ایپوکسی کوٹنگ کی موصلیت
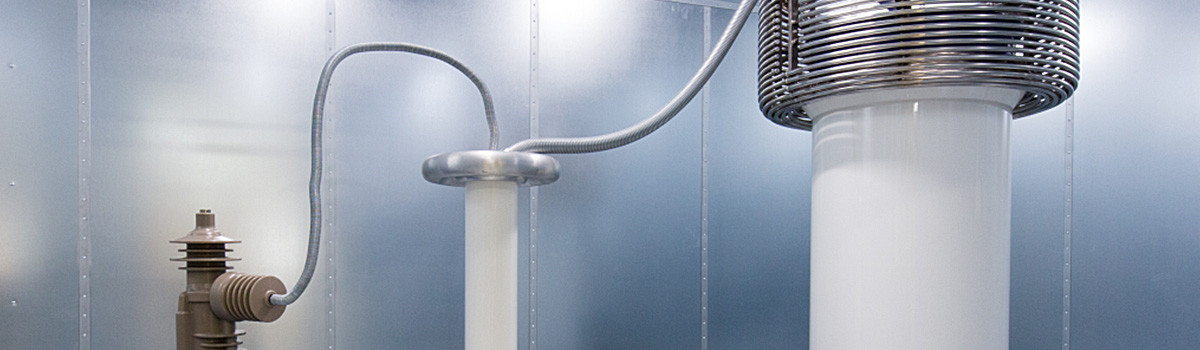
انسولیٹنگ ایپوکسی کوٹنگ ایک ورسٹائل اور وسیع پیمانے پر استعمال ہونے والا مواد ہے جس میں بہترین برقی موصلیت کی خصوصیات ہیں۔ مختلف صنعتیں عام طور پر اسے برقی اجزاء، سرکٹ بورڈز اور دیگر حساس آلات کو نمی، دھول، کیمیکلز اور جسمانی نقصان سے بچانے کے لیے استعمال کرتی ہیں۔ اس مضمون کا مقصد epoxy کوٹنگ کی موصلیت، اس کے استعمال، فوائد، اور مخصوص ضروریات کے لیے موزوں پرت کے انتخاب کے لیے اہم تحفظات پر روشنی ڈالنا ہے۔
ایپوکسی کوٹنگ کی موصلیت کو سمجھنا
انسولیٹنگ ایپوکسی کوٹنگ ایک حفاظتی کوٹنگ ہے جو مختلف سطحوں کو موصلیت اور برقی چالکتا مزاحمت فراہم کرتی ہے۔ یہ عام طور پر الیکٹرانکس، الیکٹریکل، آٹوموٹو، اور ایرو اسپیس صنعتوں میں برقی اجزاء کی حفاظت اور کارکردگی کو بڑھانے کے لیے استعمال ہوتا ہے۔
epoxy کوٹنگز کی موصلیت کا بنیادی مقصد conductive مواد کے درمیان برقی رو کے بہاؤ کو روکنا ہے۔ یہ ملعمع کاری ان سطحوں پر لگائی جاتی ہیں جو برقی شارٹ سرکٹس، سنکنرن، یا ماحولیاتی عوامل سے ہونے والے نقصان کا شکار ہیں۔ epoxy مواد ایک انسولیٹر کے طور پر کام کرتا ہے، الیکٹران کی منتقلی کو روکتا ہے اور برقی خرابی یا خرابی کے خطرے کو کم کرتا ہے۔
انسولیٹنگ ایپوکسی کوٹنگز عام طور پر ایپوکسی رال، تھرموسیٹنگ پولیمر، اور سخت کرنے والے ایجنٹ کے امتزاج سے بنتی ہیں۔ ایپوکسی رال بہترین چپکنے والی، کیمیائی مزاحمت، اور میکانکی طاقت فراہم کرتی ہے، جبکہ سخت کرنے والا ایجنٹ کراس لنکنگ ری ایکشن کو متحرک کرتا ہے جو مائع ایپوکسی کو ٹھوس، پائیدار کوٹنگ میں بدل دیتا ہے۔
ایپوکسی کوٹنگز کی موصلیت کا اطلاق کئی مراحل پر مشتمل ہے۔ سب سے پہلے، لیپت ہونے والی سطح کو اچھی طرح سے صاف کیا جاتا ہے اور مناسب چپکنے کو یقینی بنانے کے لیے تیار کیا جاتا ہے۔ کسی بھی گندگی، چکنائی، یا آلودگیوں کو صاف کرنا ضروری ہے تاکہ ایک صاف بانڈنگ سطح پیدا ہوسکے۔ پھر، ایپوکسی کوٹنگ کو کارخانہ دار کی ہدایات کے مطابق ملایا جاتا ہے اور اسپرے، برش، یا ڈپنگ تکنیک کا استعمال کرتے ہوئے سطح پر لگایا جاتا ہے۔
ایک بار لاگو ہونے کے بعد، ایپوکسی کوٹنگ ایک علاج کے عمل سے گزرتی ہے، جس کے دوران یہ سخت اور حفاظتی رکاوٹ بنتی ہے۔ علاج مختلف طریقوں سے حاصل کیا جا سکتا ہے، بشمول حرارت، کیمیکلز، یا دونوں۔ علاج کوٹنگ کی مکینیکل خصوصیات، چپکنے والی طاقت اور کیمیائی مزاحمت کو بڑھاتا ہے۔
epoxy کوٹنگز کی موصلیت کئی فوائد پیش کرتی ہے:
- وہ برقی موصلیت فراہم کرتے ہیں، برقی رو کے بہاؤ کو روکتے ہیں اور شارٹ سرکٹ یا برقی خرابی کے خطرے کو کم کرتے ہیں۔
- یہ کوٹنگز ماحولیاتی عوامل جیسے نمی، کیمیکلز اور کھرچنے کے خلاف بہترین تحفظ فراہم کرتی ہیں، جس سے لیپت اجزاء کی عمر بڑھ جاتی ہے۔
- epoxy کوٹنگز کی موصلیت سطحوں کے تھرمل استحکام اور شعلہ مزاحمت کو بڑھا سکتی ہے، جس سے وہ اعلی درجہ حرارت والے ماحول میں استعمال کے لیے موزوں ہیں۔
برقی موصلیت کی اہمیت
برقی موصلیت برقی نظام کی حفاظت، وشوسنییتا اور کارکردگی کو برقرار رکھنے میں ایک اہم کردار ادا کرتی ہے۔ اس میں مواد اور تکنیکوں کا استعمال شامل ہے تاکہ ترسیلی اجزاء یا سطحوں کے درمیان برقی رو کے بہاؤ کو روکا جا سکے۔ یہاں کچھ اہم وجوہات ہیں جو برقی موصلیت کی اہمیت کو اجاگر کرتی ہیں:
- برقی جھٹکوں سے تحفظ: برقی موصلیت لائیو کنڈکٹرز کے ساتھ براہ راست رابطے کو روکتی ہے، جس سے برقی جھٹکوں کا خطرہ کم ہوتا ہے۔ یہ ایک رکاوٹ کے طور پر کام کرتا ہے جو غیر منقولہ مواد کے ذریعے برقی رو کے بہاؤ کو روکتا ہے، لوگوں کو ممکنہ نقصان سے بچاتا ہے۔
- شارٹ سرکٹ اور برقی آگ کی روک تھام: موصلیت کنڈکٹیو مواد کے درمیان غیر ارادی برقی رابطے کو روکنے میں مدد کرتی ہے، جو شارٹ سرکٹ اور برقی آگ کا باعث بن سکتی ہے۔ تاروں، کیبلز، اور برقی اجزاء کی موصلیت برقی آرکنگ، چنگاریاں، اور زیادہ گرم ہونے کے امکانات کو کم کرتے ہیں، جس سے آگ لگنے اور سامان کے نقصان کے خطرے کو نمایاں طور پر کم کیا جاتا ہے۔
- بہتر برقی کارکردگی: اعلی ڈائی الیکٹرک طاقت اور کم برقی چالکتا کے ساتھ موصلیت کا مواد برقی نظام کی مجموعی کارکردگی کو بہتر بناتا ہے۔ وہ مناسب وولٹیج کی سطح کو برقرار رکھتے ہیں، رساو کو روکتے ہیں، اور سگنل کی مداخلت یا مسخ کو کم کرتے ہیں، برقی سرکٹس اور آلات کے بہترین کام کو یقینی بناتے ہیں۔
- ماحولیاتی عوامل سے تحفظ: برقی موصلیت کا مواد نمی، کیمیکل، دھول اور دیگر آلودگیوں کے خلاف مزاحمت کرتا ہے۔ یہ تحفظ بیرونی عوامل کی وجہ سے سنکنرن، انحطاط، اور موصلیت کی خرابی کو روکنے میں مدد کرتا ہے، اس طرح برقی اجزاء کی لمبی عمر اور وشوسنییتا کو برقرار رکھتا ہے۔
- توانائی کی کارکردگی میں اضافہ: موصلیت توانائی کے نقصان کو کم کرتی ہے اور برقی نظام کی کارکردگی کو بہتر بناتی ہے۔ موجودہ رساو کو روکنے سے، موصلیت بجلی کے ضیاع کو کم کرتی ہے اور برقی توانائی کی ترسیل اور تقسیم کو بڑھاتی ہے، جس کے نتیجے میں توانائی کی کھپت میں کمی اور آپریشنل اخراجات کم ہوتے ہیں۔
- حفاظتی معیارات اور ضوابط کی تعمیل: حکام اور صنعتی تنظیموں کی طرف سے مقرر کردہ حفاظتی معیارات اور ضوابط کو پورا کرنے کے لیے برقی موصلیت ضروری ہے۔ ان تقاضوں کی تعمیل اس بات کو یقینی بناتی ہے کہ برقی تنصیبات اور آلات کو عملے، املاک اور ماحول کے خطرات کو کم کرنے کے لیے ڈیزائن اور چلایا گیا ہے۔
- حساس آلات کا تحفظ: حساس الیکٹریکل اور الیکٹرانک آلات کو برقی رکاوٹوں اور وولٹیج کے اضافے سے بچانے کے لیے موصلیت اہم ہے۔ موصل مواد، جیسے وارنش یا کوٹنگز، نازک اجزاء کو برقی مقناطیسی مداخلت (EMI) اور الیکٹرو اسٹاٹک ڈسچارج (ESD) سے بچاتے ہیں، ان کی فعالیت کو محفوظ رکھتے ہیں اور ان کی عمر کو بڑھاتے ہیں۔
ایپوکسی کوٹنگ کی موصلیت کی ایپلی کیشنز
انسولیٹنگ ایپوکسی کوٹنگ ایک خصوصی کوٹنگ ہے جو بہترین برقی موصلیت کی خصوصیات پیش کرتی ہے، جو اسے مختلف ایپلی کیشنز کے لیے موزوں بناتی ہے۔ یہ کوٹنگ عام طور پر ایک epoxy رال پر مشتمل ہوتی ہے، جو موصلیت کی صلاحیتیں اور حفاظتی خصوصیات فراہم کرتی ہے۔ ایپوکسی کوٹنگ کی موصلیت کے کچھ اہم ایپلی کیشنز یہ ہیں:
- الیکٹرانکس اور برقی اجزاء: ایپوکسی کوٹنگ کی موصلیت الیکٹرانکس اور برقی صنعت میں بڑے پیمانے پر استعمال ہوتی ہے۔ اس کا اطلاق سرکٹ بورڈز، ٹرانسفارمرز، کیپسیٹرز، اور کنڈلیوں جیسے برقی موصلیت فراہم کرنے، شارٹ سرکٹ کو روکنے اور ان اجزاء کی مجموعی وشوسنییتا اور عمر کو بڑھانے کے لیے کیا جاتا ہے۔ کوٹنگ نمی، دھول اور دیگر ماحولیاتی آلودگیوں سے بھی بچاتی ہے۔
- پاور جنریشن اور ٹرانسمیشن: پاور جنریشن اور ٹرانسمیشن سسٹم میں epoxy کوٹنگز کی موصلیت بہت اہم ہے۔ بجلی کے رساو، کورونا ڈسچارج اور فلیش اوور کو روکنے کے لیے ان کو انسولیٹر، سوئچ گیئر، بس بارز اور دیگر ہائی وولٹیج آلات پر لگایا جاتا ہے۔ اعلی ڈائی الیکٹرک طاقت فراہم کرکے، کوٹنگ برقی انفراسٹرکچر کی سالمیت اور حفاظت کو برقرار رکھنے میں مدد کرتی ہے۔
- موٹرز اور جنریٹرز: الیکٹرک موٹرز اور جنریٹرز کو برقی خرابی کو روکنے اور موثر کارکردگی کو یقینی بنانے کے لیے موصلیت کی ضرورت ہوتی ہے۔ ان مشینوں کے وائنڈنگز اور دیگر اہم حصوں پر انسولیٹنگ ایپوکسی کوٹنگز لگائی جاتی ہیں۔ کوٹنگ برقی موصلیت کو بڑھاتی ہے، گرمی کی کھپت کو بہتر بناتی ہے، اور کیمیکلز، نمی اور مکینیکل تناؤ سے تحفظ فراہم کرتی ہے۔
- آٹوموٹو انڈسٹری: موصلی ایپوکسی کوٹنگز آٹوموٹیو سیکٹر میں مختلف ایپلی کیشنز تلاش کرتی ہیں۔ وہ گاڑیوں میں برقی رابطوں، ٹرمینلز اور وائرنگ ہارنیس کو انسولیٹ کرتے ہیں۔ یہ تہہ برقی سالمیت کو برقرار رکھنے میں مدد کرتی ہے، شارٹ سرکٹ کو روکتی ہے، اور سنکنرن، کمپن، اور تھرمل سائیکلنگ کے خلاف حفاظت کرتی ہے۔ یہ ہائبرڈ اور الیکٹرک گاڑیوں میں اجزاء کی موصلیت کے لیے بھی استعمال ہوتا ہے۔
- ایرو اسپیس اور ڈیفنس: ایرو اسپیس اور دفاعی شعبوں میں ایپوکسی کوٹنگز کی موصلیت بہت ضروری ہے۔ چیلنجنگ ماحول میں قابل اعتماد کارکردگی کو یقینی بنانے کے لیے ان کا اطلاق الیکٹرانک سسٹمز، ایونکس، ریڈار آلات اور مواصلاتی نظام پر کیا جاتا ہے۔ کوٹنگ برقی مداخلت، تابکاری، نمی اور انتہائی درجہ حرارت سے بچاتی ہے۔
- پرنٹ شدہ سرکٹ بورڈز (PCBs) کے لیے کوٹنگ: PCBs الیکٹرانک آلات کی ریڑھ کی ہڈی ہیں۔ Epoxy کوٹنگز PCBs کے سرکٹری اور سولڈر جوڑوں کو نمی، دھول اور دیگر آلودگیوں سے بچاتی ہیں۔ کوٹنگ کنڈکٹیو تہوں کے درمیان موصلیت بھی فراہم کرتی ہے، شارٹ سرکٹ کو روکتی ہے اور بورڈز کی مجموعی استحکام کو بڑھاتی ہے۔
