dozowanie w czasie/ciśnieniu: Dozowanie w czasie/ciśnieniu jest szeroko stosowaną techniką, która zapewnia spójne i kontrolowane nakładanie kleju. Polega na zastosowaniu pneumatycznych lub elektrycznych dystrybutorów z regulatorami ciśnienia i timerami. Dostosowując czas i ciśnienie dozowania, operatorzy mogą dokładnie kontrolować ilość nakładanego kleju. Ta technika jest odpowiednia dla klejów o średniej i wysokiej lepkości.
- Natryskiwanie: Natryskiwanie to technika dozowania, która wykorzystuje strumień kleju o dużej prędkości do precyzyjnego nakładania małych ilości kleju na powierzchnię docelową. Jest powszechnie stosowany w aplikacjach wymagających szybkiego i dokładnego umieszczania, takich jak montaż elektroniki lub mikrołączenie. Systemy natryskiwania wykorzystują piezoelektryczne lub pneumatyczne uruchamianie do tworzenia kontrolowanych kropel kleju.
- Dozowanie natryskowe: Dozowanie natryskowe to skuteczna technika pokrywania dużych powierzchni lub uzyskiwania równomiernego pokrycia. Polega na rozpyleniu kleju na drobne kropelki i skierowaniu ich na powierzchnię za pomocą ciśnienia powietrza lub automatycznego pistoletu natryskowego. Dozowanie natryskowe jest powszechnie stosowane w przemyśle motoryzacyjnym, drzewnym lub opakowaniowym, gdzie wymagane jest szybkie i równomierne pokrycie.
- Zrobotyzowane dozowanie: Zrobotyzowane systemy dozujące oferują precyzyjne i powtarzalne nakładanie kleju dzięki programowalnej automatyzacji. Są wyposażone w zaawansowane czujniki i zawory dozujące, które można zaprogramować tak, aby podążały za skomplikowanymi wzorami i konturami. Zrobotyzowane dozowanie zapewnia spójność i dokładność, dzięki czemu idealnie nadaje się do linii produkcyjnych o dużej objętości i złożonych procesów montażowych.
- Powlekanie filmowe/wirowe: Powlekanie filmowe lub wirowe to technika stosowana do nakładania jednolitej warstwy kleju na podłoże. Polega ona na użyciu obrotowego mechanizmu lub aplikatora do rozprowadzenia kleju w cienkiej, ciągłej warstwie. Ta metoda jest powszechnie stosowana w przemyśle motoryzacyjnym, lotniczym i budowlanym, gdzie kontrolowana grubość kleju ma kluczowe znaczenie dla optymalnej wydajności.
Wyzwania związane z aplikacją kleju wiążącego FPC
Aplikacja kleju łączącego FPC (Flexible Printed Circuit) stwarza kilka wyzwań, którym należy sprostać, aby zapewnić skuteczne łączenie i niezawodne działanie. Wyzwania te wynikają przede wszystkim z unikalnych właściwości i wymagań FPC. W tej odpowiedzi opiszę kilka kluczowych wyzwań napotykanych podczas aplikacji kleju łączącego FPC.
- Zgodność z podłożem: FPC są wykonane z elastycznych materiałów, takich jak poliimid, poliester lub cienka miedź, o innej charakterystyce powierzchni niż podłoża sztywne. Klej łączący musi być kompatybilny z materiałem FPC, aby zapewnić odpowiednią przyczepność bez powodowania rozwarstwień lub uszkodzeń podłoża.
- Przygotowanie powierzchni: Właściwe przygotowanie powierzchni ma kluczowe znaczenie dla klejenia. Powierzchnie FPC często zawierają pozostałości, oleje lub zanieczyszczenia, które mogą utrudniać przyczepność. Wyzwanie polega na wyborze właściwej metody czyszczenia lub obróbki powierzchni w celu usunięcia tych zanieczyszczeń bez narażania integralności ZKP.
- Kontrola grubości linii spoiwa: Osiągnięcie jednolitej grubości linii spoiwa ma zasadnicze znaczenie dla niezawodnego działania. Niespójna grubość kleju może prowadzić do zmian w przewodności elektrycznej, wytrzymałości mechanicznej i zarządzaniu temperaturą. Zapewnienie precyzyjnej kontroli nad grubością spoiny może być trudne ze względu na elastyczny charakter FPC.
