Underfill epoxi
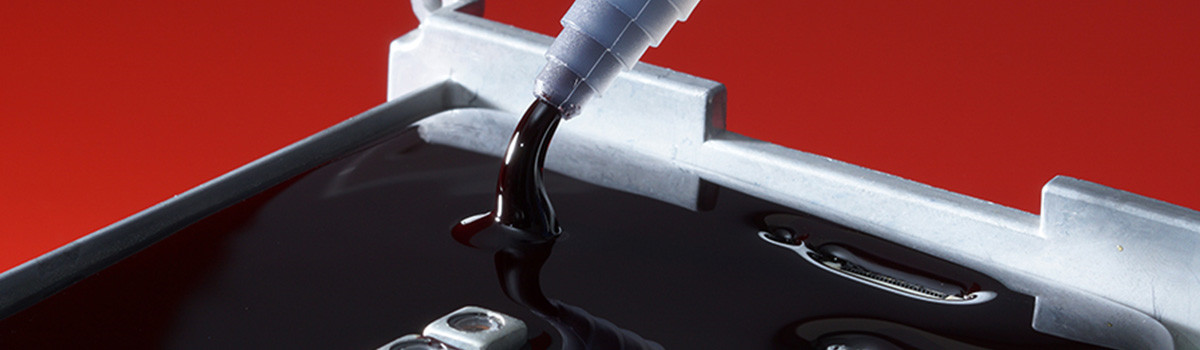
Underfill-epoxi är en typ av lim som används för att förbättra elektroniska komponenters tillförlitlighet, särskilt i halvledarförpackningsapplikationer. Den fyller gapet mellan förpackningen och det tryckta kretskortet (PCB), vilket ger mekaniskt stöd och spänningsavlastning för att förhindra termisk expansion och sammandragningsskador. Underfill-epoxi förbättrar också paketets elektriska prestanda genom att minska parasitinduktansen och kapacitansen. I den här artikeln utforskar vi de olika applikationerna av underfill-epoxi, de olika typerna som finns och deras fördelar.
Vikten av underfyllningsepoxi i halvledarförpackningar
Underfill-epoxi är avgörande i halvledarförpackningar, vilket ger mekanisk förstärkning och skydd till ömtåliga mikroelektroniska komponenter. Det är ett specialiserat självhäftande material som används för att fylla gapet mellan halvledarchipet och paketets substrat, vilket förbättrar tillförlitligheten och prestandan hos elektroniska enheter. Här kommer vi att utforska vikten av underfylld epoxi i halvledarförpackningar.
En av de primära funktionerna hos underfylld epoxi är att förbättra förpackningens mekaniska styrka och tillförlitlighet. Under drift utsätts halvledarchips för olika mekaniska påfrestningar, såsom termisk expansion och sammandragning, vibrationer och mekaniska stötar. Dessa påkänningar kan leda till bildning av sprickor i lödfogen, vilket kan orsaka elektriska fel och minska enhetens totala livslängd. Underfill-epoxi fungerar som ett spänningsreducerande medel genom att fördela den mekaniska spänningen jämnt över chipet, substratet och lödfogarna. Det minimerar effektivt bildningen av sprickor och förhindrar spridningen av befintliga sprickor, vilket säkerställer förpackningens långsiktiga tillförlitlighet.
En annan kritisk aspekt av underfill-epoxi är dess förmåga att förbättra den termiska prestandan hos halvledarenheter. Värmeavledning blir ett stort problem eftersom elektroniska enheter krymper i storlek och ökar effekttätheten, och överdriven värme kan försämra prestandan och tillförlitligheten hos halvledarchippet. Underfill-epoxi har utmärkta värmeledningsförmåga, vilket gör att den effektivt kan överföra värme från chipet och distribuera den genom hela förpackningen. Detta hjälper till att upprätthålla optimala driftstemperaturer och förhindrar hotspots, vilket förbättrar enhetens övergripande värmehantering.
Underfill-epoxi skyddar även mot fukt och föroreningar. Fuktinträngning kan leda till korrosion, elektriskt läckage och tillväxt av ledande material, vilket resulterar i enhetsfel. Underfill-epoxi fungerar som en barriär, förseglar känsliga områden och förhindrar att fukt kommer in i förpackningen. Den erbjuder också skydd mot damm, smuts och andra föroreningar som kan påverka den elektriska prestandan hos halvledarchippet negativt. Genom att skydda chippet och dess sammankopplingar säkerställer underfill-epoxi enhetens långsiktiga tillförlitlighet och funktionalitet.
Dessutom möjliggör underfylld epoxi miniatyrisering i halvledarförpackningar. Med den ständiga efterfrågan på mindre och mer kompakta enheter tillåter underfylld epoxi användning av flip-chip och chip-skala förpackningstekniker. Dessa tekniker innebär att chippet monteras direkt på förpackningssubstratet, vilket eliminerar behovet av trådbindning och reducerar förpackningsstorleken. Underfill-epoxi ger strukturellt stöd och upprätthåller integriteten hos chip-substratgränssnittet, vilket möjliggör en framgångsrik implementering av dessa avancerade förpackningsteknologier.
Hur Underfill Epoxy löser utmaningarna
Halvledarförpackningar spelar en avgörande roll för elektroniska enheters prestanda, tillförlitlighet och livslängd. Det innebär att kapsla in integrerade kretsar (IC) i skyddande höljen, tillhandahålla elektriska anslutningar och avleda värme som genereras under drift. Emellertid står halvledarförpackningar inför flera utmaningar, inklusive termisk stress och skevhet, vilket avsevärt kan påverka de förpackade enheternas funktionalitet och tillförlitlighet.
En av de främsta utmaningarna är termisk stress. Integrerade kretsar genererar värme under drift, och otillräcklig avledning kan öka temperaturen i förpackningen. Denna temperaturvariation resulterar i termisk stress när olika material i förpackningen expanderar och drar ihop sig med olika hastigheter. Den ojämna expansionen och sammandragningen kan orsaka mekanisk påkänning, vilket leder till lödfogsfel, delaminering och sprickor. Termisk stress kan äventyra förpackningens elektriska och mekaniska integritet, vilket i slutändan påverkar enhetens prestanda och tillförlitlighet.
Warpage är en annan kritisk utmaning i halvledarförpackningar. Skevning avser böjning eller deformation av förpackningssubstratet eller hela förpackningen. Det kan uppstå under förpackningsprocessen eller på grund av termisk stress. Skevhet orsakas i första hand av bristande överensstämmelse i termisk expansionskoefficient (CTE) mellan olika material i förpackningen. Till exempel kan CTE för kiselformen, substratet och formblandningen skilja sig avsevärt. När de utsätts för temperaturförändringar expanderar eller drar dessa material ihop sig i olika takt, vilket leder till skevhet.
Warpage utgör flera problem för halvledarpaket:
- Det kan resultera i stresskoncentrationspunkter, vilket ökar sannolikheten för mekaniska fel och minskar lådans tillförlitlighet.
- Skevhet kan leda till svårigheter i monteringsprocessen, eftersom det påverkar inriktningen av paketet med andra komponenter, såsom kretskortet (PCB). Denna felinställning kan försämra elektriska anslutningar och orsaka prestandaproblem.
- Warpage kan påverka paketets övergripande formfaktor, vilket gör det utmanande att integrera enheten i små formfaktorapplikationer eller tätbefolkade PCB:er.
Olika tekniker och strategier används i halvledarförpackningar för att möta dessa utmaningar. Dessa inkluderar användning av avancerade material med matchande CTE för att minimera termisk stress och skevhet. Termomekaniska simuleringar och modellering utförs för att förutsäga paketets beteende under olika termiska förhållanden. Designändringar, såsom införande av avspänningsstrukturer och optimerade layouter, implementeras för att minska termisk stress och skevhet. Dessutom hjälper utvecklingen av förbättrade tillverkningsprocesser och utrustning till att minimera förekomsten av skevhet under montering.