- کیمیائی اور سنکنرن مزاحمت: epoxy کوٹنگز کی موصلیت بہترین کیمیائی مزاحمت پیش کرتی ہے اور سطحوں کو سنکنرن مادوں سے بچا سکتی ہے۔ وہ کیمیائی پروسیسنگ، تیل اور گیس، اور گندے پانی کے علاج میں استعمال ہوتے ہیں۔ کوٹنگ کیمیائی حملوں کو روکتی ہے، سامان کی لمبی عمر میں اضافہ کرتی ہے، اور دیکھ بھال کی ضروریات کو کم کرتی ہے۔
- الیکٹریکل انکیپسولیشن: انسولیٹنگ ایپوکسی کوٹنگز کو برقی انکیپسولیشن کے لیے استعمال کیا جاتا ہے، خاص طور پر ایسی ایپلی کیشنز میں جہاں نمی یا دیگر آلودگیوں سے خطرہ ہوتا ہے۔ یہ عام طور پر الیکٹرانک اجزاء، سینسرز، اور کنیکٹرز کو پاٹنگ اور انکیپسولیٹنگ کے لیے استعمال کیا جاتا ہے۔ کوٹنگ ماحولیاتی عوامل اور مکینیکل تناؤ کے خلاف ایک حفاظتی رکاوٹ بنتی ہے۔
الیکٹرانک اجزاء کے لئے تحفظ
الیکٹرانک اجزاء کی حفاظت ان کے مناسب کام اور لمبی عمر کو یقینی بنانے کے لیے بہت ضروری ہے۔ الیکٹرانک اجزاء اکثر ماحولیاتی عوامل جیسے درجہ حرارت، نمی، بجلی کے شور اور جسمانی دباؤ کے لیے حساس ہوتے ہیں۔ مناسب تحفظ کے ساتھ، ان اجزاء کو محفوظ کیا جا سکتا ہے اور یہاں تک کہ ناقابل استعمال قرار دیا جا سکتا ہے۔ یہاں کچھ معیاری طریقے اور تکنیک ہیں جو الیکٹرانک اجزاء کی حفاظت کے لیے استعمال کی جاتی ہیں:
- ملفوظات: الیکٹرانک اجزاء کو حفاظتی دیواروں میں رکھا جا سکتا ہے، جیسے کیس، الماریاں، یا بکس۔ حصے دھول، نمی اور دیگر آلودگیوں کے خلاف جسمانی تحفظ فراہم کرتے ہیں۔ وہ اجزاء کو حادثاتی اثرات یا غلط استعمال سے بھی بچاتے ہیں۔
- EMI/RFI شیلڈنگ: برقی مقناطیسی مداخلت (EMI) اور ریڈیو فریکوئنسی مداخلت (RFI) الیکٹرانک اجزاء کے باقاعدہ کام میں خلل ڈال سکتی ہے۔ EMI/RFI شیلڈنگ میں فیراڈے کیج اثر پیدا کرنے کے لیے ترسیلی مواد، جیسے دھاتی کوٹنگز یا کنڈکٹیو گاسکیٹ کا استعمال شامل ہے۔ یہ شیلڈنگ بیرونی برقی مقناطیسی سگنلز کو حساس الیکٹرانکس میں مداخلت کرنے سے روکتی ہے۔
- تھرمل مینجمنٹ: الیکٹرانک اجزاء آپریشن کے دوران گرمی پیدا کرتے ہیں، اور ضرورت سے زیادہ گرمی ان کی کارکردگی اور وشوسنییتا کو کم کر سکتی ہے۔ تھرمل مینجمنٹ تکنیک جیسے ہیٹ سنک، پنکھے اور تھرمل پیڈ گرمی کو ختم کرنے اور بہترین آپریٹنگ درجہ حرارت کو برقرار رکھنے میں مدد کرتے ہیں۔ ہیٹ سنک گرمی کو جذب اور ختم کرتے ہیں، جبکہ پنکھے ہوا کے بہاؤ کو آسان بناتے ہیں۔ تھرمل پیڈ موثر حرارت کی منتقلی کے لیے جزو اور ہیٹ سنک کے درمیان تھرمل انٹرفیس فراہم کرتے ہیں۔
- سرج پروٹیکشن: بجلی گرنے، بجلی کی خرابیوں، یا سوئچنگ ٹرانزینٹس کی وجہ سے ہونے والے بجلی کے اضافے الیکٹرانک اجزاء کو نقصان پہنچا سکتے ہیں۔ سرج پروٹیکشن ڈیوائسز، جیسے سرج سوپریسرز یا میٹل آکسائیڈ ویریسٹرز (MOVs)، اراکین کی حفاظت کے لیے اضافی وولٹیج کو موڑ دیتے ہیں۔ یہ آلات وولٹیج کی سطح کو محدود کرتے ہیں اور عارضی اسپائکس کو حساس اجزاء تک پہنچنے سے روکتے ہیں۔
- ماحولیاتی سگ ماہی: مخصوص ایپلی کیشنز میں، الیکٹرانک اجزاء کو سخت ماحولیاتی حالات، جیسے نمی، کیمیکلز، یا انتہائی درجہ حرارت سے تحفظ کی ضرورت ہوتی ہے۔ ماحولیاتی سگ ماہی کی تکنیک، جیسے کنفارمل کوٹنگز، پوٹنگ کمپاؤنڈز، یا ہرمیٹک سیلنگ، ایک رکاوٹ پیدا کرتی ہے جو ان عناصر سے اجزاء کی حفاظت کرتی ہے۔
- سرکٹ پروٹیکشن: الیکٹرانک اجزاء اوور وولٹیج، اوور کرنٹ، اور الیکٹرو سٹیٹک ڈسچارج (ESD) کے لیے خطرناک ہو سکتے ہیں۔ سرکٹ پروٹیکشن ڈیوائسز، جیسے فیوز، سرکٹ بریکرز، عارضی وولٹیج سوپریسرز (TVS ڈایڈس) اور ESD پروٹیکشن ڈائیوڈس کو اجزاء سے دور ضرورت سے زیادہ کرنٹ، وولٹیج، یا جامد چارجز کو محدود اور ری ڈائریکٹ کرنے کے لیے استعمال کیا جاتا ہے۔
- گراؤنڈنگ اور بانڈنگ: الیکٹرانک اجزاء کو برقی شور سے بچانے اور حفاظت کو یقینی بنانے کے لیے مناسب گراؤنڈنگ اور بانڈنگ تکنیک ضروری ہیں۔ گراؤنڈنگ غیر مطلوبہ برقی چارجز کی کھپت کا راستہ فراہم کرتی ہے۔ اس کے برعکس، بانڈنگ ممکنہ اختلافات کو کم کرتی ہے جو نقصان کا سبب بن سکتے ہیں۔ گراؤنڈنگ اور بانڈنگ تکنیکوں میں زمینی طیاروں، تاروں اور عام زمینی رابطوں کا استعمال شامل ہے۔
- فلٹرنگ: برقی شور اور مختلف ذرائع سے مداخلت الیکٹرانک اجزاء کی کارکردگی کو متاثر کر سکتی ہے۔ فلٹرز جیسے لو پاس، ہائی پاس، یا برقی مقناطیسی مداخلت کے فلٹرز ناپسندیدہ سگنلز کو ختم یا کم کر سکتے ہیں اور اراکین کو صاف بجلی کی فراہمی کو یقینی بنا سکتے ہیں۔
- اینٹی سٹیٹک اقدامات: الیکٹرو سٹیٹک ڈسچارج (ESD) الیکٹرانک اجزاء کو نمایاں نقصان پہنچا سکتا ہے۔ اینٹی سٹیٹک اقدامات، جیسے ESD-محفوظ ورک سٹیشن، کلائی کے پٹے، اور پیکیجنگ مواد، جامد چارجز کو حساس حصوں میں جمع ہونے اور خارج ہونے سے روکتے ہیں۔
- باقاعدہ دیکھ بھال اور جانچ: الیکٹرانک اجزاء کے ساتھ ممکنہ مسائل کی نشاندہی کرنے کے لیے باقاعدہ دیکھ بھال، معائنہ اور جانچ ضروری ہے۔ متواتر جانچ اس بات کو یقینی بناتی ہے کہ حفاظتی اقدامات صحیح طریقے سے کام کرتے ہیں اور کسی بھی خرابی یا ناکامی کو فوری طور پر دور کیا جاتا ہے۔
ان حفاظتی تکنیکوں کو استعمال کرکے الیکٹرانک اجزاء کو ماحولیاتی خطرات، برقی رکاوٹوں اور جسمانی نقصان سے محفوظ رکھا جا سکتا ہے۔ یہ ان کے قابل اعتماد آپریشن کو یقینی بناتا ہے اور ان کی عمر کو بڑھاتا ہے، جس کی وجہ سے کارکردگی بہتر ہوتی ہے اور ڈاؤن ٹائم کم ہوتا ہے۔
سرکٹ بورڈ کوٹنگ
سرکٹ بورڈ کوٹنگ الیکٹرانکس مینوفیکچرنگ میں ایک اہم عمل ہے جس میں پرنٹ شدہ سرکٹ بورڈ (PCB) پر حفاظتی تہہ لگانا شامل ہے۔ یہ کوٹنگ موصلیت فراہم کرتی ہے، ماحولیاتی عوامل سے تحفظ فراہم کرتی ہے، اور سرکٹری کی وشوسنییتا اور لمبی عمر کو بڑھاتی ہے۔ اس مضمون میں، ہم سرکٹ بورڈ کوٹنگ کی اہمیت اور استعمال ہونے والی کوٹنگز کی مختلف اقسام کا جائزہ لیں گے۔
سرکٹ بورڈ کوٹنگ کا بنیادی مقصد مختلف ماحولیاتی دباؤ سے نازک الیکٹرانک اجزاء کی حفاظت کرنا ہے۔ ان دباؤ میں نمی، دھول، گندگی، کیمیکلز اور درجہ حرارت میں اتار چڑھاؤ شامل ہیں، جو سنکنرن، شارٹ سرکٹ اور دیگر ناکامیوں کا باعث بن سکتے ہیں۔ کوٹنگ ایک رکاوٹ کا کام کرتی ہے، ان نقصان دہ عناصر کو سرکٹری تک پہنچنے اور نقصان پہنچانے سے روکتی ہے۔
سرکٹ بورڈز کے لیے کوٹنگز کی کئی اقسام دستیاب ہیں، ہر ایک درخواست کی ضروریات کے لحاظ سے مخصوص فوائد پیش کرتی ہے۔ ایک عام قسم کنفارمل کوٹنگ ہے، جو ایک پتلی حفاظتی فلم ہے جو براہ راست PCB کی سطح پر لگائی جاتی ہے۔ کنفارمل کوٹنگز مختلف مواد سے بن سکتی ہیں، بشمول ایکریلیکس، یوریتھینز، سلیکونز، اور ایپوکسی رال۔ یہ کوٹنگز سرکٹ بورڈ کی شکل کے مطابق ہوتی ہیں، تمام اجزاء اور بے نقاب نشانات کو ڈھانپتی ہیں، اور نمی، دھول اور کیمیائی آلودگیوں سے بہترین تحفظ فراہم کرتی ہیں۔
کوٹنگ کی ایک اور قسم انکیپسولیشن یا پوٹنگ کمپاؤنڈ ہے، جو ایک موٹا مواد ہے جو پورے پی سی بی کا احاطہ کرتا ہے، اسے مکمل طور پر سمیٹتا ہے۔ برتن بنانے والے مرکبات عام طور پر ایپوکسی یا پولیوریتھین سے بنے ہوتے ہیں اور مکینیکل تناؤ، کمپن اور انتہائی درجہ حرارت کے خلاف اعلیٰ تحفظ فراہم کرتے ہیں۔ وہ عام طور پر ایسی ایپلی کیشنز میں استعمال ہوتے ہیں جہاں سرکٹ بورڈ سخت ماحول یا جسمانی تناؤ کی اعلی سطح کے سامنے آتے ہیں۔
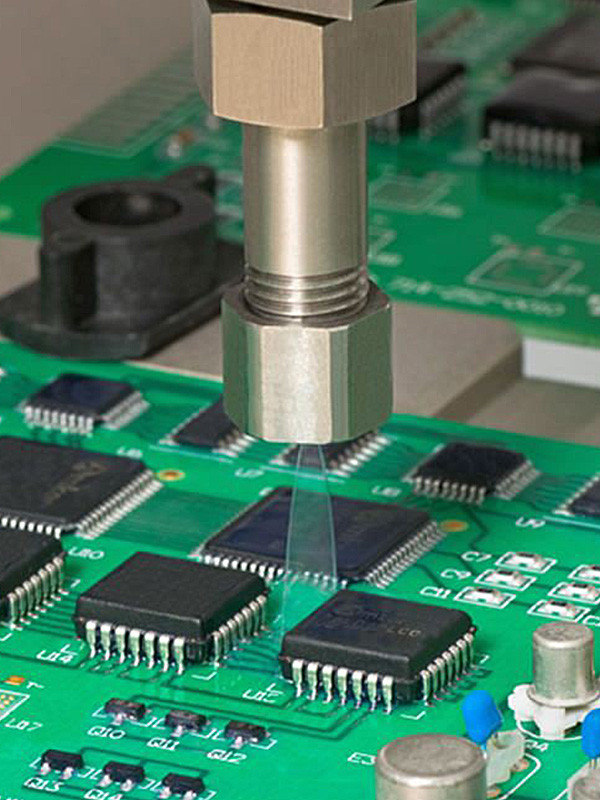
کوٹنگ کے عمل میں یکساں کوریج اور مناسب چپکنے کو یقینی بنانے کے لیے احتیاط سے استعمال کی تکنیک شامل ہوتی ہے۔ مختلف طریقے استعمال کیے جا سکتے ہیں، جیسے سپرے کوٹنگ، ڈِپ کوٹنگ، یا سلیکٹیو کوٹنگ۔ سپرے کوٹنگ میں پی سی بی پر کوٹنگ کے مواد کی باریک دھول لگانے کے لیے اسپرے گن یا ایٹمائزر کا استعمال شامل ہے۔ دوسری طرف، ڈِپ کوٹنگ پی سی بی کو کوٹنگ میٹریل کے غسل میں ڈبو دیتی ہے، جس سے یہ بورڈ کو مکمل طور پر کوٹ کر سکتا ہے۔ سلیکٹیو کوٹنگ ایک درست طریقہ ہے جو کوٹنگ کو صرف PCB کے مخصوص علاقوں پر لاگو کرتا ہے، دوسرے اجزاء کو رسائی کے لیے بغیر کوٹنگ کے چھوڑ دیتا ہے۔
ماحولیاتی تحفظ کے علاوہ، سرکٹ بورڈ کوٹنگز برقی موصلیت کی خصوصیات بھی پیش کرتی ہیں۔ کوٹنگ کے مواد میں ایک اعلی ڈائی الیکٹرک طاقت ہے، جو قریب سے فاصلے والے نشانات یا اجزاء کے درمیان کرنٹ کے رساو کو روکتی ہے۔ یہ خاص طور پر ہائی وولٹیج ایپلی کیشنز میں اہم ہے جہاں برقی تنہائی اہم ہے۔
موٹر اور ٹرانسفارمر کی موصلیت