- Zarządzanie temperaturą: FPC są często używane w aplikacjach, w których spodziewane są wahania temperatury. Klej używany do klejenia musi mieć dobrą przewodność cieplną, aby skutecznie rozpraszać ciepło, zapobiegając miejscowym gorącym punktom, które mogłyby uszkodzić FPC lub jego komponenty. Osiągnięcie optymalnego zarządzania termicznego bez uszczerbku dla elastyczności i właściwości elektrycznych FPC jest wyzwaniem.
- Utwardzanie kleju: Kleje wiążące FPC zazwyczaj wymagają procesów utwardzania, takich jak ciepło lub promieniowanie UV. Wyzwanie polegało na zapewnieniu jednolitego i pełnego utwardzenia na całej linii wiązania, zwłaszcza w złożonych lub gęsto upakowanych konstrukcjach FPC. Nieodpowiednie utwardzenie może skutkować silniejszym przyleganiem lub niepełnym wiązaniem, co prowadzi do problemów z niezawodnością.
- Elastyczność i trwałość: FPC są zaprojektowane tak, aby były elastyczne, a klej wiążący musi uwzględniać tę elastyczność bez narażania na szwank swojej integralności. Spoiwo musi wytrzymać wielokrotne zginanie, zginanie i rozciąganie bez pękania, rozwarstwiania się lub utraty przyczepności. Znalezienie wiązania, które może zachować zarówno elastyczność, jak i trwałość, może być trudne.
- Przewodność elektryczna: FPC często przenoszą sygnały elektryczne, co sprawia, że przewodność elektryczna jest krytycznym wymogiem. Klej łączący nie powinien wprowadzać dużej rezystancji, która mogłaby zakłócić działanie obwodu. Osiągnięcie dobrej przewodności elektrycznej w poprzek linii wiązania przy jednoczesnym zapewnieniu integralności mechanicznej stanowi wyzwanie.
- Automatyzacja procesu: Automatyzacja procesu nakładania kleju staje się niezbędna w branżach, w których łączenie FPC odbywa się na dużą skalę. Wyzwanie polega na opracowaniu zautomatyzowanych systemów, które mogą konsekwentnie nakładać klej z precyzją i wydajnością, uwzględniając różnice w rozmiarach, kształtach i projektach FPC.
Sprostanie tym wyzwaniom wymaga wszechstronnego zrozumienia materiałów FPC, klejów wiążących i specyficznych wymagań aplikacji. Często wiąże się to ze starannym doborem materiałów, optymalizacją procesu i testowaniem w celu zapewnienia kompatybilności, wydajności i niezawodności kleju w zastosowaniach związanych z łączeniem FPC.
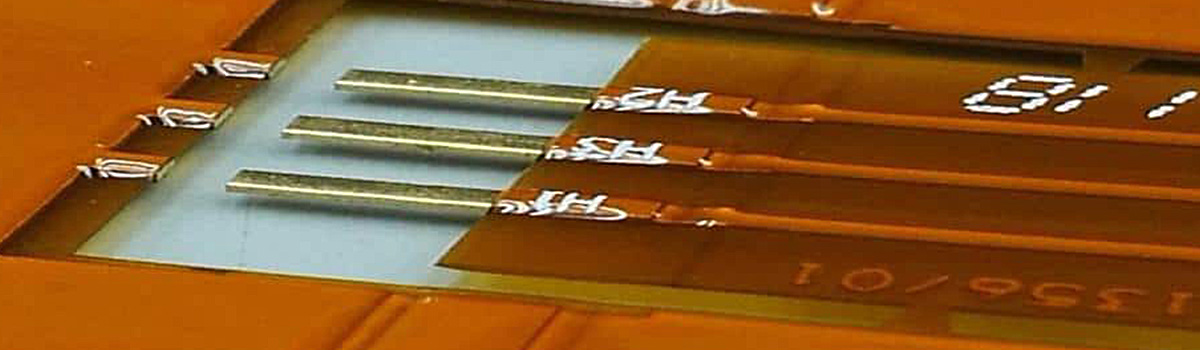
Testy niezawodności: ocena działania kleju
Testy niezawodności to kluczowy krok w ocenie wydajności klejów. Kleje są szeroko stosowane w różnych gałęziach przemysłu, w tym motoryzacyjnym, lotniczym, elektronicznym i budowlanym, do łączenia różnych materiałów. Niezawodność połączeń klejowych ma zasadnicze znaczenie dla zapewnienia bezpieczeństwa, trwałości i ogólnej wydajności produktu końcowego.
