Ondervul Epoxy
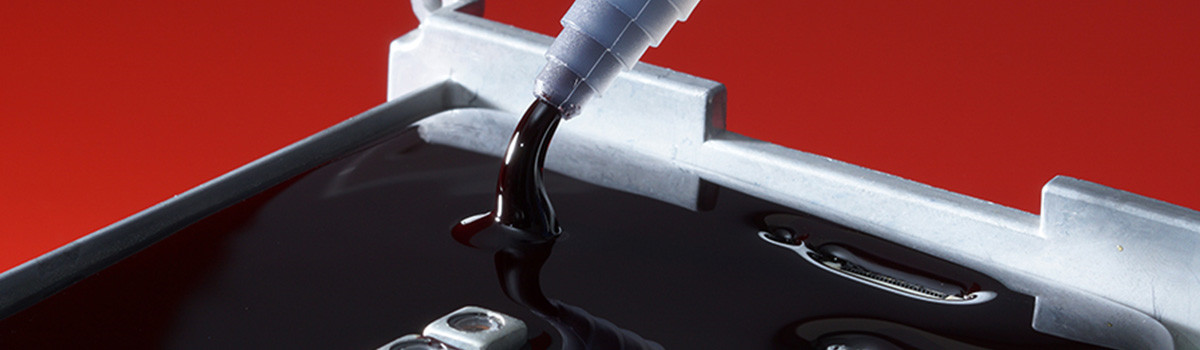
Underfill epoxy is een type lijm dat wordt gebruikt om de betrouwbaarheid van elektronische componenten te verbeteren, met name in halfgeleiderverpakkingen. Het vult de opening tussen de verpakking en de printplaat (PCB), biedt mechanische ondersteuning en spanningsverlichting om schade door thermische uitzetting en samentrekking te voorkomen. Underfill epoxy verbetert ook de elektrische prestaties van het pakket door de parasitaire inductantie en capaciteit te verminderen. In dit artikel onderzoeken we de verschillende toepassingen van underfill-epoxy, de verschillende beschikbare typen en hun voordelen.
Het belang van underfill-epoxy in halfgeleiderverpakkingen
Underfill epoxy is cruciaal in halfgeleiderverpakkingen en biedt mechanische versterking en bescherming aan delicate micro-elektronische componenten. Het is een gespecialiseerd kleefmateriaal dat wordt gebruikt om de opening tussen de halfgeleiderchip en het pakketsubstraat te vullen, waardoor de betrouwbaarheid en prestaties van elektronische apparaten worden verbeterd. Hier zullen we het belang van ondergevulde epoxy in halfgeleiderverpakkingen onderzoeken.
Een van de belangrijkste functies van ondergevulde epoxy is het verbeteren van de mechanische sterkte en betrouwbaarheid van het pakket. Tijdens bedrijf worden halfgeleiderchips onderworpen aan verschillende mechanische spanningen, zoals thermische uitzetting en samentrekking, trillingen en mechanische schokken. Deze spanningen kunnen leiden tot de vorming van scheuren in de soldeerverbinding, die elektrische storingen kunnen veroorzaken en de algehele levensduur van het apparaat kunnen verkorten. Underfill epoxy werkt als een spanningsverlagend middel door de mechanische spanning gelijkmatig over de chip, het substraat en de soldeerverbindingen te verdelen. Het minimaliseert effectief de vorming van scheuren en voorkomt de verspreiding van bestaande scheuren, waardoor de betrouwbaarheid van het pakket op lange termijn wordt gegarandeerd.
Een ander cruciaal aspect van underfill-epoxy is het vermogen om de thermische prestaties van halfgeleiderapparaten te verbeteren. Warmtedissipatie wordt een groot probleem naarmate elektronische apparaten kleiner worden en de vermogensdichtheid toenemen, en overmatige hitte kan de prestaties en betrouwbaarheid van de halfgeleiderchip verminderen. Underfill epoxy heeft uitstekende thermische geleidbaarheidseigenschappen, waardoor het op efficiënte wijze warmte van de chip kan overbrengen en door het pakket kan verdelen. Dit helpt om optimale bedrijfstemperaturen te behouden en hotspots te voorkomen, waardoor het algehele thermische beheer van het apparaat wordt verbeterd.
Underfill epoxy beschermt ook tegen vocht en verontreinigingen. Het binnendringen van vocht kan leiden tot corrosie, elektrische lekkage en de groei van geleidende materialen, wat kan leiden tot defecten aan het apparaat. Underfill epoxy fungeert als een barrière, sluit kwetsbare gebieden af en voorkomt dat vocht de verpakking binnendringt. Het biedt ook bescherming tegen stof, vuil en andere verontreinigingen die de elektrische prestaties van de halfgeleiderchip negatief kunnen beïnvloeden. Door de chip en zijn onderlinge verbindingen te beschermen, zorgt underfill epoxy voor de betrouwbaarheid en functionaliteit van het apparaat op de lange termijn.
Bovendien maakt ondergevulde epoxy miniaturisatie in halfgeleiderverpakkingen mogelijk. Met de constante vraag naar kleinere en compactere apparaten, maakt ondergevulde epoxy het gebruik van flip-chip en chip-scale verpakkingstechnieken mogelijk. Deze technieken houden in dat de chip rechtstreeks op het pakketsubstraat wordt gemonteerd, waardoor de noodzaak van draadverbinding wordt geëlimineerd en de pakketafmetingen worden verkleind. Underfill epoxy biedt structurele ondersteuning en handhaaft de integriteit van de chip-substraat-interface, waardoor de succesvolle implementatie van deze geavanceerde verpakkingstechnologieën mogelijk wordt.
Hoe Underfill Epoxy de uitdagingen aanpakt
Halfgeleiderverpakkingen spelen een cruciale rol in de prestaties, betrouwbaarheid en levensduur van elektronische apparaten. Het omvat het inkapselen van geïntegreerde schakelingen (IC's) in beschermende behuizingen, het leveren van elektrische verbindingen en het afvoeren van warmte die tijdens het gebruik wordt gegenereerd. Halfgeleiderverpakkingen staan echter voor verschillende uitdagingen, waaronder thermische spanning en kromtrekken, die de functionaliteit en betrouwbaarheid van de verpakte apparaten aanzienlijk kunnen beïnvloeden.
Een van de belangrijkste uitdagingen is thermische stress. Geïntegreerde schakelingen genereren warmte tijdens het gebruik en onvoldoende dissipatie kan de temperatuur in het pakket verhogen. Deze temperatuurvariatie resulteert in thermische spanning omdat verschillende materialen in het pakket met verschillende snelheden uitzetten en samentrekken. De niet-uniforme uitzetting en samentrekking kan mechanische belasting veroorzaken, wat leidt tot defecten aan de soldeerverbinding, delaminatie en scheuren. Thermische stress kan de elektrische en mechanische integriteit van het pakket aantasten, wat uiteindelijk de prestaties en betrouwbaarheid van het apparaat aantast.
Warpage is een andere kritieke uitdaging bij het verpakken van halfgeleiders. Warpage verwijst naar het buigen of vervormen van het pakketsubstraat of het hele pakket. Het kan optreden tijdens het verpakkingsproces of door thermische belasting. Warpage wordt voornamelijk veroorzaakt door de mismatch in de thermische uitzettingscoëfficiënt (CTE) tussen verschillende materialen in het pakket. De CTE van de siliciummatrijs, het substraat en de vormmassa kan bijvoorbeeld aanzienlijk verschillen. Wanneer ze worden blootgesteld aan temperatuurveranderingen, zetten deze materialen met verschillende snelheden uit of krimpen, wat leidt tot kromtrekken.
Warpage levert verschillende problemen op voor halfgeleiderpakketten:
- Het kan resulteren in spanningsconcentratiepunten, waardoor de kans op mechanische storingen toeneemt en de betrouwbaarheid van de doos afneemt.
- Warpage kan leiden tot moeilijkheden in het assemblageproces, omdat het de uitlijning van de verpakking met andere componenten, zoals de printplaat (PCB), beïnvloedt. Deze verkeerde uitlijning kan elektrische verbindingen aantasten en prestatieproblemen veroorzaken.
- Warpage kan de algehele vormfactor van het pakket beïnvloeden, waardoor het een uitdaging wordt om het apparaat te integreren in kleine vormfactortoepassingen of dichtbevolkte PCB's.
Bij het verpakken van halfgeleiders worden verschillende technieken en strategieën gebruikt om deze uitdagingen het hoofd te bieden. Deze omvatten het gebruik van geavanceerde materialen met bijpassende CTE's om thermische belasting en kromtrekken te minimaliseren. Thermomechanische simulaties en modellering worden uitgevoerd om het gedrag van de verpakking onder verschillende thermische omstandigheden te voorspellen. Ontwerpwijzigingen, zoals het introduceren van spanningsontlastingsstructuren en geoptimaliseerde lay-outs, worden geïmplementeerd om thermische spanning en kromtrekken te verminderen. Bovendien helpt de ontwikkeling van verbeterde productieprocessen en apparatuur het optreden van kromtrekken tijdens de montage te minimaliseren.