Fördelar med Underfill Epoxi
Underfill-epoxi är en kritisk komponent i halvledarförpackningar som erbjuder flera fördelar. Detta specialiserade epoximaterial appliceras mellan halvledarchipset och paketets substrat, vilket ger mekanisk förstärkning och hanterar olika utmaningar. Här är några av de kritiska fördelarna med underfylld epoxi:
- Förbättrad mekanisk tillförlitlighet: En av de främsta fördelarna med underfill-epoxi är dess förmåga att förbättra den mekaniska tillförlitligheten hos halvledarpaket. Underfill-epoxi skapar en sammanhängande bindning som förbättrar den övergripande strukturella integriteten genom att fylla luckorna och tomrummen mellan chipet och substratet. Detta hjälper till att förhindra att paketet skenar, minskar risken för mekaniska fel och förbättrar motståndet mot yttre påfrestningar som vibrationer, stötar och termisk cykling. Den förbättrade mekaniska tillförlitligheten leder till ökad produkthållbarhet och längre livslängd för enheten.
- Termisk stressavledning: Underfill-epoxi hjälper till att avleda termisk stress i förpackningen. Integrerade kretsar genererar värme under drift, och otillräcklig avledning kan resultera i temperaturvariationer i behållaren. Underfill-epoximaterialet, med sin lägre termiska expansionskoefficient (CTE) jämfört med spån- och substratmaterialen, fungerar som ett buffertskikt. Den absorberar den mekaniska belastningen som orsakas av termisk stress, vilket minskar risken för lödfogsfel, delaminering och sprickor. Genom att avleda termisk stress hjälper underfylld epoxi till att bibehålla förpackningens elektriska och mekaniska integritet.
- Förbättrad elektrisk prestanda: Underfyllningsepoxi påverkar den elektriska prestandan hos halvledarenheter positivt. Epoximaterialet fyller mellanrummen mellan chipet och substratet, vilket minskar parasitisk kapacitans och induktans. Detta resulterar i förbättrad signalintegritet, minskade signalförluster och förbättrad elektrisk anslutning mellan chipet och resten av paketet. De minskade parasiteffekterna bidrar till bättre elektrisk prestanda, högre dataöverföringshastigheter och ökad enhets tillförlitlighet. Dessutom ger underfylld epoxi isolering och skydd mot fukt, föroreningar och andra miljöfaktorer som kan försämra den elektriska prestandan.
- Avspänning och förbättrad montering: Underfyllningsepoxi fungerar som en avspänningsmekanism vid montering. Epoximaterialet kompenserar för CTE-felpassningen mellan chipet och substratet, vilket minskar den mekaniska påfrestningen under temperaturförändringar. Detta gör monteringsprocessen mer tillförlitlig och effektiv, vilket minimerar risken för paketskador eller felinriktning. Den kontrollerade spänningsfördelningen som tillhandahålls av underfyllningsepoxin hjälper också till att säkerställa korrekt inriktning med andra komponenter på kretskortet (PCB) och förbättrar det totala monteringsutbytet.
- Miniatyrisering och formfaktoroptimering: Underfill-epoxi möjliggör miniatyrisering av halvledarpaket och optimering av formfaktorn. Genom att tillhandahålla strukturell förstärkning och spänningsavlastning möjliggör underfill-epoxi design och tillverkning av mindre, tunnare och mer kompakta förpackningar. Detta är särskilt viktigt för applikationer som mobila enheter och bärbar elektronik, där utrymmet är en premie. Förmågan att optimera formfaktorer och uppnå högre komponentdensiteter bidrar till mer avancerade och innovativa elektroniska enheter.
Typer av underfyllningsepoxi
Flera typer av underfyllningsepoxiformuleringar finns tillgängliga i halvledarförpackningar, var och en utformad för att möta specifika krav och möta olika utmaningar. Här är några vanliga typer av underfyllningsepoxi:
- Kapillär underfyllningsepoxi: Kapillärunderfyllningsepoxi är den mest traditionella och mest använda typen. En lågviskös epoxi flödar in i gapet mellan chipet och substratet genom kapillärverkan. Kapillärunderfyllning fördelas vanligtvis på kanten av chipet, och när förpackningen värms upp flyter epoxin under chipet och fyller tomrummen. Denna typ av underfyllnad är lämplig för förpackningar med små luckor och ger bra mekanisk förstärkning.
- No-Flow Underfill Epoxi: No-Flow underfill epoxi är en högviskös formulering som inte flyter under härdning. Den appliceras som en förapplicerad epoxi eller som en film mellan spånet och underlaget. No-flow underfill epoxi är särskilt användbar för flip-chip-paket, där lödbultarna direkt interagerar med substratet. Det eliminerar behovet av kapillärflöde och minskar risken för lödfogsskador vid montering.
- Wafer-Level Underfill (WLU): Wafer-level underfill är en underfill-epoxi som appliceras på wafer-nivå innan de enskilda chipsen söndras. Det innebär att underfyllningsmaterialet fördelas över hela skivans yta och härdas. Underfyllning på wafernivå erbjuder flera fördelar, inklusive enhetlig täckning av underfyllningen, minskad monteringstid och förbättrad processkontroll. Det används ofta för tillverkning av stora volymer av små enheter.
- Formgjuten underfyllning (MUF): Formgjuten underfyllning är en underfyllningsepoxi som appliceras under inkapslingsgjutning. Underfyllningsmaterialet fördelas på substratet och sedan kapslas chipet och substratet in i en formmassa. Under formningen flyter epoxin och fyller gapet mellan spånet och substratet, vilket ger underfyllning och inkapsling i ett enda steg. Gjuten underfyllning ger utmärkt mekanisk förstärkning och förenklar monteringsprocessen.
- Non-Conductive Underfill (NCF): Icke-ledande underfill-epoxi är speciellt framtagen för att ge elektrisk isolering mellan lödfogarna på chipet och substratet. Den innehåller isolerande fyllmedel eller tillsatser som förhindrar elektrisk ledningsförmåga. NCF används i applikationer där elektrisk kortslutning mellan intilliggande lödfogar är ett problem. Den erbjuder både mekanisk förstärkning och elektrisk isolering.
- Termiskt ledande underfyllnad (TCU): Termiskt ledande underfyllningsepoxi är utformad för att förbättra förpackningens värmeavledningsförmåga. Den innehåller termiskt ledande fyllmedel, såsom keramiska eller metallpartiklar, som förbättrar den termiska ledningsförmågan hos underfyllningsmaterialet. TCU används i applikationer där effektiv värmeöverföring är avgörande, såsom högeffektsenheter eller de som arbetar i krävande termiska miljöer.
Det här är bara några exempel på de olika typerna av underfyllningsepoxi som används i halvledarförpackningar. Valet av lämplig underfyllningsepoxi beror på faktorer som förpackningsdesign, monteringsprocess, termiska krav och elektriska överväganden. Varje underfill-epoxi ger specifika fördelar och är skräddarsydd för att möta de unika behoven för olika applikationer.
Kapillär underfyllning: Låg viskositet och hög tillförlitlighet
Kapillärunderfyllning hänvisar till en process som används i halvledarförpackningsindustrin för att öka tillförlitligheten hos elektroniska enheter. Det innebär att fylla luckorna mellan ett mikroelektroniskt chip och dess omgivande förpackning med ett vätskematerial med låg viskositet, vanligtvis ett epoxibaserat harts. Detta underfyllningsmaterial ger strukturellt stöd, förbättrar termisk avledning och skyddar spånet från mekanisk påfrestning, fukt och andra miljöfaktorer.
En av de kritiska egenskaperna hos kapillär underfyllning är dess låga viskositet. Underfyllningsmaterialet är formulerat för att ha en relativt låg densitet, vilket gör att det lätt flyter in i de smala springorna mellan spånet och förpackningen under underfyllningsprocessen. Detta säkerställer att underfyllningsmaterialet effektivt kan penetrera och fylla alla tomrum och luftgap, vilket minimerar risken för tomrumsbildning och förbättrar den övergripande integriteten hos chip-paketgränssnittet.
Kapillära underfyllningsmaterial med låg viskositet erbjuder också flera andra fördelar. För det första underlättar de det effektiva flödet av materialet under chipet, vilket leder till minskad processtid och ökad produktionsgenomströmning. Detta är särskilt viktigt i högvolymtillverkningsmiljöer där tid och kostnadseffektivitet är avgörande.