Testy niezawodności polegają na poddaniu wiązań klejowych różnym warunkom i obciążeniom, które symulują rzeczywiste środowiska i scenariusze użytkowania. Celem jest ocena zdolności kleju do utrzymania siły wiązania i integralności w czasie. Oto kilka kluczowych aspektów, które należy wziąć pod uwagę przy ocenie wydajności kleju w testach niezawodności:
- Siła wiązania: Początkowa siła wiązania kleju jest oceniana za pomocą standardowych testów, takich jak próby ścinania, odrywania lub rozciągania. Testy te mierzą siłę potrzebną do zerwania wiązania kleju. Zapewnia punkt odniesienia do porównania z siłą wiązania po wystawieniu na działanie różnych warunków.
- Ekspozycja środowiskowa: Kleje są często narażone na trudne warunki środowiskowe, takie jak ekstremalne temperatury, wilgotność, promieniowanie UV i chemikalia. Testy niezawodności polegają na poddaniu próbek kleju testom przyspieszonego starzenia, które symulują te warunki przez dłuższy czas. Pomaga to ocenić odporność kleju na degradację środowiskową i jego zdolność do utrzymania siły wiązania w niesprzyjających warunkach.
- Cykle termiczne: wahania temperatury mogą powodować rozszerzanie się i kurczenie materiałów, co może obciążać wiązania klejowe. Testy cykli termicznych obejmują poddawanie próbek kleju powtarzającym się cyklom temperaturowym, od niskich do wysokich ekstremów, w celu oceny odporności kleju na naprężenia termiczne i jego zdolności do utrzymania integralności wiązania.
- Naprężenia mechaniczne: Podczas eksploatacji spoiny klejowe mogą podlegać różnym rodzajom naprężeń mechanicznych, takich jak rozciąganie, ściskanie, ścinanie i wibracje. Testy niezawodności obejmują poddawanie próbek kleju naprężeniom mechanicznym poprzez cykliczne testy zmęczeniowe, udarowe lub zginanie. Testy te pomagają ocenić zdolność kleju do wytrzymania automatycznego obciążania bez uszkodzenia wiązania.
- Trwałość i starzenie: Oczekuje się, że spoiny klejowe będą miały długotrwałą trwałość i powinny być odporne na degradację w miarę upływu czasu. Testy niezawodności obejmują długoterminowe testy starzenia, które symulują przewidywaną żywotność produktu. Może to obejmować poddawanie próbek kleju długotrwałemu działaniu czynników środowiskowych, takich jak temperatura, wilgotność i promieniowanie UV, oraz okresowe ocenianie siły i integralności wiązania.
- Kompatybilność: Kleje muszą być kompatybilne z materiałami, które mają łączyć. Testy niezawodności obejmują ocenę kompatybilności kleju z różnymi podłożami, w tym metalami, tworzywami sztucznymi, kompozytami i innymi materiałami powszechnie stosowanymi w przemyśle. Testy kompatybilności oceniają siłę wiązania kleju, odporność na interakcje chemiczne i wszelkie niekorzystne skutki dla podłoża.
Testy niezawodności dostarczają cennych informacji na temat wydajności i ograniczeń klejów w różnych warunkach. Pomaga producentom wybrać najbardziej odpowiedni klej do ich zastosowania i zapewnia jego niezawodność i trwałość w rzeczywistych scenariuszach. Przeprowadzając rygorystyczne testy niezawodności, producenci mogą zmniejszyć ryzyko uszkodzenia wiązania kleju, poprawić jakość produktów i poprawić zadowolenie klientów.
Względy środowiskowe w kleju wiążącym FPC
Kleje łączące FPC (Flexible Printed Circuit) odgrywają kluczową rolę w montażu i niezawodności urządzeń elektronicznych. Ponieważ świadomość ekologiczna i zrównoważony rozwój stają się coraz ważniejsze, konieczne jest rozważenie wpływu tych klejów na środowisko. Oto kilka krytycznych kwestii środowiskowych związanych z klejami FPC:
- Toksyczność: Jednym z głównych problemów jest toksyczność kleju i jego składników. Kleje mogą zawierać szkodliwe chemikalia, takie jak lotne związki organiczne (LZO) lub niebezpieczne zanieczyszczenia powietrza (HAP). Substancje te mogą mieć szkodliwy wpływ na zdrowie ludzi i środowisko. Producenci powinni dążyć do zminimalizowania lub wyeliminowania toksycznych chemikaliów w swoich recepturach klejów.
- Emisje i jakość powietrza: Podczas procesów produkcji i aplikacji kleje FPC mogą uwalniać LZO i inne zanieczyszczenia powietrza do atmosfery. Emisje te przyczyniają się do zanieczyszczenia powietrza i mogą niekorzystnie wpływać na jakość powietrza. Świadomi ekologicznie producenci klejów dążą do zmniejszenia tych emisji poprzez formułowanie klejów o niskiej lub zerowej zawartości LZO.