Voordelen van Underfill Epoxy
Underfill epoxy is een kritieke component in halfgeleiderverpakkingen die verschillende voordelen biedt. Dit gespecialiseerde epoxymateriaal wordt aangebracht tussen de halfgeleiderchip en het pakketsubstraat, waardoor mechanische versterking wordt geboden en verschillende uitdagingen worden aangepakt. Hier zijn enkele van de kritieke voordelen van ondergevulde epoxy:
- Verbeterde mechanische betrouwbaarheid: Een van de belangrijkste voordelen van underfill epoxy is het vermogen om de mechanische betrouwbaarheid van halfgeleiderpakketten te verbeteren. Underfill epoxy zorgt voor een samenhangende hechting die de algehele structurele integriteit verbetert door de openingen en holtes tussen de chip en het substraat op te vullen. Dit helpt kromtrekken van de verpakking te voorkomen, vermindert het risico op mechanische defecten en verbetert de weerstand tegen externe spanningen zoals trillingen, schokken en thermische cycli. De verbeterde mechanische betrouwbaarheid leidt tot een grotere productduurzaamheid en een langere levensduur van het apparaat.
- Thermische spanningsdissipatie: Underfill epoxy helpt thermische spanning binnen het pakket te verdrijven. Geïntegreerde schakelingen genereren warmte tijdens het gebruik en onvoldoende dissipatie kan leiden tot temperatuurschommelingen in de container. Het underfill-epoxymateriaal, met zijn lagere thermische uitzettingscoëfficiënt (CTE) in vergelijking met de chip- en substraatmaterialen, fungeert als een bufferlaag. Het absorbeert de mechanische belasting die wordt veroorzaakt door thermische spanning, waardoor het risico op soldeerverbindingsfouten, delaminatie en scheuren wordt verminderd. Door thermische stress af te voeren, helpt ondergevulde epoxy de elektrische en mechanische integriteit van het pakket te behouden.
- Verbeterde elektrische prestaties: Underfill epoxy heeft een positieve invloed op de elektrische prestaties van halfgeleiderapparaten. Het epoxymateriaal vult de openingen tussen de chip en het substraat, waardoor parasitaire capaciteit en inductantie worden verminderd. Dit resulteert in verbeterde signaalintegriteit, verminderde signaalverliezen en verbeterde elektrische connectiviteit tussen de chip en de rest van het pakket. De verminderde parasitaire effecten dragen bij aan betere elektrische prestaties, hogere gegevensoverdrachtsnelheden en een grotere betrouwbaarheid van het apparaat. Bovendien biedt ondergevulde epoxy isolatie en bescherming tegen vocht, verontreinigingen en andere omgevingsfactoren die de elektrische prestaties kunnen verminderen.
- Stressverlichting en verbeterde montage: Underfill-epoxy werkt als spanningsverlichtingsmechanisme tijdens de montage. Het epoxymateriaal compenseert de CTE-mismatch tussen de chip en het substraat, waardoor de mechanische spanning tijdens temperatuurveranderingen wordt verminderd. Dit maakt het assemblageproces betrouwbaarder en efficiënter, waardoor het risico op beschadiging van de verpakking of verkeerde uitlijning wordt geminimaliseerd. De gecontroleerde spanningsverdeling door underfill epoxy zorgt ook voor een goede uitlijning met andere componenten op de printplaat (PCB) en verbetert het algehele assemblagerendement.
- Miniaturisatie en vormfactoroptimalisatie: Underfill epoxy maakt miniaturisatie van halfgeleiderpakketten en optimalisatie van de vormfactor mogelijk. Door structurele versterking en spanningsverlichting te bieden, maakt underfill epoxy het mogelijk om kleinere, dunnere en compactere pakketten te ontwerpen en te vervaardigen. Dit is vooral belangrijk voor toepassingen zoals mobiele apparaten en draagbare elektronica, waar ruimte schaars is. De mogelijkheid om vormfactoren te optimaliseren en hogere componentdichtheden te bereiken, draagt bij aan meer geavanceerde en innovatieve elektronische apparaten.
Soorten Underfill Epoxy
Er zijn verschillende soorten underfill-epoxyformuleringen verkrijgbaar in halfgeleiderverpakkingen, elk ontworpen om aan specifieke vereisten te voldoen en verschillende uitdagingen aan te pakken. Hier zijn enkele veelgebruikte soorten underfill-epoxy:
- Capillaire ondervul-epoxy: Capillaire ondervul-epoxy is het meest traditionele en meest gebruikte type. Een epoxy met lage viscositeit vloeit door capillaire werking in de opening tussen de chip en het substraat. Capillaire ondervulling wordt meestal op de rand van de chip aangebracht en terwijl de verpakking wordt verwarmd, stroomt de epoxy onder de chip door en vult de holtes. Dit type ondervulling is geschikt voor verpakkingen met kleine openingen en zorgt voor een goede mechanische versteviging.
- No-Flow Underfill Epoxy: No-flow underfill epoxy is een formulering met een hoge viscositeit die niet uitvloeit tijdens het uitharden. Het wordt aangebracht als een vooraf aangebrachte epoxy of als een film tussen de chip en het substraat. No-flow underfill epoxy is met name handig voor flip-chip-pakketten, waarbij de soldeerbultjes direct in wisselwerking staan met het substraat. Het elimineert de noodzaak van capillaire stroming en vermindert het risico op beschadiging van de soldeerverbinding tijdens de montage.
- Wafer-Level Underfill (WLU): Wafer-level underfill is een underfill-epoxy die op waferniveau wordt aangebracht voordat de afzonderlijke chips worden verenkeld. Het omvat het verdelen van het underfill-materiaal over het gehele wafeloppervlak en het uitharden ervan. Underfill op wafelniveau biedt verschillende voordelen, waaronder een uniforme underfill-dekking, kortere montagetijd en verbeterde procescontrole. Het wordt vaak gebruikt voor de productie van kleine apparaten in grote volumes.
- Gegoten ondervulling (MUF): Gegoten ondervulling is een epoxy ondervulling die wordt aangebracht tijdens het inkapselingsvormen. Het underfill-materiaal wordt op het substraat aangebracht en vervolgens worden de chip en het substraat ingekapseld in een vormmassa. Tijdens het gieten vloeit de epoxy en vult deze de opening tussen de chip en het substraat, waardoor ondervulling en inkapseling in één enkele stap ontstaat. Gegoten ondervulling biedt uitstekende mechanische versterking en vereenvoudigt het montageproces.
- Niet-geleidende underfill (NCF): niet-geleidende underfill-epoxy is speciaal ontwikkeld om elektrische isolatie te bieden tussen de soldeerverbindingen op de chip en het substraat. Het bevat isolerende vulstoffen of additieven die elektrische geleidbaarheid voorkomen. NCF wordt gebruikt in toepassingen waar elektrische kortsluiting tussen aangrenzende soldeerverbindingen een probleem is. Het biedt zowel mechanische versterking als elektrische isolatie.
- Thermisch geleidende ondervulling (TCU): Thermisch geleidende ondervulling epoxy is ontworpen om de warmteafvoer van het pakket te verbeteren. Het bevat thermisch geleidende vulstoffen, zoals keramische of metaaldeeltjes, die de thermische geleidbaarheid van het ondervulmateriaal verbeteren. TCU wordt gebruikt in toepassingen waar efficiënte warmteoverdracht cruciaal is, zoals apparaten met een hoog vermogen of apparaten die in veeleisende thermische omgevingen werken.
Dit zijn slechts enkele voorbeelden van de verschillende soorten underfill epoxy die worden gebruikt in halfgeleiderverpakkingen. De keuze van de juiste ondervul-epoxy hangt af van factoren zoals het ontwerp van de verpakking, het montageproces, thermische vereisten en elektrische overwegingen. Elke underfill epoxy biedt specifieke voordelen en is op maat gemaakt om te voldoen aan de unieke behoeften van verschillende toepassingen.
Capillaire ondervulling: lage viscositeit en hoge betrouwbaarheid
Capillaire underfill verwijst naar een proces dat wordt gebruikt in de halfgeleiderverpakkingsindustrie om de betrouwbaarheid van elektronische apparaten te verbeteren. Het gaat om het vullen van de openingen tussen een micro-elektronische chip en de omringende verpakking met een vloeibaar materiaal met een lage viscositeit, meestal een op epoxy gebaseerde hars. Dit underfill-materiaal biedt structurele ondersteuning, verbetert de thermische dissipatie en beschermt de chip tegen mechanische stress, vocht en andere omgevingsfactoren.
Een van de kritische kenmerken van capillaire ondervulling is de lage viscositeit. Het underfill-materiaal is zo geformuleerd dat het een relatief lage dichtheid heeft, waardoor het tijdens het underfilling-proces gemakkelijk in de smalle openingen tussen de chip en de verpakking kan vloeien. Dit zorgt ervoor dat het underfill-materiaal alle holtes en luchtspleten effectief kan binnendringen en vullen, waardoor het risico op holtevorming wordt geminimaliseerd en de algehele integriteit van de chip-package-interface wordt verbeterd.
Laagviskeuze capillaire underfill-materialen bieden ook verschillende andere voordelen. Ten eerste vergemakkelijken ze de efficiënte stroom van het materiaal onder de chip, wat leidt tot een kortere procestijd en een hogere productiedoorvoer. Dit is vooral belangrijk in productieomgevingen met grote volumes waar tijd- en kostenefficiëntie van cruciaal belang zijn.