För det andra möjliggör den låga viskositeten bättre vätnings- och vidhäftningsegenskaper hos underfyllningsmaterialet. Det låter materialet spridas jämnt och bilda starka bindningar med chipet och förpackningen, vilket skapar en pålitlig och robust inkapsling. Detta säkerställer att chippet är säkert skyddat från mekaniska påfrestningar som termisk cykling, stötar och vibrationer.
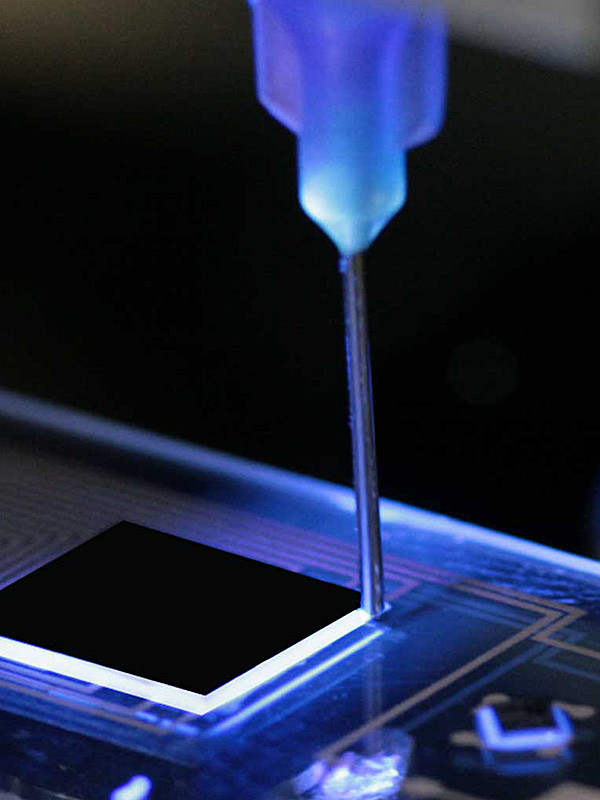
En annan avgörande aspekt av kapillärunderfyllningar är deras höga tillförlitlighet. De lågviskösa underfyllnadsmaterialen är speciellt framtagna för att uppvisa utmärkt termisk stabilitet, elektriska isoleringsegenskaper och motståndskraft mot fukt och kemikalier. Dessa egenskaper är väsentliga för att säkerställa paketerade elektroniska enheters långsiktiga prestanda och tillförlitlighet, särskilt i krävande tillämpningar som fordon, flyg och telekommunikation.
Dessutom är kapillärunderfyllnadsmaterial utformade för att ha hög mekanisk hållfasthet och utmärkt vidhäftning till olika substratmaterial, inklusive metaller, keramik och organiska material som vanligtvis används i halvledarförpackningar. Detta gör det möjligt för underfyllningsmaterialet att fungera som en spänningsbuffert, som effektivt absorberar och avleder mekaniska spänningar som genereras under drift eller miljöexponering.
No-Flow Underfill: Självdispenserande och hög genomströmning
No-flow underfill en specialiserad process som används i halvledarförpackningsindustrin för att förbättra tillförlitligheten och effektiviteten hos elektroniska enheter. Till skillnad från kapillärunderfyllningar, som förlitar sig på flöde av lågviskösa material, använder underfyllningar utan flöde ett självdispenserande tillvägagångssätt med högviskösa material. Denna metod erbjuder flera fördelar, inklusive självinställning, hög genomströmning och förbättrad tillförlitlighet.
En av de kritiska egenskaperna hos underfyllning utan flöde är dess självdispenserande förmåga. Underfyllningsmaterialet som används i denna process är formulerat med en högre viskositet, vilket hindrar det från att rinna fritt. Istället dispenseras underfyllningsmaterialet på chip-paketgränssnittet på ett kontrollerat sätt. Denna kontrollerade dispensering möjliggör exakt placering av underfyllningsmaterialet, vilket säkerställer att det appliceras endast på önskade områden utan att svämma över eller spridas okontrollerat.
Den självdispenserande karaktären hos no-flow underfill erbjuder flera fördelar. För det första tillåter det självinriktning av underfyllningsmaterialet. När underfyllningen matas ut, anpassar den sig naturligt till chipet och förpackningen, och fyller luckorna och tomrummen jämnt. Detta eliminerar behovet av exakt positionering och inriktning av spånet under underfyllningsprocessen, vilket sparar tid och ansträngning vid tillverkningen.
För det andra möjliggör den självdispenserande funktionen hos no-flow underfills hög genomströmning i produktionen. Dispenseringsprocessen kan automatiseras, vilket möjliggör snabb och konsekvent applicering av underfyllningsmaterialet över flera chips samtidigt. Detta förbättrar den totala produktionseffektiviteten och minskar tillverkningskostnaderna, vilket gör det särskilt fördelaktigt för tillverkningsmiljöer med stora volymer.
Dessutom är underfyllningsmaterial utan flöde utformade för att ge hög tillförlitlighet. De högviskösa underfyllnadsmaterialen erbjuder förbättrat motstånd mot termisk cykling, mekaniska påfrestningar och miljöfaktorer, vilket säkerställer långtidsprestanda för de förpackade elektroniska enheterna. Materialen uppvisar utmärkt termisk stabilitet, elektriska isoleringsegenskaper och motståndskraft mot fukt och kemikalier, vilket bidrar till enheternas övergripande tillförlitlighet.
Dessutom har de högviskösa underfyllnadsmaterialen som används i no-flow underfill förbättrad mekanisk styrka och vidhäftningsegenskaper. De bildar starka bindningar med chipet och förpackningen, absorberar och avleder effektivt mekaniska påfrestningar som genereras under drift eller miljöexponering. Detta hjälper till att skydda chippet från potentiell skada och förbättrar enhetens motståndskraft mot yttre stötar och vibrationer.
Gjuten underfyllning: Högt skydd och integration
Formgjuten underfyllning är en avancerad teknik som används inom halvledarförpackningsindustrin för att ge höga nivåer av skydd och integration för elektroniska enheter. Det innebär att kapsla in hela chipet och dess omgivande förpackning med en formmassa som innehåller underfyllningsmaterial. Denna process erbjuder betydande fördelar när det gäller skydd, integration och övergripande tillförlitlighet.
En av de kritiska fördelarna med gjuten underfyllning är dess förmåga att ge ett omfattande skydd för chipet. Formmassan som används i denna process fungerar som en robust barriär som omsluter hela chipet och förpackningen i ett skyddande skal. Detta ger en effektiv avskärmning mot miljöfaktorer som fukt, damm och föroreningar som kan påverka enhetens prestanda och tillförlitlighet. Inkapslingen hjälper också till att förhindra chipet från mekaniska påfrestningar, termisk cykling och andra yttre krafter, vilket säkerställer dess långvariga hållbarhet.
Dessutom möjliggör formgjuten underfyllning höga integrationsnivåer i halvledarpaketet. Underfyllningsmaterialet blandas direkt i formmassan, vilket möjliggör sömlös integrering av underfyllnings- och inkapslingsprocesserna. Denna integration eliminerar behovet av ett separat underfyllningssteg, vilket förenklar tillverkningsprocessen och minskar produktionstid och kostnader. Det säkerställer också konsekvent och enhetlig underfyllningsfördelning genom hela förpackningen, minimerar tomrum och förbättrar den övergripande strukturella integriteten.
Dessutom erbjuder gjuten underfyllning utmärkta värmeavledningsegenskaper. Formmassan är designad för att ha hög värmeledningsförmåga, vilket gör att den effektivt kan överföra värme från chipet. Detta är avgörande för att bibehålla enhetens optimala driftstemperatur och förhindra överhettning, vilket kan leda till prestandaförsämring och tillförlitlighetsproblem. De förbättrade värmeavledningsegenskaperna hos den gjutna underfyllningen bidrar till den elektroniska enhetens övergripande tillförlitlighet och livslängd.
Dessutom möjliggör gjuten underfyllning mer miniatyrisering och formfaktoroptimering. Inkapslingsprocessen kan skräddarsys för att rymma olika förpackningsstorlekar och former, inklusive komplexa 3D-strukturer. Denna flexibilitet gör det möjligt att integrera flera chips och andra komponenter i ett kompakt, utrymmeseffektivt paket. Möjligheten att uppnå högre nivåer av integration utan att kompromissa med tillförlitligheten gör formgjuten underfyllning särskilt värdefull i applikationer där storleks- och viktbegränsningar är kritiska, såsom mobila enheter, bärbara enheter och bilelektronik.