- Zużycie energii: Produkcja klejów FPC wymaga energii, która często pochodzi ze źródeł nieodnawialnych. Aby zminimalizować wpływ na środowisko, producenci powinni wdrażać energooszczędne procesy i badać wykorzystanie odnawialnych źródeł energii.
- Generowanie odpadów: procesy aplikacji kleju mogą generować odpady, w tym nadmiar materiału klejącego, opakowania i materiały czyszczące. Należy przestrzegać właściwych praktyk gospodarowania odpadami, takich jak recykling lub ponowne wykorzystanie odpadów, gdy tylko jest to możliwe. Ponadto producenci powinni zbadać możliwości opracowania klejów o dłuższym okresie przydatności do spożycia, aby zmniejszyć ilość odpadów pochodzących z przeterminowanych lub nieużywanych produktów.
- Uwagi dotyczące wycofania z eksploatacji: Utylizacja urządzeń elektronicznych zawierających kleje FPC stanowi poważny problem środowiskowy. Kleje, które nie ulegają łatwo degradacji lub zawierają niebezpieczne składniki, mogą przyczyniać się do zanieczyszczenia, gdy urządzenia są wyrzucane. Producenci klejów powinni dążyć do opracowywania produktów przyjaznych dla środowiska, które są kompatybilne z procesami recyklingu lub utylizacji, takich jak kleje, które można łatwo oddzielić od płytek drukowanych podczas recyklingu.
- Zrównoważony rozwój i ekologiczne inicjatywy: Producenci klejów powinni uwzględniać zrównoważony rozwój w swoich praktykach biznesowych. Może to obejmować stosowanie surowców odnawialnych, wdrażanie przyjaznych dla środowiska procesów produkcyjnych oraz przestrzeganie uznanych norm i certyfikatów środowiskowych. Ponadto firmy mogą uczestniczyć w ekologicznych inicjatywach, takich jak programy zwrotu produktów lub partnerstwa z zakładami recyklingu.
- Ocena cyklu życia: Przeprowadzenie kompleksowej oceny cyklu życia (LCA) klejów FPC ma kluczowe znaczenie dla zrozumienia ich wpływu na środowisko od wydobycia surowców po utylizację. LCA pomagają zidentyfikować obszary, w których można wprowadzić ulepszenia, takie jak ograniczenie emisji gazów cieplarnianych, zminimalizowanie zużycia zasobów i zwiększenie możliwości recyklingu.
Trendy i innowacje w klejach FPC Bonding Adhesive
Kleje FPC (Flexible Printed Circuit) stale ewoluują, napędzane zapotrzebowaniem na wyższą wydajność, miniaturyzację i lepszą niezawodność urządzeń elektronicznych. Oto kilka godnych uwagi trendów i innowacji w klejach FPC:
- Miniaturyzacja i smukłość: w miarę jak urządzenia elektroniczne stają się coraz mniejsze i cieńsze, rośnie zapotrzebowanie na kleje łączące FPC, aby sprostać tym wymaganiom dotyczącym kształtu. Producenci opracowują ultracienkie i niskoprofilowe kleje, które zapewniają mocne wiązanie przy jednoczesnej minimalizacji całkowitej grubości zestawu.
- Odporność na wysokie temperatury: Wiele urządzeń elektronicznych, szczególnie w zastosowaniach motoryzacyjnych, lotniczych i przemysłowych, działa w środowiskach o wysokiej temperaturze. Kleje łączące FPC o zwiększonej odporności na ciepło są opracowywane, aby zapewnić niezawodne działanie w ekstremalnych warunkach temperaturowych, zapobiegając rozwarstwieniu lub uszkodzeniu wiązania.
- Utwardzanie pod niskim ciśnieniem: Tradycyjne procesy utwardzania kleju często wymagają wysokich temperatur lub długich czasów utwardzania, co może stanowić wyzwanie w przypadku elementów wrażliwych na ciepło lub delikatnych podłoży. Innowacje w technikach niskociśnieniowych, takie jak kleje utwardzane promieniami UV lub wilgocią, oferują delikatniejsze opcje utwardzania, umożliwiając kompatybilność z komponentami i podłożami wrażliwymi na temperaturę.
- Kleje przewodzące: Zapotrzebowanie na kleje FPC o przewodności elektrycznej rośnie w zastosowaniach wymagających połączeń elektrycznych między elementami obwodów. Kleje przewodzące eliminują potrzebę różnych procesów lutowania, umożliwiając szybszy montaż i zmniejszając ryzyko termicznego uszkodzenia wrażliwych komponentów.