Ten tweede zorgt de lage viscositeit voor betere bevochtigings- en hechtingseigenschappen van het ondervulmateriaal. Hierdoor kan het materiaal zich gelijkmatig verspreiden en sterke verbindingen vormen met de chip en de verpakking, waardoor een betrouwbare en robuuste inkapseling ontstaat. Dit zorgt ervoor dat de chip veilig wordt beschermd tegen mechanische spanningen zoals thermische cycli, schokken en trillingen.
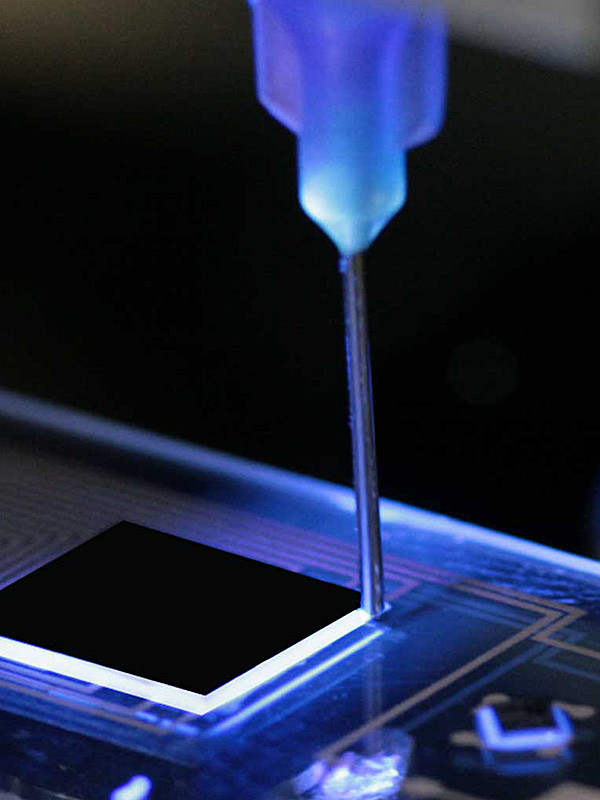
Een ander cruciaal aspect van capillaire underfills is hun hoge betrouwbaarheid. De ondervulmaterialen met lage viscositeit zijn speciaal ontworpen om uitstekende thermische stabiliteit, elektrische isolatie-eigenschappen en weerstand tegen vocht en chemicaliën te vertonen. Deze kenmerken zijn essentieel om de prestaties en betrouwbaarheid van verpakte elektronische apparaten op de lange termijn te waarborgen, met name in veeleisende toepassingen zoals de auto-industrie, ruimtevaart en telecommunicatie.
Bovendien zijn capillaire underfill-materialen ontworpen om een hoge mechanische sterkte en uitstekende hechting te hebben op verschillende substraatmaterialen, waaronder metalen, keramiek en organische materialen die gewoonlijk worden gebruikt in halfgeleiderverpakkingen. Hierdoor kan het ondervulmateriaal fungeren als een spanningsbuffer, waardoor mechanische spanningen die worden gegenereerd tijdens bedrijf of blootstelling aan de omgeving effectief worden geabsorbeerd en afgevoerd.
No-Flow Underfill: zelfdoserend en hoge doorvoer
No-flow underfill is een gespecialiseerd proces dat wordt gebruikt in de halfgeleiderverpakkingsindustrie om de betrouwbaarheid en efficiëntie van elektronische apparaten te verbeteren. In tegenstelling tot capillaire ondervullingen, die afhankelijk zijn van de stroming van materialen met een lage viscositeit, gebruiken ondervullingen zonder stroming een zelfdoserende benadering met materialen met een hoge viscositeit. Deze methode biedt verschillende voordelen, waaronder zelfuitlijning, hoge doorvoer en verbeterde betrouwbaarheid.
Een van de kritieke kenmerken van ondervulling zonder stroming is de mogelijkheid tot zelfdosering. Het ondervulmateriaal dat in dit proces wordt gebruikt, is geformuleerd met een hogere viscositeit, waardoor het niet vrij kan stromen. In plaats daarvan wordt het underfill-materiaal op een gecontroleerde manier op de chip-package-interface gedoseerd. Deze gecontroleerde dosering maakt nauwkeurige plaatsing van het ondervulmateriaal mogelijk, zodat het alleen op de gewenste gebieden wordt aangebracht zonder over te lopen of ongecontroleerd uit te spreiden.
De zelfdoserende aard van ondervulling zonder stroming biedt verschillende voordelen. Ten eerste zorgt het voor zelfuitlijning van het ondervulmateriaal. Terwijl de ondervulling wordt afgegeven, wordt deze vanzelf uitgelijnd met de chip en de verpakking, waardoor de openingen en holtes gelijkmatig worden opgevuld. Dit elimineert de noodzaak van nauwkeurige positionering en uitlijning van de chip tijdens het underfilling-proces, wat tijd en moeite bespaart bij de productie.
Ten tweede zorgt de zelfdoserende eigenschap van ondervullingen zonder stroming voor een hoge doorvoer in de productie. Het doseerproces kan worden geautomatiseerd, waardoor het underfill-materiaal snel en consistent over meerdere chips tegelijk kan worden aangebracht. Dit verbetert de algehele productie-efficiëntie en verlaagt de productiekosten, waardoor het bijzonder voordelig is voor productieomgevingen met grote volumes.
Bovendien zijn ondervulmaterialen zonder stroming ontworpen om een hoge betrouwbaarheid te bieden. De ondervulmaterialen met hoge viscositeit bieden verbeterde weerstand tegen thermische cycli, mechanische spanningen en omgevingsfactoren, waardoor de prestaties op lange termijn van de verpakte elektronische apparaten worden gegarandeerd. De materialen vertonen uitstekende thermische stabiliteit, elektrische isolatie-eigenschappen en weerstand tegen vocht en chemicaliën, wat bijdraagt aan de algehele betrouwbaarheid van de apparaten.
Bovendien hebben de ondervullingsmaterialen met hoge viscositeit die worden gebruikt in ondervulling zonder stroming verbeterde mechanische sterkte en hechtingseigenschappen. Ze vormen een sterke binding met de chip en het pakket, waardoor mechanische spanningen die tijdens bedrijf of blootstelling aan de omgeving worden gegenereerd, effectief worden geabsorbeerd en afgevoerd. Dit helpt de chip te beschermen tegen mogelijke schade en verbetert de weerstand van het apparaat tegen externe schokken en trillingen.
Gegoten ondervulling: hoge bescherming en integratie
Gegoten underfill is een geavanceerde techniek die wordt gebruikt in de halfgeleiderverpakkingsindustrie om elektronische apparaten een hoog niveau van bescherming en integratie te bieden. Het omvat het inkapselen van de hele chip en de omringende verpakking met een vormmassa waarin ondervulmateriaal is verwerkt. Dit proces biedt aanzienlijke voordelen met betrekking tot bescherming, integratie en algehele betrouwbaarheid.
Een van de cruciale voordelen van gegoten underfill is het vermogen om de chip volledig te beschermen. De vormmassa die in dit proces wordt gebruikt, fungeert als een robuuste barrière en omsluit de hele chip en het pakket in een beschermend omhulsel. Dit zorgt voor een effectieve afscherming tegen omgevingsfactoren zoals vocht, stof en verontreinigingen die de prestaties en betrouwbaarheid van het apparaat kunnen beïnvloeden. De inkapseling helpt ook voorkomen dat de chip mechanische spanningen, thermische cycli en andere externe krachten oploopt, waardoor de duurzaamheid op de lange termijn wordt gegarandeerd.
Bovendien maakt gegoten underfill hoge integratieniveaus binnen het halfgeleiderpakket mogelijk. Het ondervullingsmateriaal wordt rechtstreeks in de vormmassa gemengd, waardoor een naadloze integratie van de ondervullings- en inkapselingsprocessen mogelijk is. Deze integratie elimineert de behoefte aan een aparte ondervulstap, waardoor het fabricageproces wordt vereenvoudigd en de productietijd en -kosten worden verminderd. Het zorgt ook voor een consistente en uniforme verdeling van de ondervulling door het hele pakket, waardoor holtes worden geminimaliseerd en de algehele structurele integriteit wordt verbeterd.
Bovendien biedt gegoten ondervulling uitstekende thermische dissipatie-eigenschappen. De vormverbinding is ontworpen om een hoge thermische geleidbaarheid te hebben, waardoor het warmte efficiënt van de chip kan afvoeren. Dit is cruciaal voor het handhaven van de optimale bedrijfstemperatuur van het apparaat en het voorkomen van oververhitting, wat kan leiden tot verslechtering van de prestaties en betrouwbaarheidsproblemen. De verbeterde thermische dissipatie-eigenschappen van gegoten ondervulling dragen bij aan de algehele betrouwbaarheid en levensduur van het elektronische apparaat.
Bovendien maakt gegoten ondervulling meer miniaturisatie en optimalisatie van de vormfactor mogelijk. Het inkapselingsproces kan worden aangepast aan verschillende pakketafmetingen en -vormen, inclusief complexe 3D-structuren. Deze flexibiliteit maakt het mogelijk om meerdere chips en andere componenten te integreren in een compact, ruimtebesparend pakket. De mogelijkheid om hogere niveaus van integratie te bereiken zonder de betrouwbaarheid in gevaar te brengen, maakt gegoten ondervulling bijzonder waardevol in toepassingen waar beperkingen op het gebied van grootte en gewicht van cruciaal belang zijn, zoals mobiele apparaten, wearables en auto-elektronica.
