Powłoki ochronne dla elektroniki
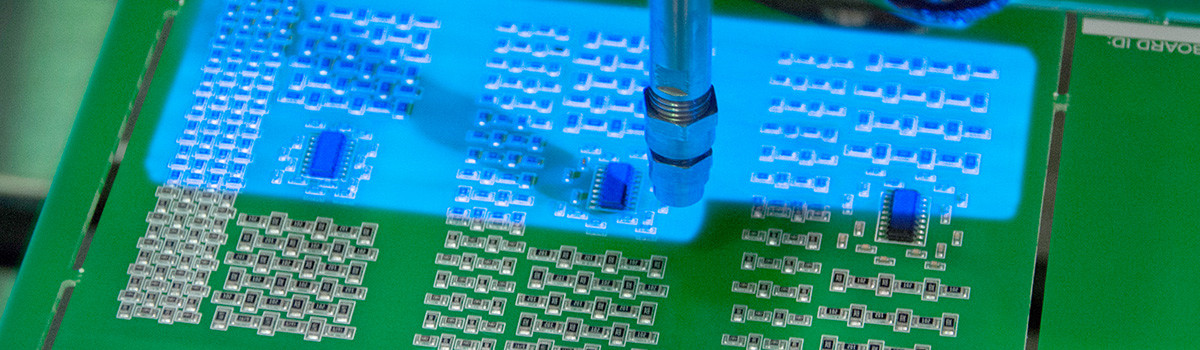
W dzisiejszym świecie urządzenia elektroniczne są integralną częścią naszego codziennego życia. Ponieważ urządzenia elektroniczne stają się coraz bardziej złożone i miniaturyzowane, potrzeba ochrony przed czynnikami środowiskowymi, takimi jak wilgoć, kurz i chemikalia, staje się coraz ważniejsza. Tutaj z pomocą przychodzą powłoki konforemne. Powłoki konforemne to specjalnie opracowane materiały, które chronią komponenty elektroniczne przed czynnikami zewnętrznymi, które mogą negatywnie wpłynąć na ich wydajność i funkcjonalność. W tym artykule zbadamy korzyści i znaczenie powłok ochronnych dla elektroniki.
Co to są powłoki ochronne dla elektroniki?
Powłoki ochronne to specjalistyczne powłoki ochronne stosowane w przemyśle elektronicznym do zabezpieczania elementów elektronicznych i płytek drukowanych przed czynnikami środowiskowymi, takimi jak wilgoć, kurz, chemikalia i ekstremalne temperatury. Powłoki te są nakładane cienką, jednolitą warstwą na powierzchnię elektroniki, dopasowując się do konturów komponentów, aby zapewnić pełne pokrycie i ochronę.
Podstawowym celem powłok ochronnych jest zapobieganie uszkodzeniom lub awariom urządzeń elektronicznych spowodowanych przez elementy zewnętrzne. Na przykład wilgoć i wilgotność mogą powodować korozję i zwarcia, podczas gdy kurz i zanieczyszczenia mogą pogarszać działanie wrażliwych komponentów. Powłoka ochronna chroni zespół elektroniczny przed tymi zagrożeniami, zapewniając jego niezawodność i długowieczność.
Powłoki ochronne są zazwyczaj wykonane z różnych preparatów chemicznych, w tym akryli, silikonów, uretanów i epoksydów. Każdy rodzaj powłoki oferuje inne właściwości i zalety. Powłoki akrylowe są szeroko stosowane ze względu na ich wszechstronność, łatwość aplikacji i opłacalność. Zapewniają dobrą odporność na wilgoć i są stosunkowo łatwe do usunięcia i ponownego nałożenia w razie potrzeby. Silikony są znane ze swojej doskonałej elastyczności, stabilności termicznej i odporności na wysokie temperatury. Powłoki uretanowe zapewniają wyjątkową odporność chemiczną oraz ochronę przed rozpuszczalnikami i paliwami. Epoksydy zapewniają doskonałą twardość i trwałość, dzięki czemu nadają się do trudnych warunków.
Powłoki ochronne wymagają szczególnej uwagi, aby zapewnić odpowiednie pokrycie i przyczepność. Różne techniki obejmują szczotkowanie, natryskiwanie, zanurzanie i selektywne powlekanie. Można zastosować różne metody w zależności od konkretnych wymagań i złożoności zespołu. Niektóre powłoki są nakładane ręcznie, podczas gdy inne są wykonywane za pomocą zautomatyzowanych procesów, takich jak zrobotyzowane natryskiwanie lub systemy powlekania zanurzeniowego.
Po nałożeniu powłoka konforemna tworzy barierę ochronną, która otacza elementy elektroniczne bez zakłócania ich funkcjonalności. Tworzy warstwę ochronną, która przylega do powierzchni i zachowuje swoje właściwości ochronne w czasie. Powłoki są zwykle przezroczyste lub półprzezroczyste, co pozwala na wizualną kontrolę montażu.
Oprócz ochrony przed czynnikami środowiskowymi, powłoki konforemne oferują również inne korzyści. Mogą zapewnić izolację elektryczną, zapobiegając upływowi prądu i zwarciom. Warstwy mogą również zwiększyć odporność zespołu na wibracje i naprężenia mechaniczne, zmniejszając ryzyko uszkodzenia podczas transportu lub eksploatacji. Ponadto mogą zapewniać ochronę przed grzybami, pleśnią i innymi zanieczyszczeniami, które mogą zagrozić wydajności urządzeń elektronicznych.
Znaczenie powłok ochronnych dla urządzeń elektronicznych
Powłoki konforemne odgrywają kluczową rolę w zwiększaniu niezawodności i trwałości urządzeń elektronicznych i oferują szereg istotnych korzyści dla zapewnienia optymalnej wydajności i trwałości. Oto kilka kluczowych powodów, dla których powłoki konforemne są niezbędne dla urządzeń elektronicznych:
- Ochrona przed wilgocią i wilgocią: Jednym z głównych celów powłok ochronnych jest ochrona elementów elektronicznych przed wilgocią i wilgocią. Woda może prowadzić do korozji, utleniania i tworzenia ścieżek przewodzących, co prowadzi do zwarć i wadliwego działania urządzeń. Powłoki ochronne działają jak bariera, zapobiegając przedostawaniu się wilgoci do wrażliwych elementów i zmniejszając ryzyko uszkodzenia.
- Zapobieganie gromadzeniu się kurzu i zanieczyszczeń: Elektronika jest często narażona na kurz, brud i zanieczyszczenia unoszące się w powietrzu. Cząsteczki te mogą osadzać się na płytkach drukowanych i komponentach, prowadząc do problemów z izolacją, zwiększonego wytwarzania ciepła i potencjalnych zwarć. Powłoki ochronne tworzą warstwę ochronną, która hamuje gromadzenie się kurzu i zanieczyszczeń, utrzymując czystość i wydajność elektroniki.
- Odporność chemiczna: Wiele powłok ochronnych jest odpornych na różne chemikalia, w tym rozpuszczalniki, paliwa, kwasy i zasady. Jest to szczególnie ważne w środowiskach, w których urządzenia elektroniczne mogą mieć kontakt z substancjami żrącymi. Powłoki działają jak tarcza, zapobiegając reakcjom chemicznym i zapewniając długowieczność komponentów.
- Zabezpieczenie termiczne: Urządzenia elektroniczne wytwarzają ciepło podczas pracy, a nadmierne ciepło może obniżyć wydajność i niezawodność komponentów. Powłoki ochronne mogą stanowić barierę termiczną, rozpraszając ciepło i zmniejszając ryzyko przegrzania. Specyficzne warstwy, takie jak te na bazie silikonu, znane są ze swojej doskonałej stabilności termicznej i wytrzymują wysokie temperatury bez uszczerbku dla swoich właściwości ochronnych.
- Izolacja elektryczna: Powłoki ochronne mogą zapewniać izolację elektryczną, zapobiegając upływowi prądu i zwarciom. Pomagają zachować pożądaną charakterystykę elektryczną komponentów i zmniejszają ryzyko awarii elektrycznych spowodowanych czynnikami środowiskowymi lub zanieczyszczeniami.
- Ochrona mechaniczna: Elektronika może być narażona na obciążenia mechaniczne, takie jak wibracje, wstrząsy lub uderzenia. Powłoki ochronne zwiększają wytrzymałość mechaniczną urządzeń elektronicznych, zapewniając dodatkową warstwę ochronną. Pomagają pochłaniać wibracje i siły uderzenia, zmniejszając ryzyko uszkodzenia delikatnych elementów i zapewniając niezawodne działanie.
- Odporność na warunki środowiskowe: Powłoki ochronne umożliwiają urządzeniom elektronicznym odporność na różne warunki środowiskowe. Mogą wytrzymać ekstremalne temperatury, promieniowanie UV, mgłę solną i inne trudne elementy. Jest to szczególnie ważne w przypadku urządzeń używanych na zewnątrz lub w zastosowaniach przemysłowych, gdzie mogą być narażone na trudne warunki otoczenia.
Korzyści ze stosowania powłok ochronnych
Stosowanie powłok ochronnych w urządzeniach elektronicznych oferuje kilka korzyści, które przyczyniają się do ich ogólnej niezawodności i trwałości. Oto kilka kluczowych zalet stosowania powłok ochronnych:
- Ochrona środowiska: Powłoki ochronne zapewniają barierę ochronną, która chroni elementy elektroniczne przed czynnikami środowiskowymi, takimi jak wilgoć, kurz, brud i chemikalia. Zapobiegają wnikaniu wody, która może powodować korozję i zwarcia, a także chronią przed gromadzeniem się kurzu i zanieczyszczeń, które mogą pogorszyć wydajność. Ta ochrona środowiska przedłuża żywotność urządzeń elektronicznych.
- Zwiększona niezawodność: chroniąc przed zagrożeniami środowiskowymi, powłoki ochronne zwiększają niezawodność urządzeń elektronicznych. Minimalizują ryzyko awarii spowodowanych problemami związanymi z wilgocią, takimi jak uszkodzenie elementów spowodowane korozją lub migracja elektrochemiczna. Ponadto powłoki chronią przed kurzem i zanieczyszczeniami, które mogą powodować zwarcia elektryczne lub uszkodzenia izolacji, zapewniając stałą i niezawodną wydajność.
- Izolacja elektryczna: Powłoki ochronne zapewniają właściwości izolacji elektrycznej, zapobiegając wyciekom prądu i zwarciom. Pomagają utrzymać pożądane właściwości elektryczne komponentów, zmniejszając możliwość awarii lub awarii elektrycznych spowodowanych zanieczyszczeniem lub wchłanianiem wilgoci. Izolacja elektryczna pomaga również w spełnieniu wymagań bezpieczeństwa i przepisów.
- Zarządzanie termiczne: Niektóre powłoki konforemne mają właściwości zarządzania termicznego, co pozwala im rozpraszać ciepło wytwarzane przez elementy elektroniczne. Ta ochrona termiczna pomaga zapobiegać przegrzaniu, które może obniżyć wydajność i skrócić żywotność wrażliwych urządzeń. Dzięki efektywnemu zarządzaniu temperaturą powłoki ochronne przyczyniają się do ogólnej niezawodności elektroniki.