- Ulepszona elastyczność i trwałość: Elastyczność i trwałość mają kluczowe znaczenie dla klejów FPC, aby wytrzymać zginanie, skręcanie i wibracje w elastycznych urządzeniach elektronicznych. Postępy w chemii polimerów i technikach formułowania skutkują klejami o ulepszonej elastyczności, wydłużeniu i odporności na naprężenia mechaniczne, zapewniając niezawodne wiązanie w dynamicznych środowiskach.
- Przyjazność dla środowiska: Względy środowiskowe, w tym stosowanie zrównoważonych surowców i redukcja substancji toksycznych, stają się coraz bardziej widoczne w opracowywaniu klejów. Producenci badają materiały pochodzenia biologicznego i odnawialne jako alternatywę dla składników ropopochodnych. Ponadto opracowywane są przyjazne dla środowiska procesy produkcyjne i receptury klejów nadające się do recyklingu, aby zminimalizować wpływ na środowisko.
- Ulepszone dozowanie i aplikacja: Wydajna i precyzyjna aplikacja kleju ma kluczowe znaczenie dla uzyskania spójnych i niezawodnych połączeń. Innowacje w technologiach dozowania, takie jak zautomatyzowane systemy dozowania i metody natryskiwania, pozwalają na kontrolowane i dokładne nakładanie klejów, nawet w złożonych projektach FPC z delikatnymi składnikami podziałki.
- Technologia folii samoprzylepnych: Folie samoprzylepne zyskują na popularności w klejeniu FPC ze względu na łatwość obsługi i precyzyjne umieszczanie. Te wstępnie uformowane folie oferują jednolitą grubość kleju, doskonałe właściwości zwilżające i uproszczone procesy montażu. Producenci stale ulepszają formuły folii klejących, aby poprawić ich skuteczność wiązania i kompatybilność z różnymi podłożami.
- Zwiększona niezawodność: Aby zapewnić długotrwałą niezawodność, opracowywane są kleje łączące FPC o zwiększonej odporności na czynniki takie jak wilgoć, chemikalia i starzenie. Kleje te przechodzą rygorystyczne testy w celu oceny ich działania w trudnych warunkach środowiskowych, zapewniając spójną funkcjonalność i integralność wiązania przez cały okres użytkowania produktu.
- Dostosowanie i rozwiązania specyficzne dla aplikacji: Kleje łączące FPC są dostosowywane do specyficznych wymagań różnych zastosowań, takich jak motoryzacja, elektronika użytkowa, urządzenia medyczne i technologia noszenia. Producenci ściśle współpracują z projektantami urządzeń i producentami w celu opracowania niestandardowych rozwiązań w zakresie klejów, które są odpowiedzią na wyjątkowe wyzwania i wymagania dotyczące wydajności każdego zastosowania.
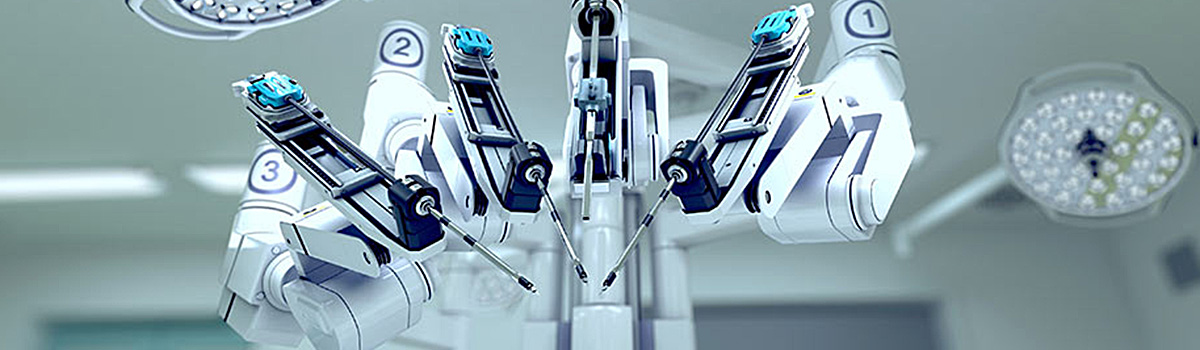
Obszary zastosowań: elektronika użytkowa, motoryzacja, urządzenia medyczne i inne
Elektroniki użytkowej: Elektronika użytkowa obejmuje szeroką gamę produktów przeznaczonych do użytku osobistego i rozrywki. Należą do nich smartfony, tablety, laptopy, konsole do gier, inteligentne telewizory, inteligentne urządzenia domowe, urządzenia do noszenia i nie tylko. Zastosowanie elektroniki użytkowej zrewolucjonizowało sposób, w jaki ludzie komunikują się, pracują i bawią. Postęp technologiczny sprawił, że elektronika użytkowa stała się mocniejsza, bardziej kompaktowa i przystępna cenowo, zapewniając użytkownikom bezproblemową łączność, wciągające wrażenia i wygodę.