Chip Scale Package (CSP) Underfill: miniaturisatie en hoge dichtheid
Chip Scale Package (CSP) underfill is een kritieke technologie die miniaturisatie en high-density elektronische apparaatintegratie mogelijk maakt. Omdat elektronische apparaten steeds kleiner worden terwijl ze meer functionaliteit bieden, speelt CSP een cruciale rol bij het waarborgen van de betrouwbaarheid en prestaties van deze compacte apparaten.
CSP is een verpakkingstechnologie waarmee de halfgeleiderchip rechtstreeks op het substraat of de printplaat (PCB) kan worden gemonteerd zonder dat er een extra verpakking nodig is. Dit elimineert de noodzaak van een traditionele plastic of keramische container, waardoor de totale omvang en het gewicht van het apparaat worden verminderd. CSP underfill is een proces waarbij een vloeistof of inkapselingsmateriaal wordt gebruikt om de opening tussen de chip en het substraat te vullen, waardoor mechanische ondersteuning wordt geboden en de chip wordt beschermd tegen omgevingsfactoren zoals vocht en mechanische stress.
Miniaturisatie wordt bereikt door CSP-underfill door de afstand tussen de chip en het substraat te verkleinen. Het underfill-materiaal vult de smalle opening tussen de chip en het substraat, waardoor een stevige hechting ontstaat en de mechanische stabiliteit van de chip wordt verbeterd. Dit maakt kleinere en dunnere apparaten mogelijk, waardoor het mogelijk wordt om meer functionaliteit in een beperkte ruimte in te pakken.
Integratie met hoge dichtheid is een ander voordeel van CSP-underfill. Door de behoefte aan een apart pakket te elimineren, maakt CSP het mogelijk de chip dichter bij andere componenten op de printplaat te monteren, waardoor de lengte van elektrische verbindingen wordt verminderd en de signaalintegriteit wordt verbeterd. Het underfill-materiaal fungeert ook als een thermische geleider, waardoor de door de chip gegenereerde warmte efficiënt wordt afgevoerd. Deze mogelijkheid tot thermisch beheer maakt hogere vermogensdichtheden mogelijk, waardoor complexere en krachtigere chips in elektronische apparaten kunnen worden geïntegreerd.
CSP-ondervulmaterialen moeten specifieke kenmerken hebben om te voldoen aan de eisen van miniaturisatie en integratie met hoge dichtheid. Ze moeten een lage viscositeit hebben om het vullen van nauwe openingen te vergemakkelijken, evenals uitstekende vloei-eigenschappen om een uniforme dekking te garanderen en holtes te elimineren. De materialen moeten ook goed hechten aan de chip en het substraat en een solide mechanische ondersteuning bieden. Bovendien moeten ze een hoge thermische geleidbaarheid vertonen om warmte efficiënt van de chip af te voeren.
CSP-underfill op waferniveau: kosteneffectief en hoog rendement
Wafer-level chip scale package (WLCSP) underfill is een kosteneffectieve en hoogrenderende verpakkingstechniek die verschillende voordelen biedt op het gebied van productie-efficiëntie en algehele productkwaliteit. WLCSP-underfill past underfill-materiaal toe op meerdere chips tegelijk terwijl ze zich nog in de vorm van een wafel bevinden, voordat ze in afzonderlijke pakketten worden verpakt. Deze aanpak biedt tal van voordelen op het gebied van kostenreductie, verbeterde procesbeheersing en hogere productieopbrengsten.
Een van de belangrijkste voordelen van WLCSP-ondervulling is de kosteneffectiviteit. Door het ondervulmateriaal op wafelniveau aan te brengen, wordt het verpakkingsproces meer gestroomlijnd en efficiënter. Het ondergevulde materiaal wordt op de wafel gedoseerd met behulp van een gecontroleerd en geautomatiseerd proces, waardoor materiaalverspilling wordt verminderd en arbeidskosten worden geminimaliseerd. Bovendien vermindert het elimineren van individuele verpakkings- en uitlijningsstappen de algehele productietijd en complexiteit, wat resulteert in aanzienlijke kostenbesparingen in vergelijking met traditionele verpakkingsmethoden.
Bovendien biedt WLCSP ondervulling verbeterde procescontrole en hogere productieopbrengsten. Aangezien het underfill-materiaal op wafelniveau wordt aangebracht, maakt het een betere controle over het doseerproces mogelijk, waardoor een consistente en uniforme underfill-dekking voor elke chip op de wafel wordt gegarandeerd. Dit verkleint het risico op holtes of onvolledige ondervulling, wat kan leiden tot betrouwbaarheidsproblemen. De mogelijkheid om de ondervulkwaliteit op wafelniveau te inspecteren en te testen, maakt ook vroegtijdige detectie van defecten of procesvariaties mogelijk, waardoor tijdige corrigerende maatregelen mogelijk zijn en de kans op defecte verpakkingen wordt verkleind. Als gevolg hiervan helpt WLCSP-underfill hogere productieopbrengsten en een betere algehele productkwaliteit te bereiken.
De benadering op wafelniveau maakt ook verbeterde thermische en mechanische prestaties mogelijk. Het underfill-materiaal dat in WLCSP wordt gebruikt, is doorgaans een capillair stromend materiaal met een lage viscositeit dat de nauwe openingen tussen de chips en de wafel efficiënt kan opvullen. Dit zorgt voor een solide mechanische ondersteuning van de chips, waardoor ze beter bestand zijn tegen mechanische belasting, trillingen en temperatuurwisselingen. Bovendien fungeert het ondervulmateriaal als een thermische geleider, waardoor de warmte die door de chips wordt gegenereerd, gemakkelijker wordt afgevoerd, waardoor het thermisch beheer wordt verbeterd en het risico op oververhitting wordt verminderd.
Flip Chip Underfill: hoge I/O-dichtheid en prestaties
Flip-chip underfill is een kritieke technologie die een hoge input/output (I/O)-dichtheid en uitzonderlijke prestaties in elektronische apparaten mogelijk maakt. Het speelt een cruciale rol bij het verbeteren van de betrouwbaarheid en functionaliteit van flip-chip-verpakkingen, die veel worden gebruikt in geavanceerde halfgeleidertoepassingen. Dit artikel onderzoekt het belang van flip-chip underfill en de impact ervan op het bereiken van hoge I/O-dichtheid en prestaties.
Flip-chiptechnologie omvat de directe elektrische verbinding van een geïntegreerde schakeling (IC) of een halfgeleiderchip met het substraat, waardoor draadverbinding overbodig wordt. Dit resulteert in een compacter en efficiënter pakket, aangezien de I/O-pads zich aan de onderkant van de chip bevinden. Flip-chip-verpakkingen bieden echter unieke uitdagingen die moeten worden aangepakt om optimale prestaties en betrouwbaarheid te garanderen.
Een van de kritieke uitdagingen bij het verpakken van flipchips is het voorkomen van mechanische belasting en thermische mismatch tussen de matrijs en het substraat. Tijdens het fabricageproces en de daaropvolgende bewerking kunnen de verschillen in thermische uitzettingscoëfficiënten (CTE) tussen de matrijs en het substraat aanzienlijke spanningen veroorzaken, wat leidt tot verslechtering van de prestaties of zelfs tot defecten. Flip-chip underfill is een beschermend materiaal dat de chip omhult en mechanische ondersteuning en spanningsverlichting biedt. Het verdeelt effectief de spanningen die worden gegenereerd tijdens thermische cycli en voorkomt dat ze de delicate verbindingen aantasten.
Een hoge I/O-dichtheid is van cruciaal belang in moderne elektronische apparaten, waar kleinere vormfactoren en meer functionaliteit essentieel zijn. Flip-chip underfill maakt hogere I/O-dichtheden mogelijk door superieure elektrische isolatie en thermische beheermogelijkheden te bieden. Het ondervulmateriaal vult de opening tussen de matrijs en het substraat, waardoor een robuuste interface ontstaat en het risico op kortsluiting of elektrische lekkage wordt verminderd. Hierdoor kunnen de I/O-pads dichter bij elkaar worden geplaatst, wat resulteert in een grotere I/O-dichtheid zonder dat dit ten koste gaat van de betrouwbaarheid.
Bovendien draagt flip-chip underfill bij aan verbeterde elektrische prestaties. Het minimaliseert de elektrische parasieten tussen de chip en het substraat, waardoor de signaalvertraging wordt verminderd en de signaalintegriteit wordt verbeterd. Het underfill-materiaal vertoont ook uitstekende thermische geleidbaarheidseigenschappen, waardoor de warmte die tijdens het gebruik door de chip wordt gegenereerd, efficiënt wordt afgevoerd. Effectieve warmteafvoer zorgt ervoor dat de temperatuur binnen acceptabele grenzen blijft, waardoor oververhitting wordt voorkomen en optimale prestaties behouden blijven.