Chip Scale Package (CSP) Underfill: Miniatyrisering och hög densitet
Chip Scale Package (CSP) underfill är en kritisk teknik som möjliggör miniatyrisering och högdensitetsintegrering av elektroniska enheter. Eftersom elektroniska enheter fortsätter att minska i storlek samtidigt som de ger ökad funktionalitet, fyller CSP en avgörande roll för att säkerställa tillförlitligheten och prestandan hos dessa kompakta enheter.
CSP är en förpackningsteknik som gör att halvledarchipset kan monteras direkt på substratet eller kretskortet (PCB) utan att behöva ett extra paket. Detta eliminerar behovet av en traditionell plast- eller keramikbehållare, vilket minskar enhetens totala storlek och vikt. CSP underfyllning en process där en vätska eller inkapslande material används för att fylla gapet mellan chipet och substratet, vilket ger mekaniskt stöd och skyddar chipet från miljöfaktorer som fukt och mekanisk påfrestning.
Miniatyrisering uppnås genom CSP-underfyllning genom att minska avståndet mellan chipet och substratet. Underfyllningsmaterialet fyller det smala gapet mellan spånet och substratet, skapar en solid bindning och förbättrar spånets mekaniska stabilitet. Detta möjliggör mindre och tunnare enheter, vilket gör det möjligt att packa in mer funktionalitet i ett begränsat utrymme.
Högdensitetsintegration är en annan fördel med CSP-underfyllning. Genom att eliminera behovet av ett separat paket, möjliggör CSP att chippet kan monteras närmare andra komponenter på kretskortet, vilket minskar längden på elektriska anslutningar och förbättrar signalintegriteten. Underfyllningsmaterialet fungerar också som en värmeledare, som effektivt leder bort värme som genereras av chipet. Denna termiska hanteringskapacitet möjliggör högre effekttätheter, vilket möjliggör integration av mer komplexa och kraftfulla chips i elektroniska enheter.
CSP-underfyllningsmaterial måste ha specifika egenskaper för att möta kraven på miniatyrisering och högdensitetsintegration. De måste ha låg viskositet för att underlätta fyllningen av smala luckor, samt utmärkta flödesegenskaper för att säkerställa enhetlig täckning och eliminera tomrum. Materialen ska också ha god vidhäftning till spånet och underlaget, vilket ger ett fast mekaniskt stöd. Dessutom måste de uppvisa hög värmeledningsförmåga för att effektivt överföra värme från chippet.
CSP-underfyllning på wafer-nivå: kostnadseffektiv och hög avkastning
WLCSP-underfyllning på wafer-level chip scale package är en kostnadseffektiv och högutbytesförpackningsteknik som erbjuder flera fördelar när det gäller tillverkningseffektivitet och övergripande produktkvalitet. WLCSP-underfyllning applicerar underfyllningsmaterial på flera chips samtidigt medan de fortfarande är i waferform innan de förenas i individuella förpackningar. Detta tillvägagångssätt erbjuder många fördelar vad gäller kostnadsminskning, förbättrad processkontroll och högre produktionsutbyte.
En av de kritiska fördelarna med WLCSP-underfyllning är dess kostnadseffektivitet. Att applicera underfillmaterialet på wafernivå gör förpackningsprocessen mer strömlinjeformad och effektiv. Det underfyllda materialet dispenseras på wafern med en kontrollerad och automatiserad process, vilket minskar materialspill och minimerar arbetskostnaderna. Dessutom, eliminering av individuella förpackningshantering och anpassningssteg minskar den totala produktionstiden och komplexiteten, vilket resulterar i betydande kostnadsbesparingar jämfört med traditionella förpackningsmetoder.
Dessutom erbjuder WLCSP underfill förbättrad processkontroll och högre produktionsutbyte. Eftersom underfyllningsmaterialet appliceras på wafernivå, möjliggör det bättre kontroll över dispenseringsprocessen, vilket säkerställer konsekvent och enhetlig täckning för varje chip på wafern. Detta minskar risken för tomrum eller ofullständig underfyllning, vilket kan leda till tillförlitlighetsproblem. Möjligheten att inspektera och testa underfyllningskvaliteten på wafernivå möjliggör också tidig upptäckt av defekter eller processvariationer, vilket möjliggör snabba korrigerande åtgärder och minskar sannolikheten för felaktiga förpackningar. Som ett resultat bidrar WLCSP underfill till att uppnå högre produktionsutbyte och bättre övergripande produktkvalitet.
Metoden på wafer-nivå möjliggör också förbättrad termisk och mekanisk prestanda. Underfyllningsmaterialet som används i WLCSP är vanligtvis ett lågvisköst, kapillärflytande material som effektivt kan fylla de smala luckorna mellan chipsen och skivan. Detta ger ett stabilt mekaniskt stöd till chipsen, vilket förbättrar deras motståndskraft mot mekanisk påfrestning, vibrationer och temperaturcykler. Dessutom fungerar underfyllningsmaterialet som en värmeledare, vilket underlättar bortledningen av värme som genereras av chipsen, vilket förbättrar värmehanteringen och minskar risken för överhettning.
Flip Chip Underfill: Hög I/O-densitet och prestanda
Flip chip underfill är en kritisk teknik som möjliggör hög input/output (I/O) densitet och exceptionell prestanda i elektroniska enheter. Det spelar en avgörande roll för att förbättra tillförlitligheten och funktionaliteten hos flip-chip-förpackningar, som används i stor utsträckning i avancerade halvledarapplikationer. Den här artikeln kommer att utforska betydelsen av flip chip underfill och dess inverkan på att uppnå hög I/O-densitet och prestanda.
Flip chip-teknik involverar direkt elektrisk anslutning av en integrerad krets (IC) eller en halvledarmatris till substratet, vilket eliminerar behovet av trådbindning. Detta resulterar i ett mer kompakt och effektivt paket, eftersom I/O-kuddarna är placerade på bottenytan av formen. Flip-chip-förpackningar innebär dock unika utmaningar som måste lösas för att säkerställa optimal prestanda och tillförlitlighet.
En av de kritiska utmaningarna i flip chip-förpackningar är att förhindra mekanisk påkänning och termisk obalans mellan formen och substratet. Under tillverkningsprocessen och efterföljande drift kan skillnaderna i termisk expansionskoefficient (CTE) mellan formen och substratet orsaka betydande spänningar, vilket leder till prestandaförsämring eller till och med fel. Flip chip underfill är ett skyddande material som kapslar in chipet, vilket ger mekaniskt stöd och avspänning. Det fördelar effektivt spänningarna som genereras under termisk cykling och förhindrar dem från att påverka de ömtåliga sammankopplingarna.
Hög I/O-densitet är avgörande i moderna elektroniska enheter, där mindre formfaktorer och ökad funktionalitet är avgörande. Flip chip underfill möjliggör högre I/O-densiteter genom att erbjuda överlägsen elektrisk isolering och termisk hanteringskapacitet. Underfyllningsmaterialet fyller gapet mellan formen och substratet, skapar ett robust gränssnitt och minskar risken för kortslutning eller elektriskt läckage. Detta möjliggör närmare avstånd mellan I/O-kuddarna, vilket resulterar i ökad I/O-densitet utan att offra tillförlitligheten.
Dessutom bidrar flip chip underfill till förbättrad elektrisk prestanda. Det minimerar de elektriska parasiter mellan formen och substratet, minskar signalfördröjningen och förbättrar signalintegriteten. Underfyllningsmaterialet uppvisar också utmärkta värmeledningsegenskaper, vilket effektivt leder bort värme som genereras av chipet under drift. Effektiv värmeavledning säkerställer att temperaturen håller sig inom acceptabla gränser, förhindrar överhettning och bibehåller optimal prestanda.
Framsteg inom flip chip underfyllningsmaterial har möjliggjort ännu högre I/O-densiteter och prestandanivåer. Nanokompositunderfyllningar, till exempel, utnyttjar fyllmedel i nanoskala för att förbättra värmeledningsförmågan och mekanisk styrka. Detta möjliggör förbättrad värmeavledning och tillförlitlighet, vilket möjliggör enheter med högre prestanda.