Automobilowy: W ostatnich latach przemysł motoryzacyjny odnotował znaczny postęp, głównie dzięki integracji technologii. Od pojazdów elektrycznych (EV) po autonomiczne systemy jazdy, aplikacje motoryzacyjne zmieniły sposób, w jaki podróżujemy. Samochody elektryczne zyskują na popularności ze względu na ich ekologiczny charakter i redukcję emisji dwutlenku węgla. Ponadto producenci samochodów wprowadzają innowacyjne funkcje, takie jak zaawansowane systemy wspomagania kierowcy (ADAS), łączność, systemy informacyjno-rozrywkowe i telematyka, aby poprawić wrażenia z jazdy, poprawić bezpieczeństwo i umożliwić efektywne zarządzanie pojazdem.
Urządzenia medyczne: Urządzenia medyczne odgrywają kluczową rolę w diagnozowaniu, monitorowaniu i leczeniu różnych schorzeń. Obejmują one zarówno proste urządzenia, takie jak termometry i ciśnieniomierze, jak i zaawansowane urządzenia, takie jak aparaty do rezonansu magnetycznego i zrobotyzowane systemy chirurgiczne. Urządzenia medyczne umożliwiają pracownikom służby zdrowia stawianie trafnych diagnoz, przeprowadzanie procedur minimalnie inwazyjnych i zdalne monitorowanie stanu zdrowia pacjentów. Zrewolucjonizowały branżę opieki zdrowotnej, poprawiając wyniki pacjentów, zmniejszając liczbę pobytów w szpitalu i poprawiając ogólną jakość opieki.
Internet rzeczy (IoT): Internet rzeczy (IoT) to sieć połączonych ze sobą urządzeń z wbudowanymi czujnikami, oprogramowaniem i możliwościami łączności. Umożliwia wymianę danych i komunikację między urządzeniami, prowadząc do automatyzacji, analizy danych i lepszego podejmowania decyzji. IoT ma zastosowanie w różnych branżach, w tym w opiece zdrowotnej, rolnictwie, produkcji i energetyce. W opiece zdrowotnej urządzenia IoT mogą monitorować parametry życiowe pacjenta, śledzić przestrzeganie zaleceń lekarskich i umożliwiać zdalne monitorowanie pacjenta. Urządzenia IoT mogą optymalizować nawadnianie, monitorować warunki glebowe i usprawniać zarządzanie uprawami w rolnictwie. IoT ma potencjał, by zrewolucjonizować branże, czyniąc je bardziej wydajnymi, zrównoważonymi i opartymi na danych.
Automatyka przemysłowa: Automatyka przemysłowa polega na wykorzystaniu technologii i systemów sterowania do automatyzacji procesów i zadań przemysłowych. Obejmuje to robotykę, systemy widzenia maszynowego, czujniki i programowalne sterowniki logiczne (PLC). Automatyka przemysłowa zwiększa produktywność, poprawia bezpieczeństwo, obniża koszty operacyjne i znajduje zastosowanie w produkcji, logistyce, energetyce i innych sektorach. Dzięki integracji sztucznej inteligencji (AI) i uczenia maszynowego (ML) automatyzacja przemysłowa może optymalizować procesy, wykrywać anomalie i umożliwiać konserwację zapobiegawczą, poprawiając wydajność i skracając przestoje.
Perspektywy i możliwości na przyszłość
Klej łączący FPC (Flexible Printed Circuit) jest kluczowym elementem w produkcji urządzeń elektronicznych. Ma to kluczowe znaczenie dla zapewnienia niezawodnych i wytrzymałych połączeń między obwodami elastycznymi a innymi częściami. Spoglądając w przyszłość, warto rozważyć kilka perspektyw i możliwości związanych z klejem FPC.
- Postępy w elastycznej elektronice: Dziedzina elastycznej elektroniki szybko się rozwija, wraz z rosnącym zapotrzebowaniem na elastyczne wyświetlacze, urządzenia do noszenia i inteligentne tekstylia. Kleje wiążące FPC będą nadal poszukiwane, aby umożliwić montaż i łączenie elastycznych obwodów w tych innowacyjnych zastosowaniach.