- Odporność chemiczna: Wiele powłok ochronnych wykazuje doskonałą odporność chemiczną. Stanowią barierę przed substancjami korozyjnymi, rozpuszczalnikami, paliwami i innymi chemikaliami, które mogą uszkodzić elementy elektroniczne. Ta odporność chemiczna zapobiega reakcjom chemicznym, degradacji materiału i potencjalnym awariom spowodowanym narażeniem na trudne warunki środowiskowe lub kontakt z chemikaliami.
- Ochrona przed wibracjami i wstrząsami: Powłoki ochronne zapewniają ochronę mechaniczną poprzez pochłanianie wibracji i zmniejszanie wpływu wstrząsów i naprężeń mechanicznych. Jest to szczególnie korzystne w przypadku urządzeń elektronicznych narażonych na transport lub trudne warunki eksploatacji. Powłoki ochronne pomagają zapobiegać uszkodzeniom delikatnych komponentów, połączeń lutowanych i połączeń, minimalizując skutki wibracji i wstrząsów.
- Łatwość kontroli i naprawy: Powłoki ochronne są często przezroczyste lub półprzezroczyste, co pozwala na wizualną kontrolę leżących pod nimi elementów. Ułatwia to wykrywanie potencjalnych problemów, takich jak wady połączeń lutowanych, uszkodzenia komponentów lub zanieczyszczenie ciałami obcymi. Co więcej, powłoki konforemne można usunąć i ponownie nałożyć, jeśli wymagane są naprawy lub modyfikacje, co upraszcza konserwację.
Jak działają powłoki ochronne?
Powłoki ochronne tworzą barierę ochronną na powierzchni elementów elektronicznych i płytek drukowanych. Powłoki te są zwykle nakładane jako cienkie, jednolite warstwy, które dopasowują się do konturów urządzeń, zapewniając pełne pokrycie i ochronę. Powłoki przylegają do powierzchni i tworzą ciągłą warstwę, która chroni przed czynnikami środowiskowymi i potencjalnymi zanieczyszczeniami.
Nakładanie powłok ochronnych obejmuje kilka etapów:
- Przygotowanie powierzchni: Przed nałożeniem powłoki ochronnej należy odpowiednio przygotować powierzchnię zespołu elektronicznego. Zwykle obejmuje to czyszczenie i usuwanie zanieczyszczeń, takich jak kurz, oleje i pozostałości. Powłokę można czyścić rozpuszczalnikami, myjką ultradźwiękową lub innymi odpowiednimi metodami, aby zapewnić czyste i gładkie podłoże do przylegania powłoki.
- Wybór materiału powłokowego: Dostępne są różne rodzaje powłok ochronnych, takie jak akryle, silikony, uretany i żywice epoksydowe, z których każda ma swoje właściwości i zalety. Wybór materiału powłokowego zależy od czynników, takich jak warunki środowiskowe, pożądany poziom ochrony, wymagania dotyczące izolacji elektrycznej i szczególne względy zastosowania.
- Metoda aplikacji: Powłoki ochronne można nakładać różnymi metodami, w tym pędzlem, natryskiem, zanurzeniem i powlekaniem selektywnym. Wybór metody aplikacji zależy od takich czynników, jak złożoność montażu, rodzaj materiału powłokowego oraz pożądany poziom precyzji. Ręczne metody aplikacji są odpowiednie do produkcji na mniejszą skalę lub do określonych obszarów wymagających ukierunkowanego powlekania. W produkcji na większą skalę często stosuje się zautomatyzowane procesy, takie jak zrobotyzowane natryskiwanie lub systemy powlekania zanurzeniowego, aby zapewnić spójne i jednolite pokrycie powłoką.
- Utwardzanie i suszenie: Po nałożeniu powłoki należy ją poddać procesowi utwardzania lub suszenia. Proces ten umożliwia zestalenie się materiału powłokowego i utworzenie filmu ochronnego. Czas i warunki utwardzania zależą od konkretnego materiału powłokowego i zaleceń producenta. Metody utwardzania mogą obejmować suszenie powietrzem, utwardzanie termiczne w piecach lub wystawianie niektórych rodzajów powłok na działanie światła UV.
Po nałożeniu i utwardzeniu powłoka ochronna tworzy barierę ochronną otaczającą elementy elektroniczne. Warstwa stanowi barierę przed wilgocią, kurzem, chemikaliami i innymi czynnikami środowiskowymi, które mogą uszkodzić lub zdegradować komponenty. Pomaga zapobiegać korozji, zwarciom elektrycznym i uszkodzeniom izolacji, zapewniając niezawodność i długowieczność urządzeń elektronicznych.
Powłoki konforemne zachowują swoje właściwości ochronne przez długi czas, zapewniając ciągłą ochronę podzespołów elektronicznych. W przypadku naprawy lub modyfikacji warstwę można wybiórczo usunąć i ponownie nałożyć, co pozwala na konserwację lub wymianę komponentów bez uszczerbku dla ogólnej ochrony zapewnianej przez powłokę.
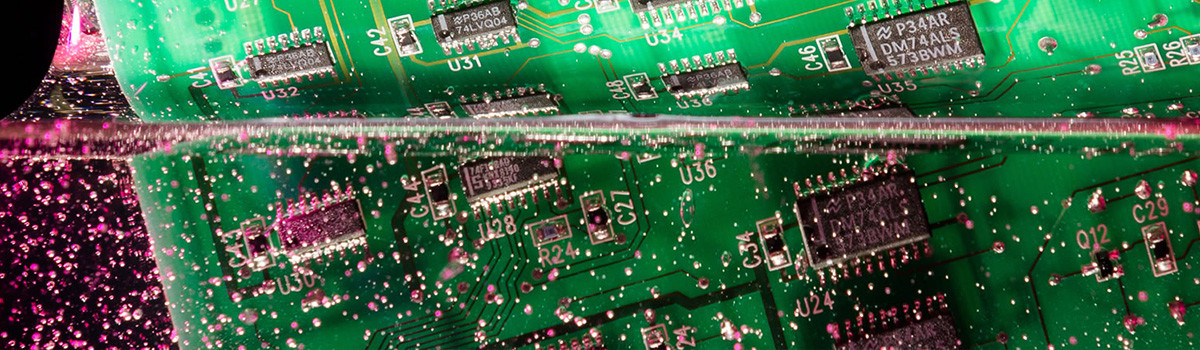
Rodzaje powłok ochronnych
Dostępnych jest kilka rodzajów powłok ochronnych, z których każda ma swoje właściwości, zalety i zastosowania. Wybór rodzaju powłoki zależy od takich czynników, jak specyficzne wymagania zespołu elektronicznego, warunki środowiskowe, pożądany poziom ochrony oraz procesy produkcyjne. Oto kilka powszechnie stosowanych rodzajów powłok ochronnych:
- Akrylowe powłoki konforemne: Powłoki akrylowe są jednym z najczęściej stosowanych typów ze względu na ich wszechstronność i opłacalność. Zapewniają dobrą odporność na wilgoć, izolację elektryczną i ochronę przed czynnikami środowiskowymi. Powłoki akrylowe są łatwe w aplikacji, można je usuwać i ponownie obrabiać. Nadają się do różnych zastosowań i zapewniają dobrą ochronę ogólnego zastosowania.
- Powłoki silikonowe: Powłoki silikonowe mają doskonałą elastyczność, stabilność termiczną i odporność na wysokie temperatury. Mogą wytrzymać ekstremalne wahania temperatury bez utraty swoich właściwości ochronnych. Powłoki silikonowe zapewniają doskonałą odporność na wilgoć i izolację elektryczną. Są często używane w zastosowaniach, w których wysoka stabilność termiczna i elastyczność mają kluczowe znaczenie, na przykład w motoryzacji, przemyśle lotniczym i zewnętrznych urządzeniach elektronicznych.
- Powłoki uretanowe: Powłoki uretanowe zapewniają wyjątkową odporność chemiczną, dzięki czemu nadają się do zastosowań, w których problemem jest narażenie na rozpuszczalniki, paliwa lub inne żrące chemikalia. Zapewniają dobrą ochronę przed wilgocią, izolację elektryczną i wytrzymałość mechaniczną. Powłoki uretanowe są często stosowane w wymagających środowiskach, takich jak zastosowania motoryzacyjne, przemysłowe i wojskowe.
- Powłoki epoksydowe: Powłoki epoksydowe są znane ze swojej doskonałej twardości i trwałości. Zapewniają solidną ochronę mechaniczną oraz odporność na ścieranie i uderzenia. Powłoki epoksydowe zapewniają dobrą odporność chemiczną i ochronę przed wilgocią. Są powszechnie stosowane w aplikacjach wymagających solidnej ochrony i wytrzymałości mechanicznej, takich jak przemysłowe systemy sterowania, wzmocniona elektronika i środowiska o dużym obciążeniu.
- Powłoki konforemne Parylenu: Parylen jest unikalnym rodzajem powłoki konforemnej osadzanej w postaci pary i tworzy cienką, pozbawioną dziurek warstwę polimeru. Warstwy parylenu zapewniają doskonałe właściwości barierowe dla wilgoci, izolację elektryczną, odporność chemiczną i biokompatybilność. Oferują wysoki poziom ochrony i są dostosowane do złożonych geometrii. Powłoki parylenowe są powszechnie stosowane w urządzeniach medycznych, przemyśle lotniczym i wrażliwych zastosowaniach elektronicznych.
- Powłoki konformalne utwardzane promieniami UV: Powłoki utwardzane promieniowaniem UV są nakładane w postaci cieczy, a następnie utwardzane światłem UV. Oferują krótkie czasy utwardzania, co może zwiększyć wydajność produkcji. Warstwy utwardzane promieniowaniem UV zapewniają dobrą odporność na wilgoć, izolację elektryczną i odporność chemiczną. Nadają się do zastosowań wymagających szybkiego utwardzania, dużej przepustowości i stałej jakości powłoki.
Należy zauważyć, że wybór odpowiedniej powłoki ochronnej zależy od konkretnych wymagań zespołu elektronicznego i zamierzonego zastosowania. Warunki środowiskowe, zakres temperatur roboczych, narażenie chemiczne i pożądany poziom ochrony należy wziąć pod uwagę przy wyborze rodzaju powłoki konforemnej, aby zapewnić optymalną wydajność i trwałość urządzeń elektronicznych.
Akrylowe powłoki ochronne
Akrylowe powłoki ochronne są szeroko stosowane w przemyśle elektronicznym ze względu na ich wszechstronność, opłacalność i łatwość aplikacji. Zapewniają szereg korzyści i są odpowiednie dla różnych zespołów elektronicznych i zastosowań. Oto kilka kluczowych cech i zalet akrylowych powłok ochronnych:
- Ochrona przed wilgocią: Powłoki akrylowe zapewniają dobrą odporność na wilgoć, pomagając zapobiegać przenikaniu wody lub wilgoci do elementów elektronicznych. Wilgoć może powodować korozję, zwarcia elektryczne i pogorszenie wydajności. Powłoki akrylowe działają jak bariera, chroniąc przed problemami związanymi z wilgocią oraz zwiększając niezawodność i żywotność urządzeń elektronicznych.