Verbeteringen in flip-chip underfill-materialen hebben nog hogere I/O-dichtheden en prestatieniveaus mogelijk gemaakt. Ondervullingen van nanocomposiet maken bijvoorbeeld gebruik van vulstoffen op nanoschaal om de thermische geleidbaarheid en mechanische sterkte te verbeteren. Dit zorgt voor verbeterde warmteafvoer en betrouwbaarheid, waardoor apparaten met hogere prestaties mogelijk worden.
Ball Grid Array (BGA) Underfill: Hoge thermische en mechanische prestaties
Ball Grid Array (BGA) ondervult een kritieke technologie die hoge thermische en mechanische prestaties biedt in elektronische apparaten. Het speelt een cruciale rol bij het verbeteren van de betrouwbaarheid en functionaliteit van BGA-pakketten, die veel worden gebruikt in verschillende toepassingen. In dit artikel zullen we het belang van BGA-ondervulling en de impact ervan op het bereiken van hoge thermische en mechanische prestaties onderzoeken.
BGA-technologie omvat een pakketontwerp waarbij de geïntegreerde schakeling (IC) of halfgeleiderchip op een substraat is gemonteerd en de elektrische verbindingen worden gemaakt via een reeks soldeerballen op het bodemoppervlak van het pakket. BGA vult een materiaal dat wordt afgegeven in de opening tussen de matrijs en het substraat, waardoor de soldeerballen worden ingekapseld en mechanische ondersteuning en bescherming wordt geboden aan de assemblage.
Een van de kritieke uitdagingen bij BGA-verpakkingen is het beheer van thermische spanningen. Tijdens bedrijf genereert de IC warmte, en thermische uitzetting en samentrekking kunnen aanzienlijke druk veroorzaken op de soldeerverbindingen die de matrijs en het substraat verbinden. BGA vervult een cruciale rol bij het verminderen van deze spanningen door een solide verbinding te vormen met de matrijs en het substraat. Het werkt als een spanningsbuffer, absorbeert de thermische uitzetting en samentrekking en vermindert de druk op de soldeerverbindingen. Dit helpt de algehele betrouwbaarheid van het pakket te verbeteren en vermindert het risico op defecte soldeerverbindingen.
Een ander cruciaal aspect van BGA-ondervulling is het vermogen om de mechanische prestaties van het pakket te verbeteren. BGA-pakketten worden vaak blootgesteld aan mechanische spanningen tijdens het hanteren, assembleren en bedienen. Het ondervulmateriaal vult de opening tussen de matrijs en het substraat en biedt structurele ondersteuning en versterking van de soldeerverbindingen. Dit verbetert de algehele mechanische sterkte van het samenstel, waardoor het beter bestand is tegen mechanische schokken, trillingen en andere externe krachten. Door de mechanische spanningen effectief te verdelen, helpt BGA-ondervulling scheuren in verpakkingen, delaminatie of andere mechanische defecten te voorkomen.
Hoge thermische prestaties zijn essentieel in elektronische apparaten om een goede functionaliteit en betrouwbaarheid te garanderen. BGA-ondervulmaterialen zijn ontworpen om uitstekende thermische geleidbaarheidseigenschappen te hebben. Hierdoor kunnen ze warmte op efficiënte wijze wegleiden van de matrijs en deze over het substraat verdelen, waardoor het algehele thermische beheer van het pakket wordt verbeterd. Effectieve warmteafvoer helpt om lagere bedrijfstemperaturen te handhaven, waardoor thermische hotspots en mogelijke prestatievermindering worden voorkomen. Het draagt ook bij aan de levensduur van de kast door de thermische belasting van de componenten te verminderen.
Verbeteringen in BGA-ondervulmaterialen hebben geleid tot nog hogere thermische en mechanische prestaties. Verbeterde formuleringen en vulmaterialen, zoals nanocomposieten of vulstoffen met een hoge thermische geleidbaarheid, hebben een betere warmteafvoer en mechanische sterkte mogelijk gemaakt, waardoor de prestaties van BGA-pakketten verder zijn verbeterd.
Quad Flat Package (QFP) Underfill: groot I/O-aantal en robuustheid
Quad Flat Package (QFP) is een pakket met geïntegreerde schakelingen (IC) dat veel wordt gebruikt in elektronica. Het heeft een vierkante of rechthoekige vorm met kabels die zich aan alle vier de zijden uitstrekken, waardoor er veel input/output (I/O)-aansluitingen zijn. Om de betrouwbaarheid en robuustheid van QFP-pakketten te verbeteren, worden gewoonlijk ondervulmaterialen gebruikt.
Underfill is een beschermend materiaal dat wordt aangebracht tussen de IC en het substraat om de mechanische sterkte van de soldeerverbindingen te versterken en door spanning veroorzaakte storingen te voorkomen. Het is met name cruciaal voor QFP's met een groot aantal I/O's, omdat het grote aantal verbindingen kan leiden tot aanzienlijke mechanische spanningen tijdens thermische cycli en operationele omstandigheden.
Het ondervulmateriaal dat voor QFP-pakketten wordt gebruikt, moet specifieke eigenschappen hebben om robuustheid te garanderen. Ten eerste moet het een uitstekende hechting hebben aan zowel de IC als het substraat om een sterke hechting te creëren en het risico van delaminatie of losraken te minimaliseren. Bovendien moet het een lage thermische uitzettingscoëfficiënt (CTE) hebben om overeen te komen met de CTE van de IC en het substraat, waardoor spanningsmismatches die tot scheuren of breuken kunnen leiden, worden verminderd.
Bovendien moet het ondervulmateriaal goede vloei-eigenschappen hebben om een uniforme bedekking en volledige vulling van de opening tussen de IC en het substraat te garanderen. Dit helpt bij het elimineren van holtes, die de soldeerverbindingen kunnen verzwakken en resulteren in verminderde betrouwbaarheid. Het materiaal moet ook goede uithardingseigenschappen hebben, waardoor het na het aanbrengen een stevige en duurzame beschermlaag kan vormen.
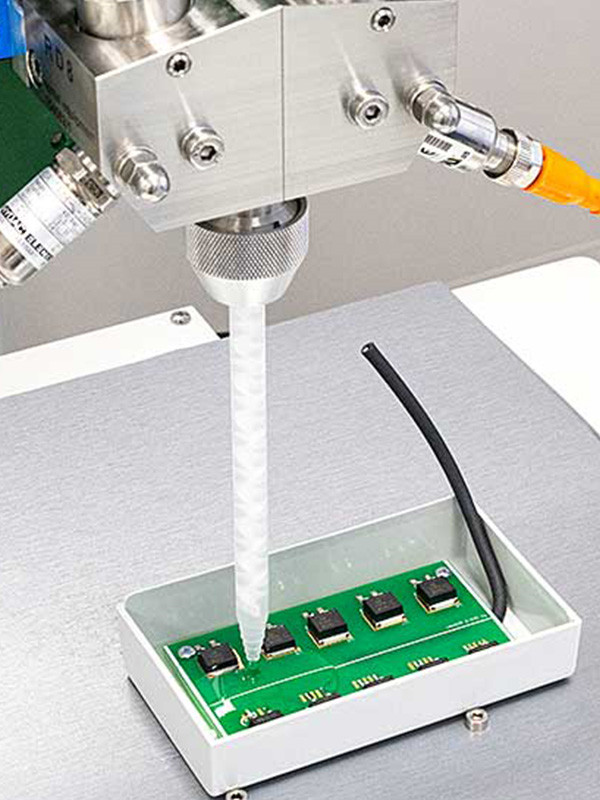
In termen van mechanische robuustheid moet de ondervulling een hoge afschuif- en afpelsterkte hebben om externe krachten te weerstaan en vervorming of scheiding van de verpakking te voorkomen. Het moet ook goed bestand zijn tegen vocht en andere omgevingsfactoren om zijn beschermende eigenschappen in de loop van de tijd te behouden. Dit is met name belangrijk bij toepassingen waarbij het QFP-pakket kan worden blootgesteld aan zware omstandigheden of temperatuurschommelingen.
Er zijn verschillende ondervulmaterialen beschikbaar om deze gewenste eigenschappen te bereiken, waaronder formuleringen op basis van epoxy. Afhankelijk van de specifieke vereisten van de toepassing, kunnen deze materialen worden gedoseerd met behulp van verschillende technieken, zoals capillaire stroming, jetting of zeefdruk.
System-in-Package (SiP) Underfill: integratie en prestaties
System-in-Package (SiP) is een geavanceerde verpakkingstechnologie die meerdere halfgeleiderchips, passieve componenten en andere elementen in één pakket integreert. SiP biedt tal van voordelen, waaronder een kleinere vormfactor, verbeterde elektrische prestaties en verbeterde functionaliteit. Om de betrouwbaarheid en prestaties van SiP-assemblages te waarborgen, worden vaak underfill-materialen gebruikt.
Underfill in SiP-toepassingen is cruciaal voor het bieden van mechanische stabiliteit en elektrische connectiviteit tussen de verschillende componenten binnen het pakket. Het helpt het risico op door spanning veroorzaakte storingen, zoals scheuren of breuken in de soldeerverbinding, te minimaliseren, die kunnen optreden als gevolg van verschillen in thermische uitzettingscoëfficiënten (CTE) tussen de componenten.