الیکٹرانک اجزاء کی حفاظت ان کے مناسب کام اور لمبی عمر کو یقینی بنانے کے لیے بہت ضروری ہے۔ الیکٹرانک اجزاء اکثر ماحولیاتی عوامل جیسے درجہ حرارت، نمی، بجلی کے شور اور جسمانی دباؤ کے لیے حساس ہوتے ہیں۔ مناسب تحفظ کے ساتھ، ان اجزاء کو محفوظ کیا جا سکتا ہے اور یہاں تک کہ ناقابل استعمال قرار دیا جا سکتا ہے۔ یہاں کچھ معیاری طریقے اور تکنیک ہیں جو الیکٹرانک اجزاء کی حفاظت کے لیے استعمال کی جاتی ہیں:
- ملفوظات: الیکٹرانک اجزاء کو حفاظتی دیواروں میں رکھا جا سکتا ہے، جیسے کیس، الماریاں، یا بکس۔ حصے دھول، نمی اور دیگر آلودگیوں کے خلاف جسمانی تحفظ فراہم کرتے ہیں۔ وہ اجزاء کو حادثاتی اثرات یا غلط استعمال سے بھی بچاتے ہیں۔
- EMI/RFI شیلڈنگ: برقی مقناطیسی مداخلت (EMI) اور ریڈیو فریکوئنسی مداخلت (RFI) الیکٹرانک اجزاء کے باقاعدہ کام میں خلل ڈال سکتی ہے۔ EMI/RFI شیلڈنگ میں فیراڈے کیج اثر پیدا کرنے کے لیے ترسیلی مواد، جیسے دھاتی کوٹنگز یا کنڈکٹیو گاسکیٹ کا استعمال شامل ہے۔ یہ شیلڈنگ بیرونی برقی مقناطیسی سگنلز کو حساس الیکٹرانکس میں مداخلت کرنے سے روکتی ہے۔
- تھرمل مینجمنٹ: الیکٹرانک اجزاء آپریشن کے دوران گرمی پیدا کرتے ہیں، اور ضرورت سے زیادہ گرمی ان کی کارکردگی اور وشوسنییتا کو کم کر سکتی ہے۔ تھرمل مینجمنٹ کی تکنیک جیسے ہیٹ سنک، پنکھے اور پیڈ گرمی کو ختم کرنے اور بہترین آپریٹنگ درجہ حرارت کو برقرار رکھنے میں مدد کرتے ہیں۔ ہیٹ سنک گرمی کو جذب اور ختم کرتے ہیں، جبکہ پنکھے ہوا کے بہاؤ کو آسان بناتے ہیں۔ تھرمل پیڈ موثر حرارت کی منتقلی کے لیے جزو اور ہیٹ سنک کے درمیان تھرمل انٹرفیس فراہم کرتے ہیں۔
- سرج پروٹیکشن: بجلی گرنے، بجلی کی خرابیوں، یا سوئچنگ ٹرانزینٹس کی وجہ سے ہونے والے بجلی کے اضافے الیکٹرانک اجزاء کو نقصان پہنچا سکتے ہیں۔ سرج پروٹیکشن ڈیوائسز، جیسے سرج سوپریسرز یا میٹل آکسائیڈ ویریسٹرز (MOVs)، اراکین کی حفاظت کے لیے اضافی وولٹیج کو موڑ دیتے ہیں۔ یہ آلات وولٹیج کی سطح کو محدود کرتے ہیں اور عارضی اسپائکس کو حساس اجزاء تک پہنچنے سے روکتے ہیں۔
- ماحولیاتی سگ ماہی: مخصوص ایپلی کیشنز میں، الیکٹرانک اجزاء کو سخت ماحولیاتی حالات، جیسے نمی، کیمیکلز، یا انتہائی درجہ حرارت سے تحفظ کی ضرورت ہوتی ہے۔ ماحولیاتی سگ ماہی کی تکنیک، جیسے کنفارمل کوٹنگز، پوٹنگ کمپاؤنڈز، یا ہرمیٹک سیلنگ، ایک رکاوٹ پیدا کرتی ہے جو ان عناصر سے اجزاء کی حفاظت کرتی ہے۔
- سرکٹ پروٹیکشن: الیکٹرانک اجزاء اوور وولٹیج، اوور کرنٹ، اور الیکٹرو سٹیٹک ڈسچارج (ESD) کے لیے خطرناک ہو سکتے ہیں۔ سرکٹ پروٹیکشن ڈیوائسز، جیسے فیوز، سرکٹ بریکرز، عارضی وولٹیج سوپریسرز (TVS ڈایڈس) اور ESD پروٹیکشن ڈائیوڈس کو اجزاء سے دور ضرورت سے زیادہ کرنٹ، وولٹیج، یا جامد چارجز کو محدود اور ری ڈائریکٹ کرنے کے لیے استعمال کیا جاتا ہے۔
- گراؤنڈنگ اور بانڈنگ: الیکٹرانک اجزاء کو برقی شور سے بچانے اور حفاظت کو یقینی بنانے کے لیے مناسب گراؤنڈنگ اور بانڈنگ تکنیک ضروری ہیں۔ گراؤنڈنگ غیر مطلوبہ برقی چارجز کی کھپت کا راستہ فراہم کرتی ہے۔ اس کے برعکس، بانڈنگ ممکنہ اختلافات کو کم کرتی ہے جو نقصان کا سبب بن سکتے ہیں۔ گراؤنڈنگ اور بانڈنگ تکنیکوں میں زمینی طیاروں، تاروں اور عام زمینی رابطوں کا استعمال شامل ہے۔
- فلٹرنگ: برقی شور اور مختلف ذرائع سے مداخلت الیکٹرانک اجزاء کی کارکردگی کو متاثر کر سکتی ہے۔ فلٹرز جیسے لو پاس، ہائی پاس، یا برقی مقناطیسی مداخلت کے فلٹرز ناپسندیدہ سگنلز کو ختم یا کم کر سکتے ہیں اور اراکین کو صاف بجلی کی فراہمی کو یقینی بنا سکتے ہیں۔
- اینٹی سٹیٹک اقدامات: الیکٹرو سٹیٹک ڈسچارج (ESD) الیکٹرانک اجزاء کو نمایاں نقصان پہنچا سکتا ہے۔ اینٹی سٹیٹک اقدامات، جیسے ESD-محفوظ ورک سٹیشن، کلائی کے پٹے، اور پیکیجنگ مواد، جامد چارجز کو حساس حصوں میں جمع ہونے اور خارج ہونے سے روکتے ہیں۔
- باقاعدہ دیکھ بھال اور جانچ: الیکٹرانک اجزاء کے ساتھ ممکنہ مسائل کی نشاندہی کرنے کے لیے باقاعدہ دیکھ بھال، معائنہ اور جانچ ضروری ہے۔ متواتر جانچ اس بات کو یقینی بناتی ہے کہ حفاظتی اقدامات صحیح طریقے سے کام کرتے ہیں اور کسی بھی خرابی یا ناکامی کو فوری طور پر دور کیا جاتا ہے۔
ان حفاظتی تکنیکوں کو استعمال کرکے الیکٹرانک اجزاء کو ماحولیاتی خطرات، برقی رکاوٹوں اور جسمانی نقصان سے محفوظ رکھا جا سکتا ہے۔ یہ ان کے قابل اعتماد آپریشن کو یقینی بناتا ہے اور ان کی عمر کو بڑھاتا ہے، جس کی وجہ سے کارکردگی بہتر ہوتی ہے اور ڈاؤن ٹائم کم ہوتا ہے۔
کیبل اور تار کی موصلیت
کیبل اور تار کی موصلیت تحفظ، موصلیت اور حفاظت فراہم کرکے برقی نظام میں اہم کردار ادا کرتی ہے۔ اس سے مراد بیرونی غلاف یا جیکٹ ہے جو برقی کنڈکٹرز کو گھیرے ہوئے ہے، غیر ارادی علاقوں میں برقی رو کے بہاؤ کو روکتی ہے اور کنڈکٹرز کو ماحولیاتی عوامل سے بچاتی ہے۔ موصلیت کے مواد کا انتخاب وولٹیج کی درجہ بندی، درجہ حرارت کی حد، ماحولیاتی حالات، اور مطلوبہ اطلاق جیسے عوامل پر منحصر ہے۔
عام طور پر استعمال ہونے والے موصلیت کے مواد میں سے ایک تھرمو پلاسٹک ہے۔ تھرمو پلاسٹک موصلیت لچکدار، پائیدار، اور رگڑ اور کیمیکلز کے خلاف مزاحم ہے۔ Polyvinyl chloride (PVC) ایک مقبول تھرمو پلاسٹک مواد ہے جو اس کی سستی اور وسیع پیمانے پر استعمال کے لیے جانا جاتا ہے۔ یہ عام طور پر کم وولٹیج ایپلی کیشنز جیسے گھریلو وائرنگ اور عام مقصد کی کیبلز میں استعمال ہوتا ہے۔ پیویسی موصلیت اچھی برقی خصوصیات فراہم کرتی ہے اور شعلہ retardant ہے.
ایک اور وسیع پیمانے پر استعمال شدہ موصلیت کا مواد تھرموسیٹ ہے۔ تھرموپلاسٹک کے برعکس، تھرموسیٹ کی موصلیت کو ایک بار سیٹ ہونے کے بعد دوبارہ پگھلا یا اصلاح نہیں کیا جا سکتا۔ کراس لنکڈ پولیتھیلین (XLPE) عام طور پر استعمال ہونے والا تھرموسیٹ مواد ہے جو اپنی بہترین برقی خصوصیات، اعلی درجہ حرارت کے خلاف مزاحمت، اور نمی اور کیمیکلز کے خلاف مزاحمت کے لیے جانا جاتا ہے۔ XLPE موصلیت اکثر درمیانے اور ہائی وولٹیج پاور کیبلز میں استعمال ہوتی ہے، بشمول زیر زمین ٹرانسمیشن اور ڈسٹری بیوشن سسٹم۔
تھرموپلاسٹک اور تھرموسیٹس کے علاوہ، دیگر خصوصی موصلیت کا مواد مخصوص ایپلی کیشنز کے لیے ڈیزائن کیا گیا ہے۔ مثال کے طور پر، سلیکون ربڑ کی موصلیت اپنے اعلی درجہ حرارت کی مزاحمت کے لیے جانا جاتا ہے، جو اسے انتہائی ماحول جیسے ایرو اسپیس اور آٹوموٹو صنعتوں میں استعمال کرنے کے لیے موزوں بناتا ہے۔ فلورو پولیمرز، جیسے پولیٹیٹرا فلوروتھیلین (PTFE)، اعلی درجہ حرارت اور اعلی تعدد ایپلی کیشنز میں ان کی بہترین برقی خصوصیات اور کیمیکلز اور گرمی کے خلاف مزاحمت کی وجہ سے استعمال ہوتے ہیں۔
وولٹیج کی درجہ بندی اور کیبل یا تار کا مطلوبہ استعمال موصلیت کی تہہ کی موٹائی کا تعین کرتا ہے۔ زیادہ وولٹیج ایپلی کیشنز کو اعلی برقی فیلڈز کو برداشت کرنے اور برقی خرابی کو روکنے کے لیے موٹی موصلیت کی تہوں کی ضرورت ہوتی ہے۔ موصلیت کی موٹائی کیبل کے مجموعی قطر اور لچک کو بھی متاثر کرتی ہے۔
موصلیت کے مواد کو ان کی کارکردگی اور حفاظت کو یقینی بنانے کے لیے مختلف ٹیسٹوں کا نشانہ بنایا جاتا ہے۔ ان ٹیسٹوں میں برقی خصوصیات کی پیمائش جیسے ڈائی الیکٹرک طاقت اور موصلیت کی مزاحمت، درجہ حرارت کے تغیرات کے خلاف مزاحمت کا اندازہ لگانا، شعلہ مزاحمت، اور میکانکی خصوصیات جیسے لچک اور کھرچنے کی مزاحمت شامل ہو سکتی ہے۔ بجلی کے نظام کی وشوسنییتا اور حفاظت کو یقینی بنانے کے لیے صنعت کے معیارات اور ضوابط کی تعمیل ضروری ہے۔
ایرو اسپیس اور آٹوموٹو انڈسٹریز
ایرو اسپیس اور آٹوموٹو دونوں صنعتوں میں انسولیٹنگ ایپوکسی کوٹنگز ضروری ایپلی کیشنز تلاش کرتی ہیں۔ یہ ملمع کاری متعدد فوائد پیش کرتی ہیں، بشمول برقی موصلیت، سنکنرن مزاحمت، اور تھرمل تحفظ۔ یہ جواب 450 الفاظ کی حد پر عمل کرتے ہوئے ایرو اسپیس اور آٹوموٹیو سیکٹرز کے اندر epoxy کوٹنگز کی موصلیت کے اہم استعمال کو تلاش کرے گا۔
ایرو اسپیس انڈسٹری:
- ہوائی جہاز کے ڈھانچے: epoxy کوٹنگز کی موصلیت ہوائی جہاز کے ڈھانچے کو ماحولیاتی عوامل، جیسے نمی، کیمیکلز اور UV تابکاری سے بچاتی ہے۔ یہ ملعمع کاری ایک رکاوٹ کے طور پر کام کرتی ہے، سنکنرن کو روکتی ہے اور اہم اجزاء کی عمر کو بڑھاتی ہے۔ مزید برآں، وہ برقی موصلیت فراہم کرتے ہیں، برقی مداخلت کے خطرے کو کم کرتے ہیں اور حفاظت کو بڑھاتے ہیں۔
- الیکٹرانک اجزاء: ایرو اسپیس سسٹمز میں الیکٹرانک اجزاء بشمول سرکٹ بورڈز، کنیکٹرز اور سینسرز پر انسولیٹنگ ایپوکسی کوٹنگز لگائی جاتی ہیں۔ یہ کوٹنگز بہترین برقی موصلیت کی خصوصیات پیش کرتی ہیں، حساس الیکٹرانکس کو جامد خارج ہونے والے مادہ، نمی اور آلودگیوں سے بچاتی ہیں۔ پرتیں گرمی کی کھپت میں بھی مدد کرتی ہیں، الیکٹرانک سسٹم کی بہترین کارکردگی اور وشوسنییتا کو یقینی بناتی ہیں۔