- Izolacja elektryczna: Powłoki akrylowe zapewniają izolację elektryczną, zapobiegając upływowi prądu i zwarciom. Pomagają zachować pożądaną charakterystykę elektryczną komponentów i zmniejszają ryzyko wadliwego działania lub awarii elektrycznych spowodowanych zanieczyszczeniem lub wchłanianiem wilgoci. Ta właściwość izolacji elektrycznej jest niezbędna do utrzymania integralności obwodów elektronicznych.
- Ochrona środowiska: Akrylowe powłoki ochronne chronią zespoły elektroniczne przed czynnikami środowiskowymi, takimi jak kurz, brud, chemikalia i wahania temperatury. Tworzą barierę przed zanieczyszczeniami unoszącymi się w powietrzu, zapobiegając ich osadzaniu się na powierzchni elementów. Powłoki akrylowe zapewniają również pewien poziom odporności na chemikalia, zapewniając dodatkową ochronę przed substancjami korozyjnymi.
- Łatwość aplikacji: Powłoki akrylowe są znane z łatwości aplikacji. Można je nakładać różnymi metodami, m.in. za pomocą pędzla, natrysku, zanurzania czy powlekania wybiórczego. Ta elastyczność pozwala na ręczne i automatyczne procesy aplikacji, w zależności od konkretnych wymagań i skali produkcji. Powłoki akrylowe mają na ogół dobrą zdolność zwilżania, zapewniając równomierne pokrycie i przyczepność do powierzchni elementów elektronicznych.
- Możliwość naprawy i przeróbki: Jedną z zalet powłok akrylowych jest możliwość ich przeróbki. Jeśli wymagane są naprawy lub modyfikacje, powłoki akrylowe można łatwo usunąć za pomocą odpowiednich rozpuszczalników, co pozwala na prace naprawcze na elementach leżących pod spodem. Możliwość usuwania i ponownego nakładania powłok akrylowych upraszcza proces naprawy i ułatwia czynności konserwacyjne.
- Przezroczyste lub półprzezroczyste: Akrylowe powłoki ochronne są zazwyczaj przezroczyste lub półprzezroczyste. Ta funkcja umożliwia wizualną inspekcję leżących pod spodem elementów bez konieczności usuwania powłoki. Kontrola wzrokowa identyfikuje potencjalne problemy, takie jak wady połączeń lutowanych, uszkodzenia komponentów lub zanieczyszczenie ciałami obcymi.
- Ekonomiczność: Akrylowe powłoki konforemne stanowią opłacalne rozwiązanie do ochrony podzespołów elektronicznych. Dobrze równoważą wydajność i przystępną cenę, dzięki czemu nadają się do szerokiego zakresu zastosowań. Stosunkowo niski koszt powłok akrylowych pozwala na efektywne kosztowo procesy produkcyjne bez uszczerbku dla pożądanej ochrony i niezawodności urządzeń elektronicznych.
Akrylowe powłoki konforemne zapewniają wiele korzyści, ale przy wyborze rodzaju powłoki należy wziąć pod uwagę specyficzne wymagania zespołu elektronicznego i warunki środowiskowe. Aby zapewnić optymalną ochronę i wydajność, należy wziąć pod uwagę takie czynniki, jak zakres temperatur pracy, narażenie na działanie substancji chemicznych i naprężenia mechaniczne.
Silikonowe powłoki ochronne
Silikonowe powłoki ochronne są szeroko stosowane w przemyśle elektronicznym ze względu na ich unikalne właściwości i odporność na trudne warunki środowiskowe. Oferują szereg korzyści, dzięki którym nadają się do różnych zespołów elektronicznych i zastosowań. Oto kilka kluczowych cech i zalet silikonowych powłok ochronnych:
- Stabilność termiczna: Powłoki silikonowe są znane ze swojej doskonałej stabilności termicznej, co pozwala im wytrzymać wysokie temperatury robocze bez utraty właściwości ochronnych. Mogą radzić sobie ze zmianami temperatury skuteczniej niż wiele innych rodzajów powłok ochronnych. To sprawia, że powłoki silikonowe doskonale nadają się do zastosowań o wysokiej stabilności termicznej, takich jak motoryzacja, lotnictwo i elektronika przemysłowa.
- Elastyczność i zgodność: Silikonowe powłoki ochronne są bardzo elastyczne i mogą dopasowywać się do kształtu złożonych zespołów elektronicznych. Można je nakładać w postaci cienkich, jednolitych warstw, które zapewniają całkowite pokrycie nawet skomplikowanych obwodów i komponentów. Elastyczność i dopasowanie powłok silikonowych zapewnia odpowiednią ochronę krytycznych obszarów, zmniejszając ryzyko uszkodzenia lub awarii.
- Ochrona przed wilgocią i środowiskiem: Powłoki silikonowe zapewniają doskonałą odporność na wilgoć, co czyni je praktyczną barierą przed wnikaniem wody i wilgoci. Ta ochrona przed wilgocią pomaga zapobiegać korozji, utlenianiu i zwarciom elektrycznym spowodowanym problemami związanymi z wilgocią. Powłoki silikonowe są również odporne na czynniki środowiskowe, takie jak kurz, brud i chemikalia, zwiększając trwałość i niezawodność urządzeń elektronicznych.
- Izolacja elektryczna: Silikonowe powłoki ochronne zapewniają właściwości izolacji elektrycznej, zapobiegając wyciekom prądu i zwarciom. Utrzymują integralność elektryczną komponentów i chronią przed awariami elektrycznymi spowodowanymi zanieczyszczeniem lub wchłanianiem wilgoci. Izolacja elektryczna oferowana przez powłoki silikonowe ma kluczowe znaczenie dla zachowania niezawodności i wydajności obwodów elektronicznych.
- Odporność chemiczna: Powłoki silikonowe wykazują dobrą odporność na różne chemikalia, w tym rozpuszczalniki, paliwa, kwasy i zasady. Ta odporność chemiczna sprawia, że powłoki silikonowe nadają się do zastosowań, w których narażenie na substancje żrące jest problemem. Warstwy działają jak bariera ochronna, zapobiegając reakcjom chemicznym i degradacji materiału oraz zapewniając długowieczność elementów elektronicznych.
- Odporność na promieniowanie UV i warunki pogodowe: Powłoki silikonowe zapewniają doskonałą odporność na promieniowanie ultrafioletowe (UV) i warunki atmosferyczne. Mogą wytrzymać przedłużoną ekspozycję na światło słoneczne i warunki zewnętrzne bez znacznej degradacji lub utraty właściwości ochronnych. To sprawia, że powłoki silikonowe idealnie nadają się do urządzeń elektronicznych używanych w zastosowaniach zewnętrznych lub narażonych na promieniowanie UV.
- Właściwości dielektryczne: Silikonowe powłoki ochronne mają dobre właściwości dielektryczne, co oznacza, że zapewniają skuteczną izolację elektryczną bez znaczącego wpływu na parametry elektryczne komponentów. Ta właściwość jest niezbędna do zachowania pożądanych właściwości elektrycznych i zapobiegania awariom elektrycznym w obwodach elektronicznych.
Silikonowe powłoki konforemne są dostępne w różnych formułach, aby spełnić określone wymagania aplikacji. Można je nakładać różnymi metodami, w tym pędzlem, natryskiem lub przez zanurzenie. Powłoki silikonowe stanowią niezawodną i trwałą warstwę ochronną dla podzespołów elektronicznych, zapewniając ich funkcjonalność i niezawodność nawet w trudnych warunkach eksploatacji.
Rozważając silikonowe powłoki konformalne, ocena czynników, takich jak zakres temperatur roboczych, narażenie na chemikalia i naprężenia mechaniczne, jest niezbędna do określenia najbardziej odpowiedniej formuły powłoki do konkretnego zastosowania.
Powłoki zgodne z żywicą epoksydową
Powłoki epoksydowe są szeroko stosowane w elektronice ze względu na ich doskonałą twardość, trwałość i odporność chemiczną. Oferują szereg korzyści, dzięki którym nadają się do różnych zespołów elektronicznych i zastosowań. Oto kilka kluczowych cech i zalet epoksydowych powłok ochronnych:
- Twardość i ochrona mechaniczna: Powłoki epoksydowe zapewniają wyjątkową twardość i ochronę mechaniczną, dzięki czemu są wysoce odporne na ścieranie, uderzenia i uszkodzenia fizyczne. Oferują solidną barierę, która chroni elementy elektroniczne przed naprężeniami mechanicznymi, zapewniając ich długowieczność i niezawodność. Powłoki epoksydowe są szczególnie odpowiednie do zastosowań wymagających zwiększonej automatycznej ochrony, takich jak przemysłowe systemy sterowania i wzmocniona elektronika.
- Odporność chemiczna: Powłoki epoksydowe wykazują doskonałą odporność na różne chemikalia, w tym rozpuszczalniki, paliwa, kwasy i zasady. Ta odporność chemiczna chroni elementy elektroniczne przed degradacją lub uszkodzeniem spowodowanym narażeniem na substancje żrące. Powłoki epoksydowe działają jak bariera, zapobiegając reakcjom chemicznym i zapewniając integralność podstawowych elementów.
- Ochrona przed wilgocią i środowiskiem: Powłoki epoksydowe zapewniają odpowiednią ochronę przed wilgocią i środowiskiem. Tworzą barierę przed wodą, wilgocią, kurzem i innymi zanieczyszczeniami środowiskowymi, które mogą uszkodzić elementy elektroniczne. Powłoki epoksydowe pomagają zapobiegać korozji, zwarciom elektrycznym i pogorszeniu wydajności, zapobiegając wnikaniu wilgoci.
- Izolacja elektryczna: Powłoki epoksydowe zapewniają doskonałe właściwości izolacji elektrycznej, zapobiegając upływom prądu i zwarciom. Utrzymują pożądane właściwości elektryczne komponentów, zmniejszając ryzyko awarii elektrycznych lub awarii spowodowanych zanieczyszczeniem lub wchłanianiem wilgoci. Izolacja elektryczna zapewniana przez powłoki epoksydowe ma kluczowe znaczenie dla zachowania niezawodności i wydajności obwodów elektronicznych.
- Odporność termiczna: Powłoki epoksydowe mają dobrą odporność termiczną, co pozwala im wytrzymać podwyższone temperatury bez znacznej degradacji lub utraty właściwości ochronnych. Pomagają rozpraszać ciepło wytwarzane przez komponenty elektroniczne, przyczyniając się do zarządzania temperaturą i zapobiegając przegrzaniu. Ta odporność termiczna sprawia, że powłoki epoksydowe nadają się do zastosowań, w których zmiany temperatury i rozpraszanie ciepła mają krytyczne znaczenie.