Ball Grid Array (BGA) Underfill: Hög termisk och mekanisk prestanda
Ball Grid Array (BGA) underfyller en kritisk teknologi som erbjuder hög termisk och mekanisk prestanda i elektroniska enheter. Det spelar en avgörande roll för att förbättra tillförlitligheten och funktionaliteten hos BGA-paket, som används flitigt i olika applikationer. I den här artikeln kommer vi att utforska betydelsen av BGA-underfyllning och dess inverkan på att uppnå hög termisk och mekanisk prestanda.
BGA-teknologin involverar en paketdesign där den integrerade kretsen (IC) eller halvledarmatrisen är monterad på ett substrat och de elektriska anslutningarna görs genom en rad lödkulor placerade på paketets bottenyta. BGA underfyller ett material som dispenseras i springan mellan formen och substratet, kapslar in lödkulorna och ger mekaniskt stöd och skydd till enheten.
En av de kritiska utmaningarna i BGA-förpackningar är hanteringen av termiska spänningar. Under drift genererar IC värme, och termisk expansion och sammandragning kan orsaka betydande tryck på lödfogarna som förbinder formen och substratet. BGA underfyller en avgörande roll för att mildra dessa påfrestningar genom att bilda en fast bindning med formen och substratet. Den fungerar som en spänningsbuffert, absorberar den termiska expansionen och kontraktionen och minskar belastningen på lödfogarna. Detta hjälper till att förbättra paketets övergripande tillförlitlighet och minskar risken för lödfogsfel.
En annan kritisk aspekt av BGA-underfyllning är dess förmåga att förbättra paketets mekaniska prestanda. BGA-paket utsätts ofta för mekaniska påfrestningar under hantering, montering och drift. Underfyllningsmaterialet fyller gapet mellan formen och substratet, vilket ger strukturellt stöd och förstärkning till lödfogarna. Detta förbättrar enhetens totala mekaniska styrka, vilket gör den mer motståndskraftig mot mekaniska stötar, vibrationer och andra yttre krafter. Genom att effektivt fördela de mekaniska påfrestningarna hjälper BGA-underfyllningen till att förhindra sprickbildning, delaminering eller andra mekaniska fel.
Hög termisk prestanda är avgörande i elektroniska enheter för att säkerställa korrekt funktionalitet och tillförlitlighet. BGA underfyllningsmaterial är designade för att ha utmärkta värmeledningsförmåga. Detta gör det möjligt för dem att effektivt överföra värme från formen och fördela den över substratet, vilket förbättrar den övergripande termiska hanteringen av förpackningen. Effektiv värmeavledning hjälper till att upprätthålla lägre driftstemperaturer, förhindrar termiska hotspots och potentiell prestandaförsämring. Det bidrar också till lådans livslängd genom att minska komponenternas termiska spänningar.
Framsteg inom BGA-underfyllningsmaterial har lett till ännu högre termisk och mekanisk prestanda. Förbättrade formuleringar och fyllmedel, såsom nanokompositer eller fyllmedel med hög värmeledningsförmåga, har möjliggjort bättre värmeavledning och mekanisk styrka, vilket ytterligare förbättrar prestandan hos BGA-paket.
Quad Flat Package (QFP) Underfill: Stort I/O-antal och robusthet
Quad Flat Package (QFP) är ett integrerat kretspaket (IC) som används ofta inom elektronik. Den har en kvadratisk eller rektangulär form med ledningar som sträcker sig från alla fyra sidorna, vilket ger många in-/utgångsanslutningar (I/O). För att öka tillförlitligheten och robustheten hos QFP-förpackningar används vanligtvis underfyllningsmaterial.
Underfill är ett skyddande material som appliceras mellan IC och substratet för att förstärka den mekaniska styrkan hos lödfogarna och förhindra stressinducerade fel. Det är särskilt viktigt för QFP:er med ett stort I/O-antal, eftersom det höga antalet anslutningar kan leda till betydande mekaniska påfrestningar under termisk cykling och driftsförhållanden.
Underfyllningsmaterialet som används för QFP-förpackningar måste ha specifika egenskaper för att säkerställa robusthet. För det första bör den ha utmärkt vidhäftning till både IC och substratet för att skapa en stark bindning och minimera risken för delaminering eller lossning. Dessutom bör den ha en låg termisk expansionskoefficient (CTE) för att matcha CTE för IC och substrat, vilket minskar spänningsfelmatchningar som kan leda till sprickor eller brott.
Vidare bör underfyllningsmaterialet ha goda flytegenskaper för att säkerställa enhetlig täckning och fullständig fyllning av gapet mellan IC och substratet. Detta hjälper till att eliminera tomrum, vilket kan försvaga lödfogarna och resultera i minskad tillförlitlighet. Materialet ska även ha goda härdningsegenskaper, vilket gör att det kan bilda ett styvt och hållbart skyddsskikt efter applicering.
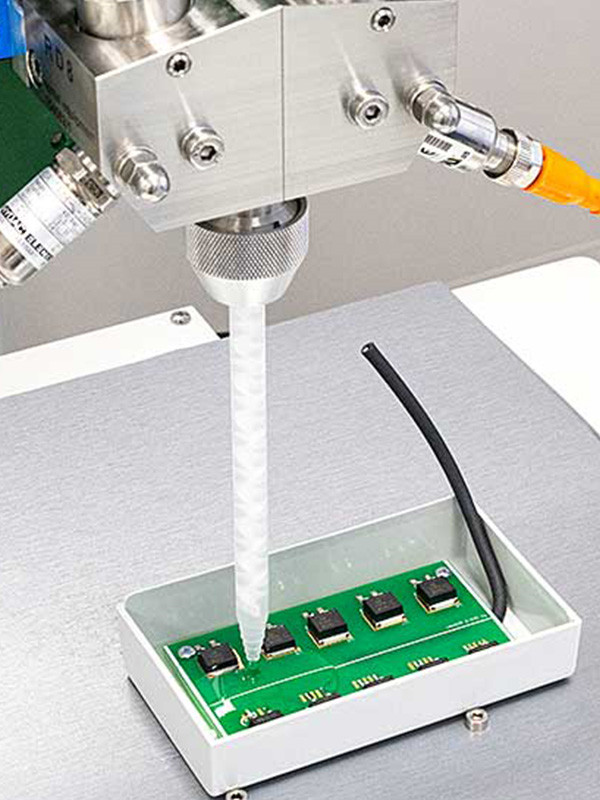
När det gäller mekanisk robusthet bör underfyllningen ha hög skjuv- och fläkhållfasthet för att motstå yttre krafter och förhindra förpackningsdeformation eller separation. Den bör också uppvisa god motståndskraft mot fukt och andra miljöfaktorer för att behålla sina skyddande egenskaper över tid. Detta är särskilt viktigt i applikationer där QFP-paketet kan utsättas för svåra förhållanden eller genomgå temperaturvariationer.
Olika underfyllningsmaterial finns tillgängliga för att uppnå dessa önskade egenskaper, inklusive epoxibaserade formuleringar. Beroende på applikationens specifika krav kan dessa material dispenseras med olika tekniker, såsom kapillärflöde, jetting eller screentryck.
System-i-Package (SiP) Underfill: Integration och prestanda
System-in-Package (SiP) är en avancerad förpackningsteknik som integrerar flera halvledarchips, passiva komponenter och andra element i ett enda paket. SiP erbjuder många fördelar, inklusive reducerad formfaktor, förbättrad elektrisk prestanda och förbättrad funktionalitet. För att säkerställa tillförlitligheten och prestandan hos SiP-enheter används ofta underfyllningsmaterial.
Underfill i SiP-applikationer är avgörande för att ge mekanisk stabilitet och elektrisk anslutning mellan de olika komponenterna i paketet. Det hjälper till att minimera risken för spänningsinducerade fel, såsom lödfogsprickor eller frakturer, som kan uppstå på grund av skillnader i termisk expansionskoefficient (CTE) mellan komponenterna.
Att integrera flera komponenter i ett SiP-paket leder till komplex sammankoppling, med många lödfogar och högdensitetskretsar. Underfyllningsmaterial hjälper till att förstärka dessa sammankopplingar, vilket förbättrar monteringens mekaniska styrka och tillförlitlighet. De stödjer lödfogarna, vilket minskar risken för utmattning eller skador orsakade av termisk cykling eller mekanisk stress.