- Radomes: Radomes، جو کہ ریڈار اینٹینا کے لیے حفاظتی حصار ہیں، سگنل کی شفافیت اور ماحولیاتی عناصر کے خلاف تحفظ کو یقینی بنانے کے لیے epoxy کوٹنگز کی موصلیت کی ضرورت ہوتی ہے۔ یہ کوٹنگز ریڈوم کی ساختی سالمیت کو برقرار رکھتے ہوئے برقی مقناطیسی مداخلت (EMI) کے خلاف موصلیت فراہم کرتی ہیں۔ وہ کٹاؤ اور موسم کے خلاف مزاحمت بھی پیش کرتے ہیں، ریڈار سسٹم کی کارکردگی کو برقرار رکھتے ہیں۔
گاڑیوں کی صنعت:
- الیکٹرک وہیکل (EV) بیٹریاں: برقی گاڑیوں کی بیٹریوں کی حفاظت کے لیے epoxy کوٹنگز کی موصلیت بہت ضروری ہے۔ یہ کوٹنگز نمی اور آلودگیوں کے داخل ہونے سے روکتی ہیں، بیٹری کے خلیات کی سالمیت اور لمبی عمر کو یقینی بناتی ہیں۔ وہ برقی موصلیت بھی فراہم کرتے ہیں، شارٹ سرکٹ کے خطرے کو کم کرتے ہیں اور ای وی کی حفاظت کو بڑھاتے ہیں۔
- انجن کے اجزاء: انجن کے اجزاء کو سنکنرن، گرمی اور کیمیائی نمائش سے بچانے کے لیے انسولیٹنگ ایپوکسی کوٹنگز کا استعمال کیا جاتا ہے۔ یہ کوٹنگز انجن کے پرزوں کی استحکام اور کارکردگی کو بہتر کرتی ہیں، جیسے سلنڈر ہیڈز، انٹیک مینی فولڈز، اور ایگزاسٹ سسٹم۔ پرتیں تھرمل موصلیت بھی فراہم کرتی ہیں، حرارت کی منتقلی کو کم کرتی ہیں اور انجن کی کارکردگی کو بہتر کرتی ہیں۔
- الیکٹریکل سسٹمز: گاڑیوں کے اندر موجود برقی نظاموں پر انسولیٹنگ ایپوکسی کوٹنگز لگائی جاتی ہیں، بشمول وائرنگ ہارنیس، کنیکٹر اور سرکٹ بورڈ۔ یہ کوٹنگز برقی موصلیت پیش کرتی ہیں، شارٹ سرکٹ کو روکتی ہیں اور قابل اعتماد کارکردگی کو یقینی بناتی ہیں۔ وہ نمی، کیمیکلز اور درجہ حرارت کے تغیرات سے بھی حفاظت کرتے ہیں، جس سے برقی اجزاء کی عمر بڑھ جاتی ہے۔
- چیسس اور انڈر باڈی پروٹیکشن: انسولیٹنگ ایپوکسی کوٹنگز گاڑیوں کے چیسس اور انڈر باڈی کو نمی، نمک اور سڑک کے ملبے کی وجہ سے ہونے والے سنکنرن سے بچاتی ہیں۔ یہ کوٹنگز ایک مضبوط رکاوٹ بنتی ہیں، جو سنکنرن مادوں کے داخلے کو روکتی ہیں اور گاڑی کی عمر کو بڑھاتی ہیں۔ اس کے علاوہ، وہ تھرمل موصلیت فراہم کرتے ہیں، گرمی کی منتقلی کو کم کرتے ہیں اور مسافروں کے آرام کو بہتر بناتے ہیں۔
میرین اور آف شور ایپلی کیشنز
سنکنرن، کھرچنے، اور برقی چالکتا کے خلاف حفاظتی رکاوٹ فراہم کرکے سمندری اور آف شور ایپلی کیشنز میں انسولیٹنگ ایپوکسی کوٹنگز ایک اہم کردار ادا کرتی ہیں۔ یہ خصوصی کوٹنگز بے شمار فوائد پیش کرتی ہیں اور سمندری اور غیر ملکی ماحول میں وسیع پیمانے پر استعمال ہوتی ہیں۔
- میرین ویسلز: بحری جہازوں بشمول بحری جہازوں، بجروں اور آف شور پلیٹ فارمز پر انسولیٹنگ ایپوکسی کوٹنگز کا بڑے پیمانے پر استعمال کیا جاتا ہے۔ یہ کوٹنگز کھارے پانی، کیمیکلز اور سمندری جانداروں کے سنکنرن اثرات سے ہلوں کی حفاظت کرتی ہیں۔ وہ ایک پائیدار حفاظتی رکاوٹ فراہم کرتے ہیں جو برتن کی عمر کو بڑھاتا ہے اور دیکھ بھال کی ضروریات کو کم کرتا ہے۔
- آف شور آئل اینڈ گیس پلیٹ فارمز: آف شور تیل اور گیس کی تلاش اور پیداوار میں، پلیٹ فارمز اور آلات کی سالمیت کو برقرار رکھنے کے لیے epoxy کوٹنگز کی موصلیت ضروری ہے۔ وہ سخت ماحولیاتی حالات کے خلاف ڈھانچے کی حفاظت کرتے ہیں، بشمول سنکنرن نمکین پانی، اعلی درجہ حرارت، اور کیمیائی نمائش۔ موصل کوٹنگز برقی موصلیت بھی فراہم کرتی ہیں، برقی کرنٹ کو حساس آلات میں مداخلت سے روکتی ہیں اور حفاظت کو یقینی بناتی ہیں۔
- پائپ لائنز اور سب سی ایپلی کیشنز: سمندری پانی، نمی اور کیمیکلز کی وجہ سے ہونے والے سنکنرن سے بچانے کے لیے انسولیٹنگ ایپوکسی کوٹنگز کو چینلز اور سب سی کے آلات پر لگایا جاتا ہے۔ یہ ملعمع کاری ایک رکاوٹ کے طور پر کام کرتی ہیں، سنکنرن مادوں کی رسائی کو روکتی ہیں اور بنیادی ڈھانچے کی سالمیت کو برقرار رکھتی ہیں۔ وہ برقی موصلیت بھی فراہم کرتے ہیں، برقی مداخلت یا نقصان کے خطرے کو کم کرتے ہیں۔
- آف شور ونڈ فارمز: غیر ملکی ونڈ فارمز کی تعمیر اور دیکھ بھال میں انسولیٹنگ ایپوکسی کوٹنگز کا استعمال کیا جاتا ہے۔ وہ ونڈ ٹربائن کے ڈھانچے بشمول ٹاورز، فاؤنڈیشنز اور زیر سمندر کیبلز کو سنکنرن اور ماحولیاتی انحطاط سے بچاتے ہیں۔ یہ کوٹنگز برقی موصلیت بھی فراہم کرتی ہیں، محفوظ اور موثر بجلی کی ترسیل کو یقینی بناتی ہیں۔
- سمندری اور سمندری سامان: Epoxy کوٹنگز مختلف میرینز اور آف شور آلات پر لگائی جاتی ہیں، جیسے پمپ، والوز، ٹینک، اور مورنگ سسٹم۔ یہ ملمع ساز سامان کو سنکنرن، رگڑ اور کیمیائی نمائش سے بچاتے ہیں، ان کی سروس کی زندگی کو بڑھاتے ہیں اور دیکھ بھال کے اخراجات کو کم کرتے ہیں۔ ان کوٹنگز کی موصلیت کی خصوصیات برقی چالکتا کے مسائل کو بھی روکتی ہیں، سامان کی حفاظت اور وشوسنییتا کو بہتر بناتی ہیں۔
- فلوٹنگ پروڈکشن سٹوریج اور آف لوڈنگ (FPSO) ویسلز: ایف پی ایس اوز آف شور تیل اور گیس کی پیداوار میں بڑے پیمانے پر استعمال ہوتے ہیں۔ انسولیٹنگ ایپوکسی کوٹنگز FPSOs کے ہلوں اور اندرونی ڈھانچے پر لگائی جاتی ہیں تاکہ انہیں سنکنرن، رگڑنے اور کیمیائی نمائش سے بچایا جا سکے۔ یہ کوٹنگز طویل مدتی تحفظ فراہم کرتی ہیں اور برتن کی ساختی سالمیت کو یقینی بناتی ہیں۔
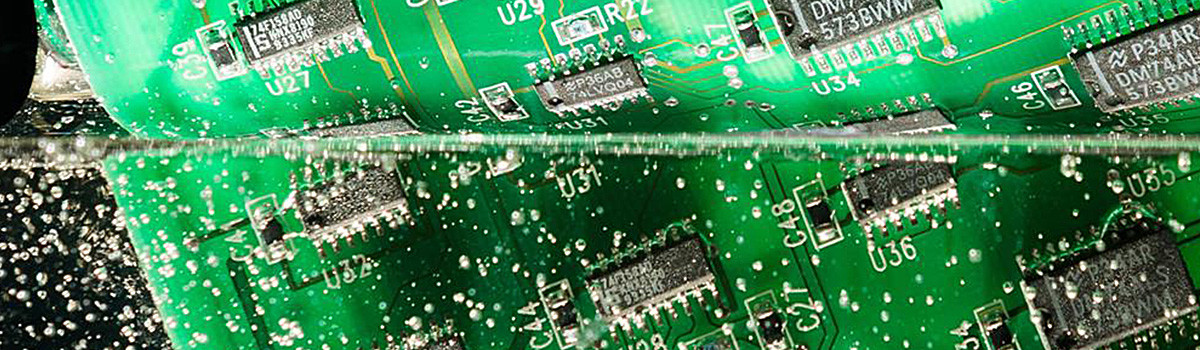
کیمیائی اور سنکنرن مزاحمت
سنکنرن اور برقی موصلیت سے بچانے کے لیے مختلف صنعتوں میں انسولیٹنگ ایپوکسی کوٹنگز بڑے پیمانے پر استعمال ہوتی ہیں۔ یہ کوٹنگز بہترین کیمیائی مزاحمت پیش کرتے ہیں، انہیں سخت ماحول کے لیے موزوں بناتے ہیں جہاں سنکنرن مادوں کی نمائش ایک تشویش کا باعث ہے۔
epoxy کوٹنگز کو موصل کرنے کے لیے کیمیائی مزاحمت بہت اہم ہے، کیونکہ وہ اکثر کیمیکلز کی ایک وسیع رینج کے سامنے آتے ہیں، بشمول تیزاب، الکلیس، سالوینٹس اور ایندھن۔ Epoxy کوٹنگز اپنے گھنے مالیکیولر ڈھانچے اور کراس سے منسلک پولیمر نیٹ ورک کی وجہ سے بہت سے سنکنرن مادوں کے خلاف مزاحمت کرتی ہیں۔ یہ ڈھانچہ ایک رکاوٹ پیدا کرتا ہے جو corrosive ایجنٹوں کی رسائی کو روکتا ہے، اس طرح بنیادی سبسٹریٹ کی حفاظت کرتا ہے۔
epoxy کوٹنگز کی کیمیائی مزاحمت میں کردار ادا کرنے والے بنیادی عوامل میں سے ایک ان کی اعلی کراس لنک کثافت ہے۔ کراس لنکنگ سے مراد ایپوکسی مالیکیولز کے درمیان کیمیائی بندھن ہے، جس کے نتیجے میں تین جہتی نیٹ ورک بنتا ہے۔ یہ نیٹ ورک سنکنرن مادوں کے پھیلاؤ کو روکنے میں رکاوٹ پیدا کرکے کیمیائی حملے کے خلاف کوٹنگ کی مزاحمت کو بڑھاتا ہے۔ نتیجے کے طور پر، لیپت سبسٹریٹ سنکنرن سے محفوظ رہتا ہے۔
مزید برآں، epoxy کوٹنگز کو ان کی کیمیائی مزاحمت کو بڑھانے کے لیے مختلف additives اور reinforcements کے ساتھ تیار کیا جا سکتا ہے۔ مثال کے طور پر، سنکنرن روکنے والوں کا اضافہ سنکنرن کے عمل کو روک کر اور ایپوکسی کے انحطاط کو کم کرکے کوٹنگ کی حفاظتی خصوصیات کو مزید بہتر بنا سکتا ہے۔ شیشے کے ریشوں یا نینو پارٹیکلز جیسی کمک بھی کوٹنگ کی مکینیکل اور کیمیائی مزاحمت کو بڑھا سکتی ہے۔
کیمیائی مزاحمت کے علاوہ، epoxy کوٹنگز کی موصلیت بہترین سنکنرن مزاحمت پیش کرتی ہے۔ سنکنرن اس وقت ہوتا ہے جب کوئی مواد اپنے ماحول کے ساتھ رد عمل ظاہر کرتا ہے، جس سے اس کے بگاڑ اور ممکنہ ناکامی ہوتی ہے۔ Epoxy کوٹنگز سنکنرن ماحول اور سبسٹریٹ کے درمیان ایک رکاوٹ کے طور پر کام کرتی ہیں، نمی، آکسیجن، اور دیگر corrosive ایجنٹوں کے اندرونی دھات کی سطح کے ساتھ رابطے کو روکتی ہیں۔
Epoxy کوٹنگز مختلف ذیلی ذخیروں کو بہترین چپکنے والی بھی فراہم کرتی ہیں، جو سنکنرن کے خلاف طویل مدتی تحفظ کو یقینی بناتی ہیں۔ پرت اور سبسٹریٹ کے درمیان مضبوط بانڈ نمی اور سنکنرن مادوں کے داخل ہونے سے روکتا ہے، جس سے سنکنرن شروع ہونے اور بڑھنے کے امکانات کم ہوتے ہیں۔
یہ نوٹ کرنا ضروری ہے کہ epoxy کوٹنگز کی موصلیت کی کیمیائی اور سنکنرن مزاحمت درجہ حرارت، نمائش کے وقت اور مخصوص کیمیائی ماحول سے متاثر ہو سکتی ہے۔ اگرچہ epoxy کوٹنگز مختلف کیمیکلز کے خلاف بہترین مزاحمت پیش کرتے ہیں، انتہائی جارحانہ مادے اب بھی طویل مدت یا انتہائی حالات میں نقصان کا باعث بن سکتے ہیں۔
بہترین کارکردگی کو یقینی بنانے کے لیے، مخصوص درخواست کی ضروریات کی بنیاد پر مناسب ایپوکسی کوٹنگ فارمولیشن کا انتخاب ضروری ہے۔ صحیح epoxy کوٹنگ سسٹم کا انتخاب کرتے وقت، آپریٹنگ ماحول، کیمیائی نمائش، درجہ حرارت، اور متوقع سروس کی زندگی پر غور کیا جانا چاہئے.