- Przyczepność i pokrycie: Powłoki epoksydowe wykazują doskonałą przyczepność do różnych podłoży, w tym metali, tworzyw sztucznych i materiałów PCB. Dobrze przylegają do powierzchni podzespołów elektronicznych, tworząc jednolitą i ciągłą warstwę ochronną. Powłoki epoksydowe mogą zapewnić pełne pokrycie, zapewniając odpowiednią ochronę wszystkich krytycznych obszarów i komponentów.
- Możliwość naprawy: Powłoki epoksydowe mają tę zaletę, że można je przerabiać i naprawiać. Jeśli wymagane są naprawy lub modyfikacje, powłoki epoksydowe można selektywnie usunąć za pomocą odpowiednich rozpuszczalników, umożliwiając prace naprawcze na elementach leżących poniżej. Ta cecha umożliwiająca naprawę upraszcza czynności konserwacyjne i ułatwia wymianę komponentów w razie potrzeby.
Powłoki epoksydowe są zwykle nakładane za pomocą pędzla, natrysku lub selektywnych metod powlekania. Powłoki utwardzają się w wyniku reakcji chemicznej lub procesu utwardzania cieplnego, tworząc trwałą warstwę ochronną. Zapewniają długotrwałą ochronę podzespołów elektronicznych, zapewniając ich funkcjonalność i niezawodność w wymagających środowiskach.
Rozważając odpowiednie powłoki epoksydowe, ocena czynników, takich jak zakres temperatur roboczych, narażenie na chemikalia, naprężenia mechaniczne oraz pożądany poziom ochrony mechanicznej i chemicznej, jest niezbędna, aby wybrać najbardziej odpowiednią formułę powłoki do konkretnego zastosowania.
Powłoki zgodne z uretanem
Powłoki konformalne uretanowe, znane również jako powłoki poliuretanowe, są szeroko stosowane w przemyśle elektronicznym ze względu na ich wyjątkową odporność chemiczną i trwałość mechaniczną. Oferują szereg korzyści, dzięki którym nadają się do różnych zespołów elektronicznych i zastosowań. Oto kilka kluczowych cech i zalet uretanowych powłok ochronnych:
- Odporność chemiczna: Powłoki uretanowe są odporne na różne chemikalia, w tym rozpuszczalniki, paliwa, oleje, kwasy i zasady. Ta odporność chemiczna sprawia, że powłoki uretanowe doskonale nadają się do zastosowań, w których narażenie na agresywne chemikalia stanowi problem. Działają jak bariera, chroniąc elementy elektroniczne przed degradacją chemiczną, korozją i innymi formami uszkodzeń.
- Ochrona przed wilgocią: Uretanowe powłoki ochronne zapewniają skuteczną odporność na wilgoć, zapobiegając wnikaniu wody lub wilgoci do elementów elektronicznych. Wilgoć może powodować korozję, zwarcia elektryczne i pogorszenie wydajności. Powłoki uretanowe działają jak bariera, chroniąc przed problemami związanymi z wilgocią oraz zwiększając niezawodność i żywotność urządzeń elektronicznych.
- Trwałość mechaniczna: Powłoki uretanowe zapewniają doskonałą trwałość mechaniczną, odporność na ścieranie, uderzenia i uszkodzenia fizyczne. Zapewniają twardą warstwę ochronną, która wytrzymuje trudne warunki użytkowania i środowiska. Powłoki uretanowe nadają się do zastosowań, w których wymagana jest zwiększona ochrona mechaniczna, na przykład w warunkach przemysłowych lub urządzeniach narażonych na duże zużycie.
- Odporność termiczna: Powłoki uretanowe wykazują dobrą odporność termiczną, dzięki czemu wytrzymują podwyższone temperatury bez znacznej degradacji lub utraty właściwości ochronnych. Pomagają rozpraszać ciepło wytwarzane przez komponenty elektroniczne, przyczyniając się do zarządzania temperaturą i zapobiegając przegrzaniu. Ta odporność termiczna sprawia, że powłoki uretanowe nadają się do zastosowań, w których zmiany temperatury i rozpraszanie ciepła mają krytyczne znaczenie.
- Elastyczność: Powłoki konforemne z uretanu zapewniają równowagę pomiędzy twardością a elastycznością. Mają pewną elastyczność, co pozwala im dostosować się do drobnych ruchów i naprężeń w zespole elektronicznym. Ta elastyczność pomaga zmniejszyć ryzyko pękania lub rozwarstwiania się powłoki, zapewniając długotrwałą ochronę elementów.
- Stabilność UV: Powłoki uretanowe wykazują dobrą odporność na promieniowanie ultrafioletowe (UV), chroniąc przed potencjalnie szkodliwym działaniem promieni słonecznych i innych źródeł UV. Są odporne na żółknięcie lub degradację pod wpływem światła UV, dzięki czemu nadają się do zastosowań zewnętrznych lub urządzeń narażonych na promieniowanie UV.
- Przyczepność i pokrycie: Powłoki uretanowe wykazują doskonałą przyczepność do różnych podłoży, w tym metali, tworzyw sztucznych i materiałów PCB. Dobrze przylegają do powierzchni podzespołów elektronicznych, tworząc jednolitą i ciągłą warstwę ochronną. Powłoki uretanowe mogą zapewnić pełne pokrycie, zapewniając odpowiednią ochronę wszystkich krytycznych obszarów i komponentów.
Powłoki konformalne uretanowe są zwykle nakładane za pomocą pędzla, natrysku lub selektywnych metod powlekania. Warstwy można utwardzać poprzez procesy utwardzania termicznego lub utwardzania wilgocią, tworząc trwałą i ochronną warstwę. Zapewniają długotrwałą ochronę podzespołów elektronicznych, zapewniając ich funkcjonalność i niezawodność w wymagających środowiskach.
Rozważając zastosowanie uretanowych powłok konforemnych, niezbędna jest ocena określonej ekspozycji chemicznej, zakresu temperatur roboczych, naprężeń mechanicznych oraz pożądanego poziomu ochrony chemicznej i mechanicznej, aby wybrać najbardziej odpowiednią formułę powłoki do konkretnego zastosowania.
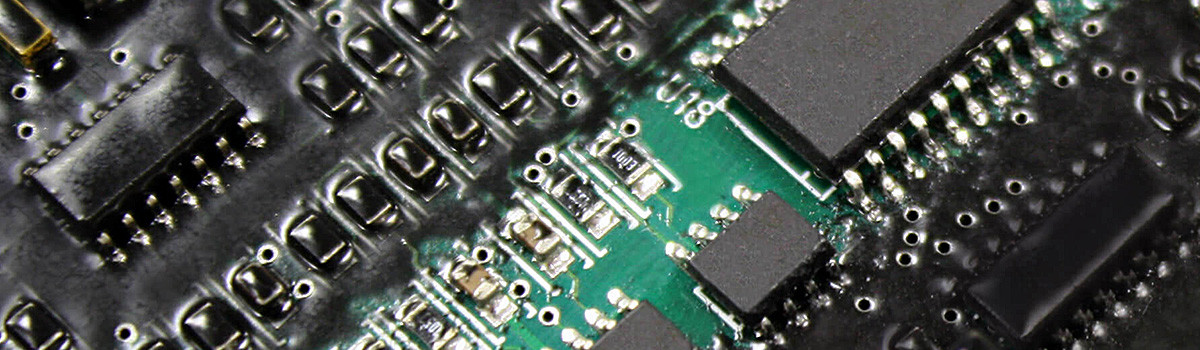
Parylenowe powłoki konforemne
Powłoki konforemne Parylenu są unikalne i zapewniają wyjątkową ochronę urządzeń elektronicznych. Powłoki parylenowe osadzają się w postaci pary i tworzą cienką, pozbawioną dziurek warstwę polimerową. Oferują one szereg korzyści, dzięki którym doskonale nadają się do różnych zespołów elektronicznych i zastosowań. Oto kilka kluczowych cech i zalet powłok konforemnych Parylenu:
- Bariera przed wilgocią i chemikaliami: Powłoki parylenowe zapewniają doskonałą barierę przed wilgocią, gazami i chemikaliami. Cienka, jednolita warstwa utworzona przez powłoki Parylenu zapewnia wysoce skuteczną barierę dla wilgoci, zapobiegając przedostawaniu się wody i wilgoci do elementów elektronicznych. Zapewniają również wyjątkową odporność na chemikalia, w tym rozpuszczalniki, kwasy, zasady i substancje żrące. Ta odporność na wilgoć i chemikalia chroni urządzenia elektroniczne przed korozją, utlenianiem i degradacją, zapewniając ich długotrwałą niezawodność.
- Zgodność i pokrycie: Powłoki parylenowe mają wyjątkowe właściwości konforemne, co oznacza, że dopasowują się do kształtu złożonych i nieregularnych powierzchni. Proces osadzania z fazy gazowej umożliwia równomierne pokrycie całego zespołu elektronicznego, w tym skomplikowanych elementów, ostrych krawędzi i szczelin. Powłoki parylenowe mogą wnikać głęboko w ciasne przestrzenie, zapewniając pełne pokrycie i ochronę wszystkich krytycznych obszarów.
- Izolacja elektryczna: Parylenowe powłoki ochronne zapewniają doskonałe właściwości izolacji elektrycznej. Mają wysoką wytrzymałość dielektryczną i mogą skutecznie izolować elementy elektryczne oraz zapobiegać wyciekom prądu lub zwarciom. Powłoki parylenowe zachowują pożądane właściwości elektryczne detali, zmniejszając ryzyko awarii elektrycznych lub awarii spowodowanych zanieczyszczeniem lub wchłanianiem wilgoci.
- Biokompatybilność: Powłoki parylenowe są biokompatybilne i chemicznie obojętne, dzięki czemu nadają się do wyrobów medycznych i wszczepialnej elektroniki. Nie powodują niepożądanych reakcji w kontakcie z tkankami biologicznymi lub płynami. Powłoki parylenowe są stosowane w aplikacjach takich jak rozruszniki serca, implanty nerwowe i bioczujniki, w których biokompatybilność ma kluczowe znaczenie.
- Stabilność termiczna: Powłoki parylenowe wykazują doskonałą stabilność termiczną i mogą wytrzymać szeroki zakres temperatur. Zachowują stabilność w niskich i wysokich temperaturach, zachowując swoje właściwości ochronne bez znacznej degradacji. Ta stabilność termiczna sprawia, że powłoki parylenowe nadają się do zastosowań, w których istotne są zmiany temperatury i rozpraszanie ciepła.
- Niski współczynnik tarcia: Powłoki parylenowe mają niski współczynnik tarcia, zapewniając smarowność i zmniejszając tarcie powierzchniowe między elementami. Ten niski współczynnik tarcia pomaga zminimalizować zużycie, zapobiega przyklejaniu się lub zakleszczaniu oraz poprawia ogólną wydajność i żywotność powlekanych urządzeń elektronicznych.
- Przejrzystość i identyfikowalność: Powłoki konforemne Parylenu są przezroczyste, co pozwala na wizualną kontrolę leżących pod spodem komponentów bez konieczności usuwania powłoki. Ta przejrzystość umożliwia ocenę i identyfikację potencjalnych problemów, takich jak wady połączeń lutowanych, uszkodzenia komponentów lub zanieczyszczenie ciałami obcymi. Dodatkowo powłoki Parylenu mogą być domieszkowane lub oznaczone identyfikowalnymi pierwiastkami, co ułatwia kontrolę jakości, śledzenie i identyfikację.