När det gäller elektrisk prestanda är underfyllnadsmaterial avgörande för att förbättra signalintegriteten och minimera elektriskt brus. Genom att fylla mellanrummen mellan komponenter och minska avståndet mellan dem hjälper underfyllning till att minska parasitisk kapacitans och induktans, vilket möjliggör snabbare och effektivare signalöverföring.
Dessutom bör underfyllningsmaterial för SiP-applikationer ha utmärkt värmeledningsförmåga för att effektivt avleda värme som genereras av de integrerade komponenterna. Effektiv värmeavledning är avgörande för att förhindra överhettning och bibehålla SiP-enhetens övergripande tillförlitlighet och prestanda.
Underfyllningsmaterial i SiP-förpackningar måste ha specifika egenskaper för att uppfylla dessa integrations- och prestandakrav. De bör ha god flytbarhet för att säkerställa fullständig täckning och fylla mellanrum mellan komponenterna. Underfyllningsmaterialet bör också ha en lågviskös sammansättning för att möjliggöra enkel dispensering och fyllning i smala hål eller små utrymmen.
Dessutom bör underfyllningsmaterialet uppvisa stark vidhäftning till olika ytor, inklusive halvledarchips, substrat och passiva material, för att säkerställa tillförlitlig bindning. Den ska vara kompatibel med olika förpackningsmaterial, såsom organiska substrat eller keramik, och uppvisa goda mekaniska egenskaper, inklusive hög skjuv- och fläkhållfasthet.
Valet av underfyllningsmaterial och appliceringsmetod beror på den specifika SiP-designen, komponentkraven och tillverkningsprocesserna. Dispenseringstekniker såsom kapillärflöde, jetting eller filmassisterade metoder tillämpar vanligtvis underfyllning i SiP-enheter.
Optoelektronik Underfill: Optisk inriktning och skydd
Optoelektronisk underfyllning inkluderar inkapsling och skydd av optoelektroniska enheter samtidigt som den säkerställer exakt optisk inriktning. Optoelektroniska enheter, såsom lasrar, fotodetektorer och optiska omkopplare, kräver ofta känslig inriktning av optiska komponenter för att uppnå optimal prestanda. Samtidigt måste de skyddas från miljöfaktorer som kan påverka deras funktionalitet. Optoelektronik underfyllning möter båda dessa krav genom att tillhandahålla optisk inriktning och skydd i en enda process.
Optisk inriktning är en kritisk aspekt av tillverkning av optoelektroniska enheter. Det handlar om att anpassa visuella element, såsom fibrer, vågledare, linser eller galler, för att säkerställa effektiv ljusöverföring och mottagning. Exakt justering är nödvändig för att maximera enhetens prestanda och bibehålla signalintegriteten. Traditionella uppriktningstekniker inkluderar manuell uppriktning med visuell inspektion eller automatiserad uppriktning med hjälp av uppriktningssteg. Dessa metoder kan dock vara tidskrävande, arbetsintensiva och benägna att göra fel.
Optoelektronik underfyller en innovativ lösning genom att införliva uppriktningsfunktioner direkt i underfyllningsmaterialet. Underfyllningsmaterial är vanligtvis flytande eller halvflytande föreningar som kan flyta och fylla mellanrummen mellan optiska komponenter. Genom att lägga till inriktningsfunktioner, såsom mikrostrukturer eller referensmärken, i underfyllningsmaterialet, kan inriktningsprocessen förenklas och automatiseras. Dessa funktioner fungerar som guider under monteringen, vilket säkerställer exakt inriktning av de optiska komponenterna utan behov av komplexa inriktningsprocedurer.
Förutom optisk inriktning skyddar underfyllningsmaterial optoelektroniska enheter. Optoelektroniska komponenter utsätts ofta för tuffa miljöer, inklusive temperaturfluktuationer, fukt och mekanisk påfrestning. Dessa externa faktorer kan försämra enheternas prestanda och tillförlitlighet över tid. Underfyllningsmaterial fungerar som en skyddande barriär, kapslar in de optiska komponenterna och skyddar dem från miljöföroreningar. De ger också mekanisk förstärkning, vilket minskar risken för skador på grund av stötar eller vibrationer.
Underfyllningsmaterial som används i optoelektroniktillämpningar är typiskt utformade för att ha lågt brytningsindex och utmärkt optisk transparens. Detta säkerställer minimal störning av de optiska signalerna som passerar genom enheten. Dessutom uppvisar de god vidhäftning till olika substrat och har låga värmeutvidgningskoefficienter för att minimera enhetens påfrestning under termisk cykling.
Underfyllningsprocessen involverar dispensering av underfyllningsmaterialet på anordningen, låter det flyta och fyller luckorna mellan optiska komponenter, och sedan härdar det för att bilda en solid inkapsling. Beroende på den specifika applikationen kan underfyllningsmaterialet appliceras med olika tekniker, såsom kapillärflöde, jetdispensering eller screentryck. Härdningsprocessen kan uppnås genom värme, UV-strålning eller båda.
Medical Electronics Underfill: Biokompatibilitet och tillförlitlighet
Medicinsk elektronik underfyller en specialiserad process som involverar inkapsling och skydd av elektroniska komponenter som används i medicinsk utrustning. Dessa enheter spelar en avgörande roll i olika medicinska tillämpningar, såsom implanterbara enheter, diagnostisk utrustning, övervakningssystem och system för läkemedelstillförsel. Medicinsk elektronik underfyllning fokuserar på två kritiska aspekter: biokompatibilitet och tillförlitlighet.
Biokompatibilitet är ett grundläggande krav för medicintekniska produkter som kommer i kontakt med människokroppen. Underfyllningsmaterialen som används i medicinsk elektronik måste vara biokompatibla, vilket innebär att de inte ska orsaka skadliga effekter eller biverkningar när de kommer i kontakt med levande vävnader eller kroppsvätskor. Dessa material bör följa strikta regler och standarder, såsom ISO 10993, som specificerar biokompatibilitetstestning och utvärderingsprocedurer.
Underfyllningsmaterial för medicinsk elektronik är noggrant utvalda eller formulerade för att säkerställa biokompatibilitet. De är designade för att vara giftfria, icke-irriterande och icke-allergiframkallande. Dessa material bör inte läcka ut några skadliga ämnen eller brytas ned med tiden, eftersom detta kan leda till vävnadsskador eller inflammation. Biokompatibla underfyllningsmaterial har också låg vattenabsorption för att förhindra tillväxt av bakterier eller svampar som kan orsaka infektioner.
Tillförlitlighet är en annan kritisk aspekt av medicinsk elektronik underfyllning. Medicinsk utrustning möter ofta utmanande driftsförhållanden, inklusive extrema temperaturer, fukt, kroppsvätskor och mekanisk stress. Underfyllningsmaterial måste skydda de elektroniska komponenterna och säkerställa deras långsiktiga tillförlitlighet och funktionalitet. Tillförlitlighet är av största vikt i medicinska tillämpningar där enhetsfel kan allvarligt påverka patientsäkerhet och välbefinnande.
Underfyllningsmaterial för medicinsk elektronik bör ha hög motståndskraft mot fukt och kemikalier för att motstå exponering för kroppsvätskor eller steriliseringsprocesser. De bör också uppvisa god vidhäftning till olika underlag, vilket säkerställer säker inkapsling av de elektroniska komponenterna. Mekaniska egenskaper, såsom låga värmeutvidgningskoefficienter och bra stöttålighet, är avgörande för att minimera belastningen på detaljerna under termisk cykling eller automatisk belastning.
Underfyllningsprocessen för medicinsk elektronik innefattar:
- Dispensera underfyllningsmaterialet på de elektroniska komponenterna.
- Fyller luckorna.
- Härdar den för att bilda en skyddande och mekaniskt stabil inkapsling.
Försiktighet måste iakttas för att säkerställa fullständig täckning av funktionerna och frånvaron av tomrum eller luftfickor som kan äventyra enhetens tillförlitlighet.
Vidare tas ytterligare hänsyn vid underfyllning av medicintekniska produkter. Till exempel bör underfyllningsmaterialet vara kompatibelt med de steriliseringsmetoder som används för enheten. Vissa material kan vara känsliga för specifika steriliseringstekniker, såsom ånga, etylenoxid eller strålning, och alternativa material kan behöva väljas.