- Miniaturyzacja i smuklejsze urządzenia: Ponieważ elektronika użytkowa staje się coraz bardziej kompaktowa i smukła, cieńsze i bardziej elastyczne rozwiązania interkonektowe mają nadrzędne znaczenie. Kleje wiążące FPC mogą ułatwić montaż ultracienkich elastycznych obwodów, tworząc smukłe i lżejsze urządzenia.
- Zwiększona wydajność klejenia: Producenci nieustannie poszukują rozwiązań klejących, które zapewniają doskonałe właściwości wiążące, takie jak wysoka wytrzymałość na ścinanie, doskonała przewodność elektryczna i stabilność termiczna. Przyszłe kleje wiążące FPC będą prawdopodobnie zawierać zaawansowane materiały i formuły, aby sprostać tym wymagającym wymaganiom.
- Integracja z zaawansowanymi procesami produkcyjnymi: Nowe technologie produkcyjne, takie jak drukowanie 3D, przetwarzanie typu „roll-to-roll” i integracja hybrydowa, otwierają nowe możliwości wytwarzania elastycznych obwodów. Kleje wiążące FPC muszą dostosowywać się i być kompatybilne z tymi procesami produkcyjnymi, zapewniając optymalną przyczepność i niezawodność.
- Elastyczna elektronika hybrydowa (FHE): FHE łączy tradycyjną sztywną elektronikę z elastycznymi komponentami, tworząc urządzenia o unikalnych rozmiarach i funkcjonalnościach. Kleje wiążące FPC odegrają kluczową rolę w montażu tych systemów hybrydowych, płynnie łącząc elastyczne i sztywne elementy.
- Zrównoważony rozwój i względy środowiskowe: Rosnący nacisk na zrównoważony rozwój i odpowiedzialność za środowisko stanowi okazję do opracowania przyjaznych dla środowiska klejów FPC. Przyszłe preparaty mogą zawierać materiały odnawialne lub nadające się do recyklingu, zmniejszając wpływ odpadów elektronicznych na środowisko.
- Integracja inteligentnych funkcji: wraz z rozwojem Internetu rzeczy (IoT) i połączonych ze sobą urządzeń, kleje łączące FPC mogą potencjalnie zawierać inteligentne funkcje, takie jak wbudowane czujniki, możliwości samoleczenia lub właściwości zarządzania termicznego. Te postępy poprawiłyby funkcjonalność i niezawodność urządzeń elektronicznych.
- Zastosowania w medycynie i opiece zdrowotnej: Dziedzina medyczna przeżywa gwałtowny wzrost liczby urządzeń do noszenia, wszczepialnych czujników i inteligentnych technologii opieki zdrowotnej. Kleje łączące FPC, które są biokompatybilne, sterylizowalne i zdolne do przylegania do różnych podłoży, znajdą znaczące zastosowania w tej dziedzinie.
- Przemysł motoryzacyjny i lotniczy: Sektory motoryzacyjny i lotniczy coraz częściej stosują elastyczne obwody ze względu na ich lekkość i oszczędność miejsca. Kleje łączące FPC, które mogą wytrzymać ekstremalne temperatury, wibracje i naprężenia mechaniczne, będą bardzo poszukiwane w tych wymagających środowiskach.
- Badania i rozwój: Dalsze prace badawczo-rozwojowe w zakresie klejów FPC doprowadzą do dalszych postępów. Innowacje w chemii klejów, technikach produkcji i optymalizacji procesów popchną branżę do przodu, umożliwiając nowe zastosowania i lepszą wydajność.
Znaczenie współpracy w rozwoju technologii klejenia FPC
Współpraca ma kluczowe znaczenie dla rozwoju technologii klejenia FPC (Flexible Printed Circuit). Umożliwia wymianę wiedzy, zasobów i ekspertyz między różnymi zainteresowanymi stronami, co prowadzi do przyspieszenia innowacji i postępu. Oto kluczowe powody podkreślające znaczenie współpracy w rozwoju technologii klejenia FPC:
- Interdyscyplinarna wiedza specjalistyczna: technologia klejenia FPC obejmuje różne dziedziny, w tym materiałoznawstwo, chemię, produkcję elektroniki i inżynierię. Współpraca łączy ekspertów z tych różnych dziedzin, wspierając interdyscyplinarne podejście do rozwiązywania problemów. Łącząc swoją wiedzę i perspektywy, naukowcy i specjaliści z branży mogą skuteczniej stawiać czoła złożonym wyzwaniom i opracowywać nowatorskie rozwiązania.