Parylenowe powłoki konforemne są zwykle nakładane przy użyciu specjalistycznego procesu osadzania z fazy gazowej. Warstwy są formowane metodą chemicznego osadzania z fazy gazowej (CVD), co zapewnia równomierne pokrycie bez dziurek. Powłoki parylenowe zapewniają długotrwałą ochronę podzespołów elektronicznych, nawet w trudnych warunkach i wymagających zastosowaniach.
Rozważając powłoki zgodne z Parylenem, niezbędna jest ocena czynników, takich jak specyficzne wymagania zespołu elektronicznego, warunki środowiskowe i pożądany poziom ochrony, aby wybrać odpowiedni typ Parylenu i proces osadzania.
Czynniki, które należy wziąć pod uwagę przy wyborze powłoki ochronnej
Wybierając odpowiednią powłokę dla urządzeń elektronicznych, należy wziąć pod uwagę kilka czynników, aby upewnić się, że powłoka spełnia specyficzne wymagania aplikacji. Oto kilka kluczowych czynników, które należy wziąć pod uwagę:
- Warunki środowiskowe: Warunki środowiskowe, w których urządzenie elektroniczne będzie działać, odgrywają kluczową rolę w wyborze odpowiedniej powłoki ochronnej. Weź pod uwagę takie czynniki, jak ekstremalne temperatury, poziomy wilgotności, narażenie na chemikalia, mgłę solną i promieniowanie UV. Różne warstwy mają różny stopień odporności na te czynniki środowiskowe, a wybór powłoki, która może wytrzymać określone warunki, ma kluczowe znaczenie dla długoterminowej niezawodności.
- Właściwości elektryczne: Rozważ właściwości elektryczne wymagane dla zespołu elektronicznego. Niektóre powłoki oferują lepsze właściwości izolacji elektrycznej niż inne. Oceń wytrzymałość dielektryczną, rezystancję powierzchniową i zdolność do utrzymania izolacji nawet w obecności wilgoci lub zanieczyszczeń. Upewnij się, że wybrana powłoka nie wpływa negatywnie na parametry elektryczne komponentów.
- Grubość i pokrycie: Wymagania dotyczące grubości i pokrycia powłoki konforemnej są istotnymi kwestiami. Cienkie warstwy są pożądane w zastosowaniach, w których ograniczona przestrzeń lub zachowanie wąskich tolerancji ma krytyczne znaczenie. Jednak grubsze powłoki mogą być konieczne w zastosowaniach wymagających zwiększonej ochrony przed naprężeniami mechanicznymi lub trudnymi warunkami środowiskowymi. Warstwa powinna być w stanie równomiernie pokryć wszystkie krytyczne obszary, w tym złożone geometrie i komponenty.
- Metoda aplikacji: Rozważ dostępne metody i wybierz powłokę zgodną z wybranym trybem. Standardowe metody aplikacji obejmują natryskiwanie, malowanie pędzlem, zanurzanie i selektywne powlekanie. Niektóre warstwy mogą być lepiej dostosowane do określonych metod aplikacji, podczas gdy inne mogą wymagać specjalistycznego sprzętu lub technik.
- Przeróbka i naprawa: Oceń wymagania dotyczące przeróbek i możliwości naprawy powłoki. W niektórych przypadkach usunięcie lub naprawa warstwy może być konieczna do wymiany części, naprawy lub modyfikacji. Niektóre powłoki można łatwo przerobić lub usunąć, podczas gdy inne mogą być trudniejsze lub wymagają specjalistycznych rozpuszczalników lub metod.
- Kompatybilność podłoża: Rozważ kompatybilność powłoki z materiałami i podłożami używanymi w zespole elektronicznym. Powłoka powinna przylegać do podłoża i wykazywać dobrą kompatybilność z komponentami, złączami lutowanymi i innymi materiałami. Problemy ze zgodnością mogą prowadzić do rozwarstwienia, zmniejszonej przyczepności lub słabej wydajności powłoki.
- Zgodność z przepisami: rozważ wszelkie szczególne wymagania prawne, które mają zastosowanie do urządzenia elektronicznego lub branży, w której będzie ono używane. Typowe zastosowania, takie jak urządzenia medyczne lub elektronika lotnicza, mogą podlegać określonym normom regulacyjnym dotyczącym powłok ochronnych. Upewnij się, że wybrana powłoka jest zgodna z odpowiednimi przepisami i normami.
- Koszt i dostępność: Oceń koszt powłoki i jej dostępność w wymaganych ilościach. Weź pod uwagę opłacalność powłoki, pożądany poziom ochrony i całkowity budżet projektu. Ponadto upewnij się, że powłoka jest łatwo dostępna od niezawodnych dostawców, aby uniknąć opóźnień lub problemów z łańcuchem dostaw.
Biorąc pod uwagę te czynniki, możesz wybrać powłokę ochronną, która zapewnia optymalną ochronę, wydajność i niezawodność dla określonych wymagań urządzenia elektronicznego i jego środowiska pracy.
Metody nakładania powłok ochronnych
Powłoki ochronne to cienkie warstwy ochronne nakładane na płytki elektroniczne i komponenty w celu zapewnienia izolacji i ochrony przed czynnikami środowiskowymi, takimi jak wilgoć, kurz, chemikalia i wahania temperatury. Powłoki te mają za zadanie „dopasować się” do kształtu podłoża, zapewniając jednolitą i ciągłą barierę ochronną. Istnieje kilka metod nakładania powłok ochronnych, z których każda ma zalety i względy. W tym artykule przyjrzymy się niektórym standardowym metodom nakładania powłok ochronnych.
- Szczotkowanie/zanurzanie: Szczotkowanie lub zanurzanie jest jedną z najprostszych i najbardziej tradycyjnych metod nakładania powłok ochronnych. Materiał powlekający jest ręcznie szczotkowany lub składniki zanurzane są w pojemniku z roztworem powlekającym. Ta metoda jest opłacalna i odpowiednia do produkcji na małą skalę. Może to jednak skutkować nierówną grubością powłoki i wymagać utwardzenia po aplikacji.
- Powlekanie natryskowe: Powlekanie natryskowe polega na użyciu sprężonego powietrza lub specjalistycznego systemu natryskowego w celu nałożenia materiału powłokowego w postaci drobnej mgiełki na podłoże. Ta metoda zapewnia szybszą aplikację i jest odpowiednia dla procesów ręcznych i automatycznych. Powlekanie natryskowe zapewnia większą kontrolę nad grubością i jednolitością powłoki, ale wymaga odpowiednich systemów wentylacji i filtracji, aby kontrolować nadmiar natrysku i zapewnić bezpieczeństwo operatora.
- Powłoka selektywna: Powłoka selektywna jest stosowana, gdy tylko określone obszary podłoża wymagają ochrony. Polega na zastosowaniu kontrolowanego systemu dozowania lub ramienia robota z precyzyjnym aplikatorem w celu precyzyjnego nałożenia materiału powłokowego w pożądane miejsca. Powłoka selektywna minimalizuje straty, zmniejsza potrzebę maskowania i pozwala na ukierunkowaną ochronę. Jest powszechnie używany do złożonych płytek drukowanych z wrażliwymi komponentami.
- Osadzanie z fazy gazowej: Metody osadzania z fazy gazowej, takie jak chemiczne osadzanie z fazy gazowej (CVD) i fizyczne osadzanie z fazy gazowej (PVD), obejmują osadzanie konforemnej warstwy powłoki na podłożu przez fazę gazową. Metody te zazwyczaj wymagają specjalistycznego sprzętu i kontrolowanych środowisk. Techniki osadzania z fazy gazowej zapewniają doskonałą jednorodność powłoki, kontrolę grubości i pokrycie złożonych geometrii. Są powszechnie używane w aplikacjach o wysokiej wydajności i zaawansowanych urządzeniach elektronicznych.
- Powlekanie Parylenem: Powlekanie Parylenem to unikalna metoda polegająca na osadzeniu cienkiej konforemnej warstwy polimeru na podłożu poprzez osadzanie z fazy gazowej. Powłoki parylenowe zapewniają wyjątkową ochronę, izolację i biokompatybilność. Materiał powłokowy wnika w szczeliny i równomiernie pokrywa całą powierzchnię, nawet na skomplikowanych elementach. Powłoki parylenowe są powszechnie stosowane w urządzeniach medycznych, lotnictwie i zastosowaniach o wysokiej niezawodności.
Wybierając metodę nakładania powłok ochronnych, należy wziąć pod uwagę kilka czynników, w tym złożoność podłoża, wielkość produkcji, właściwości materiału powłokowego, koszt i wymagania środowiskowe. Istotne jest, aby wybrać metodę, która zapewnia optymalne pokrycie, jednorodność i niezawodność powłoki, biorąc pod uwagę specyficzne potrzeby aplikacji.
Grubość powłoki ochronnej
Grubość powłoki ochronnej ma kluczowe znaczenie dla zapewnienia skuteczności i niezawodności powłoki ochronnej nakładanej na elementy elektroniczne i płytki drukowane. Grubość powłoki bezpośrednio wpływa na stopień ochrony przed czynnikami środowiskowymi, takimi jak wilgoć, kurz, chemikalia i wahania temperatury. W tym artykule zbadamy znaczenie konforemnej grubości powłoki i rozważania związane z osiągnięciem pożądanej grubości powłoki.
Podstawowym celem powłok ochronnych jest stworzenie jednolitej i ciągłej warstwy ochronnej na podłożu. Grubość powłoki powinna być wystarczająca, aby zapewnić izolację i zapobiec potencjalnym zwarciom elektrycznym lub prądom upływowym, a jednocześnie nie być tak gruba, aby powodować zakłócenia elektryczne lub problemy termiczne. Idealna grubość powłoki zależy od czynników, takich jak materiał powłoki, konkretne zastosowanie i warunki środowiskowe, z którymi będzie się zmagać powlekana elektronika.
Powłoki konforemne są na ogół nakładane jako cienkie warstwy, zwykle o grubości od kilku mikrometrów (µm) do kilkudziesięciu mikrometrów. Producent materiału powłokowego często określa zalecaną grubość powłoki lub może być zdefiniowana przez normy branżowe, takie jak IPC-CC-830 dla powłok ochronnych.
Osiągnięcie pożądanej grubości powłoki wymaga uwzględnienia kilku czynników:
- Materiał powlekający: Różne konforemne materiały powlekające mają różne lepkości i właściwości płynięcia. Te właściwości wpływają na to, jak powłoka rozprowadza się i wyrównuje na powierzchni podłoża, wpływając na uzyskaną grubość. Niezbędne jest zrozumienie specyficznych wymagań aplikacji i wybór materiału powłokowego, który można nakładać z żądaną kontrolą grubości.