Aerospace Electronics Underfill: Hög temperatur och vibrationsmotstånd
Flygelektronik underfyller en specialiserad process för att kapsla in och skydda elektroniska komponenter i flygtillämpningar. Flygmiljöer utgör unika utmaningar, inklusive höga temperaturer, extrema vibrationer och mekaniska påfrestningar. Därför fokuserar underfyllningen för flygelektronik på två avgörande aspekter: motstånd mot hög temperatur och motstånd mot vibrationer.
Högtemperaturmotstånd är av största vikt inom flygelektronik på grund av de förhöjda temperaturer som upplevs under drift. Underfyllningsmaterialen som används i flygtillämpningar måste tåla dessa höga temperaturer utan att kompromissa med de elektroniska komponenternas prestanda och tillförlitlighet. De bör uppvisa minimal termisk expansion och förbli stabila över ett brett temperaturområde.
Underfyllningsmaterial för flygelektronik väljs eller formuleras för höga glastemperaturer (Tg) och termisk stabilitet. En hög Tg säkerställer att materialet behåller sina mekaniska egenskaper vid förhöjda temperaturer, vilket förhindrar deformation eller förlust av vidhäftning. Dessa material kan motstå extrema temperaturer, såsom under start, återinträde i atmosfären eller drift i varma motorrum.
Dessutom bör underfyllnadsmaterial för flygelektronik ha låga termiska expansionskoefficienter (CTE). CTE mäter hur mycket ett material expanderar eller drar ihop sig med temperaturförändringar. Genom att ha en låg CTE kan underfyllnadsmaterial minimera belastningen på de elektroniska komponenterna som orsakas av termisk cykling, vilket kan leda till mekaniska fel eller utmattning av lödfogar.
Vibrationsmotstånd är ett annat kritiskt krav för underfyllning av flygelektronik. Flygfordon utsätts för olika vibrationer, inklusive motor, flyginducerade vibrationer och mekaniska stötar under uppskjutning eller landning. Dessa vibrationer kan äventyra de elektroniska komponenternas prestanda och tillförlitlighet om de inte är tillräckligt skyddade.
Underfyllningsmaterial som används inom flygelektronik bör uppvisa utmärkta vibrationsdämpande egenskaper. De ska absorbera och avleda den energi som genereras av vibrationer, vilket minskar belastningen och belastningen på de elektroniska komponenterna. Detta hjälper till att förhindra bildning av sprickor, sprickor eller andra mekaniska fel på grund av överdriven vibrationsexponering.
Dessutom föredras underfyllningsmaterial med hög vidhäftning och kohesiv styrka i flygtillämpningar. Dessa egenskaper säkerställer att underfyllningsmaterialet förblir stadigt bundet till de elektroniska komponenterna och substratet, även under extrema vibrationsförhållanden. Stark vidhäftning förhindrar att underfyllningsmaterialet delamineras eller separeras från elementen, bibehåller inkapslingens integritet och skyddar mot fukt eller skräp.
Underfyllningsprocessen för flygelektronik involverar vanligtvis att dispensera underfyllningsmaterialet på de elektroniska komponenterna, låta det flyta och fylla luckorna, och sedan härda det för att bilda en robust inkapsling. Härdningsprocessen kan utföras med termiska eller UV-härdningsmetoder, beroende på applikationens specifika krav.
Underfyllning för fordonselektronik: Hållbarhet och termiskt cyklingsmotstånd
Bilelektronik underfyller en kritisk process som involverar inkapsling och skydd av elektroniska komponenter i fordonstillämpningar. Bilmiljöer erbjuder unika utmaningar, inklusive temperaturvariationer, termisk cykling, mekaniska påfrestningar och exponering för fukt och kemikalier. Därför fokuserar bilelektronikunderfyllningen på två kritiska aspekter: hållbarhet och termisk cyklingsmotstånd.
Hållbarhet är ett avgörande krav för underfyllning för bilelektronik. Under normal drift upplever bilar konstanta vibrationer, stötar och mekaniska påfrestningar. Underfyllningsmaterialen som används i biltillämpningar måste skydda elektroniska komponenter robust, vilket säkerställer deras hållbarhet och livslängd. De ska motstå de hårda förhållanden och mekaniska belastningar som uppstår på vägen och motstå inträngning av fukt, damm och kemikalier.
Underfyllningsmaterial för fordonselektronik väljs eller formuleras för hög mekanisk hållfasthet och slagtålighet. De bör uppvisa utmärkt vidhäftning till de elektroniska komponenterna och substratet, vilket förhindrar delaminering eller separation under mekaniska påfrestningar. Hållbara underfyllningsmaterial hjälper till att minimera risken för skador på de elektroniska komponenterna på grund av vibrationer eller stötar, vilket säkerställer pålitlig prestanda under fordonets livstid.
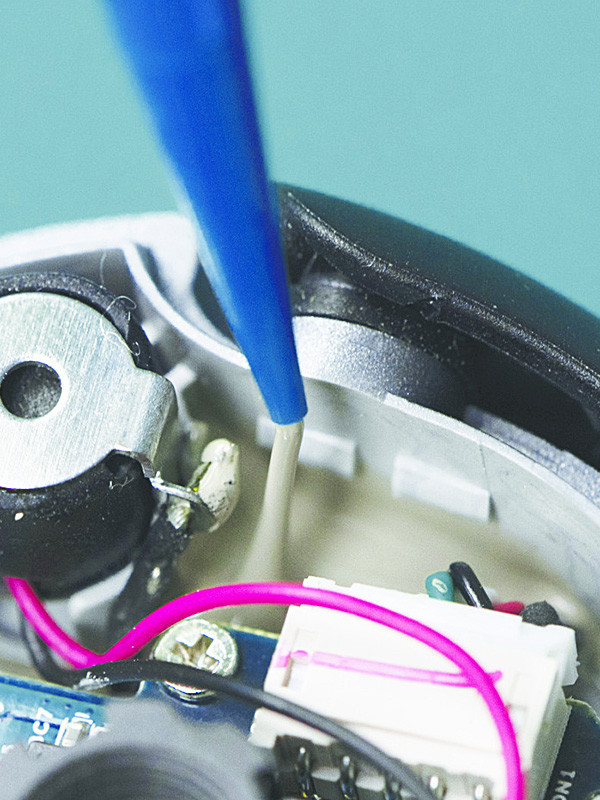
Termiskt cyklingsmotstånd är ett annat kritiskt krav för underfyllning av bilelektronik. Fordon genomgår frekventa temperaturvariationer, särskilt under motorstart och drift, och dessa temperaturcykler kan inducera termiska påfrestningar på elektroniska komponenter och det omgivande underfyllningsmaterialet. Underfyllnadsmaterialen som används i biltillämpningar måste ha utmärkt termisk cyklisk motstånd för att motstå dessa temperaturfluktuationer utan att kompromissa med deras prestanda.
Underfyllnadsmaterial för bilelektronik bör ha låga termiska expansionskoefficienter (CTE) för att minimera de elektroniska komponenternas stress under termisk cykling. En väl anpassad CTE mellan underfyllningsmaterialet och ingredienserna minskar risken för utmattning av lödfog, sprickor eller andra mekaniska fel orsakade av termisk stress. Dessutom bör underfyllnadsmaterialen uppvisa god värmeledningsförmåga för att effektivt avleda värme, vilket förhindrar lokala hotspots som kan påverka komponenternas prestanda och tillförlitlighet.
Dessutom bör underfyllnadsmaterial för fordonselektronik motstå fukt, kemikalier och vätskor. De bör ha låg vattenabsorption för att förhindra mögeltillväxt eller korrosion av de elektroniska komponenterna. Kemisk beständighet säkerställer att underfyllningsmaterialet förblir stabilt när det utsätts för fordonsvätskor, såsom oljor, bränslen eller rengöringsmedel, vilket undviker nedbrytning eller förlust av vidhäftning.
Underfyllningsprocessen för bilelektronik involverar vanligtvis att dispensera underfyllningsmaterialet på de elektroniska komponenterna, låta det flyta och fylla mellanrummen och sedan härda det för att bilda en hållbar inkapsling. Härdningsprocessen kan åstadkommas genom termiska eller UV-härdningsmetoder, beroende på applikationens specifika krav och det underfyllningsmaterial som används.