Het integreren van meerdere componenten in een SiP-pakket leidt tot complexe interconnectiviteit, met veel soldeerverbindingen en circuits met een hoge dichtheid. Underfill-materialen helpen deze onderlinge verbindingen te versterken, waardoor de mechanische sterkte en betrouwbaarheid van de assemblage worden verbeterd. Ze ondersteunen de soldeerverbindingen, waardoor het risico op vermoeidheid of schade door thermische cycli of mechanische belasting wordt verminderd.
In termen van elektrische prestaties zijn underfill-materialen van cruciaal belang bij het verbeteren van de signaalintegriteit en het minimaliseren van elektrische ruis. Door de openingen tussen componenten op te vullen en de afstand ertussen te verkleinen, helpt underfill parasitaire capaciteit en inductantie te verminderen, waardoor een snellere en efficiëntere signaaloverdracht mogelijk wordt.
Bovendien moeten ondervulmaterialen voor SiP-toepassingen een uitstekende thermische geleidbaarheid hebben om de door de geïntegreerde componenten gegenereerde warmte efficiënt af te voeren. Effectieve warmteafvoer is essentieel om oververhitting te voorkomen en de algehele betrouwbaarheid en prestaties van de SiP-assemblage te behouden.
Underfill-materialen in SiP-verpakkingen moeten specifieke eigenschappen hebben om aan deze integratie- en prestatie-eisen te voldoen. Ze moeten goed vloeibaar zijn om volledige dekking te garanderen en openingen tussen de componenten op te vullen. Het ondervulmateriaal moet ook een formulering met een lage viscositeit hebben om gemakkelijk doseren en vullen in nauwe gaten of kleine ruimtes mogelijk te maken.
Bovendien moet het ondervulmateriaal een sterke hechting vertonen op verschillende oppervlakken, waaronder halfgeleiderchips, substraten en passieve materialen, om een betrouwbare hechting te garanderen. Het moet compatibel zijn met verschillende verpakkingsmaterialen, zoals organische substraten of keramiek, en goede mechanische eigenschappen vertonen, waaronder een hoge afschuif- en afpelsterkte.
De keuze van het ondervulmateriaal en de toepassingsmethode hangt af van het specifieke SiP-ontwerp, de componentvereisten en de fabricageprocessen. Doseertechnieken zoals capillaire stroming, spuiten of filmondersteunde methoden passen gewoonlijk ondervulling toe in SiP-assemblages.
Opto-elektronica ondervulling: optische uitlijning en bescherming
Opto-elektronica-ondervulling omvat het inkapselen en beschermen van opto-elektronische apparaten terwijl een nauwkeurige optische uitlijning wordt gegarandeerd. Opto-elektronische apparaten, zoals lasers, fotodetectoren en optische schakelaars, vereisen vaak een delicate uitlijning van optische componenten om optimale prestaties te bereiken. Tegelijkertijd moeten ze worden beschermd tegen omgevingsfactoren die hun functionaliteit kunnen beïnvloeden. Opto-elektronica underfill beantwoordt aan beide vereisten door optische uitlijning en bescherming in één enkel proces te bieden.
Optische uitlijning is een cruciaal aspect van de fabricage van opto-elektronische apparaten. Het omvat het uitlijnen van visuele elementen, zoals vezels, golfgeleiders, lenzen of roosters, om een efficiënte lichttransmissie en -ontvangst te garanderen. Nauwkeurige uitlijning is nodig om de prestaties van het apparaat te maximaliseren en de signaalintegriteit te behouden. Traditionele uitlijntechnieken omvatten handmatige uitlijning met behulp van visuele inspectie of geautomatiseerde uitlijning met behulp van uitlijnfasen. Deze methoden kunnen echter tijdrovend, arbeidsintensief en foutgevoelig zijn.
Opto-elektronica ondervulmateriaal een innovatieve oplossing door uitlijningskenmerken rechtstreeks in het ondervulmateriaal op te nemen. Underfill-materialen zijn meestal vloeibare of halfvloeibare verbindingen die kunnen vloeien en de openingen tussen optische componenten kunnen opvullen. Door uitlijnkenmerken toe te voegen, zoals microstructuren of vaste markeringen, in het ondervulmateriaal, kan het uitlijnproces worden vereenvoudigd en geautomatiseerd. Deze functies fungeren als leidraad tijdens de montage en zorgen voor een nauwkeurige uitlijning van de optische componenten zonder ingewikkelde uitlijningsprocedures.
Naast optische uitlijning beschermen underfill-materialen opto-elektronische apparaten. Opto-elektronische componenten worden vaak blootgesteld aan ruwe omgevingen, waaronder temperatuurschommelingen, vocht en mechanische belasting. Deze externe factoren kunnen de prestaties en betrouwbaarheid van de apparaten na verloop van tijd verminderen. Underfill-materialen fungeren als een beschermende barrière, die de optische componenten inkapselt en ze beschermt tegen omgevingsverontreinigingen. Ze bieden ook mechanische versterking, waardoor het risico op schade door schokken of trillingen wordt verminderd.
Underfill-materialen die worden gebruikt in opto-elektronische toepassingen zijn meestal ontworpen om een lage brekingsindex en uitstekende optische transparantie te hebben. Dit zorgt voor minimale interferentie met de optische signalen die door het apparaat gaan. Bovendien vertonen ze een goede hechting op verschillende substraten en hebben ze lage thermische uitzettingscoëfficiënten om de belasting van het apparaat tijdens thermische cycli te minimaliseren.
Het underfill-proces omvat het doseren van het underfill-materiaal op het apparaat, het laten vloeien en de openingen tussen optische componenten opvullen, en het vervolgens uitharden om een stevige omhulling te vormen. Afhankelijk van de specifieke toepassing kan het ondervulmateriaal met verschillende technieken worden aangebracht, zoals capillaire stroming, jetdosering of zeefdruk. Het uithardingsproces kan worden bereikt door warmte, UV-straling of beide.
Ondervulling van medische elektronica: biocompatibiliteit en betrouwbaarheid
Medische elektronica ondervult een gespecialiseerd proces waarbij elektronische componenten die in medische apparaten worden gebruikt, worden ingekapseld en beschermd. Deze apparaten spelen een cruciale rol in verschillende medische toepassingen, zoals implanteerbare apparaten, diagnostische apparatuur, bewakingssystemen en systemen voor medicijnafgifte. Ondervulling van medische elektronica richt zich op twee kritieke aspecten: biocompatibiliteit en betrouwbaarheid.
Biocompatibiliteit is een fundamentele vereiste voor medische hulpmiddelen die in contact komen met het menselijk lichaam. De ondervulmaterialen die in medische elektronica worden gebruikt, moeten biocompatibel zijn, wat betekent dat ze geen schadelijke effecten of bijwerkingen mogen veroorzaken wanneer ze in contact komen met levend weefsel of lichaamsvloeistoffen. Deze materialen moeten voldoen aan strikte voorschriften en normen, zoals ISO 10993, waarin test- en evaluatieprocedures voor biocompatibiliteit worden gespecificeerd.
Underfill-materialen voor medische elektronica worden zorgvuldig geselecteerd of geformuleerd om biocompatibiliteit te garanderen. Ze zijn ontworpen om niet-toxisch, niet-irriterend en niet-allergeen te zijn. Deze materialen mogen geen schadelijke stoffen uitlogen of na verloop van tijd worden afgebroken, omdat dit kan leiden tot weefselbeschadiging of ontsteking. Biocompatibele ondervulmaterialen hebben ook een lage wateropname om de groei van bacteriën of schimmels die infecties kunnen veroorzaken te voorkomen.
Betrouwbaarheid is een ander cruciaal aspect van ondervulling van medische elektronica. Medische apparaten hebben vaak te maken met uitdagende bedrijfsomstandigheden, waaronder extreme temperaturen, vocht, lichaamsvloeistoffen en mechanische belasting. Underfill-materialen moeten de elektronische componenten beschermen en hun betrouwbaarheid en functionaliteit op de lange termijn waarborgen. Betrouwbaarheid is van het grootste belang in medische toepassingen waar apparaatstoringen ernstige gevolgen kunnen hebben voor de veiligheid en het welzijn van de patiënt.
Ondervulmaterialen voor medische elektronica moeten goed bestand zijn tegen vocht en chemicaliën om blootstelling aan lichaamsvloeistoffen of sterilisatieprocessen te weerstaan. Ze moeten ook een goede hechting vertonen op verschillende substraten, waardoor een veilige inkapseling van de elektronische componenten wordt gegarandeerd. Mechanische eigenschappen, zoals lage thermische uitzettingscoëfficiënten en goede schokbestendigheid, zijn cruciaal voor het minimaliseren van stress op de details tijdens thermische cycli of automatische belasting.
Het ondervulproces voor medische elektronica omvat:
- Doseren van het ondervulmateriaal op de elektronische componenten.
- De gaten vullen.
- Uitharden om een beschermende en mechanisch stabiele inkapseling te vormen.
Er moet voor worden gezorgd dat de functies volledig worden gedekt en dat er geen holtes of luchtzakken zijn die de betrouwbaarheid van het apparaat in gevaar kunnen brengen.