- Metoda aplikacji: Wybrana metoda aplikacji również odgrywa istotną rolę w określaniu grubości powłoki. Praktyki takie jak malowanie pędzlem lub zanurzanie mogą powodować różnice w grubości powłoki ze względu na ręczne techniki nakładania. Zautomatyzowane procesy, takie jak powlekanie natryskowe lub selektywne, mogą zapewnić większą kontrolę nad grubością powłoki, co skutkuje bardziej równą i jednolitą warstwą.
- Kontrola procesu: Właściwa kontrola procesu ma kluczowe znaczenie dla osiągnięcia pożądanej grubości powłoki. Czynniki takie jak ciśnienie natrysku, rozmiar dyszy, odległość natrysku i lepkość materiału powłokowego muszą być dokładnie kontrolowane podczas procesu aplikacji. Parametry procesu mogą wymagać dostosowania w zależności od geometrii podłoża i pożądanej grubości powłoki.
- Utwardzanie/kurczenie: Niektóre konforemne materiały powłokowe przechodzą proces utwardzania lub suszenia po nałożeniu. Materiał powłoki może się kurczyć podczas tego procesu, wpływając na ostateczną grubość powłoki. Przy określaniu początkowej grubości powłoki należy wziąć pod uwagę potencjalny skurcz.
- Weryfikacja i inspekcja: Po nałożeniu powłoki należy koniecznie zweryfikować jej grubość, aby upewnić się, że spełnia ona wymagane specyfikacje. Można zastosować różne techniki kontroli, takie jak kontrola wzrokowa, przekroje poprzeczne lub specjalistyczny sprzęt pomiarowy, taki jak profilometry lub mikroskop optyczny ze skalibrowanym oprogramowaniem pomiarowym.
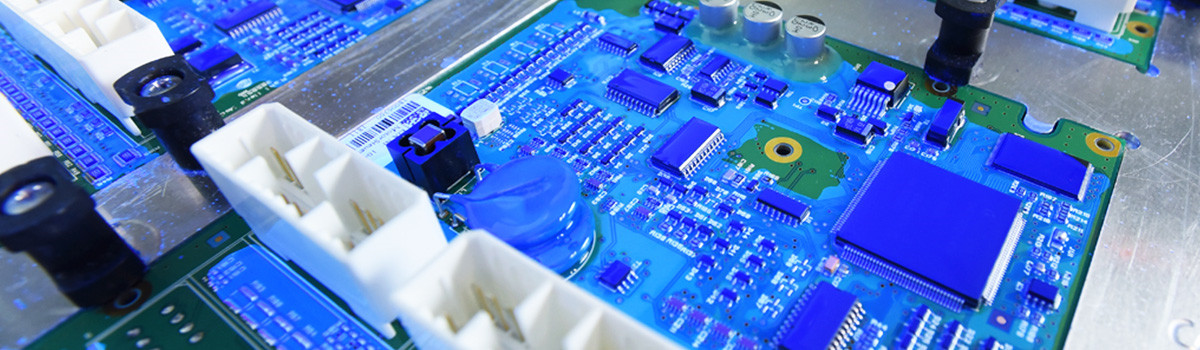
Typowe problemy z powłokami ochronnymi
Chociaż powłoki ochronne są niezbędne do ochrony elementów elektronicznych i płytek drukowanych, czasami mogą napotkać problemy, które mogą wpłynąć na ich wydajność i niezawodność. W tym artykule omówimy niektóre typowe problemy z powłokami ochronnymi i ich potencjalne przyczyny.
- Niewystarczające pokrycie: Niewystarczające pokrycie występuje, gdy powłoka nie pokrywa całej powierzchni podłoża lub pozostawia szczeliny i ubytki. Ten problem może wynikać z niewłaściwych technik aplikacji, takich jak nierównomierne natryskiwanie lub niewystarczająca lepkość powłoki. Może również wystąpić z powodu zanieczyszczenia powierzchni, nieodpowiedniego suszenia lub utwardzania lub nieodpowiedniej kontroli grubości powłoki.
- Zmienność grubości: Niejednolita grubość powłoki to kolejny częsty problem. Przyczyną mogą być niespójne techniki aplikacji, takie jak nierównomierne natryskiwanie lub nieodpowiednia kontrola parametrów procesu. Potrzebny jest dłuższy czas schnięcia lub utwardzania, niewłaściwa lepkość materiału powłokowego lub niewystarczające przygotowanie powierzchni mogą również przyczynić się do różnic w grubości.
- Pęcherze i rozwarstwienia: Pęcherze i rozwarstwienia występują, gdy powłoka ochronna tworzy pęcherzyki lub oddziela się od podłoża. Ten problem może powstać z powodu niewłaściwego czyszczenia i przygotowania powierzchni, wilgoci lub zanieczyszczenia na powierzchni, nieodpowiedniego utwardzania lub suszenia lub niewłaściwej kompatybilności materiału powłokowego z podłożem.
- Pękanie i mostkowanie: Pękanie odnosi się do powstawania pęknięć lub pęknięć w powłoce ochronnej, podczas gdy mostkowanie występuje, gdy materiał powłokowy rozciąga się na szczeliny lub sąsiednie elementy, powodując niezamierzone połączenia elektryczne. Problemy te mogą być spowodowane nadmierną grubością powłoki, nieodpowiednim utwardzaniem lub suszeniem, naprężeniami termicznymi, niewłaściwym doborem materiału powłokowego lub nieodpowiednią elastycznością powłoki.
- Słaba przyczepność: Słaba przyczepność występuje, gdy powłoka nie przylega do podłoża, co skutkuje zmniejszoną ochroną i potencjalnym odwarstwieniem powłoki. Nieodpowiednie oczyszczenie i przygotowanie powierzchni, zanieczyszczenia, niekompatybilne materiały powłoka-podłoże lub niewystarczające utwardzanie lub suszenie mogą być tego przyczyną.
- Migracja elektrochemiczna: Migracja elektrochemiczna to przemieszczanie się jonów lub zanieczyszczeń po powierzchni powlekanego podłoża, co prowadzi do potencjalnych zwarć i korozji. Może to nastąpić z powodu nieodpowiedniej grubości powłoki, obecności zanieczyszczeń przewodzących lub obecności wilgoci.
- Niewystarczająca odporność chemiczna: Powłoki ochronne mogą wymagać odporności na działanie różnych chemikaliów i rozpuszczalników. Jeśli materiał powłokowy nie ma wystarczającej odporności chemicznej, może ulec degradacji lub rozpuścić pod wpływem określonych substancji, zmniejszając jego właściwości ochronne. Właściwy dobór materiałów ma kluczowe znaczenie dla zapewnienia kompatybilności z oczekiwanym środowiskiem chemicznym.
Aby złagodzić te problemy, niezbędne jest przestrzeganie najlepszych praktyk i wytycznych dotyczących nakładania powłok ochronnych, w tym właściwe czyszczenie i przygotowanie powierzchni, dokładna kontrola parametrów procesu, odpowiedni dobór materiału powłokowego oraz odpowiednie utwardzanie lub suszenie. Należy wdrożyć regularne kontrole i środki kontroli jakości, aby wcześnie zidentyfikować i rozwiązać potencjalne problemy z powłoką. Przestrzeganie standardów branżowych, takich jak IPC-CC-830, może również pomóc w zapewnieniu niezawodności i wydajności powłok ochronnych.
Konserwacja powłok ochronnych
Powłoki ochronne chronią elementy elektroniczne i płytki drukowane przed czynnikami środowiskowymi, takimi jak wilgoć, kurz, chemikalia i wahania temperatury. Jednak, jak każda powłoka ochronna, powłoki ochronne wymagają odpowiedniej konserwacji, aby zapewnić ich długotrwałą skuteczność. Oto kilka kluczowych punktów, które należy wziąć pod uwagę, jeśli chodzi o konserwację powłok ochronnych:
- Regularna kontrola: Przeprowadzaj rutynowe kontrole powlekanych powierzchni, aby sprawdzić, czy nie występują oznaki uszkodzeń, zużycia lub rozwarstwienia. Poszukaj pęknięć, wiórów lub obszarów, w których powłoka mogła się zetrzeć. Kontrole należy przeprowadzać okresowo, zwłaszcza po manipulacji, transporcie lub narażeniu na trudne warunki.
- Czyszczenie: Utrzymuj powlekane powierzchnie w czystości, aby zapobiec gromadzeniu się zanieczyszczeń, które mogłyby zagrozić skuteczności powłoki. Użyj delikatnych metod czyszczenia, takich jak miękka szczotka lub sprężone powietrze, aby usunąć kurz, zanieczyszczenia lub cząstki stałe. Unikaj stosowania ostrych rozpuszczalników lub materiałów ściernych, które mogą uszkodzić powłokę.
- Naprawa uszkodzonych obszarów: Jeśli podczas inspekcji wykryte zostaną jakiekolwiek uszkodzenia lub zużycie, konieczne jest natychmiastowe zajęcie się nimi. Napraw uszkodzone obszary, ponownie pokrywając je tym samym konforemnym materiałem powłokowym. Upewnij się, że uszkodzony obszar jest odpowiednio oczyszczony i przygotowany przed nałożeniem nowej powłoki. Pomoże to zachować integralność warstwy ochronnej.
- Kontrola temperatury i wilgotności: Utrzymuj odpowiednią temperaturę i wilgotność w środowisku, w którym powlekane elementy są przechowywane lub eksploatowane. Ekstremalne temperatury lub wysoki poziom wilgotności mogą wpływać na działanie powłoki i prowadzić do rozwarstwienia lub zmniejszenia ochrony. Postępuj zgodnie z zaleceniami producenta dotyczącymi dopuszczalnych zakresów temperatury i wilgotności dla określonego konforemnego materiału powłokowego.
- Unikaj kontaktu z chemikaliami: Zapobiegaj wystawianiu powlekanych powierzchni na działanie agresywnych chemikaliów lub rozpuszczalników, które mogą uszkodzić powłokę. Zachowaj ostrożność podczas używania środków czyszczących lub wykonywania czynności konserwacyjnych w pobliżu zakrytych elementów. Podejmij niezbędne środki ostrożności, aby chronić powłokę ochronną przed bezpośrednim kontaktem z chemikaliami.
- Ponowne testowanie i ponowna certyfikacja: W niektórych branżach, takich jak lotnictwo i kosmonautyka, powłoki ochronne mogą wymagać okresowych ponownych testów i ponownej certyfikacji, aby upewnić się, że spełniają niezbędne normy i specyfikacje. Postępuj zgodnie z wytycznymi odpowiednich norm branżowych i przeprowadzaj niezbędne testy lub kontrole w regularnych odstępach czasu.
- Dokumentacja i prowadzenie rejestrów: Przechowuj szczegółowe zapisy aplikacji powłoki ochronnej, czynności konserwacyjnych, inspekcji i napraw. Ta dokumentacja pomoże śledzić historię konserwacji, identyfikować wzorce awarii lub zużycia oraz zapewniać zgodność z przepisami i normami branżowymi.