Att välja rätt underfyllningsepoxi
Att välja rätt underfyllningsepoxi är ett avgörande beslut vid montering och skydd av elektroniska komponenter. Underfill-epoxi ger mekanisk förstärkning, termisk hantering och skydd mot miljöfaktorer. Här är några viktiga överväganden när du väljer lämplig underfyllningsepoxi:
- Termiska egenskaper: En av de primära funktionerna hos underfill-epoxi är att avleda värme som genereras av elektroniska komponenter. Därför är det viktigt att ta hänsyn till epoxins värmeledningsförmåga och värmebeständighet. Hög värmeledningsförmåga bidrar till effektiv värmeöverföring, förhindrar hotspots och bibehåller komponenternas tillförlitlighet. Epoxin bör också ha låg termisk resistans för att minimera termisk belastning på komponenterna under temperaturcykler.
- CTE Match: Underfill-epoxins värmeutvidgningskoefficient (CTE) bör vara väl matchad med CTE för de elektroniska komponenterna och substratet för att minimera termisk stress och förhindra lödfogsfel. En nära matchad CTE hjälper till att minska risken för mekaniska fel på grund av termisk cykling.
- Flödes- och luckfyllningsförmåga: Den underfyllda epoxin bör ha goda flödesegenskaper och förmågan att fylla luckor mellan komponenterna effektivt. Detta säkerställer fullständig täckning och minimerar tomrum eller luftfickor som kan påverka enhetens mekaniska stabilitet och termiska prestanda. Epoxins viskositet bör vara lämplig för den specifika applikationen och monteringsmetoden, oavsett om det är kapillärflöde, jetdispensering eller screentryck.
- Vidhäftning: Stark vidhäftning är avgörande för underfyllning av epoxi för att säkerställa tillförlitlig vidhäftning mellan komponenterna och underlaget. Det bör uppvisa god vidhäftning till olika material, inklusive metaller, keramik och plast. Epoxins vidhäftningsegenskaper bidrar till monteringens mekaniska integritet och långsiktiga tillförlitlighet.
- Härdningsmetod: Överväg den härdningsmetod som bäst passar din tillverkningsprocess. Underfill-epoxi kan härdas genom värme, UV-strålning eller en kombination av båda. Varje härdningsmetod har fördelar och begränsningar, och det är viktigt att välja den som passar dina produktionskrav.
- Miljöbeständighet: Utvärdera underfyllningsepoxins motståndskraft mot miljöfaktorer som fukt, kemikalier och extrema temperaturer. Epoxin ska kunna motstå exponering för vatten, vilket förhindrar tillväxt av mögel eller korrosion. Kemisk beständighet säkerställer stabilitet vid kontakt med bilvätskor, rengöringsmedel eller andra potentiellt frätande ämnen. Dessutom bör epoxin bibehålla sina mekaniska och elektriska egenskaper över ett brett temperaturområde.
- Tillförlitlighet och livslängd: Tänk på underfyllningsepoxins meritlista och tillförlitlighetsdata. Leta efter epoximaterial som är testade och visat sig fungera bra i liknande applikationer eller har industricertifieringar och överensstämmelse med relevanta standarder. Tänk på faktorer som åldrande beteende, långsiktig tillförlitlighet och epoxins förmåga att behålla sina egenskaper över tid.
När du väljer rätt underfyllningsepoxi är det avgörande att ta hänsyn till de specifika kraven för din applikation, inklusive värmehantering, mekanisk stabilitet, miljöskydd och kompatibilitet med tillverkningsprocessen. Att konsultera med epoxileverantörer eller söka expertråd kan vara fördelaktigt för att fatta ett välgrundat beslut som möter din applikations behov och säkerställer optimal prestanda och tillförlitlighet.
Framtida trender inom underfyllningsepoxi
Underfill-epoxi utvecklas kontinuerligt, drivet av framsteg inom elektronisk teknik, nya applikationer och behovet av förbättrad prestanda och tillförlitlighet. Flera framtida trender kan observeras i utvecklingen och appliceringen av underfyllningsepoxi:
- Miniatyrisering och förpackning med högre densitet: Eftersom elektroniska enheter fortsätter att krympa och har högre komponentdensiteter måste underfyllningsepoxier anpassas därefter. Framtida trender kommer att fokusera på att utveckla underfyllningsmaterial som penetrerar och fyller mindre luckor mellan komponenter, vilket säkerställer fullständig täckning och tillförlitligt skydd i allt mer miniatyriserade elektroniska sammansättningar.
- Högfrekventa applikationer: Med den växande efterfrågan på högfrekventa och höghastighets elektroniska enheter, kommer underfyllningsepoxiformuleringar att behöva möta de specifika kraven för dessa applikationer. Underfyllningsmaterial med låg dielektricitetskonstant och tangenter med låg förlust kommer att vara avgörande för att minimera signalförluster och bibehålla integriteten hos högfrekventa signaler i avancerade kommunikationssystem, 5G-teknik och andra framväxande applikationer.
- Förbättrad termisk hantering: Värmeavledning är fortfarande ett kritiskt problem för elektroniska enheter, särskilt med de ökande effekttätheterna. Framtida underfyllningsepoxiformuleringar kommer att fokusera på förbättrad värmeledningsförmåga för att förbättra värmeöverföringen och hantera värmeproblem effektivt. Avancerade fyllmedel och tillsatser kommer att införlivas i underfill-epoxier för att uppnå högre värmeledningsförmåga samtidigt som andra önskade egenskaper bibehålls.
- Flexibel och töjbar elektronik: Framväxten av flexibel och töjbar elektronik öppnar för nya möjligheter för underfyllning av epoximaterial. Flexibla underfyllningsepoxier måste visa utmärkt vidhäftning och mekaniska egenskaper även vid upprepad böjning eller sträckning. Dessa material kommer att möjliggöra inkapsling och skydd av elektronik i bärbara enheter, böjbara displayer och andra applikationer som kräver mekanisk flexibilitet.
- Miljövänliga lösningar: Hållbarhet och miljöhänsyn kommer att spela en allt viktigare roll i utvecklingen av underfyllningsepoximaterial. Det kommer att läggas fokus på att skapa epoxiformuleringar fria från farliga ämnen och har minskad miljöpåverkan under hela livscykeln, inklusive tillverkning, användning och kassering. Biobaserade eller förnybara material kan också få framträdande plats som hållbara alternativ.
- Förbättrade tillverkningsprocesser: Framtida trender inom underfill-epoxi kommer att fokusera på materialegenskaper och framsteg i tillverkningsprocesser. Tekniker som additiv tillverkning, selektiv dispensering och avancerade härdningsmetoder kommer att utforskas för att optimera appliceringen och prestandan av underfill-epoxi i olika elektroniska monteringsprocesser.
- Integration av avancerade test- och karakteriseringstekniker: Med den ökande komplexiteten och kraven på elektroniska enheter kommer det att finnas ett behov av avancerade test- och karakteriseringsmetoder för att säkerställa tillförlitligheten och prestandan hos underfylld epoxi. Tekniker som oförstörande testning, in-situ övervakning och simuleringsverktyg kommer att hjälpa till vid utveckling och kvalitetskontroll av underfyllda epoximaterial.
Slutsats
Underfyllningsepoxi spelar en avgörande roll för att förbättra tillförlitligheten och prestandan hos elektroniska komponenter, särskilt i halvledarförpackningar. De olika typerna av underfyllningsepoxi erbjuder en rad fördelar, inklusive hög tillförlitlighet, självdispensering, hög densitet och hög termisk och mekanisk prestanda. Att välja rätt underfyllningsepoxi för applikationen och förpackningen säkerställer en robust och långvarig bindning. När teknologin går framåt och förpackningsstorlekarna krymper förväntar vi oss ännu mer innovativa underfill-epoxilösningar som erbjuder överlägsen prestanda, integration och miniatyrisering. Underfill-epoxi kommer att spela en allt viktigare roll i framtiden för elektronik, vilket gör det möjligt för oss att uppnå högre nivåer av tillförlitlighet och prestanda inom olika industrier.