تھرمل چالکتا اور حرارت کی کھپت
تھرمل چالکتا اور گرمی کی کھپت مختلف شعبوں میں ضروری ہے، بشمول انجینئرنگ، الیکٹرانکس، اور مواد سائنس۔ گرمی پیدا کرنے یا سنبھالنے والے نظاموں کی کارکردگی اور وشوسنییتا کا تعین کرنے میں وہ اہم ہیں۔ آئیے دی گئی لفظی حد کے اندر ان تصورات کو مزید دریافت کریں۔
حرارتی چالکتا سے مراد کسی مادے کی حرارت چلانے کی صلاحیت ہے، اور یہ ایک ایسی خاصیت ہے جو اس بات کی نشاندہی کرتی ہے کہ کسی مادے کے ذریعے حرارت کتنی آسانی سے منتقل ہو سکتی ہے۔ اعلی تھرمل چالکتا والے مواد گرمی کو تیزی سے بہنے دیتے ہیں، جبکہ کم تھرمل چالکتا والے مواد حرارت کی منتقلی میں رکاوٹ بنتے ہیں۔ تھرمل چالکتا کی پیمائش کی اکائی واٹ فی میٹر-کیلون (W/mK) ہے۔
مختلف عوامل مواد کی تھرمل چالکتا کو متاثر کرتے ہیں۔ اہم عوامل میں سے ایک سالماتی یا جوہری ڈھانچہ ہے۔ قریب سے بھرے ایٹموں یا مالیکیولز والے مادوں میں تھرمل چالکتا زیادہ ہوتی ہے۔ تانبے اور ایلومینیم جیسی دھاتیں ان کی دھاتی بانڈنگ اور قریبی پیکڈ کرسٹل ڈھانچے کی وجہ سے اپنی اعلی تھرمل چالکتا کے لیے مشہور ہیں۔
دوسری طرف، پیچیدہ مالیکیولر ڈھانچے یا بڑے voids کے ساتھ مواد، جیسے پولیمر یا انسولیٹر جیسے لکڑی یا ربڑ، نسبتاً کم تھرمل چالکتا رکھتے ہیں۔ ہوا اور دیگر گیسیں حرارت کے ناقص موصل ہیں، یہی وجہ ہے کہ پھنسے ہوئے ہوا کی جیبوں والے مواد، جیسے موصلیت کا مواد، کم تھرمل چالکتا کی نمائش کرتے ہیں۔
تاہم، حرارت کی کھپت سے مراد زیادہ گرمی کو روکنے اور زیادہ سے زیادہ آپریٹنگ حالات کو برقرار رکھنے کے لیے نظام یا جزو سے حرارت کو دور منتقل کرنا یا ختم کرنا ہے۔ آلات کی لمبی عمر اور کارکردگی کے لیے موثر گرمی کی کھپت بہت اہم ہے، خاص طور پر وہ جو کہ خاصی مقدار میں حرارت پیدا کرتے ہیں، جیسے الیکٹرانک اجزاء، پاور سسٹم، اور انجن۔
مخصوص درخواست پر منحصر ہے، گرمی کی کھپت کے مختلف طریقے ہیں. کچھ معیاری تکنیکوں میں ترسیل، نقل و حمل اور تابکاری شامل ہیں۔
ترسیل میں اشیاء کے درمیان براہ راست جسمانی رابطے کے ذریعے حرارت کی منتقلی شامل ہوتی ہے۔ موثر حرارت کو چلانے والے مواد، جیسے دھاتیں یا اعلی تھرمل چالکتا کے ساتھ مواد، گرمی پیدا کرنے والے اجزاء اور حرارت کے سنک یا کولنگ سسٹم کے درمیان حرارت کی منتقلی کو آسان بناتے ہیں۔
کنویکشن میں سیالوں کی نقل و حرکت کے ذریعے حرارت کی منتقلی شامل ہوتی ہے، جیسے ہوا یا مائع۔ یہ عمل ماخذ سے حرارت کو دور کرنے کے لیے قدرتی طور پر یا پنکھے یا پمپ کے ذریعے سیال کی گردش پر انحصار کرتا ہے۔ توسیع شدہ سطحوں کے ساتھ ہیٹ سنک اکثر محرک حرارت کی منتقلی کے لیے سطح کے رقبے کو بڑھانے کے لیے استعمال کیے جاتے ہیں۔
تابکاری سے مراد تھرمل تابکاری کا اخراج اور جذب ہوتا ہے، جو کہ ان کے درجہ حرارت کی وجہ سے اشیاء سے خارج ہونے والی برقی مقناطیسی تابکاری ہے۔ مطلق صفر درجہ حرارت سے اوپر کی تمام اشیاء تھرمل تابکاری خارج کرتی ہیں۔ تابکاری کے ذریعے حرارت کی کھپت اس وقت ہوتی ہے جب خارج ہونے والی تابکاری گرمی کو ماخذ سے زیادہ آرام دہ ماحول میں لے جاتی ہے۔
گرمی کی کھپت کو بڑھانے کے لیے مختلف تکنیکوں اور ٹیکنالوجیز کا استعمال کیا جاتا ہے، بشمول ہیٹ سنک، ہیٹ پائپ، تھرمل انٹرفیس میٹریل، پنکھے، مائع کولنگ سسٹم، اور جدید تھرمل مینجمنٹ سلوشنز۔
برقی موصلیت کی کارکردگی
مختلف صنعتوں بشمول الیکٹرانکس، برقی آلات اور پاور سسٹمز میں برقی موصلیت فراہم کرنے کے لیے ایپوکسی کوٹنگز کی موصلیت بہت اہم ہے۔ یہ کوٹنگز بجلی کے بہاؤ کو روکنے اور برقی خرابی یا شارٹ سرکٹ سے بچانے کے لیے بنائی گئی ہیں۔ آئیے دی گئی لفظی حد کے اندر epoxy کوٹنگز کی موصلیت کی برقی موصلیت کی کارکردگی کو دریافت کریں۔
ایپوکسی کوٹنگز کی برقی موصلیت کی کارکردگی میں کردار ادا کرنے والی بنیادی خصوصیات میں سے ایک ان کی اعلی ڈائی الیکٹرک طاقت ہے۔ ڈائی الیکٹرک طاقت سے مراد زیادہ سے زیادہ برقی فیلڈ ہے جو ایک مادہ بجلی کی خرابی کا سامنا کیے بغیر برداشت کر سکتا ہے۔ انسولیٹنگ ایپوکسی کوٹنگز کو ہائی ڈائی الیکٹرک طاقت رکھنے کے لیے تیار کیا گیا ہے، جس سے وہ ہائی وولٹیج کی سطح کو برداشت کر سکتے ہیں اور برقی رساو یا آرسنگ کو روک سکتے ہیں۔
کئی عوامل، بشمول رال کی تشکیل، علاج کا عمل، اور فلر مواد، epoxy کوٹنگز کی موصلیت کی ڈائی الیکٹرک طاقت کو متاثر کرتے ہیں۔ اعلی مالیکیولر وزن اور کراس لنکنگ کثافت کے ساتھ ایپوکسی رال زیادہ ڈائی الیکٹرک طاقت کی نمائش کرتے ہیں۔ علاج کا عمل بھی ایک کردار ادا کرتا ہے، کیونکہ مناسب علاج ایک گھنے اور یکساں کوٹنگ کی تشکیل کو یقینی بناتا ہے جو بجلی کے دباؤ کو برداشت کر سکتی ہے۔
برقی موصلیت کی کارکردگی کو بڑھانے کے لیے فلر مواد کو ایپوکسی کوٹنگز میں شامل کیا جا سکتا ہے۔ فلرز، جیسے شیشے کے ریشوں یا معدنی فلرز، کوٹنگ کے اندر voids یا کمزور پوائنٹس کی موجودگی کو کم کر کے ڈائی الیکٹرک طاقت کو بڑھا سکتے ہیں۔ یہ فلرز کوٹنگ کی مجموعی یکسانیت اور ساختی سالمیت کو بہتر بناتے ہیں، برقی خرابی کے خطرے کو کم کرتے ہیں۔
epoxy کوٹنگز کی موصلیت اچھی برقی مزاحمتی صلاحیت بھی پیش کرتی ہے، جس سے مراد برقی رو کے بہاؤ کے خلاف مزاحمت کرنے کی مواد کی صلاحیت ہے۔ رساو کو روکنے اور برقی موصلیت کی سالمیت کو برقرار رکھنے کے لیے ہائی برقی مزاحمتی صلاحیت بہت ضروری ہے۔ Epoxy کوٹنگز میں عام طور پر اعلی مزاحمتی اقدار ہوتی ہیں، جو برقی انسولیٹر کے طور پر ان کی تاثیر میں حصہ ڈالتی ہیں۔
برقی موصلیت کی کارکردگی کا ایک اور اہم پہلو ماحولیاتی عوامل کا مقابلہ کرنے کے لیے ایپوکسی کوٹنگز کو موصل کرنے کی صلاحیت ہے جو ان کی برقی خصوصیات کو متاثر کر سکتے ہیں۔ نمی، درجہ حرارت کے تغیرات، اور کیمیکلز کی نمائش جیسے عوامل کوٹنگ کی ڈائی الیکٹرک طاقت اور مزاحمت کو متاثر کر سکتے ہیں۔ لہذا، مخصوص ماحولیاتی حالات کے تحت طویل مدتی برقی موصلیت کی کارکردگی فراہم کرنے کے لیے مناسب فارمولیشنز اور اضافی اشیاء کے ساتھ ایپوکسی کوٹنگز کا انتخاب کرنا ضروری ہے۔
مزید برآں، طویل مدتی برقی موصلیت کو یقینی بنانے کے لیے epoxy کوٹنگز کی موصلیت کو سبسٹریٹ میں اچھی چپکنے کی نمائش کرنی چاہیے۔ پرت اور بنیادی سطح کے درمیان ایک مضبوط بانڈ voids یا خلاء کی تشکیل کو روکتا ہے جو برقی موصلیت کی کارکردگی سے سمجھوتہ کر سکتا ہے۔ سطح کی تیاری، کوٹنگ کی درخواست کی تکنیک، اور کوٹنگ اور سبسٹریٹ کے اثر و رسوخ کے درمیان مطابقت۔
خلاصہ کرنے کے لیے، epoxy کوٹنگز کی موصلیت اعلی ڈائی الیکٹرک طاقت، برقی مزاحمت، اور سبسٹریٹ کو اچھی چپکنے والی فراہم کرکے بہترین برقی موصلیت کی کارکردگی پیش کرتی ہے۔ ان کی تشکیل، علاج کا عمل، اور فلرز کا استعمال ان کی بجلی کے دباؤ کو برداشت کرنے اور برقی خرابی کو روکنے کی صلاحیت میں معاون ہے۔ الیکٹرانکس سے لے کر پاور سسٹم تک مختلف ایپلی کیشنز میں موثر برقی موصلیت کو یقینی بنانے کے لیے epoxy کوٹنگز کی موصلیت کا مناسب انتخاب اور اطلاق بہت ضروری ہے۔
ایپوکسی کوٹنگز کی موصلیت کی اقسام
متعدد قسم کی موصلیت والی ایپوکسی کوٹنگز دستیاب ہیں، ہر ایک کو مخصوص ضروریات کو پورا کرنے اور برقی موصلیت کی مختلف سطحیں فراہم کرنے کے لیے ڈیزائن کیا گیا ہے۔ ایپوکسی کوٹنگز کی حفاظت کی کچھ عام اقسام یہ ہیں:
- معیاری انسولیٹنگ ایپوکسی کوٹنگز: یہ عام مقصد کی ایپوکسی کوٹنگز ہیں جو بنیادی برقی موصلیت فراہم کرنے کے لیے تیار کی گئی ہیں۔ وہ اچھی ڈائی الیکٹرک طاقت اور برقی مزاحمت پیش کرتے ہیں، جو انہیں مختلف ایپلی کیشنز کے لیے موزوں بناتے ہیں۔
- اعلی درجہ حرارت کی موصلیت والی ایپوکسی کوٹنگز: یہ ملعمع کاری خاص طور پر ان کی برقی موصلیت کی کارکردگی پر سمجھوتہ کیے بغیر بلند درجہ حرارت کو برداشت کرنے کے لیے تیار کی گئی ہیں۔ ان کا استعمال ایسی ایپلی کیشنز میں کیا جا سکتا ہے جہاں زیادہ گرمی کی توقع کی جاتی ہے، جیسے موٹرز، ٹرانسفارمرز، یا آٹوموٹو یا ایرو اسپیس صنعتوں میں برقی اجزاء۔
- تھرمل کنڈکٹیو انسولیٹنگ ایپوکسی کوٹنگز: یہ ملعمع کاری برقی موصلیت فراہم کرتی ہے اور تھرمل چالکتا کی اضافی خاصیت رکھتی ہے۔ وہ بجلی کی موصلیت کو برقرار رکھتے ہوئے گرمی کو مؤثر طریقے سے ختم کرنے کے لیے ڈیزائن کیے گئے ہیں۔ یہ کوٹنگز عام طور پر ایسی ایپلی کیشنز میں استعمال ہوتی ہیں جن میں برقی موصلیت اور حرارت کی موثر کھپت کی ضرورت ہوتی ہے، جیسے کہ پاور الیکٹرانکس میں۔
- شعلہ ریٹارڈنٹ انسولیٹنگ ایپوکسی کوٹنگز: شعلے کے پھیلاؤ اور دہن کے خلاف مزاحمت کی پیشکش کرتے ہوئے برقی موصلیت فراہم کرنے کے لیے شعلہ ریٹارڈنٹ ایپوکسی کوٹنگز تیار کی گئی ہیں۔ یہ کوٹنگز عام طور پر ایسی ایپلی کیشنز میں استعمال ہوتی ہیں جہاں آگ کی حفاظت کا مسئلہ ہوتا ہے، جیسے کہ برقی پینل، سوئچ گیئر، یا وائرنگ۔
- کیمیکل ریزسٹنٹ انسولیٹنگ ایپوکسی کوٹنگز: ان کوٹنگز کو مختلف کیمیکلز اور سنکنرن مادوں کے خلاف بہترین مزاحمت پیش کرتے ہوئے برقی موصلیت فراہم کرنے کے لیے ڈیزائن کیا گیا ہے۔ وہ ایپلی کیشنز کے لیے موزوں ہیں جہاں سخت کیمیکلز یا سنکنرن ماحول کی نمائش متوقع ہے، جیسے کیمیکل پروسیسنگ پلانٹس یا سمندری ایپلی کیشنز میں۔