Testowanie i kontrola powłok ochronnych
Testowanie i kontrola powłok konforemnych jest niezbędna do zapewnienia ich skuteczności i niezawodności w ochronie komponentów i zespołów elektronicznych. Oto kilka powszechnie stosowanych metod testowania i kontroli powłok ochronnych:
- Kontrola wizualna: Kontrola wizualna jest niezbędnym krokiem w ocenie jakości powłok ochronnych. Polega na zbadaniu powierzchni powłoki pod kątem widocznych defektów, takich jak dziurki, pęcherzyki, pęknięcia lub nierówne pokrycie.
- Pomiar grubości: Grubość powłoki ochronnej ma kluczowe znaczenie, ponieważ wpływa na jej zdolność do zapewnienia odpowiedniej ochrony. Spójność można mierzyć za pomocą technik prądów wirowych, indukcji magnetycznej lub profilometrii optycznej. Pomiar należy porównać z określonymi wymaganiami dotyczącymi grubości powłoki.
- Test przyczepności: Testy oceniają siłę wiązania między powłoką ochronną a podłożem. Metody testowania przyczepności obejmują testy taśmowe, testy kreskowania i testy odrywania. Testy te określają, czy warstwa odpowiednio przylega do powierzchni i czy jest w stanie wytrzymać naprężenia podczas pracy i przenoszenia.
- Test rezystancji izolacji: Ten test ocenia rezystancję elektryczną powłoki ochronnej. Zapewnia, że warstwa zapewnia skuteczną izolację elektryczną, aby zapobiec wyciekom lub zwarciom. Testowanie rezystancji izolacji jest zwykle przeprowadzane za pomocą testera wysokiego napięcia lub megaomomierza.
- Test wytrzymałości napięciowej dielektryka: Test wytrzymałości na napięcie dielektryczne, znany również jako test wysokiego napięcia lub test wysokiego napięcia, sprawdza zdolność powłoki do wytrzymania wysokiego napięcia bez awarii. Powłoka konforemna jest poddawana działaniu określonego napięcia przez określony czas, aby upewnić się, że spełnia wymagane normy izolacji elektrycznej.
- Testowanie cykli termicznych: cykle termiczne wystawiają powłokę ochronną na zmiany temperatury w celu oceny jej odporności na naprężenia termiczne. Warstwa poddawana jest powtarzającym się cyklom ekstremalnych temperatur i obserwuje się wszelkie zmiany, takie jak spękania czy rozwarstwienia.
- Testy odporności na wilgoć i wilgoć: Testy te oceniają zdolność powłoki ochronnej do wytrzymywania wilgoci i wilgoci. Warstwa jest narażona na działanie wysokiej wilgotności lub wilgoci przez określony czas, a jej działanie jest oceniane pod kątem ochrony przed korozją lub awariami elektrycznymi.
- Testy odporności chemicznej: Testy odporności chemicznej sprawdzają, jak dobrze powłoka ochronna wytrzymuje działanie różnych chemikaliów, takich jak rozpuszczalniki lub środki czyszczące. Warstwę poddaje się działaniu substancji przez określony czas, ocenia się jej wygląd, przyczepność i funkcjonalność.
- Testy w mgle solnej: Testy w mgle solnej oceniają odporność powłoki na korozję w środowisku zasolonym. Powłoka konforemna jest wystawiana na działanie mgły solnej lub mgły przez określony czas i badane są wszelkie oznaki korozji lub degradacji.
Należy zauważyć, że określone wymagania testowe mogą się różnić w zależności od branży, zastosowania i norm mających zastosowanie do powłoki ochronnej. Producenci lub branżowe organizacje normalizacyjne często dostarczają wytyczne lub specyfikacje dotyczące procedur testowania i kontroli.
Normy branżowe dotyczące powłok ochronnych
Istnieje kilka norm i specyfikacji branżowych dotyczących powłok ochronnych, które zapewniają ich jakość, niezawodność i wydajność. Oto niektóre z powszechnie przywoływanych standardów:
- IPC-CC-830: Ta norma, opublikowana przez Association of Connecting Electronics Industries (IPC), jest szeroko stosowana w przypadku materiałów powłok konforemnych i wymagań aplikacji. Obejmuje ogólne warunki, właściwości materiałów, metody aplikacji i kryteria kontroli powłok ochronnych.
- MIL-STD-883: Ta norma wojskowa określa metody i procedury testowania urządzeń mikroelektronicznych, w tym powłoki ochronne. Obejmuje specyfikacje dotyczące przyczepności, rezystancji izolacji, szoku termicznego, wilgotności i innych testów odpowiednich dla powłok ochronnych.
- MIL-STD-810: Ta norma zawiera zagadnienia inżynierii środowiska i metody badań laboratoryjnych do symulacji i oceny wydajności materiałów, sprzętu i systemów w różnych warunkach środowiskowych. Obejmuje procedury testowania powłok ochronnych pod kątem temperatury, wilgotności, wibracji, wstrząsów itp.
- IEC 61086: Ta międzynarodowa norma określa wymagania i metody badań dla powłok ochronnych stosowanych w zespołach elektronicznych. Obejmuje materiały powłokowe, grubość, przyczepność, elastyczność, wytrzymałość termiczną i odporność chemiczną.
- UL 746E: Norma ta, opublikowana przez Underwriters Laboratories (UL), koncentruje się na ocenie materiałów polimerowych do stosowania w sprzęcie elektrycznym. Obejmuje wymagania testowe dla powłok ochronnych w zakresie palności, charakterystyki starzenia i właściwości elektrycznych.
- ISO 9001: ISO 9001, chociaż nie jest specyficzna dla powłok ochronnych, jest uznawaną na całym świecie normą dotyczącą systemów zarządzania jakością. Zapewnia, że organizacje przestrzegają spójnych procesów kontroli jakości, w tym produkcji i kontroli powłok ochronnych.
Należy zauważyć, że różne branże i zastosowania mogą mieć określone normy lub specyfikacje dostosowane do ich unikalnych wymagań. Ponadto wielu producentów powłok konforemnych może dostarczać arkusze danych technicznych lub wytyczne dotyczące stosowania, które mogą służyć jako cenne odniesienia przy wyborze i testowaniu powłok konforemnych.
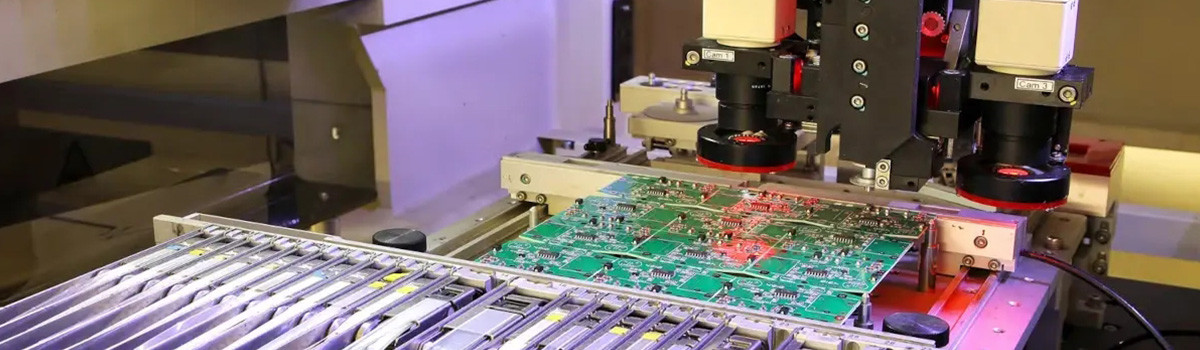
Postępy w technologii powlekania konforemnego
W ostatnich latach nastąpił znaczny postęp w technologii powlekania konforemnego, napędzany potrzebą lepszej ochrony, niezawodności i wydajności komponentów i zespołów elektronicznych. Oto kilka kluczowych ulepszeń:
- Nanopowłoki: nanopowłoki stały się obiecującym postępem w technologii powlekania konforemnego. Powłoki te składają się z ultracienkich warstw, zwykle w nanoskali, zapewniających doskonałą odporność na wilgoć i korozję przy zachowaniu parametrów elektrycznych. Nanopowłoki zapewniają doskonałe pokrycie i zgodność, zapewniając odpowiednią ochronę nawet skomplikowanych i gęsto upakowanych podzespołów elektronicznych.
- Powłoki wielofunkcyjne: Opracowywane są powłoki ochronne o właściwościach wielofunkcyjnych, aby jednocześnie sprostać wielu wyzwaniom. Na przykład niektóre powłoki oferują odporność na wilgoć i chemikalia oraz lepszą przewodność elektryczną lub zarządzanie temperaturą. Te wielofunkcyjne powłoki zmniejszają potrzebę stosowania dodatkowych warstw ochronnych i poprawiają ogólną wydajność.
- Powłoki samonaprawiające się: Powłoki konformalne samonaprawiające się są przeznaczone do automatycznej naprawy drobnych uszkodzeń. Powłoki te zawierają kapsułkowane środki lecznicze uwalniane w momencie uszkodzenia, wypełniające pęknięcia lub ubytki oraz przywracające właściwości ochronne powłoki. Powłoki samonaprawiające przedłużają żywotność elementów elektronicznych poprzez łagodzenie skutków zużycia lub wpływu czynników środowiskowych.
- Elastyczne i rozciągliwe powłoki: Wraz z rozwojem elastycznej elektroniki i urządzeń do noszenia, powłoki konforemne muszą dostosowywać się do zginania, rozciągania i skręcania podłoży. Elastyczne i rozciągliwe warstwy zostały opracowane w celu zapewnienia solidnej ochrony przy jednoczesnym zachowaniu integralności pod obciążeniem mechanicznym. Powłoki te pozwalają na konforemne pokrycie na elastycznych podłożach, poszerzając zakres zastosowań.
- Powłoki o niskiej zawartości lotnych związków organicznych (LZO) i przyjazne dla środowiska: coraz większy nacisk kładzie się na opracowywanie powłok konforemnych o obniżonej zawartości lotnych związków organicznych (LZO) i preparatów przyjaznych dla środowiska. Powłoki te mają na celu zminimalizowanie wpływu na środowisko podczas aplikacji i użytkowania przy jednoczesnym zachowaniu wysokiej wydajności. Powłoki na bazie wody lub bezrozpuszczalnikowe są opracowywane jako alternatywy dla tradycyjnych powłok na bazie rozpuszczalników.
- Powłoki utwardzane promieniami UV: Powłoki konforemne utwardzane promieniowaniem UV zapewniają szybki czas utwardzania, umożliwiając wyższą przepustowość procesów produkcyjnych. Powłoki te wykorzystują światło ultrafioletowe (UV) do zainicjowania reakcji utwardzania, co pozwala na szybsze cykle produkcyjne i mniejsze zużycie energii. Powłoki utwardzane promieniowaniem UV zapewniają również doskonałe pokrycie i przyczepność, zwiększając ogólną niezawodność powlekanych zespołów.
- Technologie kontroli powłok konforemnych: postęp w technologiach kontroli pomaga w ocenie jakości i wydajności powłok ochronnych. Zautomatyzowane systemy kontroli optycznej (AOI) z kamerami o wysokiej rozdzielczości i algorytmami analizy obrazu mogą wykrywać defekty, takie jak dziurki, pęcherzyki lub różnice w grubości powłoki. Poprawia to wydajność i niezawodność inspekcji, zapewniając stałą jakość powłoki.