Bovendien wordt rekening gehouden met aanvullende overwegingen bij het ondervullen van medische hulpmiddelen. Het ondervulmateriaal moet bijvoorbeeld compatibel zijn met de sterilisatiemethoden die voor het apparaat worden gebruikt. Sommige materialen kunnen gevoelig zijn voor specifieke sterilisatietechnieken, zoals stoom, ethyleenoxide of straling, en het kan nodig zijn om alternatieve materialen te kiezen.
Aerospace Electronics Underfill: bestand tegen hoge temperaturen en trillingen
Lucht- en ruimtevaartelektronica ondervult een gespecialiseerd proces om elektronische componenten in ruimtevaarttoepassingen in te kapselen en te beschermen. Lucht- en ruimtevaartomgevingen vormen unieke uitdagingen, waaronder hoge temperaturen, extreme trillingen en mechanische spanningen. Daarom richt ondervulling van ruimtevaartelektronica zich op twee cruciale aspecten: weerstand tegen hoge temperaturen en weerstand tegen trillingen.
Weerstand tegen hoge temperaturen is van het grootste belang in ruimtevaartelektronica vanwege de hoge temperaturen die tijdens het gebruik worden ervaren. De ondervulmaterialen die worden gebruikt in ruimtevaarttoepassingen moeten bestand zijn tegen deze hoge temperaturen zonder de prestaties en betrouwbaarheid van de elektronische componenten in gevaar te brengen. Ze moeten minimale thermische uitzetting vertonen en stabiel blijven over een breed temperatuurbereik.
Underfill-materialen voor luchtvaartelektronica worden geselecteerd of geformuleerd voor hoge glasovergangstemperaturen (Tg) en thermische stabiliteit. Een hoge Tg zorgt ervoor dat het materiaal zijn mechanische eigenschappen behoudt bij verhoogde temperaturen, waardoor vervorming of verlies van hechting wordt voorkomen. Deze materialen zijn bestand tegen extreme temperaturen, zoals tijdens het opstijgen, atmosferische terugkeer of het werken in hete motorcompartimenten.
Bovendien moeten ondervulmaterialen voor luchtvaartelektronica lage thermische uitzettingscoëfficiënten (CTE) hebben. De CTE meet hoeveel een materiaal uitzet of samentrekt bij temperatuurveranderingen. Door een lage CTE te hebben, kunnen underfill-materialen de spanning op de elektronische componenten minimaliseren die wordt veroorzaakt door thermische cycli, wat kan leiden tot mechanische storingen of vermoeidheid van de soldeerverbinding.
Trillingsbestendigheid is een andere kritieke vereiste voor ondervulling van ruimtevaartelektronica. Lucht- en ruimtevaartvoertuigen zijn onderhevig aan verschillende trillingen, waaronder trillingen van de motor, door vluchten veroorzaakte trillingen en mechanische schokken tijdens de lancering of landing. Deze trillingen kunnen de prestaties en betrouwbaarheid van elektronische componenten in gevaar brengen als ze niet voldoende worden beschermd.
Underfill-materialen die worden gebruikt in luchtvaartelektronica moeten uitstekende trillingsdempende eigenschappen hebben. Ze moeten de door trillingen gegenereerde energie absorberen en afvoeren, waardoor de belasting van de elektronische componenten wordt verminderd. Dit helpt de vorming van scheuren, breuken of andere mechanische defecten als gevolg van overmatige blootstelling aan trillingen te voorkomen.
Bovendien hebben underfill-materialen met een hoge hechting en cohesieve sterkte de voorkeur in lucht- en ruimtevaarttoepassingen. Deze eigenschappen zorgen ervoor dat het ondervulmateriaal stevig gehecht blijft aan de elektronische componenten en het substraat, zelfs onder extreme trillingsomstandigheden. Sterke hechting voorkomt dat het ondervulmateriaal delamineert of loslaat van de elementen, waardoor de integriteit van de inkapseling behouden blijft en het wordt beschermd tegen het binnendringen van vocht of vuil.
Het underfill-proces voor ruimtevaartelektronica omvat typisch het doseren van het underfill-materiaal op de elektronische componenten, het laten vloeien en de openingen opvullen, en het vervolgens uitharden om een robuuste inkapseling te vormen. Het uithardingsproces kan worden uitgevoerd met behulp van thermische of UV-uithardingsmethoden, afhankelijk van de specifieke eisen van de toepassing.
Ondervulling van auto-elektronica: duurzaamheid en weerstand tegen thermische cycli
Auto-elektronica ondervult een kritisch proces waarbij elektronische componenten in autotoepassingen worden ingekapseld en beschermd. Automotive-omgevingen bieden unieke uitdagingen, waaronder temperatuurschommelingen, thermische cycli, mechanische spanningen en blootstelling aan vocht en chemicaliën. Daarom richt de ondervulling van auto-elektronica zich op twee kritieke aspecten: duurzaamheid en weerstand tegen thermische cycli.
Duurzaamheid is een cruciale vereiste voor ondervulling van auto-elektronica. Tijdens normaal gebruik ervaren autovoertuigen constante trillingen, schokken en mechanische spanningen. De ondervulmaterialen die in automobieltoepassingen worden gebruikt, moeten elektronische componenten robuust beschermen en hun duurzaamheid en levensduur waarborgen. Ze moeten bestand zijn tegen de zware omstandigheden en mechanische belastingen die op de weg voorkomen en bestand zijn tegen het binnendringen van vocht, stof en chemicaliën.
Underfill-materialen voor auto-elektronica worden geselecteerd of geformuleerd voor hoge mechanische sterkte en slagvastheid. Ze moeten een uitstekende hechting aan de elektronische componenten en het substraat vertonen, waardoor delaminatie of scheiding onder mechanische belasting wordt voorkomen. Duurzame ondervulmaterialen helpen het risico van schade aan de elektronische componenten als gevolg van trillingen of schokken te minimaliseren, waardoor betrouwbare prestaties gedurende de levensduur van het voertuig worden gegarandeerd.
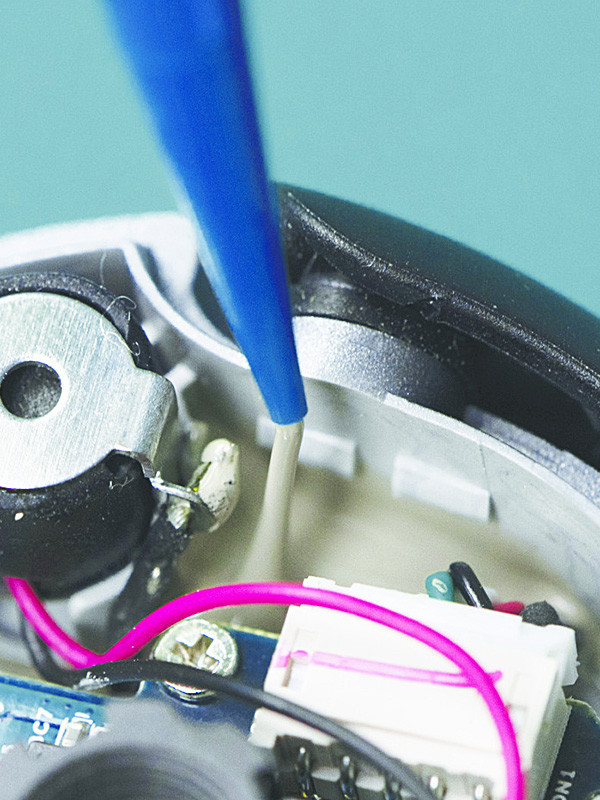
Weerstand tegen thermische cycli is een andere kritieke vereiste voor ondervulling van auto-elektronica. Automobielvoertuigen ondergaan frequente temperatuurschommelingen, vooral tijdens het starten en draaien van de motor, en deze temperatuurcycli kunnen thermische spanningen veroorzaken op elektronische componenten en het omliggende ondervulmateriaal. De ondervulmaterialen die in automobieltoepassingen worden gebruikt, moeten een uitstekende weerstand tegen thermische cycli hebben om bestand te zijn tegen deze temperatuurschommelingen zonder hun prestaties in gevaar te brengen.
Underfill-materialen voor auto-elektronica moeten lage thermische uitzettingscoëfficiënten (CTE) hebben om de spanning van de elektronische componenten tijdens thermische cycli te minimaliseren. Een goed op elkaar afgestemde CTE tussen het underfill-materiaal en de ingrediënten vermindert het risico op vermoeidheid van de soldeerverbinding, barsten of andere mechanische defecten veroorzaakt door thermische spanning. Bovendien moeten de ondervulmaterialen een goede thermische geleidbaarheid hebben om warmte efficiënt af te voeren, waardoor plaatselijke hotspots worden voorkomen die de prestaties en betrouwbaarheid van de componenten kunnen beïnvloeden.
Bovendien moeten ondervulmaterialen voor auto-elektronica bestand zijn tegen vocht, chemicaliën en vloeistoffen. Ze moeten een lage wateropname hebben om schimmelgroei of corrosie van de elektronische componenten te voorkomen. Chemische weerstand zorgt ervoor dat het ondervulmateriaal stabiel blijft wanneer het wordt blootgesteld aan autovloeistoffen, zoals oliën, brandstoffen of reinigingsmiddelen, waardoor degradatie of verlies van hechting wordt voorkomen.