- UV-مزاحم موصلی Epoxy کوٹنگز: الٹرا وایلیٹ (UV) تابکاری کے نقصان دہ اثرات سے تحفظ فراہم کرتے ہوئے الیکٹریکل موصلیت فراہم کرنے کے لیے UV-مزاحم کوٹنگز تیار کی جاتی ہیں۔ یہ کوٹنگز عام طور پر بیرونی ایپلی کیشنز یا ماحول میں استعمال ہوتی ہیں جہاں سورج کی روشنی کی نمائش اہم ہوتی ہے، جیسے سولر پینلز یا آؤٹ ڈور برقی آلات۔
- لچکدار انسولیٹنگ ایپوکسی کوٹنگز: لچکدار ایپوکسی کوٹنگز کو ایپلی کیشنز میں برقی موصلیت فراہم کرنے کے لیے ڈیزائن کیا گیا ہے جہاں لیپت سبسٹریٹ مکینیکل دباؤ یا حرکت سے گزرتا ہے۔ یہ ملعمع کاری اچھی چپکنے والی اور لچک پیش کرتی ہے، جس سے وہ بجلی کی موصلیت میں کریکنگ یا سمجھوتہ کیے بغیر موڑنے یا کھینچنے کا مقابلہ کر سکتے ہیں۔
یہ نوٹ کرنا ضروری ہے کہ مناسب انسولیٹنگ ایپوکسی کوٹنگ کی قسم کا انتخاب درخواست کی مخصوص ضروریات، ماحولیاتی عوامل اور کارکردگی کی توقعات پر منحصر ہے۔ کوٹنگ مینوفیکچررز یا صنعت کے ماہرین سے مشاورت کسی خاص ایپلی کیشن کے لیے موزوں ترین موصلی ایپوکسی کوٹنگ کا تعین کرنے میں مدد کر سکتی ہے۔
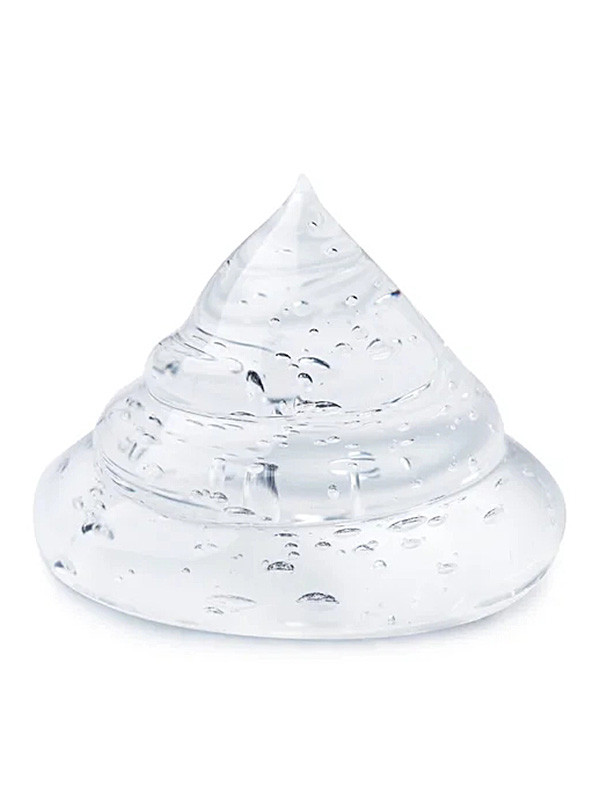
دو حصوں والی ایپوکسی کوٹنگز
دو حصوں پر مشتمل ایپوکسی کوٹنگز ان کی غیر معمولی استحکام، کیمیائی مزاحمت اور استعداد کے لیے مختلف صنعتوں میں بڑے پیمانے پر استعمال ہوتی ہیں۔ یہ کوٹنگز دو اجزاء پر مشتمل ہیں: ایک رال اور ایک ہارڈنر۔ صحیح تناسب میں جوڑنے پر، وہ ایک کیمیائی رد عمل سے گزرتے ہیں جسے کیورنگ کہا جاتا ہے، جس کے نتیجے میں ایک ٹھوس اور حفاظتی کوٹنگ ہوتی ہے۔ یہاں، ہم دو حصوں پر مشتمل epoxy کوٹنگز کی اہم خصوصیات، ایپلی کیشنز اور فوائد کا جائزہ لیں گے۔
خصوصیات: دو حصوں والی ایپوکسی کوٹنگز کئی اہم خصوصیات پیش کرتی ہیں جو انہیں بہت سے ایپلی کیشنز میں انتہائی مطلوبہ بناتی ہیں۔ سب سے پہلے، وہ کنکریٹ، دھات، لکڑی، اور فائبر گلاس سمیت مختلف ذیلی ذخیروں کو بہترین چپکنے کی سہولت فراہم کرتے ہیں۔ یہ چپکنا دیرپا کارکردگی کو یقینی بناتا ہے اور چھیلنے یا ڈیلامینیشن جیسے مسائل کو روکتا ہے۔ مزید برآں، ایپوکسی کوٹنگز اعلی کیمیائی مزاحمت کی نمائش کرتی ہیں، جو انہیں سنکنرن مادوں، کیمیکلز یا سالوینٹس کے سامنے والے ماحول میں استعمال کے لیے موزوں بناتی ہیں۔ وہ اپنی غیر معمولی سختی، رگڑنے کی مزاحمت، اور اثر مزاحمت کے لیے بھی جانے جاتے ہیں، جو ان کی لمبی عمر اور استحکام میں اہم کردار ادا کرتے ہیں۔ مزید برآں، مطلوبہ جمالیاتی اور فنکشنل تقاضوں پر منحصر ہے، ایپوکسی کوٹنگز کو مختلف فنشز کے لیے تیار کیا جا سکتا ہے، بشمول چمکدار، دھندلا، یا بناوٹ۔
درخواستیں: دو حصوں پر مشتمل ایپوکسی کوٹنگز اپنی استعداد اور کارکردگی کی خصوصیات کی وجہ سے مختلف صنعتوں میں درخواستیں تلاش کرتی ہیں۔ صنعتی شعبے میں، وہ عام طور پر مینوفیکچرنگ پلانٹس، گوداموں اور گیراجوں میں کنکریٹ کے فرش کی حفاظت کے لیے استعمال ہوتے ہیں۔ ایپوکسی کوٹنگ ایک ہموار، پائیدار سطح بناتی ہے جو بھاری ٹریفک، اثرات، اور کیمیائی رساؤ کو برداشت کر سکتی ہے۔ سمندری صنعت میں، epoxy کوٹنگز کو کشتیوں کے سوراخوں، ڈیکوں اور دیگر ڈھانچے کے لیے استعمال کیا جاتا ہے، جو پانی کے داخل ہونے، UV تابکاری اور سنکنرن سے بچاتے ہیں۔ یہ ملعمع کاری آٹوموٹیو انڈسٹری میں کار باڈیز، انجن کے پرزہ جات، اور انڈر باڈی کوٹنگز پر حفاظتی تہہ فراہم کرنے کے لیے بھی استعمال کی جاتی ہے، جس سے ان کی کھرچنے، کیمیکلز اور موسم کے خلاف مزاحمت بڑھ جاتی ہے۔ مزید برآں، تعمیراتی شعبے میں واٹر پروفنگ، کنکریٹ کی مرمت اور آرائشی فرش کے نظام کے لیے دو حصوں پر مشتمل ایپوکسی کوٹنگز بڑے پیمانے پر استعمال ہوتی ہیں۔
فوائد: دو حصوں والی ایپوکسی کوٹنگز کا استعمال صنعتی اور تجارتی صارفین کو بے شمار فوائد فراہم کرتا ہے۔ سب سے پہلے، ان کی غیر معمولی استحکام اور پہننے اور آنسو کے خلاف مزاحمت لیپت سطحوں کے لیے طویل عمر کو یقینی بناتی ہے، دیکھ بھال اور متبادل کے اخراجات کو کم کرتی ہے۔ Epoxy کوٹنگز لاگو کرنے میں بھی نسبتاً آسان ہیں، جو صنعتی سیٹنگز میں موثر تنصیب اور کم سے کم وقت کی اجازت دیتی ہیں۔ ان کی ہموار اور غیر غیرمحفوظ نوعیت انہیں حفظان صحت اور صاف کرنے میں آسان بناتی ہے، ایسے ماحول کے لیے مثالی ہے جہاں صفائی کی اعلیٰ سطح کی ضرورت ہوتی ہے، جیسے کہ صحت کی دیکھ بھال کی سہولیات یا فوڈ پروسیسنگ پلانٹس۔ مزید برآں، epoxy کوٹنگز کو مخصوص ضروریات کو پورا کرنے کے لیے اپنی مرضی کے مطابق بنایا جا سکتا ہے، بشمول اینٹی پرچی خصوصیات، گرمی کی مزاحمت، یا برقی چالکتا۔ یہ استعداد مختلف ایپلی کیشنز میں موزوں حل کی اجازت دیتی ہے۔ آخر میں، دو حصوں پر مشتمل ایپوکسی کوٹنگز ماحول دوست ہیں کیونکہ ان میں غیر مستحکم نامیاتی مرکبات (VOCs) کم ہوتے ہیں، جو انہیں کارکنوں اور ماحول کے لیے محفوظ بناتے ہیں۔
ایک حصہ ایپوکسی کوٹنگز
ون پارٹ ایپوکسی کوٹنگز سنگل پرزنٹ کوٹنگز ہیں جو روایتی دو پارٹ ایپوکسی کوٹنگز کے مقابلے میں بہت سے فوائد پیش کرتی ہیں لیکن ایپلی کیشن کے آسان عمل کے ساتھ۔ یہ کوٹنگز ایک رال کے ساتھ تیار کی جاتی ہیں جس میں ایپوکسی رال اور کیورنگ ایجنٹ دونوں ہوتے ہیں، جس سے علیحدہ ہارڈنر کی ضرورت ختم ہوتی ہے۔ یہ مضمون ایک حصہ ایپوکسی کوٹنگز کی خصوصیات، ایپلی کیشنز اور فوائد کو تلاش کرے گا۔
خصوصیات: ایک حصہ ایپوکسی کوٹنگز میں کئی اہم خصوصیات ہیں جو انہیں مختلف صنعتوں میں مقبول بناتی ہیں۔ یہ کوٹنگز مختلف ذیلی ذخیروں کے ساتھ بہترین چپکنے کی نمائش کرتی ہیں، بشمول کنکریٹ، دھات اور لکڑی، ایک ٹھوس بندھن اور دیرپا تحفظ کو یقینی بناتی ہیں۔ وہ اچھی کیمیائی مزاحمت فراہم کرتے ہیں، سنکنرن مادوں، کیمیکلز اور سالوینٹس سے تحفظ فراہم کرتے ہیں۔ مزید برآں، ایک حصے والی ایپوکسی کوٹنگز اچھی کھرچنے کے خلاف مزاحمت اور پائیداری فراہم کرتی ہیں، جو انہیں بھاری ٹریفک یا پہننے والی سطحوں کے لیے موزوں بناتی ہیں۔ مطلوبہ جمالیاتی اپیل کو حاصل کرنے کے لیے انہیں مختلف فنشز، جیسے چمکدار یا دھندلا کے ساتھ بھی تیار کیا جا سکتا ہے۔
درخواستیں: ایک حصہ ایپوکسی کوٹنگز مختلف صنعتوں اور سطحوں پر ایپلی کیشنز تلاش کرتی ہیں۔ تعمیراتی صنعت میں، وہ عام طور پر کنکریٹ کے فرش کی حفاظت اور ان کو بڑھانے کے لیے استعمال ہوتے ہیں، جو گوداموں، خوردہ جگہوں، اور تجارتی عمارتوں جیسی ترتیبات میں ہموار اور پائیدار کور فراہم کرتے ہیں۔ یہ کوٹنگز آٹوموٹو انڈسٹری میں بھی ایپلی کیشنز تلاش کرتی ہیں، جہاں وہ گاڑی کے انڈر کیریجز، چیسس کے اجزاء، اور دیگر دھاتی سطحوں پر سنکنرن سے تحفظ کے لیے استعمال ہوتی ہیں۔ مزید برآں، سمندری صنعت میں کشتیوں کے ڈیکوں، سوئمنگ پولز اور سمندری ڈھانچے کے لیے ایک حصے کی ایپوکسی کوٹنگز استعمال کی جاتی ہیں، جو پانی، UV تابکاری اور کیمیکلز کے خلاف مزاحمت فراہم کرتی ہیں۔ انہیں دھاتی سطحوں پر بھی استعمال کیا جا سکتا ہے، جیسے کہ مشینری، سامان، یا اسٹوریج ٹینک، سنکنرن اور پہننے سے بچانے کے لیے۔
فوائد: ایک حصہ ایپوکسی کوٹنگز کئی فوائد پیش کرتے ہیں جو انہیں بہت سے ایپلی کیشنز کے لیے فائدہ مند بناتے ہیں۔ اہم فوائد میں سے ایک ان کے استعمال اور استعمال میں آسانی ہے۔ چونکہ وہ پہلے سے مخلوط ہوتے ہیں، اس لیے متعدد اجزاء کی پیمائش اور اختلاط، کوٹنگ کے عمل کو آسان بنانے اور غلطیوں کے امکانات کو کم کرنے کی ضرورت نہیں ہے۔ یہ انہیں چھوٹے منصوبوں یا ایپوکسی کوٹنگز کے ساتھ محدود تجربہ رکھنے والے صارفین کے لیے مثالی بناتا ہے۔ مزید برآں، ایک حصے کی ایپوکسی کوٹنگز میں اکثر دو حصوں کے نظاموں کے مقابلے میں طویل برتن کی زندگی ہوتی ہے، جس سے کام کرنے کا وقت بڑھایا جاتا ہے اور زیادہ سیدھا استعمال ہوتا ہے۔ وہ بہترین چپکنے والی، پائیداری، اور کیمیائی مزاحمت بھی پیش کرتے ہیں، لیپت سطحوں کے لیے دیرپا تحفظ کو یقینی بناتے ہیں۔ مزید یہ کہ، ایک حصے کی ایپوکسی کوٹنگز عام طور پر غیر مستحکم نامیاتی مرکبات (VOCs) میں کم ہوتی ہیں، جو انہیں ماحول دوست اور صارفین کے لیے محفوظ بناتی ہیں۔
صحیح انسولیٹنگ ایپوکسی کوٹنگ کا انتخاب
مختلف ایپلی کیشنز کے لیے مناسب موصلیت اور تحفظ کو یقینی بنانے کے لیے انسولیٹنگ ایپوکسی کوٹنگ کا انتخاب بہت ضروری ہے۔ انسولیٹنگ ایپوکسی کوٹنگز کو بجلی کی موصلیت اور تھرمل مزاحمت فراہم کرنے، برقی چالکتا اور حرارت کی منتقلی کو روکنے کے لیے ڈیزائن کیا گیا ہے۔ مناسب موصلیت والی ایپوکسی کوٹنگ کا انتخاب کرتے وقت یہاں کچھ اہم عوامل پر غور کرنا ہے:
- الیکٹریکل پراپرٹیز: ایک موصلیت بخش ایپوکسی کوٹنگ کا بنیادی کام برقی موصلیت فراہم کرنا ہے۔ لہذا، کوٹنگ کی برقی خصوصیات پر غور کرنا ضروری ہے، جیسے ڈائی الیکٹرک طاقت، حجم کی مزاحمت، اور سطح کی مزاحمت۔ ڈائی الیکٹرک طاقت زیادہ سے زیادہ وولٹیج کا تعین کرتی ہے کہ کوٹنگ ٹوٹنے سے پہلے کس حد تک برداشت کر سکتی ہے، جب کہ مزاحمتی قوت مواد کی برقی رو کے بہاؤ کے خلاف مزاحمت کرنے کی صلاحیت کی پیمائش کرتی ہے۔ یقینی بنائیں کہ پرت آپ کی مخصوص ایپلی کیشن کے لیے مطلوبہ برقی معیارات پر پورا اترتی ہے۔
- حرارتی مزاحمت: حرارت کی منتقلی کو روکنے کے لیے epoxy کوٹنگز کی موصلیت سے تھرمل مزاحمت کی بھی توقع کی جاتی ہے۔ کوٹنگ کی اعلی درجہ حرارت کو برداشت کرنے اور موثر تھرمل موصلیت فراہم کرنے کی صلاحیت پر غور کریں۔ حرارت کی منتقلی کو کم کرنے اور درجہ حرارت کے استحکام کو برقرار رکھنے کے لیے کم تھرمل چالکتا والی تہوں کو تلاش کریں۔