- Cieńsze i lżejsze powłoki: Zapotrzebowanie na miniaturyzację i lekkie konstrukcje urządzeń elektronicznych napędza rozwój cieńszych i lżejszych powłok ochronnych. Powłoki te zapewniają wystarczającą ochronę przy jednoczesnym zminimalizowaniu wpływu na wagę i rozmiar powlekanych elementów. Cieńsze warstwy zapewniają również lepsze odprowadzanie ciepła, co ma kluczowe znaczenie w zastosowaniach wymagających dużej mocy.
Te postępy w technologii powlekania konforemnego przyczyniają się do rozwoju bardziej niezawodnych i trwałych urządzeń elektronicznych. Wraz z ciągłym rozwojem przemysłu elektronicznego oczekuje się, że trwające badania i innowacje w zakresie powłok konforemnych sprostają pojawiającym się wyzwaniom i umożliwią lepszą ochronę w różnych zastosowaniach.
Kwestie środowiskowe i powłoki ochronne
Kwestie środowiskowe odgrywają znaczącą rolę w opracowywaniu i stosowaniu powłok ochronnych. Ponieważ przemysł elektroniczny stale się rozwija, konieczne jest zrównoważenie korzyści płynących z powłok ochronnych z ich potencjalnym wpływem na środowisko. Oto kilka krytycznych aspektów związanych z ochroną środowiska i powłokami ochronnymi:
- Lotne związki organiczne (LZO): Tradycyjne powłoki ochronne na bazie rozpuszczalników często zawierają duże ilości LZO, przyczyniając się do zanieczyszczenia powietrza i szkodząc zdrowiu ludzkiemu. W odpowiedzi na to rośnie zapotrzebowanie na preparaty o niskiej zawartości LZO lub wolne od LZO. Powłoki na bazie wody i powłoki o niskiej zawartości LZO są opracowywane jako alternatywy w celu zmniejszenia wpływu na środowisko.
- Substancje niebezpieczne: Niektóre powłoki ochronne mogą zawierać niebezpieczne substancje, takie jak metale ciężkie lub trwałe zanieczyszczenia organiczne (TZO). Substancje te mogą mieć długotrwały wpływ na środowisko i stwarzać zagrożenie podczas produkcji, stosowania i utylizacji po zakończeniu eksploatacji. Aby temu zaradzić, przepisy i normy, takie jak dyrektywa o ograniczeniu stosowania substancji niebezpiecznych (RoHS), ograniczają stosowanie niektórych niebezpiecznych substancji w produktach elektronicznych.
- Ocena cyklu życia (LCA): ocena cyklu życia ocenia wpływ powłok ochronnych na środowisko w całym ich cyklu życia, od wydobycia surowców po utylizację. Pomaga identyfikować obszary wymagające poprawy i ukierunkowuje rozwój warstw przyjaznych dla środowiska. LCA uwzględnia zużycie energii, wyczerpywanie się zasobów, emisje i wytwarzanie odpadów.
- Formuły przyjazne dla środowiska: Producenci powłok ochronnych aktywnie opracowują formuły przyjazne dla środowiska, które minimalizują wpływ na środowisko. Obejmuje to stosowanie materiałów pochodzenia biologicznego, zasobów odnawialnych i przyjaznych dla środowiska rozpuszczalników. Biopowłoki pochodzące ze źródeł naturalnych oferują potencjalne korzyści w zakresie zmniejszonego śladu ekologicznego i lepszego zrównoważonego rozwoju.
- Recykling i zarządzanie odpadami: Właściwa utylizacja i recykling powłok ochronnych są niezbędne, aby zapobiec zanieczyszczeniu środowiska. Recykling komponentów i zespołów elektronicznych powinien uwzględniać usunięcie lub oddzielenie powłok ochronnych, aby umożliwić efektywne odzyskiwanie materiału. Rozwój technologii i procesów recyklingu pomaga sprostać wyzwaniom związanym z usuwaniem powłok i gospodarką odpadami.
- Przepisy dotyczące ochrony środowiska: ramy regulacyjne i standardy, takie jak rozporządzenie Unii Europejskiej w sprawie rejestracji, oceny, udzielania zezwoleń i stosowanych ograniczeń w zakresie chemikaliów (REACH), mają na celu ochronę zdrowia ludzkiego i środowiska przed potencjalnie szkodliwymi substancjami. Zgodność z tymi przepisami gwarantuje, że powłoki ochronne spełniają określone wymagania środowiskowe i normy bezpieczeństwa.
- Zrównoważone praktyki produkcyjne: Przyjęcie zrównoważonych praktyk produkcyjnych zmniejsza wpływ na środowisko związany z produkcją powłok ochronnych. Obejmuje to optymalizację wykorzystania zasobów, minimalizację wytwarzania odpadów, wdrażanie efektywnych energetycznie procesów i promowanie odnawialnych źródeł energii.
- Certyfikaty środowiskowe: Certyfikaty środowiskowe, takie jak ISO 14001, zapewniają organizacjom ramy zarządzania i ciągłego doskonalenia ich wyników w zakresie ochrony środowiska. Producenci powłok ochronnych mogą ubiegać się o certyfikację, aby wykazać swoje zaangażowanie w odpowiedzialność za środowisko i zrównoważone praktyki.
Wraz z ciągłym rozwojem branży coraz większy nacisk kładzie się na opracowywanie powłok ochronnych, które zapewniają odpowiednią ochronę przy jednoczesnym minimalizowaniu wpływu na środowisko. Producenci, organy regulacyjne i użytkownicy końcowi współpracują w celu promowania stosowania powłok przyjaznych dla środowiska oraz zapewnienia odpowiedzialnych i zrównoważonych praktyk w całym cyklu życia produktów elektronicznych.
Przyszłe perspektywy dla powłok ochronnych w elektronice
Przyszłe perspektywy dotyczące powłok ochronnych w elektronice są obiecujące, napędzane postępem technologicznym, rosnącym zapotrzebowaniem na wysokowydajne urządzenia elektroniczne oraz pojawiającymi się trendami w branży. Oto kilka kluczowych aspektów kształtujących przyszłość powłok ochronnych:
- Miniaturyzacja i wyższa integracja: Trend w kierunku mniejszych i bardziej kompaktowych urządzeń elektronicznych o wyższym poziomie integracji stanowi wyzwanie dla powłok ochronnych. Przyszłe powłoki muszą zapewniać odpowiednią ochronę przy jednoczesnym zachowaniu integralności zminiaturyzowanych komponentów i gęsto upakowanych zespołów. Obejmuje to opracowanie cieńszych warstw o lepszym pokryciu i dopasowywaniu się.
- Elastyczna i rozciągliwa elektronika: Rozwój elastycznej i rozciągliwej elektroniki, w tym urządzeń do noszenia, wymaga odpowiednich powłok, które są w stanie wytrzymać obciążenia mechaniczne i wielokrotne zginanie bez uszczerbku dla ich właściwości ochronnych. Przyszłe warstwy będą koncentrować się na elastyczności, trwałości i przyczepności, aby sprostać wyjątkowym wymaganiom tych powstających aplikacji.
- Zaawansowane materiały: opracowywanie nowych materiałów o ulepszonych właściwościach wpłynie na przyszłość powłok ochronnych. Obejmuje to stosowanie nanomateriałów, takich jak nanocząsteczki i nanokompozyty, w celu poprawy właściwości powłok pod względem odporności na wilgoć, przewodności elektrycznej, odprowadzania ciepła i właściwości barierowych. Zaawansowane materiały pozwolą powłokom sprostać zmieniającym się potrzebom urządzeń elektronicznych.
- Wielofunkcyjne powłoki: Zapotrzebowanie na wielofunkcyjne powłoki, które zapewniają wiele korzyści poza ochroną, będzie nadal rosło. Przyszłe warstwy mogą obejmować zdolności samoleczenia, przewodność cieplną, właściwości antystatyczne, właściwości przeciwdrobnoustrojowe lub funkcje zbierania energii. Powłoki wielofunkcyjne oferują lepszą wydajność, mniejszą złożoność i zwiększoną niezawodność zespołów elektronicznych.
- Względy środowiskowe: nacisk na zrównoważony rozwój ekologiczny i przepisy dotyczące substancji niebezpiecznych będą miały wpływ na przyszłość powłok ochronnych. Rozwój ekologicznych receptur o obniżonej zawartości lotnych związków organicznych (LZO) oraz stosowanie materiałów pochodzenia biologicznego stanie się bardziej powszechne. Strategie recyklingu i gospodarowania odpadami w przypadku powłok ochronnych również odegrają znaczącą rolę w minimalizowaniu wpływu na środowisko.
- Zaawansowane techniki aplikacji: Innowacje w technikach aplikacji zwiększą wydajność i jakość procesów powlekania konforemnego. Obejmuje to zrobotyzowane systemy dozowania, selektywne metody powlekania i zaawansowane technologie natryskiwania w celu zapewnienia precyzyjnego i równomiernego pokrycia powłoką, zmniejszenia strat materiału i poprawy wydajności.
- Zaawansowane metody kontroli i testowania: Wraz ze wzrostem złożoności zespołów elektronicznych pojawi się zapotrzebowanie na bardziej wyrafinowane metody kontroli i testowania powłok ochronnych. Obejmuje to opracowanie automatycznych systemów kontroli optycznej (AOI) z zaawansowanymi możliwościami obrazowania i analizy w celu wykrywania i oceny defektów powłoki, zmian grubości i jakości przyczepności.
- Normy branżowe i certyfikaty: Ciągły rozwój norm branżowych i certyfikacji będzie nadal kształtował przyszłość powłok ochronnych. Producenci i użytkownicy końcowi będą polegać na zaktualizowanych standardach, aby zapewnić jakość, niezawodność i zgodność niosek ze zmieniającymi się wymaganiami i przepisami.
Ogólnie rzecz biorąc, przyszłość powłok konforemnych w elektronice wygląda obiecująco, koncentrując się na poprawie wydajności, możliwości dostosowania do nowych technologii, zrównoważeniu środowiskowym oraz opracowaniu zaawansowanych materiałów i technik aplikacji. Te postępy umożliwią powłokom ochronnym zapewnienie solidnej ochrony urządzeń elektronicznych w zróżnicowanych i wymagających środowiskach.
Wnioski: Konformalne powłoki elektroniczne stanowią doskonałe rozwiązanie do ochrony urządzeń elektronicznych przed czynnikami środowiskowymi, które mogą doprowadzić do ich awarii lub nieprawidłowego działania. Wraz z rozwojem technologii zapotrzebowanie na bardziej efektywne i niezawodne powłoki konforemne będzie tylko rosło. Producenci, projektanci i inżynierowie muszą nadążać za najnowszymi osiągnięciami w tej dziedzinie, aby zapewnić optymalną ochronę swoich urządzeń elektronicznych. Powłoki ochronne są kluczowym elementem procesu produkcji elektroniki i mogą pomóc w wydłużeniu żywotności i wydajności urządzeń elektronicznych.