Het underfill-proces voor auto-elektronica omvat typisch het doseren van het underfill-materiaal op de elektronische componenten, het laten vloeien en de openingen opvullen, en het vervolgens uitharden om een duurzame inkapseling te vormen. Het uithardingsproces kan worden bereikt door middel van thermische of UV-uithardingsmethoden, afhankelijk van de specifieke vereisten van de toepassing en het gebruikte ondervulmateriaal.
De juiste ondervul-epoxy kiezen
Het kiezen van de juiste underfill epoxy is een cruciale beslissing bij de montage en bescherming van elektronische componenten. Underfill-epoxies bieden mechanische versterking, thermisch beheer en bescherming tegen omgevingsfactoren. Hier zijn enkele belangrijke overwegingen bij het selecteren van de juiste ondervul-epoxy:
- Thermische eigenschappen: Een van de belangrijkste functies van underfill epoxy is het afvoeren van warmte die wordt gegenereerd door elektronische componenten. Daarom is het essentieel om rekening te houden met de thermische geleidbaarheid en thermische weerstand van de epoxy. Een hoge thermische geleidbaarheid helpt bij een efficiënte warmteoverdracht, waardoor hotspots worden voorkomen en de betrouwbaarheid van de componenten behouden blijft. De epoxy moet ook een lage thermische weerstand hebben om thermische spanning op de componenten tijdens temperatuurwisselingen te minimaliseren.
- CTE-overeenkomst: de thermische uitzettingscoëfficiënt (CTE) van de underfill-epoxy moet goed worden afgestemd op de CTE van de elektronische componenten en het substraat om thermische spanning te minimaliseren en soldeerverbindingsfouten te voorkomen. Een goed afgestemde CTE helpt het risico op mechanische storingen als gevolg van thermische cycli te verminderen.
- Vloei- en spleetvullend vermogen: De ondergevulde epoxy moet goede vloei-eigenschappen hebben en de mogelijkheid hebben om spleten tussen componenten effectief op te vullen. Dit zorgt voor volledige dekking en minimaliseert holtes of luchtzakken die de mechanische stabiliteit en thermische prestaties van de assemblage kunnen beïnvloeden. De viscositeit van de epoxy moet geschikt zijn voor de specifieke toepassing en assemblagemethode, of het nu gaat om capillaire stroming, jetdosering of zeefdruk.
- Hechting: Een sterke hechting is cruciaal voor het ondervullen van epoxy om een betrouwbare hechting tussen de componenten en de ondergrond te garanderen. Het moet een goede hechting vertonen op verschillende materialen, waaronder metalen, keramiek en kunststoffen. De hechtingseigenschappen van de epoxy dragen bij aan de mechanische integriteit en betrouwbaarheid op lange termijn van de assemblage.
- Uithardingsmethode: Overweeg de uithardingsmethode die het beste bij uw productieproces past. Underfill-epoxies kunnen worden uitgehard door hitte, UV-straling of een combinatie van beide. Elke uithardingsmethode heeft voordelen en beperkingen, en het is essentieel om degene te kiezen die aansluit bij uw productie-eisen.
- Omgevingsbestendigheid: Evalueer de weerstand van de underfill-epoxy tegen omgevingsfactoren zoals vocht, chemicaliën en extreme temperaturen. De epoxy moet bestand zijn tegen blootstelling aan water, waardoor schimmelgroei of corrosie wordt voorkomen. Chemische weerstand zorgt voor stabiliteit bij contact met autovloeistoffen, reinigingsmiddelen of andere potentieel bijtende stoffen. Bovendien moet de epoxy zijn mechanische en elektrische eigenschappen behouden over een breed temperatuurbereik.
- Betrouwbaarheid en levensduur: houd rekening met het trackrecord en de betrouwbaarheidsgegevens van de underfill-epoxy. Zoek naar epoxymaterialen die zijn getest en waarvan bewezen is dat ze goed presteren in vergelijkbare toepassingen of die beschikken over branchecertificeringen en naleving van relevante normen. Overweeg factoren zoals verouderingsgedrag, betrouwbaarheid op lange termijn en het vermogen van de epoxy om zijn eigenschappen in de loop van de tijd te behouden.
Bij het selecteren van de juiste underfill-epoxy is het cruciaal om rekening te houden met de specifieke vereisten van uw toepassing, waaronder thermisch beheer, mechanische stabiliteit, milieubescherming en compatibiliteit met het productieproces. Het raadplegen van epoxyleveranciers of het inwinnen van deskundig advies kan nuttig zijn bij het nemen van een weloverwogen beslissing die voldoet aan de behoeften van uw toepassing en zorgt voor optimale prestaties en betrouwbaarheid.
Toekomstige trends in ondervulepoxy
Underfill epoxy evolueert voortdurend, gedreven door vooruitgang in elektronische technologieën, opkomende toepassingen en de behoefte aan verbeterde prestaties en betrouwbaarheid. Er zijn verschillende toekomstige trends waar te nemen in de ontwikkeling en toepassing van underfill epoxy:
- Miniaturisatie en verpakkingen met een hogere dichtheid: aangezien elektronische apparaten blijven krimpen en hogere componentdichtheden hebben, moeten underfill-epoxies zich dienovereenkomstig aanpassen. Toekomstige trends zullen zich richten op het ontwikkelen van underfill-materialen die kleinere openingen tussen componenten doordringen en opvullen, waardoor volledige dekking en betrouwbare bescherming wordt gegarandeerd in steeds meer geminiaturiseerde elektronische assemblages.
- Hoogfrequente toepassingen: met de groeiende vraag naar hoogfrequente en snelle elektronische apparaten, zullen epoxyformuleringen voor ondervulling moeten voldoen aan de specifieke vereisten van deze toepassingen. Underfill-materialen met een lage diëlektrische constante en verliesarme raaklijnen zullen essentieel zijn om signaalverlies te minimaliseren en de integriteit van hoogfrequente signalen in geavanceerde communicatiesystemen, 5G-technologie en andere opkomende toepassingen te behouden.
- Verbeterd thermisch beheer: warmteafvoer blijft een kritiek punt van zorg voor elektronische apparaten, vooral met de toenemende vermogensdichtheden. Toekomstige underfill-epoxyformuleringen zullen zich richten op verbeterde thermische geleidbaarheid om de warmteoverdracht te verbeteren en thermische problemen effectief te beheersen. Geavanceerde vulstoffen en additieven zullen worden opgenomen in underfill-epoxies om een hogere thermische geleidbaarheid te bereiken met behoud van andere gewenste eigenschappen.
- Flexibele en rekbare elektronica: De opkomst van flexibele en rekbare elektronica opent nieuwe mogelijkheden voor het ondervullen van epoxymaterialen. Flexibele underfill-epoxies moeten uitstekende hechting en mechanische eigenschappen vertonen, zelfs bij herhaaldelijk buigen of strekken. Deze materialen zullen de inkapseling en bescherming van elektronica in draagbare apparaten, buigbare displays en andere toepassingen die mechanische flexibiliteit vereisen, mogelijk maken.
- Milieuvriendelijke oplossingen: duurzaamheid en milieuoverwegingen zullen een steeds belangrijkere rol spelen bij de ontwikkeling van ondervulbare epoxymaterialen. De nadruk zal liggen op het creëren van epoxyformuleringen die vrij zijn van gevaarlijke stoffen en die gedurende hun hele levenscyclus een verminderde impact op het milieu hebben, inclusief productie, gebruik en verwijdering. Biogebaseerde of hernieuwbare materialen kunnen ook aan belang winnen als duurzame alternatieven.
- Verbeterde productieprocessen: toekomstige trends in underfill-epoxy zullen zich richten op materiaaleigenschappen en vooruitgang in productieprocessen. Technieken zoals additieve fabricage, selectieve dosering en geavanceerde uithardingsmethoden zullen worden onderzocht om de toepassing en prestaties van underfill-epoxy in verschillende elektronische assemblageprocessen te optimaliseren.
- Integratie van geavanceerde test- en karakteriseringstechnieken: met de toenemende complexiteit en eisen van elektronische apparaten, zal er behoefte zijn aan geavanceerde test- en karakteriseringsmethoden om de betrouwbaarheid en prestaties van ondergevulde epoxy te waarborgen. Technieken zoals niet-destructief testen, in-situ monitoring en simulatietools zullen helpen bij de ontwikkeling en kwaliteitscontrole van ondergevulde epoxymaterialen.
Conclusie
Underfill epoxy speelt een cruciale rol bij het verbeteren van de betrouwbaarheid en prestaties van elektronische componenten, met name in halfgeleiderverpakkingen. De verschillende soorten underfill epoxy bieden een reeks voordelen, waaronder hoge betrouwbaarheid, zelfdosering, hoge dichtheid en hoge thermische en mechanische prestaties. Het kiezen van de juiste underfill epoxy voor de toepassing en het pakket zorgt voor een robuuste en langdurige hechting. Naarmate de technologie voortschrijdt en de pakketgroottes kleiner worden, verwachten we nog meer innovatieve epoxy-oplossingen voor ondervulling die superieure prestaties, integratie en miniaturisatie bieden. Underfill epoxy zal een steeds belangrijkere rol gaan spelen in de toekomst van elektronica, waardoor we in verschillende industrieën hogere niveaus van betrouwbaarheid en prestaties kunnen bereiken.