- سبسٹریٹ مطابقت: سبسٹریٹ مواد کے ساتھ ایپوکسی کوٹنگ کی مطابقت کا اندازہ کریں۔ انسولیٹنگ ایپوکسی کوٹنگز عام طور پر تانبے، ایلومینیم یا سٹیل کی دھاتوں پر استعمال ہوتی ہیں۔ اس بات کو یقینی بنائیں کہ کوٹنگ مخصوص سبسٹریٹ مواد پر اچھی طرح سے عمل کرنے کے لیے بنائی گئی ہے، جو ایک مضبوط بانڈ اور طویل مدتی کارکردگی فراہم کرتی ہے۔
- درخواست کا طریقہ: منتخب کردہ موصلی ایپوکسی کوٹنگ کے لیے درخواست کے طریقہ کار اور استعمال میں آسانی پر غور کریں۔ کچھ کوٹنگز سپرے کے لیے موزوں ہیں، جبکہ دیگر برش یا رولر لگانے کے لیے زیادہ موزوں ہیں۔ ایک پرت کا انتخاب کریں جو دستیاب ایپلیکیشن آلات اور پروجیکٹ کی ضروریات کے مطابق ہو۔
- ماحولیاتی مزاحمت: کوٹنگ کے سامنے آنے والے ماحولیاتی حالات کا اندازہ لگائیں، جیسے نمی، نمی، کیمیکل، یا UV تابکاری۔ طویل مدتی کارکردگی اور تحفظ کو یقینی بنانے کے لیے epoxy کوٹنگز کی موصلیت کو ان ماحولیاتی عوامل کے خلاف بہترین مزاحمت پیش کرنی چاہیے۔ اگر سخت ماحول کا سامنا ہو تو اعلی کیمیائی مزاحمت اور UV استحکام والی کوٹنگز پر غور کریں۔
- سرٹیفیکیشن اور معیارات: درخواست کے لحاظ سے کچھ سرٹیفیکیشنز یا معیارات درکار ہوسکتے ہیں۔ مثال کے طور پر، epoxy کوٹنگز کی موصلیت کو بجلی کی صنعت میں مخصوص برقی معیارات یا سرٹیفکیٹس کو پورا کرنے کی ضرورت پڑ سکتی ہے۔ اس بات کو یقینی بنائیں کہ تعمیل اور کارکردگی کو یقینی بنانے کے لیے منتخب کردہ کوٹنگ صنعت کے معیارات اور سرٹیفیکیشن پر پورا اترتی ہے۔
- کارکردگی اور استحکام: انسولیٹنگ ایپوکسی کوٹنگ کی مجموعی کارکردگی اور استحکام پر غور کریں۔ پائیدار موصلیت اور تحفظ کو یقینی بنانے کے لیے بہترین چپکنے والی، رگڑنے کے خلاف مزاحمت، اور طویل مدتی استحکام والی تہوں کو تلاش کریں۔ کوٹنگ کی جسمانی نقصان کے خلاف مزاحمت کا اندازہ لگائیں، جیسے اثر یا کھرچنا، جو موصلیت کی خصوصیات سے سمجھوتہ کر سکتا ہے۔
- لاگت اور قدر: آخر میں، انسولیٹنگ ایپوکسی کوٹنگ کی قیمت اور قدر کا اندازہ لگائیں۔ ابتدائی لاگت، پرت کی متوقع عمر، اور وقت کے ساتھ ساتھ ممکنہ دیکھ بھال یا متبادل اخراجات جیسے عوامل پر غور کریں۔ طویل مدتی کارکردگی اور پائیداری کے ساتھ پیشگی سرمایہ کاری کو متوازن کرنے سے کوٹنگ کی مجموعی قدر کا تعین کرنے میں مدد ملے گی۔
ماحولیاتی تحفظات
ماحولیاتی تحفظات epoxy کوٹنگز کے انتخاب اور استعمال میں اہم کردار ادا کرتے ہیں۔ ایسی کوٹنگز کا انتخاب کرنا جو مناسب موصلیت فراہم کرتی ہوں اور اپنی زندگی کے دوران ماحولیاتی اثرات کو کم سے کم کرتی ہوں۔ یہاں کچھ اہم ماحولیاتی تحفظات ہیں جن کو دھیان میں رکھنے کے لیے ایپوکسی کوٹنگز کی موصلیت کا انتخاب کرتے وقت:
- VOC مواد: غیر مستحکم نامیاتی مرکبات (VOCs) ایسے کیمیکل ہیں جو فضائی آلودگی میں حصہ ڈال سکتے ہیں اور صحت پر ممکنہ اثرات مرتب کر سکتے ہیں۔ انسولیٹنگ ایپوکسی کوٹنگز کا انتخاب کرتے وقت، کم VOC یا VOC فری فارمولیشنز کا انتخاب کریں۔ یہ کوٹنگز استعمال کے دوران کم نقصان دہ دھوئیں کا اخراج کرتی ہیں اور انڈور اور آؤٹ ڈور ہوا کے بہتر معیار میں حصہ ڈالتی ہیں۔
- مضر مادے: ایپوکسی کوٹنگ کی تشکیل میں خطرناک مادوں کی موجودگی کا اندازہ کریں۔ کچھ اضافی اشیاء، سالوینٹس، یا بھاری دھاتیں انسانی صحت یا ماحول کو نقصان پہنچا سکتی ہیں۔ محفوظ ہینڈلنگ، ٹھکانے لگانے اور طویل مدتی ماحولیاتی اثرات کو یقینی بناتے ہوئے، خطرناک مادوں سے پاک یا کم سطح والی کوٹنگز تلاش کریں۔
- بایوڈیگریڈیبلٹی: انسولیٹنگ ایپوکسی کوٹنگ کی بایوڈیگریڈیبلٹی پر غور کریں۔ بایوڈیگریڈیبل کوٹنگز وقت کے ساتھ قدرتی طور پر ٹوٹ جاتی ہیں، جس سے ماحول پر ان کے اثرات کم ہوتے ہیں۔ ان تہوں کو تلاش کریں جو قابل تجدید وسائل سے حاصل کی گئی ہیں یا جن کی بایوڈیگریڈیبلٹی کے لیے جانچ اور تصدیق کی گئی ہے۔
- توانائی کی کارکردگی: ایپوکسی کوٹنگز کی موصلیت اکثر گرمی کی منتقلی کو کم کرکے توانائی کی کارکردگی کو بہتر بناتی ہے۔ اعلی تھرمل مزاحمتی خصوصیات کے ساتھ کوٹنگز کا انتخاب کرکے، آپ برقی موصلیت، عمارت کی موصلیت، یا تھرمل رکاوٹوں جیسی ایپلی کیشنز میں توانائی کی کارکردگی کو بڑھا سکتے ہیں۔ اس سے توانائی کی کھپت میں کمی اور ماحولیاتی اثرات کم ہو سکتے ہیں۔
- استحکام اور لمبی عمر: بہترین پائیداری اور لمبی عمر کے ساتھ موصلی ایپوکسی کوٹنگز کا انتخاب کریں۔ پہننے، سنکنرن، یا انحطاط کے لیے زیادہ مزاحم کوٹنگز کو کم بار بار دیکھ بھال، دوبارہ استعمال اور ٹھکانے لگانے کی ضرورت ہوتی ہے۔ یہ کوٹنگز کے استعمال سے وابستہ مجموعی ماحولیاتی اثرات کو کم کرتا ہے۔
- پیکجنگ اور فضلہ: انسولیٹنگ ایپوکسی کوٹنگز کی پیکیجنگ اور ان کے استعمال کے دوران فضلہ پیدا کرنے پر غور کریں۔ ایسی کوٹنگز کا انتخاب کریں جو ری سائیکل یا ماحول دوست مواد میں پیک کی گئی ہوں۔ مزید برآں، کوٹنگز جو استعمال کے دوران فضلہ پیدا کرنے کو کم کرتی ہیں، جیسے کہ اوور سپرے یا کم سے کم مکسنگ کی ضروریات، ماحولیاتی اثرات کو کم کرنے میں مدد کر سکتی ہیں۔
- ماحولیاتی سرٹیفیکیشنز: ماحولیاتی سرٹیفیکیشنز حاصل کرنے والے یا تسلیم شدہ ماحولیاتی معیارات کی تعمیل کرنے والی epoxy کوٹنگز کو تلاش کریں۔ مثالوں میں سرٹیفکیٹ جیسے LEED (توانائی اور ماحولیاتی ڈیزائن میں قیادت) یا ISO 14001 ماحولیاتی انتظام کے معیارات کی پابندی شامل ہیں۔ یہ سرٹیفیکیشن اس بات کو یقینی بناتے ہیں کہ کوٹنگز سخت جانچ سے گزری ہیں اور ماحولیاتی کارکردگی کے مخصوص معیار پر پورا اترتی ہیں۔
- مناسب ڈسپوزل اور ری سائیکلنگ: epoxy کوٹنگز کی موصلیت کے لیے مناسب تصرف اور ری سائیکلنگ کے اختیارات پر غور کریں۔ مقامی قواعد و ضوابط اور رہنما خطوط کو چیک کریں تاکہ یہ یقینی بنایا جا سکے کہ کوٹنگز کو ان کے لائف سائیکل کے اختتام پر مناسب طریقے سے ضائع یا دوبارہ استعمال کیا جا سکتا ہے۔ کچھ کوٹنگز میں مخصوص ری سائیکلنگ پروگرام یا اختیارات دستیاب ہو سکتے ہیں۔
ان ماحولیاتی تحفظات کو مدنظر رکھتے ہوئے، آپ انسولیٹنگ ایپوکسی کوٹنگز کا انتخاب کر سکتے ہیں جو مناسب موصلیت فراہم کرتے ہیں اور ان کے ماحولیاتی اثرات کو کم کرتے ہیں۔ ماحول دوست کوٹنگز کا انتخاب پائیداری کی کوششوں میں حصہ ڈالتا ہے، آلودگی کو کم کرتا ہے، اور ایک صحت مند ماحولیاتی نظام کو فروغ دیتا ہے۔
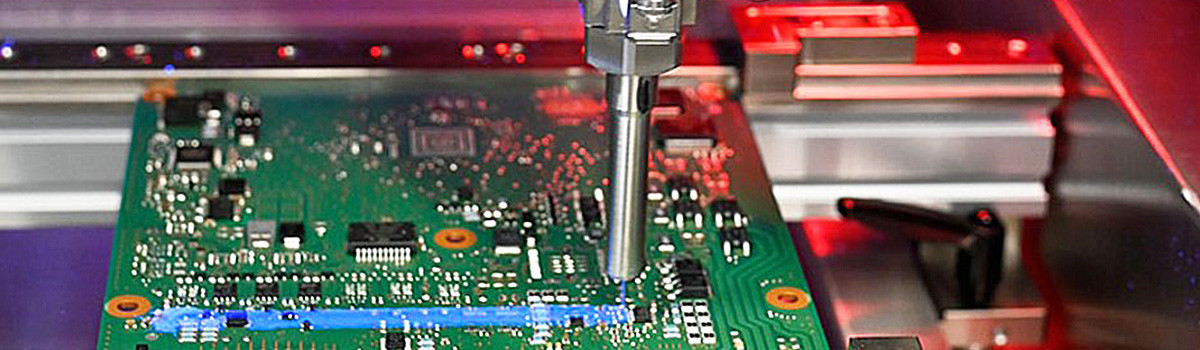
درخواست کی تکنیک اور تجاویز
ایپوکسی کوٹنگز کی موصلیت کے وقت بہترین نتائج حاصل کرنے کے لیے مناسب استعمال کی تکنیکیں ضروری ہیں۔ درج ذیل نکات ایک کامیاب ایپلی کیشن کو یقینی بنانے اور پرت کی کارکردگی کو بڑھانے میں مدد کریں گے۔
- سطح کی تیاری: انسولیٹنگ ایپوکسی کوٹنگ لگانے سے پہلے سطح کو اچھی طرح صاف اور تیار کریں۔ کسی بھی گندگی، دھول، چکنائی، یا موجودہ کوٹنگز کو ہٹا دیں جو چپکنے میں مداخلت کرسکتے ہیں. سطح کی تیاری کی تکنیکوں میں سینڈنگ، ڈیگریزنگ، یا مناسب صفائی ایجنٹوں کا استعمال شامل ہوسکتا ہے۔ کوٹنگ اور سبسٹریٹ کے لیے مخصوص سطح کی تیاری کے لیے مینوفیکچرر کی ہدایات پر عمل کریں۔
- اختلاط تناسب اور برتن کی زندگی: اختلاط کے تناسب اور برتن کی زندگی کے بارے میں مینوفیکچرر کی ہدایات پر احتیاط سے عمل کریں۔ انسولیٹنگ ایپوکسی کوٹنگز عام طور پر دو حصوں کے نظام ہیں جن میں رال اور سخت اجزاء کے درست اختلاط کی ضرورت ہوتی ہے۔ غلط اختلاط کا نتیجہ نامکمل علاج یا سمجھوتہ کارکردگی کا سبب بن سکتا ہے۔ برتن کی زندگی اور اجزاء کے ملنے کے بعد دستیاب کام کے وقت پر توجہ دیں۔ مناسب اطلاق کو یقینی بنانے کے لیے برتن کی زندگی کو زیادہ کرنے سے گریز کریں۔
- درخواست کا طریقہ: سطح اور پراجیکٹ کی ضروریات کی بنیاد پر انسولیٹنگ ایپوکسی کوٹنگ کے لیے مناسب درخواست کا طریقہ منتخب کریں۔ معیاری درخواست کے طریقوں میں برش، رولر، یا سپرے کی درخواست شامل ہے۔ چھوٹے علاقوں کے لیے برش اور رولرس استعمال کریں یا جب درستگی کی ضرورت ہو۔ سپرے ایپلی کیشن بڑے کمروں یا زیادہ یکساں تکمیل کے لیے موزوں ہے۔ درخواست کے طریقہ کار اور آلات سے متعلق مخصوص کوٹنگ کے لیے صنعت کار کی سفارشات پر عمل کریں۔
- درجہ حرارت اور نمی: درخواست کے دوران محیط درجہ حرارت اور نمی کے حالات پر غور کریں۔ زیادہ سے زیادہ کارکردگی کے لیے epoxy کوٹنگز کی موصلیت میں مخصوص درجہ حرارت اور نمی کے تقاضے ہو سکتے ہیں۔ درخواست اور علاج کے دوران تجویز کردہ درجہ حرارت کی حد اور نمی کے حالات کے بارے میں مینوفیکچرر کے رہنما خطوط پر عمل کریں۔ انتہائی درجہ حرارت یا زیادہ نمی کوٹنگ کے علاج کے وقت اور مجموعی کارکردگی کو متاثر کر سکتی ہے۔
- درخواست کی موٹائی: مطلوبہ موصلیت اور تحفظ کے لیے تجویز کردہ موٹائی پر انسولیٹنگ ایپوکسی کوٹنگ لگائیں۔ کوٹنگ کی کافی موٹائی موصلیت کی خصوصیات سے سمجھوتہ کر سکتی ہے، جب کہ ضرورت سے زیادہ موٹائی علاج کے مسائل یا غلط چپکنے کا باعث بن سکتی ہے۔ گیلی فلم کی موٹائی گیج کا استعمال کریں تاکہ پوری درخواست کے دوران کوٹنگ کی موٹائی مستقل اور درست ہو۔
- وینٹیلیشن اور حفاظت: دھوئیں یا بخارات کے سانس کو کم سے کم کرنے کے لیے درخواست کے علاقے میں مناسب وینٹیلیشن کو یقینی بنائیں۔ مناسب ذاتی حفاظتی سامان (پی پی ای) کا استعمال کریں جیسا کہ مینوفیکچرر تجویز کرتا ہے، جیسے دستانے، چشمیں، یا سانس کی حفاظت۔ درخواست کے عمل کے دوران اپنی اور دوسروں کی حفاظت کے لیے حفاظتی ہدایات اور ضوابط پر عمل کریں۔