- Dzielenie się wiedzą: współpraca ułatwia dzielenie się informacjami, wynikami badań i najlepszymi praktykami między różnymi podmiotami. Producenci, dostawcy, badacze i instytucje akademickie mogą współpracować w celu rozpowszechniania cennych spostrzeżeń i wiedzy technicznej na temat technologii klejenia FPC. Ta wspólna wiedza pomaga uniknąć zbędnych wysiłków, promuje standaryzację i przyspiesza ogólny rozwój.
- Dostęp do zasobów: Wspólne wysiłki umożliwiają dostęp do szerszego zakresu zasobów, w tym funduszy, sprzętu, obiektów i materiałów. Współpraca z organizacjami, instytutami badawczymi lub agencjami rządowymi może zapewnić dostęp do specjalistycznych zasobów, które mogą nie być dostępne indywidualnie. Dostęp ten umożliwia szersze eksperymentowanie, testowanie i tworzenie prototypów, co prowadzi do ulepszonych receptur klejów FPC i procesów produkcyjnych.
- Przyspieszona innowacja: Współpraca sprzyja środowisku otwartej innowacji i kreatywności. Dzięki połączeniu różnych perspektyw i wiedzy specjalistycznej mogą pojawić się nowe pomysły i koncepcje, przesuwając granice technologii klejenia FPC. Projekty oparte na współpracy mogą również wykorzystać mocne strony każdego z partnerów, łącząc ich unikalne możliwości i zasoby w celu opracowania innowacyjnych rozwiązań w przyspieszonym tempie.
- Wgląd w rynek i trendy branżowe: Współpraca z partnerami branżowymi i użytkownikami końcowymi zapewnia cenny wgląd w wymagania rynku, pojawiające się trendy i wymagania klientów. To zrozumienie pomaga dostosować rozwój technologii klejenia FPC do zmieniających się potrzeb przemysłu. Wspólne wysiłki pozwalają na wczesną informację zwrotną i weryfikację, zapewniając, że opracowane rozwiązania są praktyczne, odpowiednie i opłacalne komercyjnie.
- Zapewnienie jakości i standaryzacja: Współpraca ułatwia ustanowienie środków zapewnienia jakości i standardów branżowych dla technologii klejenia FPC. Współpraca z organizacjami normalizacyjnymi i organami regulacyjnymi gwarantuje, że opracowane kleje spełniają wymagania dotyczące bezpieczeństwa, niezawodności i wydajności. Współpraca umożliwia również udostępnianie metodologii testowania i protokołów walidacji, co prowadzi do bardziej spójnych i ustandaryzowanych procesów łączenia.
- Walidacja i zastosowanie w świecie rzeczywistym: Współpraca z użytkownikami końcowymi, producentami i integratorami systemów umożliwia potwierdzenie technologii klejenia FPC w rzeczywistych zastosowaniach. Dzięki współpracy producenci klejów mogą uzyskać cenne informacje zwrotne dotyczące wydajności, użyteczności i możliwości produkcyjnych. Ta pętla sprzężenia zwrotnego pomaga udoskonalić i udoskonalić receptury klejów, zapewniając ich przydatność do różnych zastosowań i środowisk.
- Ograniczanie ryzyka: Współpraca rozkłada ryzyko związane z pracami badawczo-rozwojowymi. Partnerzy mogą wspólnie stawiać czoła wyzwaniom i ograniczać indywidualne ryzyko, łącząc zasoby i wiedzę. Współpraca umożliwia również dzielenie się własnością intelektualną i prawami patentowymi, tworząc bardziej sprzyjające współpracy i mniej konkurencyjne środowisko.
Wnioski
Klej wiążący FPC ma kluczowe znaczenie dla elastyczności i niezawodności urządzeń elektronicznych. Zdolność tych klejów do zapewnienia silnych właściwości wiążących, izolacji elektrycznej i ochrony przed czynnikami środowiskowymi przy jednoczesnym zapewnieniu elastyczności i trwałości płyt FPC ma kluczowe znaczenie w produkcji i montażu różnych urządzeń elektronicznych. Wraz z rozwojem technologii opracowywanie innowacyjnych rozwiązań w zakresie klejów oraz współpraca między producentami, badaczami i użytkownikami końcowymi będzie miała kluczowe znaczenie dla sprostania rosnącym wymaganiom i wyzwaniom przemysłu elektronicznego. Wykorzystując potencjał kleju FPC, możemy utorować drogę jeszcze bardziej elastycznym, trwałym i niezawodnym urządzeniom elektronicznym, które zasilają nasz współczesny świat.