- کیورنگ اور خشک کرنے کا وقت: موصلیت والی ایپوکسی کوٹنگ کے لیے کافی کیورنگ اور خشک ہونے کا وقت دیں۔ مناسب چپکنے اور کارکردگی کے لیے تجویز کردہ علاج کے وقت اور ماحولیاتی حالات کے بارے میں مینوفیکچرر کی ہدایات پر عمل کریں۔ کوٹنگ کی سطح کو ضرورت سے زیادہ نمی یا مکینیکل تناؤ کے تابع کرنے سے گریز کریں جب تک کہ کوٹنگ مکمل طور پر ٹھیک نہ ہوجائے۔
- معائنہ اور دیکھ بھال: کسی بھی نقصان یا پہننے کی علامات کے لیے لیپت سطح کا باقاعدگی سے معائنہ کریں۔ انسولیٹنگ ایپوکسی کوٹنگ کی مسلسل تاثیر کو یقینی بنانے کے لیے معمول کی دیکھ بھال کریں۔ مزید چوٹ یا بگاڑ کو روکنے کے لیے کسی بھی مسئلے کو فوری طور پر حل کریں۔
ایپلی کیشن کی ان تکنیکوں اور تجاویز پر عمل کرتے ہوئے، آپ انسولیٹنگ ایپوکسی کوٹنگز لگاتے وقت کامیاب نتائج حاصل کر سکتے ہیں۔ سطح کی مناسب تیاری، درست اختلاط، مناسب اطلاق کے طریقے، اور علاج کے رہنما خطوط پر عمل کرنا آپ کی درخواست کی مطلوبہ موصلیت اور تحفظ کو یقینی بنانے میں مدد کرے گا۔
علاج اور خشک کرنے کا عمل
ایپوکسی کوٹنگز کی موصلیت کے لیے علاج اور خشک کرنے کا عمل ایک اہم مرحلہ ہے جو کوٹنگ کی حتمی خصوصیات اور کارکردگی کا تعین کرتا ہے۔ مناسب علاج ایک مضبوط، پائیدار، اور مکمل طور پر موصل پرت کو یقینی بناتا ہے۔ epoxy کوٹنگز کی موصلیت کے علاج اور خشک کرنے کے عمل کے اہم عوامل اور تحفظات یہ ہیں:
- مینوفیکچرر کی ہدایات پر عمل کریں: کوٹنگ کے لیے درکار ماحولیاتی حالات اور ٹھیک کرنے اور خشک کرنے کے اوقات کے بارے میں مخصوص رہنمائی کے لیے ہمیشہ مینوفیکچرر کی ہدایات اور تکنیکی ڈیٹا شیٹ کا حوالہ دیں۔ مختلف epoxy کوٹنگز میں مختلف علاج کے عمل اور تجویز کردہ خشک ہونے کے اوقات ہوسکتے ہیں۔
- محیطی درجہ حرارت: ایپوکسی کوٹنگز کا علاج کرنے کا عمل درجہ حرارت پر منحصر ہے۔ زیادہ تر ایپوکسی کوٹنگز کو مناسب علاج کے لیے کم سے کم اور زیادہ سے زیادہ محیطی درجہ حرارت کی حد کی ضرورت ہوتی ہے۔ اس بات کو یقینی بنائیں کہ پورے کیورنگ اور خشک کرنے کے عمل کے دوران محیطی درجہ حرارت مخصوص حد کے اندر آتا ہے۔ انتہائی گرم اور سرد درجہ حرارت کیورنگ کے عمل اور کوٹنگ کی حتمی کارکردگی کو بری طرح متاثر کر سکتا ہے۔
- رشتہ دار نمی: نمی کی سطح epoxy کوٹنگ کی موصلیت کے علاج اور خشک ہونے پر بھی اثر انداز ہو سکتی ہے۔ زیادہ نمی والے ماحول میں، پرت سے نمی کے سست بخارات کی وجہ سے علاج کا وقت طویل ہو سکتا ہے۔ اس کے برعکس، کم نمی کی وجہ سے کوٹنگ بہت جلد ٹھیک ہو سکتی ہے، اس کی سالمیت پر سمجھوتہ کر سکتا ہے۔ زیادہ سے زیادہ علاج کے لیے مینوفیکچرر کے ذریعہ تجویز کردہ نمی کی سطح کو برقرار رکھیں۔
- وینٹیلیشن: مناسب ہوا کی گردش اور دھوئیں یا بخارات کی کھپت کو یقینی بنانے کے لیے علاج اور خشک ہونے کے دوران مناسب وینٹیلیشن بہت ضروری ہے۔ اچھا وینٹیلیشن علاج کے عمل کو آسان بنانے میں مدد کرتا ہے اور سالوینٹس کے پھنسنے کے خطرے کو کم کرتا ہے، جو کوٹنگ کی کارکردگی کو متاثر کر سکتا ہے۔
- کیورنگ ٹائم: ایپوکسی کوٹنگز کی موصلیت کا علاج کرنے کا وقت مخصوص فارمولیشن، لگائی گئی پرت کی موٹائی اور محیط حالات کے لحاظ سے مختلف ہو سکتا ہے۔ مکمل کراس لنکنگ اور مطلوبہ خصوصیات کی نشوونما کو یقینی بنانے کے لیے مینوفیکچرر کے ذریعہ تجویز کردہ کیورنگ ٹائم کی اجازت دینا ضروری ہے۔ علاج کے عمل کے دوران نمی، دھول یا مکینیکل تناؤ کا قبل از وقت نمائش کوٹنگ کی کارکردگی پر سمجھوتہ کر سکتا ہے۔
- خشک ہونے کا وقت: خشک ہونے کا وقت اس وقت ہوتا ہے جب سالوینٹ کوٹنگ سے بخارات بنتے ہیں۔ خشک ہونے کا وقت کوٹنگ کی موٹائی، درجہ حرارت، نمی اور وینٹیلیشن کی بنیاد پر مختلف ہو سکتا ہے۔ مناسب فلم کی تشکیل کو حاصل کرنے اور قبل از وقت ہینڈلنگ یا نمائش سے بچنے کے لیے کوٹنگ کے لیے تجویز کردہ خشک ہونے کا وقت دینا بہت ضروری ہے۔
- مکمل علاج: اگرچہ تجویز کردہ خشک ہونے کے بعد کوٹنگ چھونے پر خشک محسوس ہو سکتی ہے، لیکن یہ نوٹ کرنا ضروری ہے کہ مکمل علاج میں زیادہ وقت لگ سکتا ہے۔ مکمل علاج سے مراد ایپوکسی کوٹنگ کی مکمل کیمیکل کراس لنکنگ اور سخت ہونا ہے۔ لیپت سطح کو بھاری بوجھ، کھرچنے، یا دیگر تناؤ کا نشانہ بنانے سے پہلے تجویز کردہ مکمل علاج کے وقت کے بارے میں مینوفیکچرر کی ہدایات پر عمل کریں۔
- پوسٹ کیورنگ: کچھ انسولیٹنگ ایپوکسی کوٹنگز پوسٹ کیورنگ سے فائدہ اٹھا سکتی ہیں تاکہ ان کی خصوصیات کو مزید بہتر بنایا جا سکے۔ پوسٹ کیورنگ میں ٹھیک شدہ پرت کو ایک مخصوص مدت کے لیے بلند درجہ حرارت پر رکھنا شامل ہے۔ یہ عمل کوٹنگ کی کیمیائی مزاحمت، سختی اور آسنجن کو بہتر بنا سکتا ہے۔ اگر قابل اطلاق ہو تو، تجویز کردہ پوسٹ کیورنگ کے عمل سے متعلق مینوفیکچرر کے رہنما خطوط کا حوالہ دیں۔
مینوفیکچرر کی ہدایات پر احتیاط سے عمل کرتے ہوئے، مناسب ماحول کو برقرار رکھتے ہوئے، مناسب علاج اور خشک ہونے کے وقت کی اجازت دے کر، اور مناسب وینٹیلیشن کو یقینی بنا کر، آپ ایپوکسی کوٹنگز کی موصلیت میں بہترین نتائج حاصل کر سکتے ہیں۔ مناسب طریقے سے ٹھیک اور خشک کوٹنگز مطلوبہ استعمال کے لیے مطلوبہ برقی موصلیت اور تھرمل مزاحمت فراہم کریں گی۔
انسولیٹنگ ایپوکسی کوٹنگز کی دیکھ بھال اور مرمت
برقی آلات اور انفراسٹرکچر کی حفاظت اور موصلیت کے لیے مختلف صنعتوں میں انسولیٹنگ ایپوکسی کوٹنگز بڑے پیمانے پر استعمال ہوتی ہیں۔ یہ کوٹنگز ایک پائیدار حفاظتی رکاوٹ فراہم کرتی ہیں جو نمی، کیمیکلز اور دیگر آلودگیوں کو نیچے کی سطحوں تک پہنچنے سے روکتی ہے۔ تاہم، کسی دوسرے کوٹنگ سسٹم کی طرح، epoxy کوٹنگز کی موصلیت کو ان کی تاثیر اور لمبی عمر کو یقینی بنانے کے لیے دیکھ بھال اور مرمت کی ضرورت پڑ سکتی ہے۔
epoxy کوٹنگز کی موصلیت کی دیکھ بھال میں بنیادی طور پر باقاعدہ معائنہ اور صفائی شامل ہوتی ہے۔ لیپت سطحوں کا وقتاً فوقتاً معائنہ کریں تاکہ نقصان کی کسی بھی علامت کی نشاندہی کی جا سکے، جیسے کہ دراڑیں، چھالے یا چھلکے۔ براہ کرم ان علاقوں پر پوری توجہ دیں جو سخت حالات یا مکینیکل تناؤ سے دوچار ہیں، کیونکہ وہ نقصان کا زیادہ خطرہ رکھتے ہیں۔ اگر کسی بھی مسئلے کا پتہ چل جائے تو مزید بگاڑ کو روکنے کے لیے فوری طور پر ان کا ازالہ کریں۔
مٹی، دھول، تیل، اور وقت کے ساتھ جمع ہونے والے دیگر آلودگیوں کو دور کرنے کے لیے لیپت سطحوں کی صفائی ضروری ہے۔ سطحوں کو نرمی سے صاف کرنے کے لیے ہلکے، غیر کھرچنے والے کلینر اور نرم برش یا کپڑوں کا استعمال کریں۔ سخت کیمیکلز یا کھرچنے والے مواد سے پرہیز کریں جو کوٹنگ کو کھرچتے یا خراب کرتے ہیں۔ باقاعدگی سے صفائی epoxy کوٹنگ کی موصلی خصوصیات کو برقرار رکھنے میں مدد کرتی ہے اور کنڈکٹیو مواد کی تعمیر کو روکتی ہے جو اس کی تاثیر سے سمجھوتہ کر سکتی ہے۔
جب مرمت کی بات آتی ہے تو نقصان کی حد کے لحاظ سے نقطہ نظر مختلف ہو سکتا ہے۔ آپ epoxy مرمت کٹس کا استعمال کر سکتے ہیں جو خاص طور پر چھوٹے دراڑوں یا چپس جیسی معمولی چوٹوں کے لیے کوٹنگز کی موصلیت کے لیے بنائی گئی ہیں۔ ان کٹس میں عام طور پر ایپوکسی فلر اور اسے صحیح طریقے سے لگانے کی ہدایات شامل ہوتی ہیں۔ تباہ شدہ جگہ کو اچھی طرح سے صاف کریں، آلات کے ساتھ فراہم کردہ ہدایات پر عمل کریں، اور تباہ شدہ حصے پر ایپوکسی فلر استعمال کریں۔ اسے کارخانہ دار کی سفارشات کے مطابق علاج کرنے دیں۔
ایسی صورتوں میں جہاں نقصان زیادہ اہم ہے، کوٹنگ کے خراب حصے کو ہٹانا ضروری ہو سکتا ہے جیسا کہ epoxy کی موصلیت کی نئی تہہ لگانا ضروری ہے۔ اس کے لیے سطح کی احتیاط سے تیاری کی ضرورت ہوتی ہے، بشمول نئی کوٹنگ کے مناسب چپکنے کو یقینی بنانے کے لیے نقصان کے ارد گرد کے علاقے کی صفائی اور کھردرا کرنا۔ نئی ایپوکسی کوٹنگ لگانے کے بارے میں مینوفیکچرر کی ہدایات پر عمل کریں، بشمول علاج کے اوقات اور درجہ حرارت کی ضروریات۔
بعض صورتوں میں، انسولیٹنگ ایپوکسی کوٹنگز کو برقرار رکھنے اور مرمت کرنے کے لیے پیشہ ورانہ مدد حاصل کرنا زیادہ عملی ہو سکتا ہے۔ تجربہ کار ٹھیکیدار یا کوٹنگ کے ماہرین نقصان کی حد کا اندازہ لگا سکتے ہیں، مرمت کا موزوں ترین طریقہ تجویز کر سکتے ہیں، اور اس بات کو یقینی بنا سکتے ہیں کہ بہتر کوٹنگ ضروری معیارات اور تقاضوں کو پورا کرتی ہے۔
یاد رکھیں کہ epoxy کوٹنگز کی موصلیت کی عمر بڑھانے کے لیے باقاعدہ معائنہ اور احتیاطی دیکھ بھال بہت ضروری ہے۔ معمولی مسائل کو جلد حل کرکے اور صفائی کے مناسب طریقہ کار پر عمل کرکے، آپ وسیع مرمت کی ضرورت کو کم کر سکتے ہیں اور برقی آلات اور انفراسٹرکچر کی حفاظت اور موصلیت میں کوٹنگ کی مسلسل تاثیر کو یقینی بنا سکتے ہیں۔
نتیجہ
برقی اجزاء اور آلات کو مختلف بیرونی عوامل سے بچانے کے لیے ایپوکسی کوٹنگز کی موصلیت بہت اہم ہے۔ الیکٹرانک اجزاء سے لے کر سرکٹ بورڈز، موٹرز اور کیبلز تک کی ایپلی کیشنز کے ساتھ، یہ کوٹنگز نمی، کیمیکلز اور جسمانی نقصان کے خلاف ضروری تحفظ فراہم کرتی ہیں۔ مناسب موصل epoxy کوٹنگ کا انتخاب ماحولیاتی حالات، کارکردگی کی ضروریات، اور درخواست کی تکنیک پر منحصر ہے. ایپوکسی کوٹنگز کی موصلیت سے وابستہ فوائد اور تحفظات کو سمجھ کر، صنعتیں اپنے برقی نظام اور آلات کی پائیداری، وشوسنییتا اور لمبی عمر کو بڑھانے کے لیے باخبر انتخاب کر سکتی ہیں۔